Welcome! Here are the website rules, as well as some tips for using this forum.
Need to contact us? Visit https://heatinghelp.com/contact-us/.
Click here to Find a Contractor in your area.
Has anyone ever seen this?
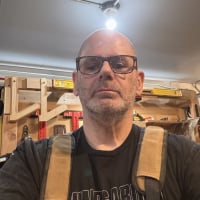
Steve Minnich
Member Posts: 2,868
I pulled this out of a built-in casting/pump flange on a very old American Standard boiler? The boiler side pump flange was actually cast into the section. But...I've never seen this brass fitting inside the pump outlet flange? Does anyone know if this was actually an American Standard part? It was a perfect fit. Or, some after market remedy of some sort?
Steve Minnich
0
Comments
-
It puzzles me too. I can't figure out why they wanted to restrict flow. Typical Series 100 that was on there. I was betting on Dan, Hot Rod, Ice Sailer, Gordy, or Ironman to have the answer.Steve Minnich0
-
Sailor***Steve Minnich0
-
There was an error rendering this rich post.
2 -
some sort of diffuser mechanism. maybe to encourage flow across the sections instead of a straight path?Bob "hot rod" Rohr
trainer for Caleffi NA
Living the hydronic dream0 -
I'm going to venture a guess. Depending on the location of the flange casting, that piece may have been used to disperse the water as it entered the boiler. To prevent a current from forming through one section and not enough flow through the other sections.
Do you have pics of the casting?0 -
Thanks HR
Harvey, I do not.
Mark, I was thinking the same thing.Steve Minnich0 -
I agree with Harv and HR. Those old Am Stan boilers had extremely large, open water ways on them, and water being like my ex brother in law (wet lazy and stupid) likes to follow the path of least resistance. Having the baffle immediately inside the boiler causes a turbulence that breaks up a straight shot through the sections resulting in leaving hot spots and wasted energy.
I am thinking that if you did a combustion analysis with the baffle in, and then removed the baffle and retested, you'd see a significantly higher flue gas temperature due to this syndrome.
Frank Wilsey (Steamhead) has an article in the archives about sizing a pump for older gravity to forced circulation systems. It follows the same theory of being able to run water through these old low pressure drop boilers so fast that they don't get a chance to get their sections scrubbed by the moving water.
Or, it could be a turbo encabulator :-)
I've seen something similar in copper tube boilers, but it was made of a spun fiberglass insert. Its function was to negate hydraulic erosion corrosion on the return side of the heat exchanger. It had rifling inside to cause the water to swirl as it went down the tube, thereby scrubbing the heat exchange surface, thereby increasing the Reynolds numbers and avoiding reverse turbo encabulation… (all but the encabulation comment is true, honestly.) Seriously :-)There was an error rendering this rich post.
0 -
FWIW, I too think it is some form of a diffuser to diffuse flowing water in the boiler.
I had a customer with a really old house. That had been moved and re-assembled hundreds of years before, on top of the existing buried foundation of a prior house. Sometime in the 1930's to the 1950's. they put heat in. In the back of the house off the kitchen was a LOOOOOONG radiator. Well over 30 sections with a leg section in the middle. It was fed on one end. You couldn't get to the other end because of a old foundation below. The radiator never heated beyond the first three sections.
I removed the radiator, took a piece of 3/4" copper tube that was 3/4's of the length of the radiator, drilled some 1/4" holes along the length, left the end open and put it inside the top nipple passage. I turned it back on and it worked like a charm. The owner was thrilled. It now worked. Getting the hot water to the far end of the radiator got hot water along a longer section of the radiator and eliminated the dead spot because of the length.
We didn't know it specifically, but old boilers we erected had the return in the back with two returns and one larger supply outlet. We used to add a recirc line to help with internal mixing in the boiler. I installed a few real ship box 4 section dry base boilers in the mid 1970's. The Tankless was in the back section but all the boiler water went through the front section. I installed a 6 section. The tankless wouldn't get hot because the circulation to the back of the boiler was so bad, the hot water by-passed the back. Bad internal circulation.0 -
Were you replacing the boiler? If not did you put it back in?0
Categories
- All Categories
- 86.7K THE MAIN WALL
- 3.1K A-C, Heat Pumps & Refrigeration
- 56 Biomass
- 423 Carbon Monoxide Awareness
- 104 Chimneys & Flues
- 2K Domestic Hot Water
- 5.6K Gas Heating
- 103 Geothermal
- 158 Indoor-Air Quality
- 3.5K Oil Heating
- 68 Pipe Deterioration
- 940 Plumbing
- 6.2K Radiant Heating
- 385 Solar
- 15.3K Strictly Steam
- 3.4K Thermostats and Controls
- 54 Water Quality
- 43 Industry Classes
- 47 Job Opportunities
- 18 Recall Announcements