Welcome! Here are the website rules, as well as some tips for using this forum.
Need to contact us? Visit https://heatinghelp.com/contact-us/.
Click here to Find a Contractor in your area.
Another 1700's radiant retro-fit! (PAH)
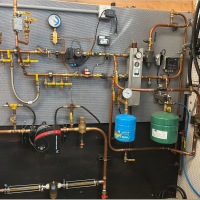
hot_rod
Member Posts: 23,852
I'm drawn to challenges, I guess. This one's been in the same family for five generations. Stone walls, logs everywhere tubing wants to run - tis a tain breezer of a job. My digital is busted, but being rebuilt - so no pics yet to share. The oil fired boiler is an antique Burnham Jubilee. The owners came to me with literature in hand (downloaded from the internet) for their choice - a Laars oil fired Max, which I am not familiar with. Looks like a fairly compact unit & will have a "balanced flue" for sidewall venting.
Bob "hot rod" Rohr
trainer for Caleffi NA
Living the hydronic dream
trainer for Caleffi NA
Living the hydronic dream
0
Comments
-
Cant wait to see your pics
but in the meantime, tell us about the house and what was there when you started besides the Jubilee............
To Learn More About This Contractor, Click Here to Visit Their Ad in "Find A Contractor"All Steamed Up, Inc.
Towson, MD, USA
Steam, Vapor & Hot-Water Heating Specialists
Oil & Gas Burner Service
Consulting0 -
Call it
Hello radiant, goodbye cast iron!
When we started......
Old cast iron rads (more on them later).
Uneven plank flooring over hand hewn beams over a dirt crawl space.
No insulation - stone walls.
Cold uncomfortable sixth generation occupants.
Today there are now three radiant floors(G).
Kitchen, bath and laundry rooms.
The rest of the house will remain on standing cast rads - except we'll now be using indoor reset to modulate boiler temps & make those hunks of cast iron huggable.
An indirect is replacing the electric water heater, which has exposed element wiring - yikes!
A bit of mixing methodology that initially threw off the engineers - thinking outside the box. Budget was a real concern, so simple mixing strategies were needed. Reduced pumps and mixing valves by running water (higher temps) through the staple-up floors first and using that two-loop manifold's return flow to feed the lower temps required radiant on top of the floor kitchen floor and then return to the boiler from there - one larger series loop. What the heck, the flow rates were low enough to support the strategy. One pump, one mixing valve = $$$ saved.
The GC is a dream to work with & "gets it". He beefed up the floors and managed to get us R-23 under the radiant floors! They'll be tile when finished, so that gave us the ability to bump up temps a tad. He even helped cart the boiler in and lift it up onto a shelf. Heavy little bugger. (The boiler, not the GC!)
Today was a beautiful day to be working on a 1700's farm house in rural PA. Blue skies, lots of flies and the sweet smell of manure being spread on the fields. Mix in the odors from the nearby chicken house and dairy operation & you can begin to sense the "atmosphere".(G) Moooooooooooove on over old technology!
The owner chipped in too. In order to reduce costs for his investment in his family's future comfort, he decided to add sweat equity. We cut off the boiler piping & he went to town breaking down that old cast iron beastie into its smallest pieces. By noon, he'd managed to completely dismantle and remove all traces! I think I'll hire him(G). He hossed out the boiler sections by himself. On second thought, he's a workman's comp liability risk!
To Learn More About This Contractor, Click Here to Visit Their Ad in "Find A Contractor"Bob "hot rod" Rohr
trainer for Caleffi NA
Living the hydronic dream0 -
Laars
I thought your favorite boiler was Laars. What's a ballanced flue?
Shouldn't have problems snaking PEX or PAP through that place. Sure beats sweating copper down in the craw.
An oil fired copper fin boiler?
To Learn More About This Contractor, Click Here to Visit Their Ad in "Find A Contractor"0 -
well
Can't say Laars is my favorite Gary, but they too make a great product. I install whatever is wanted by the homeowners or if it's a referral from a manufacturer, I don't bite the hand that's sending work my way by switching brands.
My blood runs pretty blue(G)when I get to choose brands and also condensing boilers if that's warranted or wanted.
Balanced flue is their termination for direct venting the Max. Looks to be quick and easy with flex SS lines between the boiler's exhaust & outdoor air & termination box where the incoming air passes over the outgoing SS piping to pre-warm the incoming air. No flue draft regulator needed when using this kit. No copper fins either, it's a two-pass cylindrical HX. Lots of weight for such a small package!
To Learn More About This Contractor, Click Here to Visit Their Ad in "Find A Contractor"0 -
Dave, got a question for you.
What is your policy on parts and service for a piece of equipment you don't normally handle? Do you take care of it if there's a problem or refer the owner to someone else who works with that line?0 -
depends
Steve,
If we're supplying the materials, we check with the supplier regarding stocked inventory of essential repair parts. For newer products, like the Munchkin, where we're installing multiple units - we build up our own inventory of essential parts, which naturally builds up our overhead too. We have more money tied up in controls and PC boards than I'd like, but nobody in our industry builds standardization into their products anymore. For shops like ours that service all brands, the stocking costs per truck have soared in recent years & has less to do with our product sales than the changes in technology and controls.
If the owners are the ones requesting a particular brand for which we don't stock parts, we forwarn them that that could mean a night without heat or A/C until we can obtain parts. In some cases, like with York equipment, that can be a three working day turn around (which doesn't make sense since I'm in York, but I can't buy York in York & must purchase via Philadelphia!). If they're still convinced that's what they want, I don't have any problem with that. They're the boss.
If, on the other hand, they want to purchase and supply the product(s). They must read and sign our our written warranty policy, which clearly spells out how any product issues will be handled - including breakage and mis-fits and that they will be billed accordingly. Once they read it, they (more often than not) elect to have us purchase and supply the materials. I can e-mail a copy of the text to anyone interested in adapting it to their business. The best part about having them read and sign the policy is that they can't get out of paying for our labor brought on by any material defects when they arise. I can't stop them from shopping, but I'm entitled to make a profit or I can turn away the work. Either way, I'm intent on remaing in the driver's seat. If it's someone we haven't worked for in the past and not a referral from a previous customer, we typically refuse work with customer supplied goods unless I can flat rate the installation - if you get my drift. It doesn't say United Way on the side of my trucks!
To Learn More About This Contractor, Click Here to Visit Their Ad in "Find A Contractor"0
This discussion has been closed.
Categories
- All Categories
- 86.5K THE MAIN WALL
- 3.1K A-C, Heat Pumps & Refrigeration
- 53 Biomass
- 423 Carbon Monoxide Awareness
- 95 Chimneys & Flues
- 2K Domestic Hot Water
- 5.5K Gas Heating
- 101 Geothermal
- 156 Indoor-Air Quality
- 3.5K Oil Heating
- 64 Pipe Deterioration
- 928 Plumbing
- 6.1K Radiant Heating
- 384 Solar
- 15.1K Strictly Steam
- 3.3K Thermostats and Controls
- 54 Water Quality
- 41 Industry Classes
- 48 Job Opportunities
- 17 Recall Announcements