Two-Pipe Balance Question
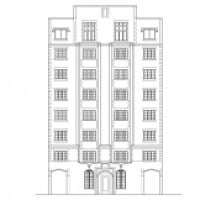
My immediate problem is two-fold: steam through the returns, which I've traced back to a specific return and am dealing with getting a trap replaced to deal with that - the suspect trap isn't readily accessible and requires removing a convector to get at it. The pressure has been at 1-1/2 pounds and I talked the janitor into 1 pound. No improvement, but also no worsening.
The other problem is a bit bigger. There are two steam mains which snake their way west from the boiler room, one on the north side of the building, about 65' long and one at the south, about 97' long. The rooms serviced by the north main have been cooler this year, partially, I think by the sensor locations of the new R&D system - the system is satisfied even if the rooms are too cold or the main rooms cool down too quickly. That's easily fixable by moving them, which is in the works. That said, however, this side of the building has always been a problem - it's cooler, not just because of the north exposure and despite replacement windows in most of those units. The temperature difference can be nearly 10-12 degrees! Almost all the traps, including the F&T traps were replaced two years ago. The longer main has a Hoffman FT015H4 and the shorter an FT015H3, both are located after a cooling leg at the end of the runs with a drip down into the returns.
There are 5 returns, each with an F&T trap and a pump back into the boiler. One interesting feature of the north main and north return are that they supply the lobby convector - which then ties into a return from the south main and has an air vent at the convector itself.
I've attached plans of the first floor and basement showing the layout of the mains and returns. Still working on the upper plans. I have the feeling that the heating wasn't entirely satisfactory even at day one, either through insufficient radiation or poor system management, since there are lots of replacements with larger radiators or convectors and the rear bathrooms have had one-pipe radiators tapped onto the hybrid convective/radiator originally provided (essentially a six-floor pipe radiator with each floor having the pipes enclosed in a convector flue with registers near the floor and ceiling). A building built by the same architect-developer two years later had conventional cast iron radiators....
Any suggestions as to where I should start directing my attention beyond sensor location and making sure everything within units is in good working order (i.e. traps, dampers, valves, etc).
Comments
-
When the air has been pushed into the returns, where does it go from there? If there is a final restriction, then the steam will have trouble getting in.--NBC0
-
There is a vent pipe just incorporated into the return pump assembly. As I understand it, that is the only vent that should be in the system.
Have attached photo of return array. Vent pipe (sorry, don't have shot of the top of it) is central pipe in the picture. Spoke too soon, there's the top of it.0 -
What I was wondering was if the F&T trap at the end of the north main had failed or was insufficient. Would removing convectors/radiators that were originally located at the end of the main (there was a ceiling radiator that was removed in a former washroom and two convectors on the 8th floor were removed in favor of electric baseboard) have caused problems? There is a section of cast iron baseboard at the 8th floor, originally a radiator I think, and a convector in the exercise room, at the very end of the main. The exercise room is noticeably cooler than the bike room, which have similarly sized convectors (there is also a steam pipe in the bike room soffit providing some radiant heat too).nicholas bonham-carter said:When the air has been pushed into the returns, where does it go from there? If there is a final restriction, then the steam will have trouble getting in.--NBC
0 -
Perhaps an obvious question -- and very likely you have already addressed it, but... is the relationship between the actual installed radiation, as it is functioning today, vs. the actual room by room heat loss for the various rooms at least more or less the same everywhere in the building? If not, balancing can become... shall we say interesting?Br. Jamie, osb
Building superintendent/caretaker, 7200 sq. ft. historic house museum with dependencies in New England0 -
You might well, and should well ask.... I think I've talked about it previously in other posts....Jamie Hall said:Perhaps an obvious question -- and very likely you have already addressed it, but... is the relationship between the actual installed radiation, as it is functioning today, vs. the actual room by room heat loss for the various rooms at least more or less the same everywhere in the building? If not, balancing can become... shall we say interesting?
The north side of the building in particular, has a lot of add on radiators and convectors. One of my neighbors has the original convector in her living room as well as TWO additional radiators, one of which is HUGE (have never been in that unit). However, those are on the south main.
But the short answer is, probably, no. Interestingly I did a quick calc of what was needed for my living room for -10 F and I think I needed radiation of 92 EDR and the max of the original Trane from what I could find, was like 86 (and for a wider/deeper element than I think was originally installed).
Back to your original question, the room with the biggest variety is the living rooms and then the second floor units which are partially over driveways (and one is over the boiler room). I think the bulk of the radiation on the north main, however, is pretty even on each floor. Or are you saying the entire building as a whole?0 -
I was thinking more of the building as a whole -- comparing the spaces which are warm enough with those which aren't. Just because it sort of sounds to me as though the original installation may have left something to be desired in that regard...Br. Jamie, osb
Building superintendent/caretaker, 7200 sq. ft. historic house museum with dependencies in New England0 -
I agree that it left a lot to do desired. Interestingly the rooms that are cold have the same size convectors as the side that is warm. However, the units over the driveway also had the same size convectors, one one of them now has a convector that is more than three times bigger (haven't figured out the EDR, it may not be that much bigger, just physical size is larger).Jamie Hall said:I was thinking more of the building as a whole -- comparing the spaces which are warm enough with those which aren't. Just because it sort of sounds to me as though the original installation may have left something to be desired in that regard...
I'm going to have to start by investigating the existing radiation and heat loss. My gut feeling is the boiler itself is oversized, but I could be wrong (it was sized to also provide hot water via a heat exchanger apparatus, long abandoned).0 -
So here's my game plan:
1. Measure and map out original convectors, their sizes, edr and locations versus heat loss.
2. Measure current heating units, either original convectors or replacement radiator/convector.
3. Measure piping sizes where possible.
4. Check F&T traps to make sure they are working at both ends of the main and returns.
Does that sound like a reasonable way to start?
I've attached some photos of the "problem" north steam main. The F&T trap at the end, the connection for a downfeed convector and it's returns where they tie into a return fed by the south main and of the return array where there are F&T traps before the return pipes merge into the return pump.0 -
Number one goal should be to get the steam arriving at all the radiators/emitters simultaneously. This job could be made easier by renting an IR camera, with recording capabilities, and viewing the steam rising up from a 10 degree setback. Start in the basement, and watch for steam bottlenecks. Later on, you can show the recording to the steam expert, in order to determine the next course of action (trap replacement, sagging pipe repitching,etc.).
Once the system is giving all points on a floor simultaneous steam, then you can address those individuals, who are under or over radiated.
With the size of your building, and the potential fuel economies, which could be realized, I would consider the purchase, or long term rental of a camera.
Without this methodical examination, you will continue to be shooting in the dark, for another year.--NBC0 -
NBC - thanks for the suggestion, I'm going to have to set up an organizational chart or plan for myself to do it methodically.
One thing I neglected to mention was that the return temperature sensor for the old heat timer was on the problem return (not that it necessarily worked) - do you think the F&T trap at the end of this return could be failed closed, if I recall correctly, this return was one of the colder ones.0 -
Time is running out for this, so make it so!
Probably not much organization needed:
Get IR camera
Notify all residents of an off period
Set controls back up to temp after a few hours
Observe how the steam flows with the camera, looking for slow areas.
Finally, show the recording to your steam pro for him to locate/rectify the bottlenecks.--NBC0 -
I think NBC is onto something. What happens to the air after it leaves the F&T trap? Some pictures of the piping coming back from the trap would help. Also, does the discharge from the F&T trap at the end have to go thru another trap before it reaches the tank/pump?nicholas bonham-carter said:When the air has been pushed into the returns, where does it go from there? If there is a final restriction, then the steam will have trouble getting in.--NBC
All Steamed Up, Inc.
Towson, MD, USA
Steam, Vapor & Hot-Water Heating Specialists
Oil & Gas Burner Service
Consulting0 -
Steamhead, sorry for the slow response, haven't been online for a few days. The F&T at the end of the main ties into the drip/return line (interestingly a return served by the other main) that runs down to collect condensate from the convector to the right of it in the photo above, from there the return goes under the slab after tying in to another return - not sure exactly where and then pops out into the basement (there is only a partial basement). At the end of that return (the return that the F&T connects to) there is another F&T before the receiver. See the plans & photos in the posts above.0
-
I had looked at your post a while ago, I'm not sure if it was this thread or an earlier one, but I didn't have time to reply. Sorry. I think you have a very clear problem going on that is a bit difficult to see because of the way the piping all comes together at your condensate receiver pump with all those f&t traps, etc. It is a bit of a confused mess! I think your posts provide an answer to the affirmative, but I'm not 100% sure. Here is my take on your problems.
It appears that your condensate return lines are feeding into f&t traps and then into the receiver. Is this correct? This is NOT the way it should be. The only reason that this is done is as a band-aide, and a very bad one at that, done because steam is getting into the return piping as a result of failed radiator/convector traps in this system. The f&t trap at the end, called a "master trap" is placed as a cheap fix to keep steam out of the receiver. However, the resulting problems of steam in the condensate lines is not corrected and will cause some of the radiators to heat poorly. Also, the f&t trap itself will restrict the free flow of air that is needed to allow the returns to freely breath and expel air. Also keep in mind that the return piping must be arranged to allow both air and water to flow without restriction. This means that there can be no dips down and then rising back up unless the line splits into a wet leg and an air leg.
As for any drips from the steam mains or end of steam main drips, these do need traps if connected to a condensate pump.
If I am seeing your system clearly and you have master traps, you may have a failed thermostatic element, which could prevent the passage of air. Since you're looking building wide in your plan for real solutions, I would fix all of the traps and get rid of the master traps. (If indeed you have them. I might be all wrong on my take, if so, ooops. Sorry!)Dave in Quad Cities, America
Weil-McLain 680 with Riello 2-stage burner, December 2012. Firing rate=375MBH Low, 690MBH Hi.
System = Early Dunham 2-pipe Vacuo-Vapor (inlet and outlet both at bottom of radiators) Traps are Dunham #2 rebuilt w. Barnes-Jones Cage Units, Dunham-Bush 1E, Mepco 1E, and Armstrong TS-2. All valves haveTunstall orifices sized at 8 oz.
Current connected load EDR= 1,259 sq ft, Original system EDR = 2,100 sq ft Vaporstat, 13 oz cutout, 4 oz cutin - Temp. control Tekmar 279.
http://grandviewdavenport.com0 -
This is the sort of problem, which could be easily identified by the IR camera, instead of feeling all the traps, taking their temperature,etc.
As this is getting to the end of winter, it becomes more and more difficult to run the boiler nonstop for diagnostic purposes.--NBC0 -
It's my understanding that the F&T traps should be there because of the pump - everything I'm reading indicates that to me unless I'm really misreading. I can't seem to find a diagram right now that shows this. The piping is all pitched pretty nicely from what I can tell with no siphons.
I've been delving deeply into Dan's books and it appears that its the traps - I have the sneaky feeling that we need to replace them all again and find the hidden traps that I suspect are lurking behind built-ins. There also may be at least one more hidden convector on the riser with the most problems.
I'm trying to get at the low hanging fruit first, a couple of leaky valves and traps that I know are bad, etc. The last time we replaced the traps there was nearly a revolt because people had plastered over the access to them!0 -
Meant to include this link: https://heatinghelp.com/systems-help-center/what-you-ought-to-know-about-f-and-t-traps/
0 -
The traps discharging into the dry return need to be there, to keep steam out of the dry return.
The trap at the inlet to the condensate tank does NOT belong there. If steam appears at the tank, either one or more of the traps discharging into the dry return is bad, or the pressure is high enough that the water entering the dry return is flashing into steam.
Anytime we see a trap installed at the inlet to a condensate tank, we know the system has been knuckleheaded.
If you're in Chicago, call Dave Bunnell, also known as "The Steam Whisperer". He's in the Find a Contractor section of this site.All Steamed Up, Inc.
Towson, MD, USA
Steam, Vapor & Hot-Water Heating Specialists
Oil & Gas Burner Service
Consulting0 -
So I re-read Dan's books on that last night and it appears I was mistaken, I think it's just a check valve that needs to be there. Unfortunately, Dave's not taking new clients as of end of last year. We're not going to be able to do any drastic work until we take care of some other urgent projects (masonry and water system) - ugh.
The max pressure is set at 2 (and appears to be hitting 3 psi) - since only one return appears to be hot it's failed traps. The F&T traps at the end of the two mains are new, but may need to be checked. We were told by our current "boiler guy" that the F&T traps were put in by "someone who knew what they were doing" - he said some other things that made me wonder whether he really knew very much. I'm guessing they were installed in '71 when the oil burner was replaced with gas (the labels have zip codes, so early/mid 60's at the very earliest). I suspect that these traps are causing air blockages...0 -
Another correction:
The only place that a check valve belongs on a condensate tank is on the pump discharge.
Restating Steamhead's (and my own) previous statements on traps, an F&T trap is needed at the drip end of a steam main. The discharge can connect into the condensate return line or directly to the condensate receive tank/pump set. The other set of lines are the "dry" condensate return lines. These carry air and condensate, but never steam and they never have pressure. These lines should connect into the vented condensate receiver tank, with no F&T trap, no check valve, no nothing. Just an open connection. If there is steam in this line, it is because a trap somewhere in the system has failed open. Many times in old systems, knuckle heads, (sometimes erroneously known as knowledgeable steam men) will deal with the problem of steam in the condensate lines by adding a master trap where the line comes to the condensate tank. When this is done, it will cause serious balance problems because it will restrict the ability of the return lines to vent air out of the system.
Dave in Quad Cities, America
Weil-McLain 680 with Riello 2-stage burner, December 2012. Firing rate=375MBH Low, 690MBH Hi.
System = Early Dunham 2-pipe Vacuo-Vapor (inlet and outlet both at bottom of radiators) Traps are Dunham #2 rebuilt w. Barnes-Jones Cage Units, Dunham-Bush 1E, Mepco 1E, and Armstrong TS-2. All valves haveTunstall orifices sized at 8 oz.
Current connected load EDR= 1,259 sq ft, Original system EDR = 2,100 sq ft Vaporstat, 13 oz cutout, 4 oz cutin - Temp. control Tekmar 279.
http://grandviewdavenport.com0 -
Thanks for the, um, disheartening, info. It looks like we're not going to (or be able to) do much beyond checking the F&T traps this season since they have "worked" in the past and obviously we can't shut down the system for long in this weather. As I've suspected its going to be a long term project.
I also had an interesting chat with my janitor this morning. He's of the opinion that the system was originally vacuum and they let the pump fail and decided to replace it with the rats nest (assuming that it wasn't done upon the shift from oil to gas). Judging from the added one pipe radiators tapped off the bathroom pipe "radiators" (a pipe in a metal chase inside the wall with a register top and bottom to create a convective flow - I have yet to find how to confirm the EDR for them) I don't see how a vacuum system could have functioned for long. With all the changes to radiators elsewhere there were design or operational problems from day one. The interesting thing is I don't see any tell tale evidence of any vacuum equipment left in the boiler room unless I'm mistaken about the big hanging tank that I thought was for hot water.0 -
Have you posted a pic of that tank? It could be for a vacuum system. Someone just posted that recently on a Hoffman.Two-pipe Trane vaporvacuum system; 1466 edr
Twinned, staged Slantfin TR50s piped into 4" header with Riello G400 burners; 240K lead, 200K lag Btus. Controlled by Taco Relay and Honeywell RTH6580WF0 -
Lets see if I have one. It's HUGE, as in nearly as big as the boiler. There are old pipes from the sides of the boiler that there "sawed" off (torched more likely) that sort of follow into the remaining original hot water piping - the current water heater is a regular tank off in a corner of the boiler room.
It's way up near the ceiling - to give you a point of reference the pressure gauge is above the top of the boiler. The photo with the three knobs to the right of the LWCO look like they may have connected to the tank at one time. I'll try and see if I can get better photos - the boiler room is tight, especially where the controls are. The picture of the pressure gauge shows the pipe coming down towards the boiler. I'd never thought it might have once been vacuum, so now I may do a bit more sleuthing down there.0 -
That's an old domestic hot water tank that was heated by a steam coil.All Steamed Up, Inc.
Towson, MD, USA
Steam, Vapor & Hot-Water Heating Specialists
Oil & Gas Burner Service
Consulting0 -
I didn't think that was part of a vacuum system. The coil must have been in the huge asbestos coated hood (always seemed to me that it was some sort of massive heat exchanger). Any evidence of a vacuum system in the boiler room is long gone.Steamhead said:That's an old domestic hot water tank that was heated by a steam coil.
0
Categories
- All Categories
- 87K THE MAIN WALL
- 3.2K A-C, Heat Pumps & Refrigeration
- 58 Biomass
- 426 Carbon Monoxide Awareness
- 117 Chimneys & Flues
- 2.1K Domestic Hot Water
- 5.7K Gas Heating
- 109 Geothermal
- 161 Indoor-Air Quality
- 3.6K Oil Heating
- 70 Pipe Deterioration
- 994 Plumbing
- 6.3K Radiant Heating
- 389 Solar
- 15.4K Strictly Steam
- 3.4K Thermostats and Controls
- 54 Water Quality
- 44 Industry Classes
- 48 Job Opportunities
- 18 Recall Announcements