Welcome! Here are the website rules, as well as some tips for using this forum.
Need to contact us? Visit https://heatinghelp.com/contact-us/.
Click here to Find a Contractor in your area.
heat loss
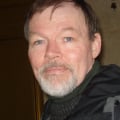
Brad White
Member Posts: 2,399
I can take this one on. Your points are well worth discussing but I would not take your points as a reason not to insulate. There are qualifications you are right, and these must be stated.
If the insulation is imperfect is is still better than not insulating at all. If your vapor barrier is not perfect (how could it be?) it is not as bad as it seems, in reality. This assumes you do not cook rice and spaghetti daily without ventilation and do not have a foil-wrapped house of course!
I agree in your pure sense about what can happen without vapor barriers. (I take it that you are in Canada where you really have vapour and a surplus of the letter "u". :)
Here are the qualifiers (and I live in an old meaning 1873 farm house in Boston). A few good coats of oil based paint over the years coupled with vapor retarders (6 mil PE sheeting) have been applied. Tyvek on the outside. Is it perfect? No. But I do not humidify my house. But in retrofitting my house since insulating, years later, I have seen no evidence of moisture different from what was there for the 110 years before I insulated and what happened in the 20 years since I did. None.
(Much if what I am writing below is well known to you, obviously so is directed really at the wider readership- not meaning to lecture you know!)
The basic philosophy of building or retrofitting for insulation in cold climates where moisture is of concern is, "tighten up the inside, loosen up the outside", meaning that interior-side components have a higher perm rating and the exterior components are far more "moisture breathable".
Remember, the perm rating is "grains per hour per SF per inch of Hg. difference in vapor pressure". Drywall alone has a perm rating of about 40, easily cut in half by application of two coats of even latex paint. Also, as you know, a perm rating of 1.0 or less qualifies it as a vapor retarder ("barrier" being an often used but less precise term).
I have seen houses all but destroyed because an owner had the house aluminum sided over aluminum foil. Later, they went back and had cellulose blown in. Naturally the first thing moisture found on the way outside was the now-cold aluminum foil. A fungus Woodstock.
Most moisture transfered though a wall fabric is by airflow and associated moisture. The more airtight the wall, the less this will occur. This is why Corbond and Icynene and Dense-Pack cellulose insulations and/or Tyvek/Typar house wraps help in many ways. They dramatically slow down the airflow through the fabric of the wall itself. To an air and water molecule, a wall looks like a fishnet. The air and associated moisture get carried through wholesale, depositing at the appropriate dewpoint.
The other factor is diffusion, the dispersal of moisture molecules to achieve equilibrium. Try and stop that one! You can slow it down, same as heat loss but not stop it. Diffusion moves about 10% of the moisture as is carried by airflow. Stop the airflow and you stop 90% of the moisture being carried with it. The rest is diffusion.
The key to diffusion is vapor pressure. My indoor RH in winter is roughly 18-20% with a vapor pressure of about 0.148 inches Hg. Outdoors, when it is zero degrees F. outside (Canadian Summer to you!) and 50% RH, the vapor pressure is 0.019, about 10% or a 10:1 gradient. This difference, about 0.129 inches Hg. is, while 90% of the difference, almost insignificant. Keep in mind too that this gradient occurs only a fraction of winter hours. The average winter temperature here is in the high 30's but at freezing (32F/0C), the outdoor vapor pressure is 0.09" Hg. and the difference is only 0.058" Hg.
Essentially, the wall is as good as the lowest perm-rated layer as an absolute, but even so, the series of layers of different perm ratings each play a role in slowing down diffusion by migration. This is analogous to insulation. Each component slows the flow of heat but at different rates. Some help, some make little difference, but the "star of the show" is the best layer, much as your insulation would be, thermally speaking.
A retrofit house with a total wall perm rating of about 5 and the aforementioned vapor pressure difference of 0.129" Hg. would pass, by diffusion, about 0.64 grains of moisture per hour per SF, not much. The key is, is there any component within the wall in an outward path which will hold back that moisture at a location below the dewpoint? If you have Tyvek or even builders felt, moisture will still get through in the vapor state.
Older houses with no insulation such as yours, probably has stains on the inside face of the exterior sheathing. Frost develops but the air going through also dries it before damage starts; it does not stay in a liquid state long enough to get a toe-hold on fungus development. That is how loose your wall must be.
The fact that you insulated your attic and basement walls (moisture has a way of finding a path anywhere and in any direction towards lower vapor pressure) tells me that you must be doing OK. I do think your walls should benefit also.
In summary, I would not let fear of moisture prevent you from lowering your heating bills. The damage potential from diffusion (once air flow is substantially eliminated through the wall fabric) is not of concern if the outside of your house can breathe out the water vapor.
If the insulation is imperfect is is still better than not insulating at all. If your vapor barrier is not perfect (how could it be?) it is not as bad as it seems, in reality. This assumes you do not cook rice and spaghetti daily without ventilation and do not have a foil-wrapped house of course!
I agree in your pure sense about what can happen without vapor barriers. (I take it that you are in Canada where you really have vapour and a surplus of the letter "u". :)
Here are the qualifiers (and I live in an old meaning 1873 farm house in Boston). A few good coats of oil based paint over the years coupled with vapor retarders (6 mil PE sheeting) have been applied. Tyvek on the outside. Is it perfect? No. But I do not humidify my house. But in retrofitting my house since insulating, years later, I have seen no evidence of moisture different from what was there for the 110 years before I insulated and what happened in the 20 years since I did. None.
(Much if what I am writing below is well known to you, obviously so is directed really at the wider readership- not meaning to lecture you know!)
The basic philosophy of building or retrofitting for insulation in cold climates where moisture is of concern is, "tighten up the inside, loosen up the outside", meaning that interior-side components have a higher perm rating and the exterior components are far more "moisture breathable".
Remember, the perm rating is "grains per hour per SF per inch of Hg. difference in vapor pressure". Drywall alone has a perm rating of about 40, easily cut in half by application of two coats of even latex paint. Also, as you know, a perm rating of 1.0 or less qualifies it as a vapor retarder ("barrier" being an often used but less precise term).
I have seen houses all but destroyed because an owner had the house aluminum sided over aluminum foil. Later, they went back and had cellulose blown in. Naturally the first thing moisture found on the way outside was the now-cold aluminum foil. A fungus Woodstock.
Most moisture transfered though a wall fabric is by airflow and associated moisture. The more airtight the wall, the less this will occur. This is why Corbond and Icynene and Dense-Pack cellulose insulations and/or Tyvek/Typar house wraps help in many ways. They dramatically slow down the airflow through the fabric of the wall itself. To an air and water molecule, a wall looks like a fishnet. The air and associated moisture get carried through wholesale, depositing at the appropriate dewpoint.
The other factor is diffusion, the dispersal of moisture molecules to achieve equilibrium. Try and stop that one! You can slow it down, same as heat loss but not stop it. Diffusion moves about 10% of the moisture as is carried by airflow. Stop the airflow and you stop 90% of the moisture being carried with it. The rest is diffusion.
The key to diffusion is vapor pressure. My indoor RH in winter is roughly 18-20% with a vapor pressure of about 0.148 inches Hg. Outdoors, when it is zero degrees F. outside (Canadian Summer to you!) and 50% RH, the vapor pressure is 0.019, about 10% or a 10:1 gradient. This difference, about 0.129 inches Hg. is, while 90% of the difference, almost insignificant. Keep in mind too that this gradient occurs only a fraction of winter hours. The average winter temperature here is in the high 30's but at freezing (32F/0C), the outdoor vapor pressure is 0.09" Hg. and the difference is only 0.058" Hg.
Essentially, the wall is as good as the lowest perm-rated layer as an absolute, but even so, the series of layers of different perm ratings each play a role in slowing down diffusion by migration. This is analogous to insulation. Each component slows the flow of heat but at different rates. Some help, some make little difference, but the "star of the show" is the best layer, much as your insulation would be, thermally speaking.
A retrofit house with a total wall perm rating of about 5 and the aforementioned vapor pressure difference of 0.129" Hg. would pass, by diffusion, about 0.64 grains of moisture per hour per SF, not much. The key is, is there any component within the wall in an outward path which will hold back that moisture at a location below the dewpoint? If you have Tyvek or even builders felt, moisture will still get through in the vapor state.
Older houses with no insulation such as yours, probably has stains on the inside face of the exterior sheathing. Frost develops but the air going through also dries it before damage starts; it does not stay in a liquid state long enough to get a toe-hold on fungus development. That is how loose your wall must be.
The fact that you insulated your attic and basement walls (moisture has a way of finding a path anywhere and in any direction towards lower vapor pressure) tells me that you must be doing OK. I do think your walls should benefit also.
In summary, I would not let fear of moisture prevent you from lowering your heating bills. The damage potential from diffusion (once air flow is substantially eliminated through the wall fabric) is not of concern if the outside of your house can breathe out the water vapor.
"If you do not know the answer, say, "I do not know the answer", and you will be correct!"
-Ernie White, my Dad
-Ernie White, my Dad
0
Comments
-
old house blues
when doing a heat loss calculation what r value would you assign to a empty wall cavity with lath, horse hair plaster on the inside and clapboard siding over 3/4' boards on the outside. the wall is a full 4' thick plus. they won't go for insulation at this time. thanks0 -
i dont know where I heard it but "Insulation is the fuel you pay for once." The money they are going to save in insulating it going to go pay for the extra fuel cost.0 -
A pirate gives an R value
Assuming the parameters you gave, I get an overall R value of 4.27 with a corresponding u-factor of 0.2342.
Keep in mind the biggest variable is how tight the air cavity is. If old felt (I have never seen it intact), you can expect a good decrease in your air space value (0.98 if still air) which, in addition to losing that R value will also chill the other layers. The numbers are "laboratory theoretical" really. Other factors that may change from the assumed is the sheathing. I took 3/4" pine but it might actually be 7/8 spruce. No big deal but you get the idea.
As Derrick said, you pay for insulation once. If you size a heating system, particularly the boiler for this larger heat loss, you will do them no favors. If you have blown in Nu-Wool or other dense-pack cellulose which is tight enough to be a reasonable air barrier, you could raise the R value by 14 overall, allowing for framing. Tyvek and tape the house and you have really done something.
If you have 2000 SF of wall that costs you $3,000 to insulate ($1.50 per SF, just a wild guess), the heat loss for that portion would drop from almost 33,000 BTUH (70F indoors, zero outdoors) to about 8,750 BTUH, call it down to almost 1/4 of the wall loss.
That savings of about 24,000 BTUH, (not even counting the lower infiltration rate) would save about 350 therms of gas a year if you burn 85% efficiently and have 6,000 degree-days.
If you are paying $1.70 per therm as I have been, that comes out to almost $600 per year or a five-year simple payback.
Throw in the uncounted infiltration rate improvements and you have shortened this to an unknown but measurable degree.
Tell them this and let their decision be a more informed one."If you do not know the answer, say, "I do not know the answer", and you will be correct!"
-Ernie White, my Dad0 -
I agree with the \"Bradster\",
only I got R-4.11. The way he broke it down is right-on, so I hope you can get it through to them.
Good-Luck,,now back to our long weekend eh!
Dave0 -
thanks for the details, now i can do the heat loss both ways and show the customer the difference in initial install cost and future heating costs. sure hope she listens.0 -
Although this is risky
you can make some assumption for infiltration reduction with insulation IF you go with Nu-Wool or other Dense Pack Cellulose option. Icynene will do even better but at twice the cost on average, yet better sealing.
How much? Absent a blower door test it is all a guess. If you took the infiltration "as-is" at 1.0 air changes per hour, I would think that you could conservatively reduce that by 25% (for the infiltration portion only). Assume windows are pretty tight of course, same in each case.
In actual practice, I would figure a reduction of 1/3 but would rather not over-sell an unknown/uncontrollable result. Rather, let them be surprised, pleasantly.
Size the system to the new heat loss and the biggest savings are yours/hers for the cost of a pencil and paper.
Good luck and let us know how it goes."If you do not know the answer, say, "I do not know the answer", and you will be correct!"
-Ernie White, my Dad0 -
Um... well...
I think this is a first: gotta debate a little with Brad. It is quite true that insulaton will help a great deal -- given two things, which may not be possible with an old house (like, for instance, mine). First, can you get it into all the spaces? Like ALL the spaces? Otherwise, the infiltration will still be pretty bad. Second, and much more important, can you create a positivie vapour barrier on the inside? If not, you can kiss your outer wall goodbye, as well as at least some of the framing and the paint. Which just could get expensive...
All of which is why my house is NOT insulated in the walls (it is, attic and basement walls)Br. Jamie, osb
Building superintendent/caretaker, 7200 sq. ft. historic house museum with dependencies in New England0 -
Jamie
I would say adding insulation would be a persons best defense against the elements(and high fuel bills), as opposed to not having any period. Would it go everywhere if blown-in?, well that would depend on the insulation contractors knowledge of how the home is framed. There are ways(or used to be), of conducting infra-red tests to find any missed spots within cavities. As far as vapor-barriers go, without wrecking the inside there are special paints that can be applied to the inside of the walls that give adequate protection, not easy to find but they are out there.
Hope this helps.
Dave0 -
rot
My father insulated an old house inthe mid 70's and precipitated the greatest advance in carpenter ant civaliztion in Connecticut up to that time. That particular house rotted from the inside out and is no longer standing. He has put a nice new one in its place. That being said Dow has a house wrap for old houses that breathes (for real not like Tyvek) it is light blue and is made of styrofoam. It is on my house under my new cedar and over my new blown in cellulose. I'll let you know how it goes. The gas bills were about a third less this winter and comfort level was way up.0 -
insulation
i got my customer to start leaning toward insulation, but the question becomes what is the best way to go. the house is ballooned framed with no vapor barrier that i can see in the places it has been demoed inside. i do not want to promise her results that i am not sure of. how much will i save, will moisture become a problem ? the house is located in southern vermont with some serious winter weather.0 -
Balloon Framing
is an opportunity here. The continuous nature of the stud cavity means a good pass by the floor joists.
The one caution I would take is that the floor joists are often sitting on a ledger and the stud cavity and floor joist cavities are open to one another. Such was the case in my house and much insulation was pumped into the joist space between first and second floors.
What I am doing now (today in fact as a function of other projects) is injecting foam into the ends of those cavities to close them off. This will allow greater integrity of the final product. I suggest that Tigerfoam or other low pressure expansion foam be used for this part.
That said, my default would be to use NuWool or other dense-pack cellulose. For more money but greater integrity, Icynene as formulated for enclosed cavities. What you do not want is high expansion which can bulge the walls. The product has to expand to fill the cavity then stop.
Call some knowledgeable insulation companies and hear what they have to say."If you do not know the answer, say, "I do not know the answer", and you will be correct!"
-Ernie White, my Dad0 -
Brad, if i had to insulate my old balloon frame house again
with blown-in cellulose, I would have first foamed the rim joist cavities, then do the cellulose. By doing the cellulose first, I pretty much made it impossible to foam afterwards. It's not a total loss, since those cavities did fill up quite nicely with the cellulose; but as you know those cavities have a big open end towards the interior of the house, so it's not packed as tight as it should be.
Also, had I sealed the basement cavities, I would probably have had to add a fresh air intake into the boiler room, unless the window and other house infiltration was sufficient for proper combustion.
As far as I understand each floor has these cavities just below ceiling level.
Thanks for the detailed insulation explanation.
David0 -
Balloon framing
Had a friend of mine who figured he`d save a few bucks by dumping-in Zonolite from the attic,,long story short, he wound-up with about 8 bags on the basement floor before he caught-on.
Dave0 -
windows
the windows are one of the few places that are relatively tight, they are newer replacement double pane. at least someone took a step in the right direction. the old front door and side lites are all single pane0 -
Arne, please listen up to Brad and David on this point. Why? Because it has taken me (slow learner, I suppose) 20 years to realize that, while the walls in our 1930s bungalow in Minneapolis are doing well (blown-in cellulose), the perimeter of the first floor's ceiling/2nd floor's floor (joist area) is taking a beating from condensation -- just what they are talking about.
The previous owner blew fiberglas into the whole floor (don't ask), which is generally fine... but gives moisture vapor near-infinite ways to get into the joist area, and then we get signs of moisture damage at the outside walls. I thought it was the ice dams doing it. I was wrong.
It will all get foamed, tightly, whether from above or below, as possible. Better late than never? Good luck!0
This discussion has been closed.
Categories
- All Categories
- 86.7K THE MAIN WALL
- 3.1K A-C, Heat Pumps & Refrigeration
- 56 Biomass
- 423 Carbon Monoxide Awareness
- 104 Chimneys & Flues
- 2K Domestic Hot Water
- 5.6K Gas Heating
- 103 Geothermal
- 159 Indoor-Air Quality
- 3.6K Oil Heating
- 68 Pipe Deterioration
- 940 Plumbing
- 6.2K Radiant Heating
- 385 Solar
- 15.3K Strictly Steam
- 3.4K Thermostats and Controls
- 54 Water Quality
- 43 Industry Classes
- 47 Job Opportunities
- 18 Recall Announcements