Welcome! Here are the website rules, as well as some tips for using this forum.
Need to contact us? Visit https://heatinghelp.com/contact-us/.
Click here to Find a Contractor in your area.
American Standard A-3 Hydronic Boiler
Options
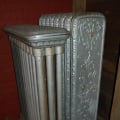
SALBuild1
Member Posts: 11
in Oil Heating
I have an American Standard A-3 hydronic boiler (circa 1954). When it was serviced last, the sheet metal flange that holds the burner on the front of the boiler was not secured correctly, in that it pinched the round access panel below the blast tube, so I can not clean out the burn chamber (and that round panel was wedged open, so the boiler has been running poorly). I need to remove the sheet metal flange and burner assembly to take off the round access panel. I have removed the two top bolts, but can not pull them out of the flange, nor screw them back in. I have not removed the bottom bolt yet.
My Questions:
Q1: Shouldn’t the bolts just come out? They screw into the cast iron boiler, yes?, so why can’t I screw them back in? AKA: How do I remove the flange and burner assembly?
Q2: There is a label stating not to use a vacuum to clean out the chamber, as it is Kaowool, so how do I get the carbon pellets out of the bottom?
The picture is sideways, with the flange to the left (the white blotch is the screw head- not a nut and stud), and the round access panel to the right, with the wingnut. I couldn't rotate the picture, it should be rotated 90 degrees clockwise.
Thanks for everyones help!
SALBuild
My Questions:
Q1: Shouldn’t the bolts just come out? They screw into the cast iron boiler, yes?, so why can’t I screw them back in? AKA: How do I remove the flange and burner assembly?
Q2: There is a label stating not to use a vacuum to clean out the chamber, as it is Kaowool, so how do I get the carbon pellets out of the bottom?
The picture is sideways, with the flange to the left (the white blotch is the screw head- not a nut and stud), and the round access panel to the right, with the wingnut. I couldn't rotate the picture, it should be rotated 90 degrees clockwise.
Thanks for everyones help!
SALBuild
0
Comments
-
What they probably did
was run bolts thru the cast-iron front plate and secure them with nuts. This is common when upgrading burners on older boilers. You'll have to remove the front plate from the boiler by removing the bolts at its perimeter.
That "cleanout opening" was actually a secondary air inlet, since the DH-series burners that originally came with these boilers were very finicky and sometimes needed secondary air. With a modern flame-retention burner this is not needed, and we generally close and seal them, since this extra air lowers efficiency.
The proper retrofit chamber for that boiler is a standard "bathtub" type made of Kaowool. The proper size depends on the exact boiler model. Not only does this make a very nice flame environment, but it doesn't use or need a secondary air inlet if used with a modern burner.
The burner will need to be tuned with a digital combustion analyzer after any repairs or modifications are made.All Steamed Up, Inc.
Towson, MD, USA
Steam, Vapor & Hot-Water Heating Specialists
Oil & Gas Burner Service
Consulting0 -
Job completed Successfully.
Thanks Steamhead.
I finally figured out that there were nuts on the back of the faceplate, by reaching my hand in through the viewing window, so I was able to tighten them down.
I also was wondering if that bottom round plate was an air inlet, but it has never been closed and sealed. I wonder if that is why we only have about 78% efficiency (and thus the reason that I want to replace the thing, as well as it being rated for 136 MBh in a 900 sq.ft house!- can't have too much heat in NH in 1954!)
Now with it running for 12 hours, I agree that it probably needs tuning, but given that I want to replace it this spring/summer, I'd rather put the money towards the new system.
It's still TBD- direct replacement boiler, condensing boiler or mod/con propane. Anyone know of a cost comparison calculator that takes into account boiler efficiency and fuel cost and BTU per fuel? There must be some on the web, but I don't even know what to search for.
This all started because the blower to pump coupler disintegrated. Thought it was going to be a quick replacement, and grew into "well, while I'm in there" quick cleaning- that made the job take me all day. But it's finished, and we have heat again....but I never did get the carbon granules out of the chamber.
Thanks again Steamhead for answering.0 -
comparison calculator
[Anyone know of a cost comparison calculator that takes into account boiler efficiency and fuel cost and BTU per fuel?]
Try the attached file.There was an error rendering this rich post.
0 -
-
Cost Calculator
Thanks Alan and Dan,
It will definitely help, but as a pdf, I can't actually use it (I can't input current data in the cells), so therefore Dan, can you just point me in the right direction as to where I can find it, or was there something wrong with the original link?
Thanks so much. This forum has helped me out many times, thanks Dan, for hosting it!0 -
There was an error rendering this rich post.
0
This discussion has been closed.
Categories
- All Categories
- 87K THE MAIN WALL
- 3.2K A-C, Heat Pumps & Refrigeration
- 58 Biomass
- 427 Carbon Monoxide Awareness
- 113 Chimneys & Flues
- 2.1K Domestic Hot Water
- 5.7K Gas Heating
- 109 Geothermal
- 161 Indoor-Air Quality
- 3.6K Oil Heating
- 70 Pipe Deterioration
- 995 Plumbing
- 6.3K Radiant Heating
- 391 Solar
- 15.4K Strictly Steam
- 3.4K Thermostats and Controls
- 55 Water Quality
- 44 Industry Classes
- 48 Job Opportunities
- 18 Recall Announcements