Welcome! Here are the website rules, as well as some tips for using this forum.
Need to contact us? Visit https://heatinghelp.com/contact-us/.
Click here to Find a Contractor in your area.
Electric water heater as buffer tank
Options
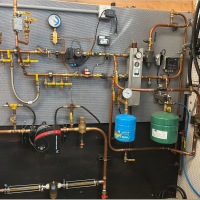
hot_rod
Member Posts: 25,526
has 4 hw baseboard zones and 4 radiant. On several zones both radiant and baseboard will be on one thermostat.
The buffer is the primary loop, notice the homemade air scoop!
I used the 1" bottom element holes with 1" mip X 1-1/4" copper adapter. The top is a 3/4" mip X 1-1/4" copper adapter. This allows the 12 gpm flow for the 20 delta tee with the 117,000 boiler output, math wise!
Plus I wanted to try the custom 1-1/4" dies that REMS built for me, thanks again REMS :)
The top element hole is a well for the thermostat that will "run" the buffer tank temperature.
The factory T&P is left in place and a 30 lb relief is on the boiler.
I suppose the boiler is considered a secondary as is the baseboard and radiant loops.
I used my REMS bender and expander to pipe. I used "store bought" tees where I had to wrench on them at the boiler connections.
I also discovered that the foam insulation can be twisted radially when it is put on the bends and it eliminates the "bunching" typical on the inside of the sweep. You only need to trim the butt ends, as they end up uneven when you twist the foam.
Thinking about a Taco post purge card for the boiler pump, as it has a bang, bang, return protection control.
Any thoughts or ideas?
hot rod
The buffer is the primary loop, notice the homemade air scoop!
I used the 1" bottom element holes with 1" mip X 1-1/4" copper adapter. The top is a 3/4" mip X 1-1/4" copper adapter. This allows the 12 gpm flow for the 20 delta tee with the 117,000 boiler output, math wise!
Plus I wanted to try the custom 1-1/4" dies that REMS built for me, thanks again REMS :)
The top element hole is a well for the thermostat that will "run" the buffer tank temperature.
The factory T&P is left in place and a 30 lb relief is on the boiler.
I suppose the boiler is considered a secondary as is the baseboard and radiant loops.
I used my REMS bender and expander to pipe. I used "store bought" tees where I had to wrench on them at the boiler connections.
I also discovered that the foam insulation can be twisted radially when it is put on the bends and it eliminates the "bunching" typical on the inside of the sweep. You only need to trim the butt ends, as they end up uneven when you twist the foam.
Thinking about a Taco post purge card for the boiler pump, as it has a bang, bang, return protection control.
Any thoughts or ideas?
hot rod
Bob "hot rod" Rohr
trainer for Caleffi NA
Living the hydronic dream
trainer for Caleffi NA
Living the hydronic dream
1
Comments
-
thats some nice piping!
i'm going to be installing a buffer tank for a job i'm designing out, so i've a question for you..i got lost on why you reduced the top outlet,,can you explain this better for me..i was planning on using both element openings, which would leave alot of wasted dead water area..i like your method better but i'm having trouble understanding the 1 1/4'' pipe requirement being fed via the 3/4''..i try to keep my piping all the same size, with nothing acting as an orifice,,not for any reason other than my math skills suck so bad that it makes it easier to figure out..0 -
Actually
I increased the 3/4" and 1" openings for better flow. The pipe size I chose was based on the gpm flow and the delta T I designed aroung. Siggy's design software has a great module that allows you to pick pipe sizes bases on flow and delta T.
That reduction from 1-1/4" to 3/4" and 1" for such a short distance, will create a very small pressure drop, about what a reduced ball valve port would or a flow setter, not a big deal as the pump has plenty of head to move the loop and tank.
I think using top and bottom element holes would assure pretty good mixing in the tank. Add a homemade dip tube to the bottom connection for piece of mind
Sounds like you are trying to pipe with all 3/4"? What kind of BTUs are you trying to move. Siggys software will pop up a warning when velocities exceed 4 fps. Try the free demo version at www.hydronicpros.com
Also try the B&G online "System Sizer" to calculate this info.
Temperature also plays into the calc. I assumed 120 for a heat pump application and I was able to push 6.1 gpm at 20 delta t for a 3.8 fps velocity in 3/4" copper.
This should move around 60,000 BTUs per hour for you. The pressure drop will change with the addition of fittings or devices, of course.
Grab a copy of the Hydronic Design Studio from "Books and More" here. You will be surprised how much info it can provide with a few key strokes!
hot rodBob "hot rod" Rohr
trainer for Caleffi NA
Living the hydronic dream0 -
Buffer Tank as Primary
That's the same way I look at it when the buffer itself is supplying all the heat to the system...
"4 hw baseboard zones and 4 radiant. On several zones both radiant and baseboard will be on one thermostat" Sounds like that would have nightmarish problems without the buffer.
That "Siggy Software" sure seemed great for buffering--not only allowing you to instantly play "what if" but to see the effects on the boiler and even energy consumption. Most importantly it allows you to "see" why, when and how much it's needed in the first place.
-------------------------
Tried your "insulation twisting" idea on a scrap of tube with a few elbows. Seemed to work well but will see if the adhesive holds through the bends...0 -
I found
with those long sweeping bends there is very little strain on the split joint. In the crawl space I actually used un-slit insulation and slid it on from one end after I soldered.
Short turn 90's are tough to bend 1/2" or thicker, walled foam around. Probably best to cut 45's on the insulation. I've never been too good at that:) They really need to be glued to hold after you miter them.
hot rodBob "hot rod" Rohr
trainer for Caleffi NA
Living the hydronic dream0 -
Hot Rod...You obviously like what you do!
Nice work! Using a glass lined tank is certainly the least expensive option but I worry about their life cycle. 95% of glass lined tanks leak at a tank penetration due to the anode being consumed and the water attacking the exposed metal. I've been told this is due to a process called "burn-back" where the glass gets burned away from the tank penetration when it is being cooked in the industrial 0vens that cure the glass. Flue gas velocity in the ovens is the culprit. I was at a show this past week and looked at an Amtrol storage tank that is essentially their indirect without the coil. Good insulation, probably much better life. Would that fit your application?0 -
buffer tank piping
Nice looking job Hot Rod. It reminds me of the "signature systm" that Mike Reif worked with in Sitka Alaska. This solution eliminates flow through the boiler when the burner is not firing. Very nice compact installation.
I also wondered about the life of the glass lining - but in a closed loop system this may be irrelevant.
Did you use the standard hot and cold connections on the DHW tank for anything?
One other question: Is that a cross fitting at the top of the tank for the air vent?
On a side note: Mario and I expect to release the update to the Hydronics Design Studio software with the buffer tank simulator in a couple of weeks. It will be a free downloadable update for all those who own the software. A preliminary screen dump is attached.0 -
Glass lined tank life
I really think this tank will last as long as the boiler! Once the system is purged and I add the Rhomar hydronic inhibitor there should be no O2 present to support any corrosion process. Being a sealed system, without a water fill, it's unlikely any O2 will enter. I will use PAP for the plate/radiant. I feel the PAP's offer the best O2 ingress protection.
I have some glass lined steel indirects going on 12 years in service, and they see constant fresh, oxygenated water.
Siggy, the top connections were used. One for the tridicator gauge, and the other is the loop connection that connects to the bottom element hole. The upper element hole is a well for my setpoint control.
That is a homemade air purger, with a brass air vent on top and the bottom connection will be for the expansion tank, remotely mounted. I have a bucket full of those brass cross fittings, I came across years ago. Thinking of sticking a stainless steel fitting brush in it for "micro bubble" collection and removal
The secondary loops also have a Spiro, and a Honeywell for rapid air removal in the secondary circuits, as it often takes a while for all the air to get back to the primary loop/tank.
hot rodBob "hot rod" Rohr
trainer for Caleffi NA
Living the hydronic dream0 -
Boiler
Hot Rod, does the boiler you are useing have a solid bottom under the burners ? bob0 -
buffer tank simulator
The screen image of the new buffer tank simulator module didn't post with my first try. Hopefully this will do it.0 -
It is a
wet leg boiler, at least I think that is the proper term. The end sections come down around the side of the burners.
I believe it has a metal pan under the burners, is this what you mean? Think it needs an non combustiable base to be used over combustiable floors.
A pretty nice "entry level" Viessmann. It is sold ala cart as the damper and even the pump are extras! I'm undecided if it is worth 800 more clams than US iron.
Quality of fit and construction are first class. I like the wet leg castings. Sure is a heavy buggerI took it down those stairs by myself! With a little help from a come a long.
hot rodBob "hot rod" Rohr
trainer for Caleffi NA
Living the hydronic dream0 -
-
Good point, Bob
I'll contact Viessman for an answer. This is located in a storm shelter. A small 10 X 10 below grade room. I noticed a pit for a sump pump and worried about a flood should power go out. So I thought the blocks would offef some protection. I suppose I could lift it, AGAIN, and install a plate if need be.
hot rodBob "hot rod" Rohr
trainer for Caleffi NA
Living the hydronic dream1 -
A limitation of wet leg boilers....
Is that the block assembly can't move easily as it expands and contracts. I hope Veismann built in some type of support assembly under the legs to allow this movement. I've seen several wet leg boilers crack where the leg meets the main section assembly, especially when there isn't much reinforcement and the boiler sees rapid temperature changes (ie baseboard systems, multiple zones, with no reset). I tend to prefer cast iron that sits on a combustion chamber base which allows movement.
Boilerpro0 -
Atmospheric boilers
are notoriously difficult when it comes to controlling excess air in combustion. All of the air for firing comes in from the bottom. The plate that one would put under the boiler is only there for protection against combustibles. Elevating the boiler, be it on blocks or whatever, will not effect performance anymore than setting the boiler on the floor.
Ironically, Viessmann has found a way to control air coming into an atmospheric boiler in the Vitogas 100 series. By isolating the combustion chamber in the manner done, Viessmann can control fuel air mix and combustion (NOx<27.9 ppm and CO<9.2 ppm both air free).
Viessmann also offers a stand that lifts for you (Vitogas 100 and up)so that blocks are not necessary and the end package is a professional and polished package. Even if the stand is not used, all of our boilers have leveling "feet" that keep the wetleg castings off of the ground.
Thanks,
Henry
VI Midwest0
This discussion has been closed.
Categories
- All Categories
- 87.1K THE MAIN WALL
- 3.2K A-C, Heat Pumps & Refrigeration
- 58 Biomass
- 427 Carbon Monoxide Awareness
- 113 Chimneys & Flues
- 2.1K Domestic Hot Water
- 5.7K Gas Heating
- 110 Geothermal
- 161 Indoor-Air Quality
- 3.6K Oil Heating
- 70 Pipe Deterioration
- 998 Plumbing
- 6.3K Radiant Heating
- 391 Solar
- 15.4K Strictly Steam
- 3.4K Thermostats and Controls
- 55 Water Quality
- 44 Industry Classes
- 48 Job Opportunities
- 18 Recall Announcements