Gas venting - Condensation - Liner needed? (CT)

Trying to diagnose a problem and trying to figure out which of the more than half-a-dozen contractors is actually on the money. Any advice much appreciated.
Description of problem:
2-story brick chimney on 2-story brick colonial. In Connecticut (CT). Have owned the house 1.5 years. House built in 1956.
Last winter replaced oil boiler with gas boiler - Burham Series 3 Boiler (Model 306B). Venting was connected to chimney as before - containing a clay-lined flue.
About a month ago I started noticing moisture getting into the house where the chimney meets the lower roof of an addition to the house.
Looking above the spot, the chimney looks wet. More specifically, the bricks on the half of the chimney over on that side of the house look wet all the way up to the top of the chimney.
At first every contractor said the problem was rain was getting through - I needed to add flashing to the lower roof. But the more I look at it the more it seems the wet bricks are not going away - even after several days of dry weather.
In fact, on dry days I can sometimes see the bricks sweating (water coming out of the bricks).
I have a feeling that the venting might be related to the problem or contributing to it.
I'm trying to figure out if I really need/should have/required to have a stainless steel liner. One contractor said that this was code (in CT) and that the heating company should have installed it.
I've also tried to call the manufacturer of boiler (Burnham) to ask if this boiler requires it. I wanted to know b/c the manual is a little ambiguous: one page (p.9) says that the venting should be chosen up "to NFPA 54 and applicable local codes" but then Appendix B1 (p.38) has a sentence that states "clay flue lined masonry chimneys do not meet the venting requirements for this appliance".
I tried to call Burnham but they refuse to clarify. Saying that only answer technical questions from inspectors, not homeowners, for liability issues". I thought that was weird.
In any case, does anybody know if CT codes require stainless steel liners? And I've also read conflicting statements about how long-lasting they may or may not be? Thoughts?
I attach a photo of what it looks like today.
Any advice much appreciated.
Thanks.
-Alex
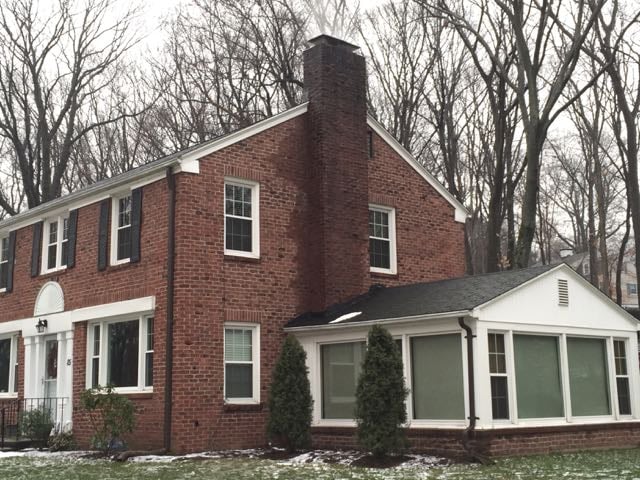
Comments
-
"" One contractor said that this was code (in CT) and that the heating company should have installed it. ""
He's the smart one. Hire him to have the liner installed.
In Massachusetts, that's considered a 3 sided chimney and in some cases now, it can't be vented into.
In Massachusetts, the person who takes out the gas permit, is responsible for the gas venting for the new gas conversion equipment and to be sure it is brought up to current code.
"" but then Appendix B1 (p.38) has a sentence that states "clay flue lined masonry chimneys do not meet the venting requirements for this appliance". ""
That about says it all. The I/O manual says not to connect it to a clay tile chimney because of condensation issues. The clay tiles are now destroyed by the acid in the flue gasses.
IMO, no matter how the installer slices it, he installed it improperly. That photo is a poster child for what happens when someone thinks they know what they are doing, but don't.0 -
The 306B has a heating output of 146,000BTU’s who sized this unit?
During last week’s cold spell did you notice any short cycling of the boiler?0 -
That cap you have on the top of the chimney. Do you have two fireplaces and are those "top dampers" with the chain that hang down into the fireplace so you can open and close the dampers? Is the boiler flue coming up between the two flues? Do you have water running down and into the fire boxes of the fireplaces?
That house looks like a brick veneer on a wood frame. They used a Common Bond and there are no header courses to tie the wall together. And it isn't a Flemish Bond or any other bond that I know of. If it is just a veneer, there may be serious water damage occurring between the brick and the wood framing behind the chimney. You should have it attended to as soon as possible. Are you getting water stains on the sunroom ceiling where it meets the chimney yet?0 -
Do you have an old cleanout that will allow you to look into the chimney from the basement--if so use a mirror to look up there to look for water dripping to confirm. NG exhaust definitely has lots of acidic water vapor in exhaust, whether enough to make that sort of staining, I am not sure. That looks to be quite a bit of moisture leaking all along the flueway.
I have two brick chimneys, both clay lined flues in good shape. One is unused (fireplace) and the other vents the boiler only. During conversion I did use SS liner even though not required by code in my area for reason stated above. So far it has done well and during cold snaps you will see lots of frozen ice near the cap and running down the immediate bricks, so yes lots of water vapor. But I have also done lots of water repairs to the chimneys as they do need good caps/crowns, tight flashing and where exposed a chimney specific water repellent (allows moisture to breathe out). These all make a huge difference.
0 -
Ok, thanks. Ironically, I really did not like the guy who mentioned the liner b/c he was adamant the main problem was actually the roofing and the flashing on the study. It was only after some insistence that you went to check on the flue in the basement (he did not look from the top) - and although he said the thing about the code he still didn't think that was the source of the problem (I also caught him with a blatant over-charging on a water-proofing quote).icesailor said:"" One contractor said that this was code (in CT) and that the heating company should have installed it. ""
He's the smart one. Hire him to have the liner installed.
In Massachusetts, that's considered a 3 sided chimney and in some cases now, it can't be vented into.
In Massachusetts, the person who takes out the gas permit, is responsible for the gas venting for the new gas conversion equipment and to be sure it is brought up to current code.
"" but then Appendix B1 (p.38) has a sentence that states "clay flue lined masonry chimneys do not meet the venting requirements for this appliance". ""
That about says it all. The I/O manual says not to connect it to a clay tile chimney because of condensation issues. The clay tiles are now destroyed by the acid in the flue gasses.
IMO, no matter how the installer slices it, he installed it improperly. That photo is a poster child for what happens when someone thinks they know what they are doing, but don't.
I also called the installer after that visit and the installer was adamant that this is not the problem ("stainless steel liner not necessary and contractor must be a scammer"). What's frustrating is that I've had 6 different chimney/mason companies look at this in the last month and everybody tells me something different (mostly focused on re-pointing or fixing flashing). I have one more chimney company coming tomorrow to check this. Anything specific I should say/check so that I get a better on-hands diagnosis?
Thanks a million for the help.
0 -
Are you suggesting it's way too much for the house? I believe it was sized roughly based on the size of the house (~2300 sq ft) but I don't know how carefully. Can you give me some roundabout numbers for short-cycling? I haven't been on the lookout for that and haven't noticed anything too dramatic. The temperature tends to hold fairly reasonably (the house has new windows and retains heat well).pecmsg said:The 306B has a heating output of 146,000BTU’s who sized this unit?
During last week’s cold spell did you notice any short cycling of the boiler?
Thank you for the advice.
-Alex
0 -
The masons/chimney expert should examine from the top including the flashings. They do leak and are often sources of water inside chimneys. However generally leaking flashing is easily noted by inspection and via looking inside attic area where roofline interior meets flashing/chimney. If flashing you should see old staining, spalling/cracking of mortar, bricks, etc. If you have had melting snow on the roof, it will often pool water into leaking areas.
My advice would be to reline with SS asap, and possibly redo flashing or re-seal it. Once warmer retuck mortar as necessary, waterproof exposed areas, possibly recap or crown. It can get expensive and a handy DIY not afraid of heights can do many of these things, but also well worth getting a professional who mentions all these things.0 -
We have one fireplace (that we do not use). Never open or closed dampers. We have 3 cleanouts. One is in the basement (labelled 7 x 9), the other two are on the chimney inside the study. One is labelled 7 x 9; the other is labelled 10 x 12.icesailor said:That cap you have on the top of the chimney. Do you have two fireplaces and are those "top dampers" with the chain that hang down into the fireplace so you can open and close the dampers? Is the boiler flue coming up between the two flues? Do you have water running down and into the fire boxes of the fireplaces?
That house looks like a brick veneer on a wood frame. They used a Common Bond and there are no header courses to tie the wall together. And it isn't a Flemish Bond or any other bond that I know of. If it is just a veneer, there may be serious water damage occurring between the brick and the wood framing behind the chimney. You should have it attended to as soon as possible. Are you getting water stains on the sunroom ceiling where it meets the chimney yet?
I believe the boiler flue is running alongside the part of the chimney that seems most wet (it's also on the shaded side of the house) but not 100% certain.
Do we have water in the fire boxes? Very good question. The answer is no. And this is the main reason that most chimney companies have said that the water is not coming from inside. I have tried to look but hadn't thought of the mirror trick.
House structure description (from the inspection): Wall construction: wood frame; Masonly - brick. I don't know if that's what you mean by veneer. The house was built in 1954 and it's been described by several as "very well built" - for what it's worth.
Water stains on the sunroom ceiling where it meets the chimney: yes, exactly. That's how I first noticed the problem. (and everybody wants to fix the roofing on the sunroom hence...).
As soon as possible: I agree!! But I've had at least 2 contractors come and tell me to call them back in late March because this is not a good time of the year for this kind of work and "not to worry" that with the frozen weather there shouldn't be much more leaking... contrary to all evidence, of course.
Thanks for your advice.
0 -
Mirror idea I hadn't thought of. I might try that (though hard to see without light!)conversiontime said:Do you have an old cleanout that will allow you to look into the chimney from the basement--if so use a mirror to look up there to look for water dripping to confirm. NG exhaust definitely has lots of acidic water vapor in exhaust, whether enough to make that sort of staining, I am not sure. That looks to be quite a bit of moisture leaking all along the flueway.
I have two brick chimneys, both clay lined flues in good shape. One is unused (fireplace) and the other vents the boiler only. During conversion I did use SS liner even though not required by code in my area for reason stated above. So far it has done well and during cold snaps you will see lots of frozen ice near the cap and running down the immediate bricks, so yes lots of water vapor. But I have also done lots of water repairs to the chimneys as they do need good caps/crowns, tight flashing and where exposed a chimney specific water repellent (allows moisture to breathe out). These all make a huge difference.
I haven't seen any water dripping into the basement or unused fireplace - which is why most contractors have dismissed the condensation as the likely culprit. I am unconvinced, which is why I am posting here.
About the amount of moisture - yes, I agree. I suppose it is possible that crown or flashing up on the main roof may be also involved and letting that condensate and/or rain to trickle down. Tricky time of the year - contractors seem a little reluctant to work on this right now (January in Connecticut).
Thoughts on immediate steps?
1) Install flue. Wait and see or
2) repair flashing at the same time?
Thanks for your thoughts on the matter.0 -
Yes that seems large for 2300 Sq Ft but I can only guess from here.delenca said:
Are you suggesting it's way too much for the house? I believe it was sized roughly based on the size of the house (~2300 sq ft) but I don't know how carefully. Can you give me some roundabout numbers for short-cycling? I haven't been on the lookout for that and haven't noticed anything too dramatic. The temperature tends to hold fairly reasonably (the house has new windows and retains heat well).pecmsg said:The 306B has a heating output of 146,000BTU’s who sized this unit?
During last week’s cold spell did you notice any short cycling of the boiler?
Thank you for the advice.
-Alex
Somehow I guess the contractor never did a Manual J calculation for the house to size the boiler. Next time it gets to single digits outside the boiler should run almost all the time. If it cycles on and off good chance its oversized.
Again guessing from here but I think you need a liner installed.
0 -
A roof/chimney inspection should confirm, but it could have two or even three flues in one chimney so likely the fireplace has its own flue and the boiler vent has its own. That is probably why no water in fireplace, but based on picture the left side as facing the chimney is likely where the boiler venting runs.
yes line with SS asap, you should check and/or reflash top and of course that sunroom area looks bad, likely asphalt patched over flashing. There are flashing products like flash seal that work better than tar if you just want to seal the flashing it until next roofing. I used flash seal on on chimney 5 years ago and still holding up well.0 -
FWIW: An snarkyness in any comment by me isn't pointed at you.
I worked until I retired in an extremely isolated location. If you wanted someone else, you probably wouldn't get someone else. They had other things to do. Most all "Old Timers" had to be multi-talented and had the skills to multi-task any situation. Today, in the age of specialization, many carpenters don't know how to use a 16 oz. claw hammer and pull a nail with it. When people have a leak, they call the Plumber. I once had a call from a customer that had a water leak on his second floor bathroom ceiling. There was no bathroom above the ceiling, just the roof. Supposedly, a "roofer" couldn't find any leaks. I carry a pair of binoculars on my truck for such emergency's. Is that guy over there have a fish on? Is that hot pink bathing suit have a good looker inside? Does that rubber boot on the copper flashing on the 3" roof vent have a split from the Sun? Why yes it does. Get your blind roofer to change the flashing.
99.99999999999999999% of all water leaks through a ceiling with a bathroom above, and intermittent water coming through a ceiling is water leaking somewhere around a tub. IT IS NOT A BROKEN PIPE!!!!!!!!!!!!!. But some Carpenters are bound and determined to prove themselves right. And when there is no leak to be found, they call the plumber. Who becomes the @$$hat for pointing out all the places that the water was getting through the floor around the tub. And someone has to patch or replace a perfectly good ceiling. Like the museum like hotel where the maintenance guy went looking for the water leak in a ceiling with 3/8" rock lath with 1/2" OD copper stapled to it, 3/4" if structolite brown coat plaster and hard finish lime plaster, with a sharp wood chisel. Amazing how much water came out of that little hole.
Ask those Mason's if they grew up in Florida where it is a parallel universe. Heat flows to cold, dampness flows to dryness. In New England and the rest of the world. In Florida, it's the opposite. In New England, Dampness flows to dryness, heat flows to cold. Which in my experience means that the warm moist exhaust gasses from the boiler are flowing outward. From the inside of the flue to the outside of the brick. Next thing, they are going to tell you that you need to "waterproof" the chimney by spraying silicone waterproofing on the outside of the chimney to stop the water from migrating through the brick. Great. Now, the water can't get out.
Then, there's your "plumber" or whatever he calls himself. There are 4 categories of venting for boilers Two are non-condensing, and the other two are condensing. We all learned about vent categories in the 1980's when they started coming out with fan assisted venting on gas boilers that had flue gasses that could or would condense. I went to a 4 hour Meet, Eat and Learn with Weil-McLain when they came out with their HE and VHE boilers that needed SS venting. In fact, it was at the same place that the guy put the hole in the radiant copper ceiling. Every installer should be knowing that if you switch from oil to gas, you need to run a liner. End of discussion. The manufacturer told your installer that in their I/O manual. Its important to RTFM, its even more important to understand what it says.
The longer that runs like that, the more damage is being done. The brick mortar is being broken down by the acid in the flue gasses. Depending on the type of brick, the brick can be breaking down. Those aren't "water struck" brick which are harder than the tar road. 1956 means they are some form of local bank run clay fired brick. If and when the sun comes out, does the area around the chimney dry out and have white fluffy edges? If so, you will need to take a garden sprayer and mix some white vinegar or muriatic acid to get rid of it, and get some waterproof company to waterproof the side of the house. On the off chance that there is something wrong with some flashing, it isn't the cause of your problem.
You need a liner as soon as possible. Make sure that it is sized properly. Someone in your area can do a proper job.
Don't get cheap. You get what you pay for.0 -
Thanks for the feedback and info.conversiontime said:A roof/chimney inspection should confirm, but it could have two or even three flues in one chimney so likely the fireplace has its own flue and the boiler vent has its own. That is probably why no water in fireplace, but based on picture the left side as facing the chimney is likely where the boiler venting runs.
yes line with SS asap, you should check and/or reflash top and of course that sunroom area looks bad, likely asphalt patched over flashing. There are flashing products like flash seal that work better than tar if you just want to seal the flashing it until next roofing. I used flash seal on on chimney 5 years ago and still holding up well.
1)
Yes, fully agree. The fireplace and the boiler vent to different flues. I looked up into the fireplace flue and it looks, to my eye, clean as a whistle. The boiler vent I can't see (and there's no clean-out) - b/c it's connected to the exhaust. We'll see what the Chimney company that's coming this afternoon says.
2)
Flash seal: thanks; yes, that's my goal.
0 -
It was fairly cold last night (~9-10 F). Inside the house thermostat set at 62oF o/n. I turned thermostat up to 68oF around 6AM (when it was still very cold) and the boiler raised the temperature gradually from 62-68oF over a period of maybe ~30-45 min or so. It did not feel excessively quick to me.pecmsg said:
Yes that seems large for 2300 Sq Ft but I can only guess from here.delenca said:
Are you suggesting it's way too much for the house? I believe it was sized roughly based on the size of the house (~2300 sq ft) but I don't know how carefully. Can you give me some roundabout numbers for short-cycling? I haven't been on the lookout for that and haven't noticed anything too dramatic. The temperature tends to hold fairly reasonably (the house has new windows and retains heat well).pecmsg said:The 306B has a heating output of 146,000BTU’s who sized this unit?
During last week’s cold spell did you notice any short cycling of the boiler?
Thank you for the advice.
-Alex
Somehow I guess the contractor never did a Manual J calculation for the house to size the boiler. Next time it gets to single digits outside the boiler should run almost all the time. If it cycles on and off good chance its oversized.
Again guessing from here but I think you need a liner installed.
Liner: yes, that's what I'm leaning to. One more inspection this afternoon. Hope it will be "cut and dry" - pun intended - and can get this addressed asap.
This morning when I left the house, the chimney did not look as grim. It's been dry for 2 days and very cold. Perhaps the moisture on the brick is frozen?0 -
The question is whether the moisture is coming in from the outside or inside.
Brick is very porous... water can soak thru bricks, mortar and masonry chimney caps (read story below). Chimneys or any brick surface for that matter should be treated with a water sealant (usually every 10yrs or so). Rain can also go right down the flue if you’re missing a chimney cap (metal/decorative). Any cracks (bricks or chimney cap) or recessed/missing mortar (joints) can let water in and should be fixed and later sealed. Flashing is another problem area. Not just the flashing, but also how its attached and sealed to the chimney and surrounding roofing.
Gas boilers do produce condensate and it can accumulate inside the chimney/flue. Have you gotten a lot of rain recently?
As far as lining the chimney, I live in CT too, my understanding with a gas boiler or WH vented thru a masonry chimney needs lining. Hell, they want a liner now for a wood burning insert even if its clay tile lined. I would call your town/local building inspector and ask. Mine has been very helpful with all the DIY work I've been doing.
Story:
My house, built '56, and recently had the roof done. A couple of months ago we got a lot of rain (major downpour for 4-5hrs straight). I came home to work on the house and saw the chimney bricks & cement blocks were wet all the way down from the roof-line to the mantle.
The reason I could see it was we were in the process of insulating (drywall ripped out). I thought it was the flashing around the chimney. I knew the chimney needs repointing... I just didn't figure that much water could absorb thru the brick.
Sure enough, I wrapped the chimney with a tarp and its been drying since (i.e. weeks later it was still damp). Since then its rained and no more visible water.0 -
Yes, several have suggested a waterproofing products that "breathe". Others have said can't do this now as we'll trap the water. Not sure who to believe.icesailor said:In New England, Dampness flows to dryness, heat flows to cold. Which in my experience means that the warm moist exhaust gasses from the boiler are flowing outward. From the inside of the flue to the outside of the brick. Next thing, they are going to tell you that you need to "waterproof" the chimney by spraying silicone waterproofing on the outside of the chimney to stop the water from migrating through the brick. Great. Now, the water can't get out.
Ok, this is a point I'm going to revisit with the installer. On the other hand, TFM hides that statement way deep in the manual and Burnham refuses to confirm or deny my question about whether it's required or not ("only speak with technicians"). What the hell?!
Every installer should be knowing that if you switch from oil to gas, you need to run a liner. End of discussion. The manufacturer told your installer that in their I/O manual. Its important to RTFM, its even more important to understand what it says.
Yes, I have the white stuff that's typical of water marks. I don't know if that's what you mean but I'll take a look at cleaning that before any waterproofing is done.
The longer that runs like that, the more damage is being done. The brick mortar is being broken down by the acid in the flue gasses. Depending on the type of brick, the brick can be breaking down. Those aren't "water struck" brick which are harder than the tar road. 1956 means they are some form of local bank run clay fired brick. If and when the sun comes out, does the area around the chimney dry out and have white fluffy edges? If so, you will need to take a garden sprayer and mix some white vinegar or muriatic acid to get rid of it, and get some waterproof company to waterproof the side of the house. On the off chance that there is something wrong with some flashing, it isn't the cause of your problem.
You need a liner as soon as possible. Make sure that it is sized properly. Someone in your area can do a proper job.
Don't get cheap. You get what you pay for.0 -
That's an interesting point. The problem became visible (in the sunroom) after a significant rainy day 2 months ago (December 12th).bmwpowere36m3 said:The question is whether the moisture is coming in from the outside or inside.
Brick is very porous... water can soak thru bricks, mortar and masonry chimney caps (read story below). Chimneys or any brick surface for that matter should be treated with a water sealant (usually every 10yrs or so). Rain can also go right down the flue if you’re missing a chimney cap (metal/decorative). Any cracks (bricks or chimney cap) or recessed/missing mortar (joints) can let water in and should be fixed and later sealed. Flashing is another problem area. Not just the flashing, but also how its attached and sealed to the chimney and surrounding roofing.
Gas boilers do produce condensate and it can accumulate inside the chimney/flue. Have you gotten a lot of rain recently?
As far as lining the chimney, I live in CT too, my understanding with a gas boiler or WH vented thru a masonry chimney needs lining. Hell, they want a liner now for a wood burning insert even if its clay tile lined. I would call your town/local building inspector and ask. Mine has been very helpful with all the DIY work I've been doing.
Story:
My house, built '56, and recently had the roof done. A couple of months ago we got a lot of rain (major downpour for 4-5hrs straight). I came home to work on the house and saw the chimney bricks & cement blocks were wet all the way down from the roof-line to the mantle.
The reason I could see it was we were in the process of insulating (drywall ripped out). I thought it was the flashing around the chimney. I knew the chimney needs repointing... I just didn't figure that much water could absorb thru the brick.
Sure enough, I wrapped the chimney with a tarp and its been drying since (i.e. weeks later it was still damp). Since then its rained and no more visible water.
It's been dry for 2 days (the 1st picture was on a rainy day) and very cold (~10-25 F). This is what the Chimney looks like today:
0 -
To insulate or not to insulate?
Company on the job right now agrees: problem is lack of liner. They're running the numbers right now. The cost is higher than I've been quoted before. Mostly due (according to him) to the need to insulate between liner and the brick - to prevent corrosion to the stainless steel down the line from further condensation in the future. Thoughts?0 -
As far as moisture getting in from the outside... for sure your chimney should be inspected. Masonry chimney caps repaired if cracked and mortar joints repointed if needed. Then a sealer can be applied. As far as when best to apply, I would defer to the manufacturer of the sealant.delenca said:
That's an interesting point. The problem became visible (in the sunroom) after a significant rainy day 2 months ago (December 12th).bmwpowere36m3 said:The question is whether the moisture is coming in from the outside or inside.
Brick is very porous... water can soak thru bricks, mortar and masonry chimney caps (read story below). Chimneys or any brick surface for that matter should be treated with a water sealant (usually every 10yrs or so). Rain can also go right down the flue if you’re missing a chimney cap (metal/decorative). Any cracks (bricks or chimney cap) or recessed/missing mortar (joints) can let water in and should be fixed and later sealed. Flashing is another problem area. Not just the flashing, but also how its attached and sealed to the chimney and surrounding roofing.
Gas boilers do produce condensate and it can accumulate inside the chimney/flue. Have you gotten a lot of rain recently?
As far as lining the chimney, I live in CT too, my understanding with a gas boiler or WH vented thru a masonry chimney needs lining. Hell, they want a liner now for a wood burning insert even if its clay tile lined. I would call your town/local building inspector and ask. Mine has been very helpful with all the DIY work I've been doing.
Story:
My house, built '56, and recently had the roof done. A couple of months ago we got a lot of rain (major downpour for 4-5hrs straight). I came home to work on the house and saw the chimney bricks & cement blocks were wet all the way down from the roof-line to the mantle.
The reason I could see it was we were in the process of insulating (drywall ripped out). I thought it was the flashing around the chimney. I knew the chimney needs repointing... I just didn't figure that much water could absorb thru the brick.
Sure enough, I wrapped the chimney with a tarp and its been drying since (i.e. weeks later it was still damp). Since then its rained and no more visible water.
It's been dry for 2 days (the 1st picture was on a rainy day) and very cold (~10-25 F). This is what the Chimney looks like today:
I think it would be best applied when the masonry is "dry", outside temps reasonable and at least a couple days without rain after application. The sealant waterproofs the masonry, but it still allows it to “breathe”. Personally I wouldn’t apply it to “soaked” masonry.
With respect to the liner, consult a few contractors, ask the boiler manufacturer (sometimes you need to speak to a technical representative) and confirm with local building codes.
I always thought the liner was due to the pH content of exhaust fumes and condensation affecting the integrity of masonry chimneys. I’m surprised the “wet” chimney is solely due to the boiler fumes. Mine looked like that but it was down pouring for two days….
Insulating the liner I think has to due with venting (keeping fumes hotter, so they rise) and not so much corrosion… it’s stainless right? I think insulating a liner is important if you have an exposed chimney (runs along the outside of the house) and not so much when it comes thru the house (interior).0 -
Insulated liner is ideal for exterior chimney but much depends on existing clay liner--if still in good shape (hard to say based on seeping) then the insulation is not necessary. In my case I needed a large liner b/c of boiler size and the liner with a wrap would have not fit in the existing clay liner. FWIW I live in area where temps of -25F are not unusual and I have had no issues with uninsulated SS but the size of the boiler and draft negate the need in my case.
Regarding corrosion, make sure the SS liner is type (e.g 316) ,that matches your fuel being burned, this is best preventative but as contractor mentioned, insulating would be the ultimate addition if you can afford it. And again once summer rolls around have the chimney crown, mortar and flashing looked at closer.0 -
"" I think it would be best applied when the masonry is "dry", outside temps reasonable and at least a couple days without rain after application. The sealant waterproofs the masonry, but it still allows it to “breathe”. Personally I wouldn’t apply it to “soaked” masonry. ""
I didn't know that Gore-Tex was making a breathable water proofing for bricks.
1 -
I'm not referring to a tar based or paint sealer. It's a liquid that is sprayed on and absorbs into the masonry and creates a protective film below the surface of the masonry. It still allows moisture/vapor to permeate out and in. Like drylok for basement walls...0
-
I'm under the impression that when the dew point is reached, water will condense. The old boiler vented out hotter air, kept the chimney warm [ above the dew point]. The CONDENSING boiler pushes out much cooler air, & into an outside chimney. There is no way that chimney can stay warm enough in CT. to prevent condensation. The picture tells it all. Fix the problem not the symptom. Line it, & be sure there is a condensation pump to get rid of what is still going to happen inside of that liner.1
-
Adding the insulation adds about $800. The chimney runs along the side of the house.
However, the type of insulation is poured "chim mix". I asked why and he said something like "the only way to get insulation in there". Uneasy about poured insulation (down the line, if there's a problem how much of a mess is that going to be?).
We're in CT, where it gets cold, so I'm getting the feeling that insulation is probably the right move (costs more now but hopefully prevents expensive damage later).
The 1st contractor had not recommended insulation and had priced me a 5.5 inch liner (he said "he's allowed a .5 inch step down" - which I'm trying to check with town inspector). He said when I asked him about the insulation that the "84% efficiency gas boiler" should probably not throw out so much water that it requires insulation but he could also price the poured insulation but that it requires a certain temperature for pouring.
So, the main questions are:
1) Thoughts about poured insulation?
2) Is the step-down liner quote a bad sign for that contractor (the overall quote of this contractor would be ~$300 less).
Thanks for your help.
-Alex0 -
Has not a single one of these people done the calculations to see if your projected 5.5" corrugated SS flue liner can handle the output of your boiler? A flue size too small is as bad as one that is too big. And it being a 3 sided outside chimney is a factor. There is no official registration or instruction requirements for people dropping flue liners in. The person who installed the gas piping for the boiler is responsible for the venting.
If you have a really bad belly ache, you don't go to a podiatrist to have them trim an ingrown toenail.
The input of the boiler, and the length of the flue determine the size of the liner. Not too big, not too small, but just right. Especially for a condensing boiler. Which that is.
I will suggest that Burnham and other boiler manufacturers are having such a time with this problem of improperly vented equipment, that on advice of counsel, they won't even tell the Pro's what to do.
Or, as my old dead boss once said, "When you get to this level, you're supposed to know what you are doing".0 -
Calculations were not shared with me. Both contractors are well rated (on Angie's list and BBB and yelp).icesailor said:
The input of the boiler, and the length of the flue determine the size of the liner. Not too big, not too small, but just right. Especially for a condensing boiler. Which that is.
Looking at specs for the 306B model in the model, it comes with a 6 inch vent. The manual states in the Venting Appendix that:
"DO NOT REDUCE THE DIAMETER of the vent connector between the boiler and the chimney. It must not be smaller than the outlet on the draft hood, damper, or vent reducer supplied with the boiler."
But that's only about the vent connector. It doesn't say anything about the liner dimensions.
Actually, I suppose I have enough information now that I could do the calculations myself.
The 306B has a heating output of 146,000BTU. It's fan assisted.
The chimney is 28 feet tall. Exterior.
The proposed liners are either 5.5 inch or 6 inch.
I did a quick google search for an appropriate calculator but didn't get much further.
0 -
"" Calculations were not shared with me. Both contractors are well rated (on Angie's list and BBB and yelp). ""
That and a 5 dollar bill (includes the tip) will get you a Venti coffee at Starbucks. Doesn't include a muffin.
No matter how many times they did the calculations, the manufacturer says that it must be a lined chimney because of corrosion. We've known that since the 1980's.
http://www.michiganair.com/newsletters/2007-3/section1.htm
You have a category 2, natural draft, condensing boiler. When it was switched from oil to gas, it was required to be lines with an approved type of liner that was corrosion resistant of the proper size.
As far as Angie's list, you pay to be listed. All it takes is for some disgruntled customer to put the bad mouth on you and you're toast. For example, if I (or someone else) told you that needed to line the chimney if you went from oil to gas and what it would cost, and you spoke with ABC heating and he told you that I/we are full of ships and you didn't need any stinking liner and I/we were trying to screw you, you might get mad and post me/we on Angie's list.
Your problem is so bad, that in Massachusetts, we had 2 hours of a 3 hour CEU to keep our licenses, just on venting gas appliances. And that is a 6 hour course that we have to do every year to keep our licenses. 3 hours on gas, 3 hours on plumbing.0 -
A riddle! I think I might be too tired to glean your meaning... :-)icesailor said:"" Calculations were not shared with me. Both contractors are well rated (on Angie's list and BBB and yelp). ""
That and a 5 dollar bill (includes the tip) will get you a Venti coffee at Starbucks. Doesn't include a muffin.
In case you are suggesting not to take those ratings too seriously - true, I look on them on wearily. Though if I see a high volume of good ratings I am more likely to trust them. Also I've had several neighbor recommended chimney/mason contractors come out and they haven't been much more helpful - the divergence of opinions of steps to take is astounding.
Yeah, there's no question I'll do the liner at this point. Although it will still take ~2-3 weeks for material to arrive and for job to be done at the earliest - which is frustrating. I want the job done last week.
No matter how many times they did the calculations, the manufacturer says that it must be a lined chimney because of corrosion. We've known that since the 1980's.
Further, I have NOT pulled the trigger yet b/c I'm still trying to figure out if insulation is the correct choice (for the extra $800).
From what I'm reading and from the characteristics of the situation (external chimney, CT winter) I think insulation is probably the safer bet and may save money and aggravation in the long run.
Once bitten, twice shy - I am trying to do as much due dilligence as I can. Hence I appreciate everybody's help and feedback on the forum.0 -
Thanks for the information!icesailor said:""
http://www.michiganair.com/newsletters/2007-3/section1.htm
You have a category 2, natural draft, condensing boiler. When it was switched from oil to gas, it was required to be lines with an approved type of liner that was corrosion resistant of the proper size.
I looked through it. How do you determine that my boiler is a category 2, condensing boiler?
I ask because my boiler is not listed as a "condensing boiler" in the Burnham's literature. i.e. Burnham Gas Boiler Series 3, 84% AFUE section of
http://www.hvacforlife.com/boilers-hydronic-heating/gas-boilers/burnham.html
It says, "In most cases, simply connecting the Series 3 to the home's existing chimney is all that's required (vent system MUST comply with NFPA-54 Venting Code and all applicable codes)."
Of course, the "most cases" and "must comply with applicable codes" gives them wiggle-room here.
Basically, I'm curious how I can go back to the installer armed with specific information that states unequivocally that they messed up the venting. (besides the "proof is in the pudding" images of 75% blocked flue and white marks of water damage from yesterday - see below).
Thanks!0 -
"" That about says it all. The I/O manual says not to connect it to a clay tile chimney because of condensation issues. The clay tiles are now destroyed by the acid in the flue gasses. ""
This says it all for Burnham. That absolves them of any errors on the installers part. Without going back to find the Burnham boiler I/O manual, someone posted a link to it.
This is not a new issue.
When you take your automobile to the dealer, they have a well trained staff of mechanics that have certified factory training, and the computers to diagnose problems. We as professionals have a responsibilities to ourselves and our customers to be up with the current regulations.
We've known this for 20 years. How many jobs did I not get because the chimney needed to be lined, and the low bidder said it wasn't necessary on conversion from oil to gas. They were wrong.
What's happening to your installer was my greatest fear if I did what he did. Who is going to be responsible.
The stuff blocking the flue in the first photo is from the clay tiles dissolving from the acid eating away at the clay in the tile. The yellow stuff on the round flue pipe is sulfur. The yellow stuff mixes with water to create sulfur dioxide. Which causes marble statues in the park to deteriorate.
I've seen worse. Burning creosote lumber in wood stoves.
Read this:
http://www.duravent.com/docs/product/L1039_gas_bltn_June2011_web.pdf
1 -
One contractor I spoke with over the phone told me to smell the wet spots in the sunroom and to see if I could detect a faint smell of H2S. It's faint but I believe I smell it... (I have CO detectors everywhere and that seems to be ok (for now)).icesailor said:""
The stuff blocking the flue in the first photo is from the clay tiles dissolving from the acid eating away at the clay in the tile. The yellow stuff on the round flue pipe is sulfur. The yellow stuff mixes with water to create sulfur dioxide. Which causes marble statues in the park to deteriorate.
I've seen worse. Burning creosote lumber in wood stoves.
Read this:
http://www.duravent.com/docs/product/L1039_gas_bltn_June2011_web.pdf
I wonder if the large blockade was reducing the draft so much as to make the situation much worse? i.e. I'm hoping I bought myself some time when the block was cleared? (it looks like the earliest anybody can install the liner is another 2-3 weeks).
Reading material - YES! That's what I was looking for. Very informative. Thank you so much.
Wish you'd be around here 2 months ago when the problem started and before I contacted 6 different contractors with 6 different agendas, noone aligned with my immediate needs.
Thanks a million.
Of course, I've been waiting since the morningg for the 2 contractors who've quoted me liners + inspectors to get back to me so we can get this process started...0 -
In a word, YES. That boiler is at least twice as big as you need, and quite likely more like 2.5-3X. Between that and the improper venting job which has clearly caused damage to your house, I would suggest that you hire a very competent contractor or a consultant to quantify all this. A carefully worded letter to the original installer with a copy to his liability insurance carrier would be the next step.delenca said:
Are you suggesting it's way too much for the house?pecmsg said:The 306B has a heating output of 146,000BTU’s who sized this unit?
0 -
Back in '91 when the efficiency minimums went to 78% on gas equipment, from about 60% prior to that, lining really became an issue. Over the years, subsequent issues of NFPA 54 became more and more stringent as to the requirement for liners, and with good reason. I was the rep for Z-Flex and Metalbestos at that time and we did a ton of training and encountered much resistance, notably from the utilities. There was just no getting around the facts and they finally embraced "the right way"
I think you should contact a chimney sweep certified by the Nat'l Chimney Sweep Guild. They are not afraid to get up on a roof and that is where this first inspection should take place. That is where the chimney will be in the worst condition.
Your original contractor is a nitwit. I wish I could phrase it more delicately, but I just read the whole thread so I feel entitled to call a spade a spade. The likelihood of an exterior chimney not condensing is ZERO. Apparently the Manuf agrees.
Yours looks like a straight up and down flue. Yes? I would look at a system from Dura-vent called Duraliner. It is an insulated liner and may fit without a lot of hassle. I have had it in my home before and it is a really good product from a good company. Personally I do not like poured in loose insulation. I once went out on a call where the damn holding the insulation popped and the living room was full of...well, you get the idea.
One of the best things you can do for system operation is to have an insulated vent connector from the boiler to the flue. You can probably go onto Z-flex'es site and find a calculator for sizing the liner diameter. The taller the flue the smaller the diameter can be.
We, the industry, are over 25 years into this "issue" as Ice has correctly pointed out. You can just hear the frustration coming out of him that this is not universally understood. Rightfully so, I might add.
You may not get Burnham to discuss this over the phone with you, but they do have a local rep. Find out who he is and have him come out with the original contractor. That is his job. When there are issues he needs to know and should pin the tail on the donkey. These are almost always unpleasant calls, believe me, I know, but a lot of good should come from it. Burnham is a good company. I understand that they are even making boilers today that hold water.
Another thing! It is likely that you had condensation issues with this flue with the prior system. Oil/gas, the physics are the same as to dew point. Exterior chimneys are the worst.
In fact in todays world, a masonry chimney is an excellent architectural device but a terrible mechanical device. 11th century technology venting 21st century appliances.
After this one, I need a drink. Oh, no, it's January. I'm on the wagon!1 -
Thank you all.
I signed a contract to have a liner installed 1st week of February. Insulation will be chim-mix. I asked some questions about it (also a bit leery of the poured insulation) - contractor says the poured insulation has worked well (sets into a cork-like consistency) and it works well here b/c the flue is not exactly vertical. I can try to insist for a different type of insulation if everybody here were to say the poured is a terrible idea but frankly just ready to get this job done and haven't seen anything terribly scary about the poured type of insulation so far. The chim-mix adds ~$800 to the cost. If you tell me of a good insulated liner that doesn't cost an arm and a leg (liner will be 28 foot, 6 inch), I can try to push contractor accordingly.
In any case, good idea to try to contact the local Burnham rep. I will try to put a package together to show the installer. Not sure what I can expect/demand from installer but I will certainly let them know I will report them? What do you expect installer might do in return?0 -
""" Yours looks like a straight up and down flue. Yes? I would look at a system from Dura-vent called Duraliner. It is an insulated liner and may fit without a lot of hassle. I have had it in my home before and it is a really good product from a good company. Personally I do not like poured in loose insulation. I once went out on a call where the damn holding the insulation popped and the living room was full of...well, you get the idea. """
Duraliner might be cheap at twice the price.
The installer may not know about this product, or have never dealt with it. We all fear the unknown. The installer may find out that this product is better than sliced bread. Or like the description of pure quality that Richard Pryor describes in the movie "Silver Streak" with Gene Wilder and Jill Clayburg.
0
Categories
- All Categories
- 87K THE MAIN WALL
- 3.2K A-C, Heat Pumps & Refrigeration
- 58 Biomass
- 427 Carbon Monoxide Awareness
- 113 Chimneys & Flues
- 2.1K Domestic Hot Water
- 5.7K Gas Heating
- 109 Geothermal
- 161 Indoor-Air Quality
- 3.6K Oil Heating
- 70 Pipe Deterioration
- 995 Plumbing
- 6.3K Radiant Heating
- 391 Solar
- 15.4K Strictly Steam
- 3.4K Thermostats and Controls
- 55 Water Quality
- 44 Industry Classes
- 48 Job Opportunities
- 18 Recall Announcements