Welcome! Here are the website rules, as well as some tips for using this forum.
Need to contact us? Visit https://heatinghelp.com/contact-us/.
Click here to Find a Contractor in your area.
Above subfloor plates...U or inverted U
Options

jusjoken
Member Posts: 3
I am planning a radiant solution in a renovation and will install the heating plates above the subfloor. So I need to know if the heat transfer plates should be installed above or below the added 3/4 inch spacer boards.
So which option listed top to bottom....
Option 1...
Finished floor boards (engineered floating boards)
Transfer plate as U
3/4 in plywood spacers
Subfloor
Option 2
Finished floor as above
3/4 inch plywood spacers
Transfer plates as upside-down U
Subfloor
Picture added for clarity...
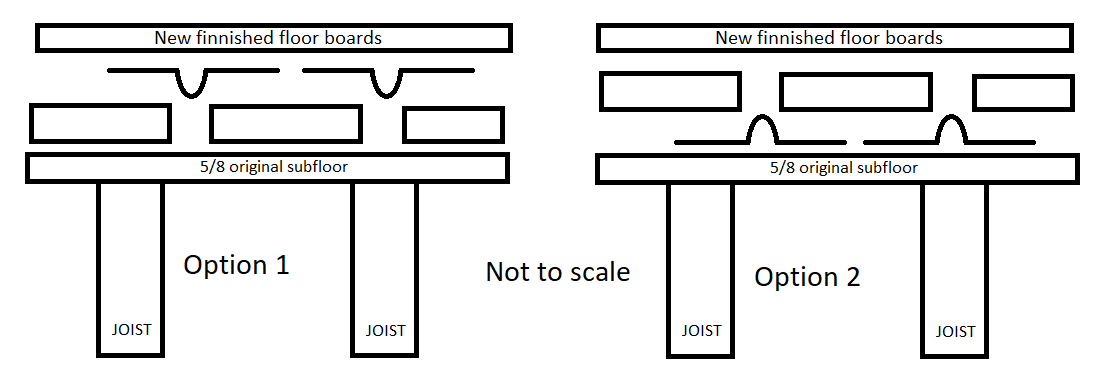
Hope this question makes sense but I have seen installers do either and wondering pros/cons of both approaches
Thanks
So which option listed top to bottom....
Option 1...
Finished floor boards (engineered floating boards)
Transfer plate as U
3/4 in plywood spacers
Subfloor
Option 2
Finished floor as above
3/4 inch plywood spacers
Transfer plates as upside-down U
Subfloor
Picture added for clarity...
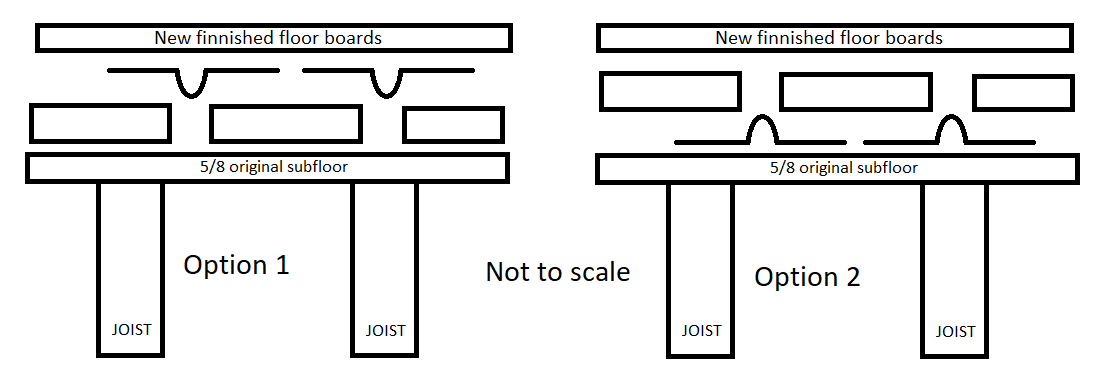
Hope this question makes sense but I have seen installers do either and wondering pros/cons of both approaches
Thanks
0
Comments
-
I think you mean C fin or U fin? The C fin are most common, sold by many brands, U fin are not as common. The U fin puts the aluminum up closer to thre finished floor, not a huge difference in performance
snoop around Radiantdesign. Com for infoBob "hot rod" Rohr
trainer for Caleffi NA
Living the hydronic dream0 -
I'm in the middle of planning a similar job. We have several "omega" samples in hand of RHT, Warmboard S and R, Roth panel, Ecowarm, Thermalboard, and Sunboard. All of them have the "u" facing up.0
-
Thanks for the comments...I updated the original post to include this diagram to better illustrate my question...
Hope this helps to clarify...Pros/Cons of an install using Option 1 or Option 2....
Thanks
0 -
given the limitations of wood for thermal transfer and as thermal mass (it does both but not either well), I prefer the option 1 although you can have trouble occasionally with the pipe staying down which obviously ain't gonna be a problem with option 2 (except at the bends which won't be covered, you haven't detailed if you plan for the bends to be in the floor or in the wall or off space) but it is easier to service problems with option 1. of course the idea is be careful and don't have problems. i'm going to try that sometime.
so there is also a habit of using caulk in the omega plates to improve overall contact and heat transfer and that helps keep the pipe in the plates once cured but you may need to put temporary cleats in places to hold it down. I much prefer 3/8 pex because it has less of mind of its own and you can get omega plates for it. harder to find but the folks who have serviced this technology for quite some time have got them. although you technically ought to make the runs a little shorter per leg it has more transfer surface per btu in the pipe. it also saves you wood and minor cubic inches in house. these days, these sheet cost of plywood is through the roof and it doesn't make as much difference between 1/2, 5/8 and 3/4 but it does make a difference. of course you also have the problem that 1/2 is not half with plywood. if I had the time and forethought I'd go to the local saw mill and get some rough board that are 3/4 in the rough pine boards and let them season for a few seasons (or take them to someone with a dehumidfication kiln) and then plane them to 1/2" or 9/16" whatever experience tells you if you experiment a little before you have them planed. that is the most cost effective way to get spacers these days.
after all that circuitous talk, although i haven't done it, you have got me thinking that the system with 3/8 pex could probably just be installed with 1/2" plywood and the floating floor and whatever its underlayment could take up the difference (also a minor issue with the plates on the surface of the spacers (ditto 5/8 ply and 1/2" tubing). . . . or with 3/8 tube you could use 1/2" hardibacker as spacers and snap 5 foot running lengths in the spacer width. or maybe, depending on spacing you could use hardibacker or concrete siding and you don't need to cut it and you get a little better mass and predictable thickness.
i take it that you don't need insulation and that the space under the floor you're working on is also conditioned as i might have other recommendations if that were not the case.0 -
Thanks for the detailed response and yes the area below is conditioned. The loops will be in the floor just like the rest of the pex. I will do some more research on the caulking "habit" and see if I should add that to the plan. I guess I will be going forward with option 1 then.
Thanks0
Categories
- All Categories
- 85.7K THE MAIN WALL
- 3K A-C, Heat Pumps & Refrigeration
- 49 Biomass
- 418 Carbon Monoxide Awareness
- 72 Chimneys & Flues
- 1.9K Domestic Hot Water
- 5.2K Gas Heating
- 92 Geothermal
- 149 Indoor-Air Quality
- 3.2K Oil Heating
- 59 Pipe Deterioration
- 849 Plumbing
- 5.8K Radiant Heating
- 372 Solar
- 14.5K Strictly Steam
- 3.2K Thermostats and Controls
- 50 Water Quality
- 39 Industry Classes
- 47 Job Opportunities
- 15 Recall Announcements