Rinnai I Series with mixed slab heat

I am thinking that I should not need another circulator on the primary because of the internal circulator in the Rinnai.
I am planning on using the included Rinnai low loss header, a Caleffi 3-way mixing valve, with the circulator downstream of the AB port, directly into the slab manifold.
See attached illustration.
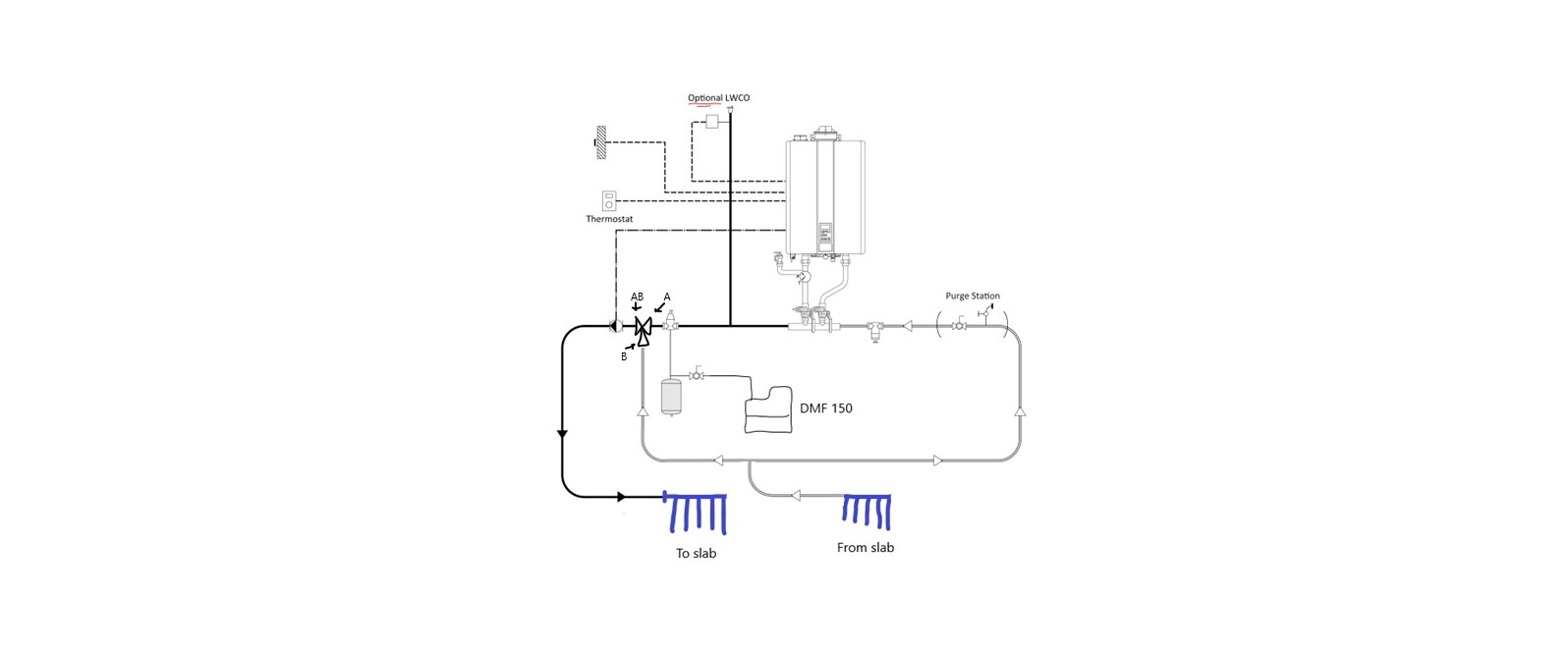
Comments
-
Yes you need a system circulator with that primary secondary header.
But why a mixing valve? Just run the boiler at the supply temperature you need, with outdoor reset if possible.
If you use a 3 wat thermostatic, the boiler would need to run 25 degrees hotter than the mix temperature you need. So you lose some efficiency, and no ODR with a thermostatic.Bob "hot rod" Rohr
trainer for Caleffi NA
Living the hydronic dream3 -
They show you in the manual how to pipe it. The "heat emitter" can be a radiator, baseboard or radiant.
I like Rinnai boilers although the last time I installed one, they didn't have line voltage contacts for the system pump. Maybe that's changed.
8.33 lbs./gal. x 60 min./hr. x 20°ΔT = 10,000 BTU's/hour
Two btu per sq ft for degree difference for a slab1 -
-
The manufacturer will list the temperature difference required for the valve to meet the ASSE test standard. This is usually done on a test bench. In some cases it is an observed test by the listing agency, you pay them to visit your factory and certify the device.
Look around and find that required delta varies from valve to valve, the Caleffi 520 has a 10 delta, for example. The attached example shows 27 degree.
Now if you don’t have that exact delta, the valve will still flow but the mixed outlet temperature will vary as the valve hunts. In Hydronics that is not a big issue, but standing in a shower you would notice a valve that is hunting and temperatures fluctuations if 3 or more degrees
In most cases a temperature gauge will not respond quickly enough to catch the variation, but your bald head under a shower certainly will! That is why the manufacturer give you valve specs to operate accuratelyBob "hot rod" Rohr
trainer for Caleffi NA
Living the hydronic dream0 -
Thanks Bob,hot_rod said:Yes you need a system circulator with that primary secondary header.
But why a mixing valve? Just run the boiler at the supply temperature you need, with outdoor reset if possible.
If you use a 3 wat thermostatic, the boiler would need to run 25 degrees hotter than the mix temperature you need. So you lose some efficiency, and no ODR with a thermostatic.
My first notion was that I wouldn't need a mixing valve, then I read the i-Series manual, and found the lowest temperature setting was 104°F. I was thinking that might be a bit high. this will be my first mod-con system design and install and I guess it seems too simple.
If you think I will be fine with an entry temperature of 104, I am game to give it a go.
If the customer complains about the floor being too warm, I know how to fix it.0 -
Ideally a heat load and design was for the system. That would indicate the supply water temperature the system requires
The boiler could run down as low as required, if 90 degrees covers the load run it there.
The floor temperature needs to be higher than room temperature to transfer heat.
usually floors run too hot inadequate tube was installed, or the heat load is higher than the floor can coverBob "hot rod" Rohr
trainer for Caleffi NA
Living the hydronic dream1 -
This "customer" is a guy that is only now looking for some "help'. He put 5 - 1/2" pex loops at 380 feet long, and bought and hung the boiler on the wall. Thankfully his boiler has plenty of capacity to meet the load.hot_rod said:Ideally a heat load and design was for the system. That would indicate the supply water temperature the system requires
The boiler could run down as low as required, if 90 degrees covers the load run it there.
The floor temperature needs to be higher than room temperature to transfer heat.
usually floors run too hot inadequate tube was installed, or the heat load is higher than the floor can cover
I have the load calculated at 55,000 Btuh, and at 11' head for the loops, I have figured a UPS 15-58 will work fine.
My biggest concern was the 104°F minimum that the Rinnai outputs. I understand that their newest models will go lower.
I was hoping for some good advice here, and I thought it might be to scrap the mixing, so I do appreciate the input.
Dave
0 -
Danger Will Robinson! Using the manifold piping in the drawing will not circulate around your loop without the secondary pump pictured in the drawing. If you do only the heat loop, using the boiler pump, don't use the manifold shown. I just reworked a job where the plumber made that mistake. If the pump and pipe match your flow requirements, you are good. If not go with primary secondary it will give you more leeway to have other temps and flows for other loops. Here you can create additional controlled Temps and or circulator zones. A boiler is just a heated pot. A heat system is everything we connect to it. We must know what we are doing to build and make it work right. WE will control the horizontal, we will control the vertical, we can change the focus to a soft blur or sharpen it to crystal clarity.0
-
A hydraulic separator is another good` option. For not much more $$ than those copper manifolds. You get hydraulic separation, air removal, dirt removal, and magnetic particle removal.
Closely spaced tee/ headers/ manifolds only give you hydraulic separation. You need to add extra components to handle the other concerns.Bob "hot rod" Rohr
trainer for Caleffi NA
Living the hydronic dream0 -
Hey bud, Rinnai heating rep here. I work with the I Series literally daily.
So, to address some things mentioned, yes, you are going to want to use some form of P/S separation- the manifolds are fine, as is a hydraulic separator.
Regarding boiler temperature, the I Series will run as low as 86 degrees supply temp. I would recommend using outdoor reset, change boiler parameter 01 to "D" (custom curve, takes setpoint and drops 36 degrees off it unless you hit 86, at which point that's your limit temp), and parameter 02 to "C" (boost function, basically disengages ODR after 30/60 minutes continuous run, "C" being 60). From there, set your high temp on the boiler control, and the unit will automatically adjust setpoint based on the reset curve.
These boilers *love* radiant heat. Feel free to shoot me any questions with regards to setup and whatnot.
Hope this helps.1 -
What changes would U suggest above for a single circuit baseboard system using I series solo?
0
Categories
- All Categories
- 87.1K THE MAIN WALL
- 3.2K A-C, Heat Pumps & Refrigeration
- 58 Biomass
- 427 Carbon Monoxide Awareness
- 113 Chimneys & Flues
- 2.1K Domestic Hot Water
- 5.7K Gas Heating
- 110 Geothermal
- 161 Indoor-Air Quality
- 3.6K Oil Heating
- 70 Pipe Deterioration
- 998 Plumbing
- 6.3K Radiant Heating
- 391 Solar
- 15.4K Strictly Steam
- 3.4K Thermostats and Controls
- 55 Water Quality
- 44 Industry Classes
- 48 Job Opportunities
- 18 Recall Announcements