Flow is dismal, radiant circuit
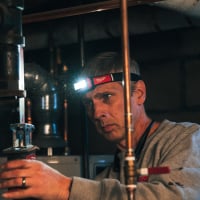
this is a new one, never had a radiant system act up. Seems like the manifold may have gooked up. The previous Alpha pump died. My guy slipped a new one in. It’s a brand new 15-58 which requires an app to unlock feature and see gpm- he didn’t know there was an underlying issue.
I ran over last evening. Alpha app says 19 ft head and .5 gpm, that’s way off. Something is impeding flow. Purging to a bucket in the basement agreed with these low numbers, flow was poor
3rd floor system is the same sq footage, alpha is running 3 gpm- right on
the water may be an issue here- watts steel manifold.
The manifold is on a finished floor, in a closet. The carpentry people built a beautiful box around the manifold, I had to stick my camera into the general area to get this shot.
looking like I need to yank the manifolds and clean them out? Or maybe the flush cart from the basement?
Yes water conditioner are needed. I need to get the flow back first
Thanks for any tips
Comments
-
you sure he purged it correctly?
0 -
-
yes, the bucket in the basement proved that, in my opinion. The homeowner was watching the pressure as I fast filled. Got to 25 and the flow in the basement was still poor. Pressure was climbing. Flow was not increasing.
1 -
@kcopp
It’s Hydronic Alternatives, multi layer plastic heat tube. 3/8”0 -
It's good to disassemble the old circ, to see what failed. Is the rotor seized?
What mode is the new circ set in. The GO app on your phone or device makes it easy to try different operation modes.
I watch the wattage change on the circ, and the RPM increase to know I have it speeding up
Bob "hot rod" Rohr
trainer for Caleffi NA
Living the hydronic dream0 -
. 4 gpm is a common design for 3/8 tube.
A 250' loop at .4 gpm is 7' head
Purging a single 250' loop with 12- 20 psi will not flow all that much.
If you think loops are sludged, put city water pressure on the manifold at the purge valves on the manifold. Isolated from the rest of the system of course.
Purge into a bucket to see what you get out.
Bob "hot rod" Rohr
trainer for Caleffi NA
Living the hydronic dream0 -
thanks HotRod, I’m getting rusty on the radiant; been peddling more heat pumps in the last bunch of years.
Yes I fiddled with different settings but the ft/head didn’t change and the Gpm didn’t either, well maybe a couple or few 1/10s of a gpm but essentially the head was super high.
The Constant Curve- I was able to grab the curve and max it. Pump made a little more noise but all in vain.
I forget how many circuits and I didn’t count- guessing 7 or 8 circuits. I suspect I did 200 footers back when we installed
I was purging the entire manifold, not one at a time. When I opened the purge valve in the basement it came with some velocity, then slowed down a lot within a second or so. I would think running 25 psi through 7 or 8 circuits would flow a lot. Maybe I’m thinking too much like a basic bb loopThat’s gauge glass is goopy- you thinking I’m probably not jammed at the manifold?
Thanks
0 -
those 3/8 loops are slow flowing, think of 200’ of garden hose. But with all open it should flow quickly into a bucket
Ive never seen an entire manifold clog?
I would try a power purge either a hose or pump cart
Any y strainers in the piping?
Bob "hot rod" Rohr
trainer for Caleffi NA
Living the hydronic dream0 -
-
no strainers- it a 20 year old modern system, wall hung Viessmann. Just radiant heat and unico water coils and an indirect
This Radiant is 8 years old- the house is taking many years to fully complete
yes the flow gauges seem like a choke point for goop, I’ll probably open it up and see what’s going on1 -
those flow meters probably turn to adjust. Crank them both directions, maybe the disc is stuck to the port opening
Bob "hot rod" Rohr
trainer for Caleffi NA
Living the hydronic dream0 -
Is the space heating adequately? It's very possible, if you have only purged from the mechanical room and didn't isolate each loop separately, that there are multiple loops which are airlocked. This is very common with radiant. It'll likely be a 2 person job, but having one person in the mech rm and another up at the manifold to isolate one loop at a time and purge them all separately is going to be your best bet here
0 -
No the whole fl is cold
It's warm at the supply manifold but the ret manifold is room temp (cold)
We can purge at the manifold (run a hose downstairs and simply pinch-squeeze the hose and listen for air)
0 -
If only one loop is flowing, the supply main would feel warm. But you need to check each loop individually. It has flowmeters, put eyes on them and you'll have your answer.
0 -
flow meters are barely legible. My thinking was: the 3rd fl is fine so there's no reason the 2nd fl would lose flow in circuits due to air; defies mama nature
0 -
-
Air doesn't care where it ends up. If it simply floated to the high point, we wouldn't ever have to purge radiant floors but that is not the case or even close to it. My money is on an airlock, but again it can be easily diagnosed in a couple minutes onsite. If flowmeters are illegible (don't appear to be), check temps of each loop entering the floor. Purge as necessary.
0 -
I'll let you know, it seems very odd to lose an entire floor for one bubble
0 -
If that bubble divided into several bubbles and stopped up several loops, it's not odd at all and happens every day with radiant systems.
0 -
I am in a blue mood—-somebody take a stab at what the problem was. I never would’ve thought of this in 1 million years. (I need to chat with my employee that installed the new circ)
Always something
0 -
-
-
yes! He’s the metal guy, I didn’t think to discuss the check. Oh well. Just some hours driving and purging into buckets, scraping my head. We shall remount and keep riding
1 -
-
it was definitely flowing, and i was getting little bubbles. It’s conceivable the original alpha died due to air bind, but I’ll never know.
—-it was actually flowing normal operation. It was registering .5 gpm a, and I can tell by closing the valves that it was moving water. Had the pump said zero GPM I might’ve seen the light 💡 a little bit sooner-0 -
Well, he had the letters on the pump installed correctly. I was in my Urologists office years back, and they had HWBB in their building. All of a sudden there was a BANG and the HWBB jumped. I told my urologist that their pump was installed backwards. He said they had JUST hired their plumber to replace the old B&G pump. I asked him if he wanted me to look at it. I did and found that the oil cups were facing up… But the pump was installed upside down, flowing through the ZV's backwards, and we all know what happens when you do that. BANG. Maybe that's what BanG stands for eh… Next time I saw him, system was silent. He said the plumber didn't realize it was possible to install them backwards, and thought that installing it with the oil port facing up was most correct… It happens… Good sleuthing on your part Gary. Merry Christmas and Happy New Years to all the old Wallies.
2 -
Are you sure the radiant circ is pumping to the Supply, and not to the Return by mistake? Many radiant manifolds don't work well when flow is reversed. If not this, could there be a piece of debris stuck inside the manifold?
For what it's worth, the manifold and tubing look like the ones shown here:
0 -
Hi
yes my guy (he doesn't do much wet stuff) put the check in backwards, ooops. I was supposed to be a simple call. The real bummer was we were flowing a tiny bit, which made it harder to pin point. I went to swap the two pumps to see if it would make a difference and we saw the upside down check. Always something
1 -
Mark yes that's a good one, pumping into a zone valve, backwards. I saw that once about 25 years ago.
Hope you're doing well
1
Categories
- All Categories
- 87K THE MAIN WALL
- 3.2K A-C, Heat Pumps & Refrigeration
- 58 Biomass
- 426 Carbon Monoxide Awareness
- 113 Chimneys & Flues
- 2.1K Domestic Hot Water
- 5.7K Gas Heating
- 109 Geothermal
- 161 Indoor-Air Quality
- 3.6K Oil Heating
- 70 Pipe Deterioration
- 994 Plumbing
- 6.3K Radiant Heating
- 391 Solar
- 15.4K Strictly Steam
- 3.4K Thermostats and Controls
- 55 Water Quality
- 44 Industry Classes
- 48 Job Opportunities
- 18 Recall Announcements