An infrared look at various radiant installation methods
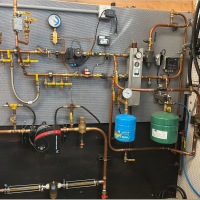
I rented a Flir camera with professional operator from Springfield Utilities. They use this camera to find transformer and connection hot spots on their overhead lines. At the time it was a $7000.00 camera, probably get the same or better resolution for 2500 now

I built these 4X8 demo boards, same SWT, same flow rate and same length tube, shop was about 65F at time of testing. 6" fiberglass batts below the bays.
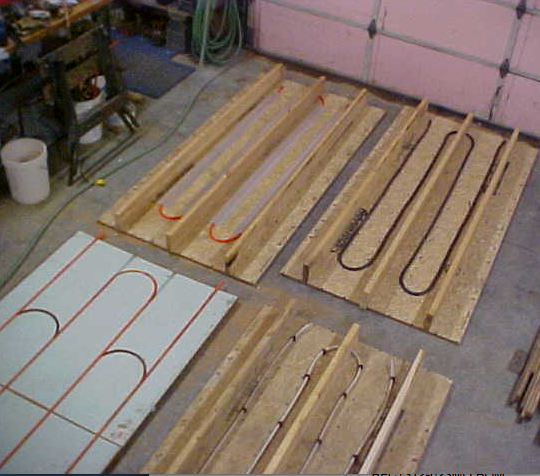
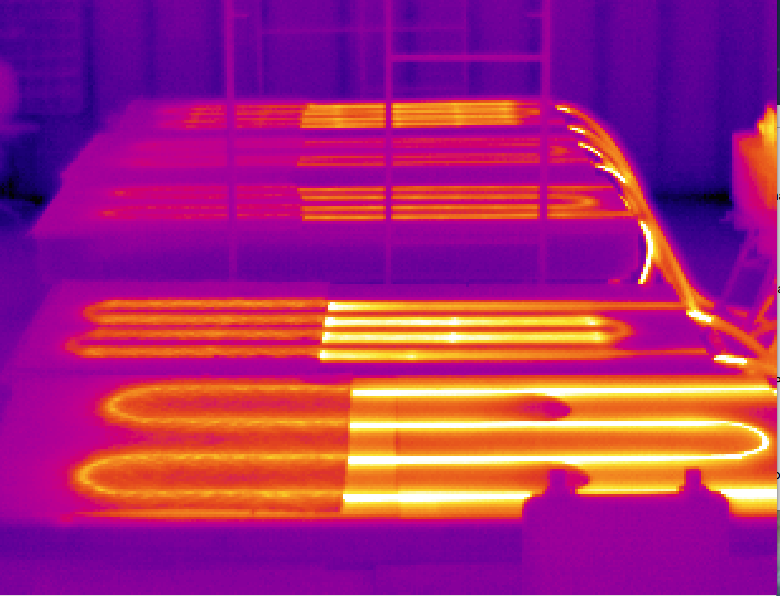
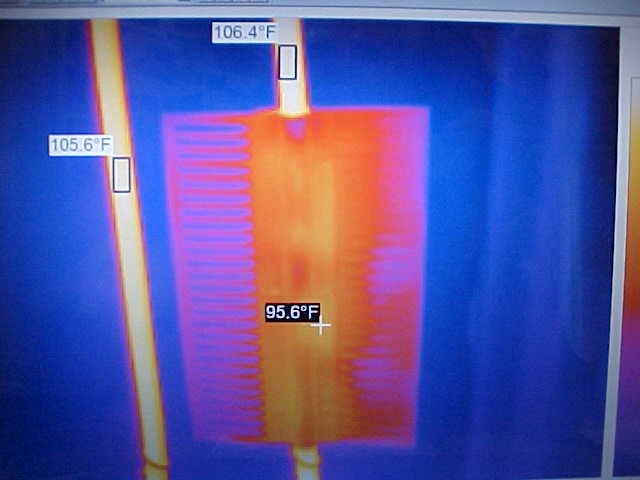
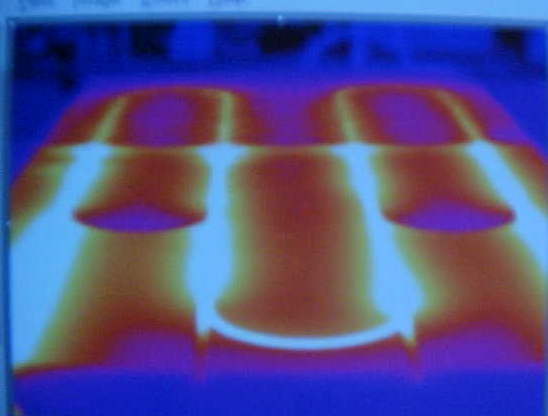
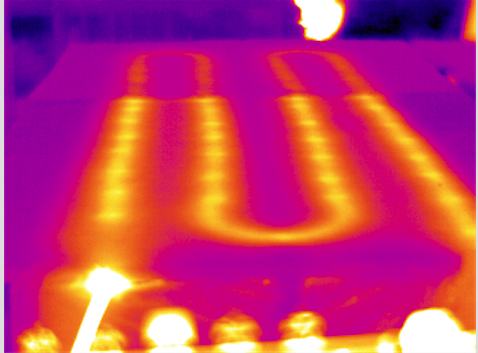
The closest on the overview is Warmboard 12" OC, the rest are 8" OC.
ThermoFin™ wide, heavy gauge model.
Next in line is copper tube in TF
Wirsbo (now Uponor) in TF
Onix staple up
Suspended Wirsbo
Interesting details:
I had to pull the copper out of the TF to crimp the pex onto the copper, on the supply and return ends. Just pulling the tube out of the TF groove 1/8" shows a transfer difference. The fit of the tube, completely into the TF makes a difference.
Warmboard had a few grooves router into it from a previous demo, cutting the aluminum has an noticable transfer effect.
The Onix staple up shows where the tube does not touch the Advantec tightly. It was stapled every 6" as per installation and the staples were confirmed to be in contact. Notice the best transfer is around, and the staple itself.
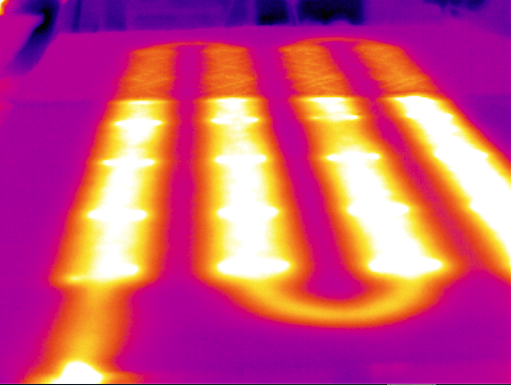
1/2 of the sheet was covered with berber carpet, no pad below.
Also an example of the UltraFin™ product at work on bare, suspended Wirsbo pex
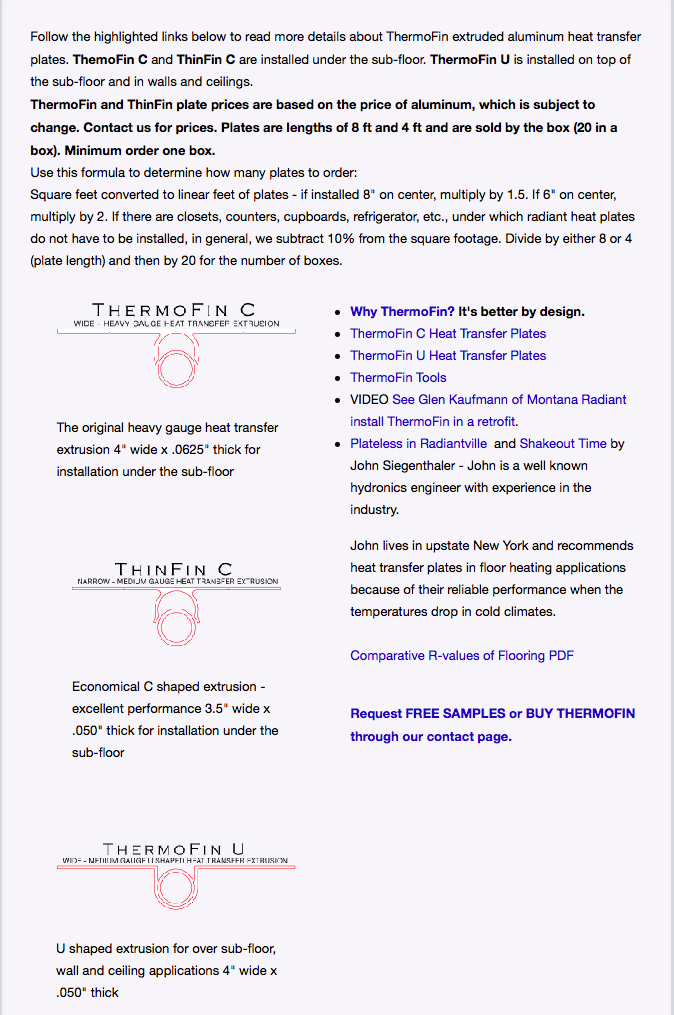
trainer for Caleffi NA
Living the hydronic dream
Comments
-
That's quite interesting. Thanks for sharing.0
-
Very nice.
You don't happen to have any that shows the various depths of tubing in a sand bed under pavers do you?
I have been fighting an uphill battle on that lately."If you can't explain it simply, you don't understand it well enough"
Albert Einstein0 -
This archived article shows how output is effected with tube at the bottom of a slab for some idea. Quite an output hit.
Modeling through sand is not so easy as the moisture content makes a difference in transfer. Also how well the pavers contact the sand bed. I imagine a FEA could be done for dry and wet sand, for comparison.
I'll think on that today and see if I have anything on sand bed performance.
http://www.pmmag.com/articles/87540-depth-perceptionBob "hot rod" Rohr
trainer for Caleffi NA
Living the hydronic dream0 -
I remember this post from long ago. Should be a reference for people deciding RF details.0
-
I did some pretty extensive FEA modeling of different plates and application methods while I was at Wirsbo/Uponor. I will have to dig into my old backup drives to see if I still have them. Him Ly at Uponor will probably have some good stuff. One of the interesting things that we learned about plates is that thickness played a somewhat lesser role as compared to tube contact area and the amount of material in the area of the transition from the omega to the flat plate. This of course took the thin, flashing metal type plates out of the running. Extruded plates had significantly better heat transfer. Dale and I had a pretty good debate about the thickness issue. His plates were the thickest available and Wirsbo plates were somewhat thinner but the difference in heat output and reaction time was nearly negligible although, there was a difference.
1 -
Dales original Thermofin were, are, about an inch wider then the "thin fin" extruded plates, so some performance edge there also.
The key to Thermofin is the thickness where the tube socket meets the actual fin. More material there helps keep the tension of the groove tighter. It's all about the amount of aluminum in the design and hows it's used.
Bob "hot rod" Rohr
trainer for Caleffi NA
Living the hydronic dream0 -
I've got a bathroom radiant job coming up and I'm debating staple-up vs. Viega Climate Panel. The bathroom is being gutted, so I can use either, but staple-up would be much easier and would still get the job done.
8.33 lbs./gal. x 60 min./hr. x 20°ΔT = 10,000 BTU's/hour
Two btu per sq ft for degree difference for a slab0 -
Categories
- All Categories
- 87K THE MAIN WALL
- 3.2K A-C, Heat Pumps & Refrigeration
- 58 Biomass
- 426 Carbon Monoxide Awareness
- 113 Chimneys & Flues
- 2.1K Domestic Hot Water
- 5.7K Gas Heating
- 109 Geothermal
- 161 Indoor-Air Quality
- 3.6K Oil Heating
- 70 Pipe Deterioration
- 994 Plumbing
- 6.3K Radiant Heating
- 391 Solar
- 15.4K Strictly Steam
- 3.4K Thermostats and Controls
- 55 Water Quality
- 44 Industry Classes
- 48 Job Opportunities
- 18 Recall Announcements