HELP! 1" Pex over concrete slab its cold want to optimize heat transfer

1" Pex mounted on side of 2x4 runners bolted into concrete floor through panels of DOW TUFF R reflective foam insulation board. The subfloor sitting over the Pex is 4x8 sheets of 22/32 engineered ply. Total 2400sqft pushed through by Two 50 gallon electric Water heaters with an expansion tank pumping 70/30 water to glycol. I dont know enough about the pump offhand if thats critical I will look into it with more detail. Guages report steady movement.
THE ISSUE:
The heat is not impacting the 2400sq ft space enough. I suspect the wooden subfloor sitting over the pex may be too thick to allow the heat to transfer adequately. I read somewhere that reflective panels installed in the cavity under the pex to spread heat do not work overtime due to dust buildup on the plate. Would a passive floor grates improve the situation.
THE KICKER:
I was in a car accident while preparing this studio for use. I trusted my landlord to manage the project in my absence. I suspect he sandbagged my floor intentionally into his space to prevent me from ever taking out the materials ( even though I own it by the terms of the lease ) by having the carpenters glue down the plywood subfloor onto the 2x4's. I know it is common to glue down subfloors to prevent excessive movement but not when heated tubes are under it. Am I being paranoid or did this guy just use a detail of the install to force me to leave the floor in place. He did place access panels where the pex is coupled. I would never have glued it down just in case there was some accident and I needed to get into the floor. I am suspect of this choice of his which he never happened to mention to me and which I would not have discovered had my upstairs neighbor not had a spill into my space that made me want to pull up some ply. What say yee experts who made it this far down the line?
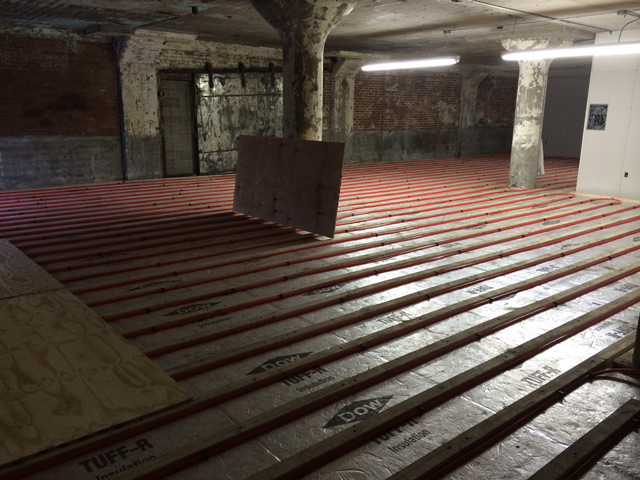
Comments
-
I would like to see a better picture of the floor detail. I don't think I like what I see.
That system will fail miserably if that tubing is not up against your subfloor with plates. The reflective foam has zero effect for reflecting radiant energy if that's why you used it.0 -
What you have is suspended tube 16" on center. And a heat source probably lucky to get 140 AWT. Plus your using glycol. Don't know the floor coverings either0
-
I agree with Gordy. I'd much rather see 2 1/2" pex runs in each bay and pour lightweight between the sleepers. Or, plywood sleepers set up to accept U-Fin transfer plates. I highly recommend not putting down the finish floor. The subfloor is not the problem. The lack of a proven radiant panel is.Steve Minnich1
-
I totally agree that the lack of heat transfer plates and the 16" OC spacing is one major problem.
The other is your choice of heating equipment. An electric water heater with a 4.5kw element has an out put of 15k btu's. With two of them, you've got 30k btu's. Your heat loss is probably close to twice that much at design temp.
Who designed this? Was an accurate heat loss calculation done?
The only simple thing that can be done short of tearing up the floor is to get a heat source with adequate output and crank the supply temp up high enough to get enough output from the floor. The down side to that is that running water temps too high can damage the floor.
There's no easy fix for improper design.Bob Boan
You can choose to do what you want, but you cannot choose the consequences.6 -
Is that a work space? Any ventilation?
2 electric water heaters provide 30,000 BTU's.0 -
I guess even the low bidder can make it look nice to the untrained eye.0
-
So long story short this floor is FUBAR and I should just suck it up and get an air blower to supplement . If the panels of ply were not glued down I would consider pulling them up and attempting to ad reflective aluminum as it stands its all glued down.. FFS what a train wreck.
0 -
it will move some heat, maybe enough for mild to medium cold days. you need a load calc to get an exact answer.
With 1" pex you need some pretty good flow rates to provide 2-4 fps to get air out and assure turbulent flow. What pump and how long of loops?
With enough electrical power you could get 60,000 BTU/ hr from two tanks with both elements firing. 72,000 BTU/hr if you stepped up to 5.5KW elements.
But the bottleneck may be the tube spacing and heat transfer. consider it a floor warming systemBob "hot rod" Rohr
trainer for Caleffi NA
Living the hydronic dream0 -
Wow , and no happy ending ! What a shame .You didn't get what you didn't pay for and it will never be what you thought it would .
Langans Plumbing & Heating LLC
732-751-1560
Serving most of New Jersey, Eastern Pa .
Consultation, Design & Installation anywhere
Rich McGrath 732-581-38330 -
Keep in mind the higher the r value floor covering the less the return on the heating if you intend on trying to get a little out of it.
Conduction is king . Reflective is not a good term to use or apply in transferring btus to a surface enough said.0 -
I've never heard of it being done but would it be possible to drill a hole at each end of the bays and pump a gyp slurry into them to fill the void and give mass and contact?0
-
I get the impression the OP was attempting to do a temporary install that could be removed later on when they moved out of the space.0
-
Rob that's not a bad idea, but I think it would take more than a hole on each end of each bay. That, and the tubing is still 16" on center.0
-
That's a good idea Rob, but only if the subfloor is an Advantec product or equal. If it is regular plywood it will absorb to much moisture and buckle.0
-
This is exactly what I was thinking after all the responses. drill holes every five or ten feet for each run. Pump in some sort of cement that would improve conduction and retention allow it to cure. avoid the hell of removing glued down panels.RobG said:I've never heard of it being done but would it be possible to drill a hole at each end of the bays and pump a gyp slurry into them to fill the void and give mass and contact?
0 -
Just a note about the common misconception that something reflective will reflect heat rays: reflection works with light rays which can be converted to heat. HEAT rays are NOT light rays and reflection does little or nothing to get them aimed back up through the floor. The common misconception that heat rays can be reflected back up through the floor has been the cause of many a failed radiant design.knucklekneck said:So long story short this floor is FUBAR and I should just suck it up and get an air blower to supplement . If the panels of ply were not glued down I would consider pulling them up and attempting to ad reflective aluminum as it stands its all glued down.. FFS what a train wreck.
As Gordy said "conduction is king".
Bob Boan
You can choose to do what you want, but you cannot choose the consequences.0 -
It is regular plywood. wouldnt the plywood strt to dryout after a week or so of the cement curingHarvey Ramer said:That's a good idea Rob, but only if the subfloor is an Advantec product or equal. If it is regular plywood it will absorb to much moisture and buckle.
0 -
Not a chance. The plywood will dry out, yes, but it will stay convoluted forever.knucklekneck said:
It is regular plywood. wouldnt the plywood strt to dryout after a week or so of the cement curingHarvey Ramer said:That's a good idea Rob, but only if the subfloor is an Advantec product or equal. If it is regular plywood it will absorb to much moisture and buckle.
1 -
-
looking for an improved solution .. as it stands the floor is not cold to the touch but not warm either, the air is holding steady at 58 degrees with outside temps hitting 28 rest of the building unheated.0
-
.0
-
Outside of tearing up the floor, and doing it right , or getting an actual heat source to give the water temps you need either through larger elements in the water heaters as HotRod suggested, or an actual boiler. That is it.0
-
Reflective foil?
I heard a sales person at the supply house, giving a presentation to the manager and a bunch of HVAC guys about how aluminized bubble wrap was equal to R-19 fiberglass batt insulation. They sold a lot of rolls of bubble wrap.
I never saw it work as advertised. But they sure sell a lot of it.0 -
As HotRod said, you could keep it to warm the floor, but you'll need something to supplement it.knucklekneck said:looking for an improved solution .. as it stands the floor is not cold to the touch but not warm either, the air is holding steady at 58 degrees with outside temps hitting 28 rest of the building unheated.
Panel rads, low temp baseboard or a fan coil(s) are the obvious solutions, but you'll need an adequate heat source to drive them.
Bob Boan
You can choose to do what you want, but you cannot choose the consequences.0 -
Going back to hotrods post.. here are more specs..
1 -
Off topic, but I just sit here wondering? How many millions of dollars in wasteful spending in our industry is a direct result of internet peddlers giving out misinformation in order to sell their wares. They put out incorrect diagrams and spec applications that don't have a prayer of working.
I guess that's why we need to give the RPA our full support. That way they can become the go to name for research in Radiant.
Harvey2 -
Your right Harvey, but then there are a never ending amount of people that just think radiant heat is as simple as throwing down a bunch of tubing, and feeding it with the cheapest heat source is all you need no internet required.......until it does not work. Sadly then when they find the right answers after searching......the Internet it's to late, or band aid fixes are all that can be done.
All I can say to people looking at this thread. Is all aspects of construction involve science, and calculations from the roof down to the foundation, and all mechanicals with in.
Millions? I think billions in the over all construction industry.
The Internet is a great tool to research anything of our hearts content. The problem is as Ice puts it the "cheap gene"over powers the mental drive to do things right, there is a cost.
As in this example reflective polyiso insulation costs more than xps. 1/2", or even 3/8" pex would have been plenty big for this installation at 12" on center or better yet 8". The addition of Plates would have made this installation a dream. Using two 50 gal water heaters may have been cut to one with a larger element, or a small electric boiler, along with many other options on the fire side if gas was an option.
To the OP I'm not coming down on you. It sounds like maybe you did not have total control of this project. My mumblings are said to people who hopefully are doing research here, and stumble on to this thread...... Before they start.1 -
My favorite shot as an example of the lack of conduction.
Or shall I say conduction to all the wrong contact points of the tubing in the cavity detail.
https://us.v-cdn.net/5021738/uploads/editor/0z/5w6j4rj62d8x.jpg0 -
I am not an expert nor was I on site for the construction. I was assured it would heat the space which it is technically doing but not adequately enough. It admittedly was a very cut-rate and fast installation and shortcuts were made to get the entire job in with labor and materials at 8500. So the short of it is this. Will a bigger pump help improve the flow? The image of the gauges on the output were taken when the pump was off. The system is actually moving 1GPM and the red indicators are at the midway mark. The saying goes, "You can't polish a turd." I may be spinning my wheels here but I appreciate the feedback and reality check. Given all of this new information I will likely remove the pex, water heaters, pump and valves and reinstall at a second location with improved CONDUCTION arrangement once I move to a new location.0
-
Enlarging the the circ will make little if any difference. That's the least issue that you have. It's in the middle of the btu train and you don't have anywhere near enough means to create enough btu's at the source or get rid of them at the point of delivery.
Each water heater has two elements that are internally wire so that only one can operate at a time. As HotRod pointed out, they can be wired to operate simultaneously, but the size of the electric circuit would have to be increased to each heater. This would double your btu production but not do anything for the floors ability to emitt those btu's. Raising the supply water temp will have far more benefit than anything else you can do as it will increase the Delta T between the tubing and the floor. Heat moves toward cold; the greater the temperature difference ( delta T), the faster it moves. Of course, there's only so much temp the floor materials can take.
On another note: what is the voltage being supplied to the water heaters? It appears you're in a commercial building of some size which means it would be supplied by a 3 phase electric service. A 3 phase Y connected service may only be supplying 208 volts, not 240. As noted on the water heater data tag, you only get 3500 watts @ 208 volts, not 4500 watts. That means instead of 15k btu's output, the water heater only has 12k btu's output.Bob Boan
You can choose to do what you want, but you cannot choose the consequences.0 -
At least electric resistance doesn't lose efficiency when running high temps the way combustion does.
You should seriously consider an electric resistance boiler. They're surprisingly affordable, even when you include outdoor reset control.
If you move, I wouldn't bother ripping out the PEX. Your time is worth far more than it would cost to replace with new, properly sized pipe. The pump is marginal, assuming it's exactly the size you need for the new space.
If you need more heat, I'd give some thought to adding an infrared radiant heater. Do you have gas available in the building?0 -
Honestly done right I really don't see a radiant floor as being portable other than the heat source, and associated hardware.
There is the option of added cost if head room allows of doing 3/8 pex with 1/2" plywood sleepers, and extruded plates over the top of the existing floor in place. Reuse existing manifold, and add another 6 loop set. Closer centers 9"- 12" would require more loops. Existing heat source still maybe questionable, but then no one did a heatload calc.......yet.0
Categories
- All Categories
- 87.1K THE MAIN WALL
- 3.2K A-C, Heat Pumps & Refrigeration
- 58 Biomass
- 427 Carbon Monoxide Awareness
- 113 Chimneys & Flues
- 2.1K Domestic Hot Water
- 5.7K Gas Heating
- 110 Geothermal
- 161 Indoor-Air Quality
- 3.6K Oil Heating
- 70 Pipe Deterioration
- 998 Plumbing
- 6.3K Radiant Heating
- 391 Solar
- 15.4K Strictly Steam
- 3.4K Thermostats and Controls
- 55 Water Quality
- 44 Industry Classes
- 48 Job Opportunities
- 18 Recall Announcements