Rinnai Duo check valve failure analysis
Rinnai CU199iN Duo series (w/119 gal Rinnai storage tank)
Serial Number: MB.BA-023699
Hello Ben! : )
This is a request to your engineering personnel to conduct a failure analysis into our two (2) catastrophic early field failures of the check valve that resides immediately above your internal circulator pump.
prelude:
I was first engaged for service of these twin CU-199iN units to access an extremely low recovery rate during our recent three day cold spell (15 degrees F outside temps).
In troubleshooting the system, I discovered that the plastic check valves in both units had exploded into separate pieces (see attached pics) and dropped into the circulator pump housing. This caused a noise rattling and intermittently impeded the circulator pump's proper vane rotation.
I suspect this valve's failure caused the above mixing valve to mix incorrectly thru the heat exchanger and by-pass loop resulting in its very poor heat recovery.
My thoughts on these issues
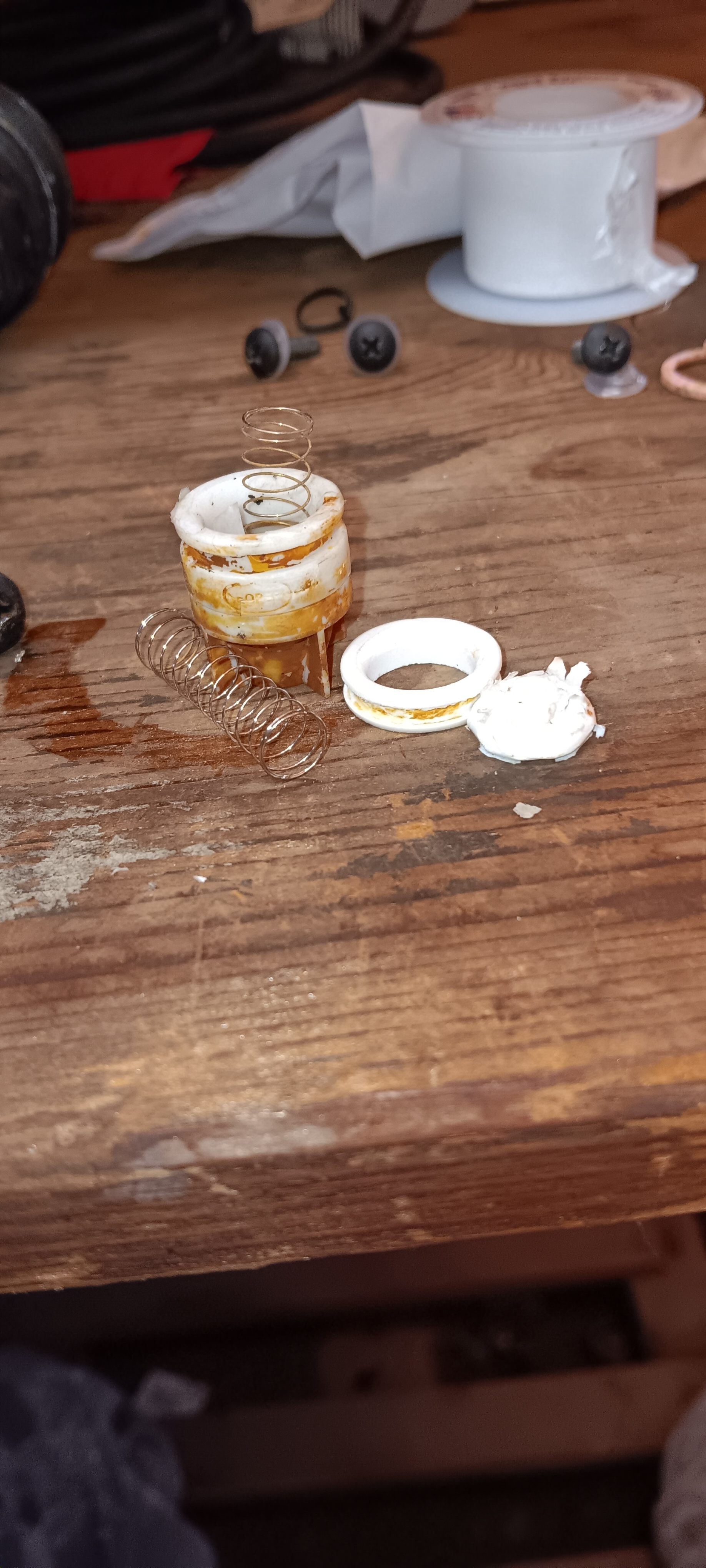
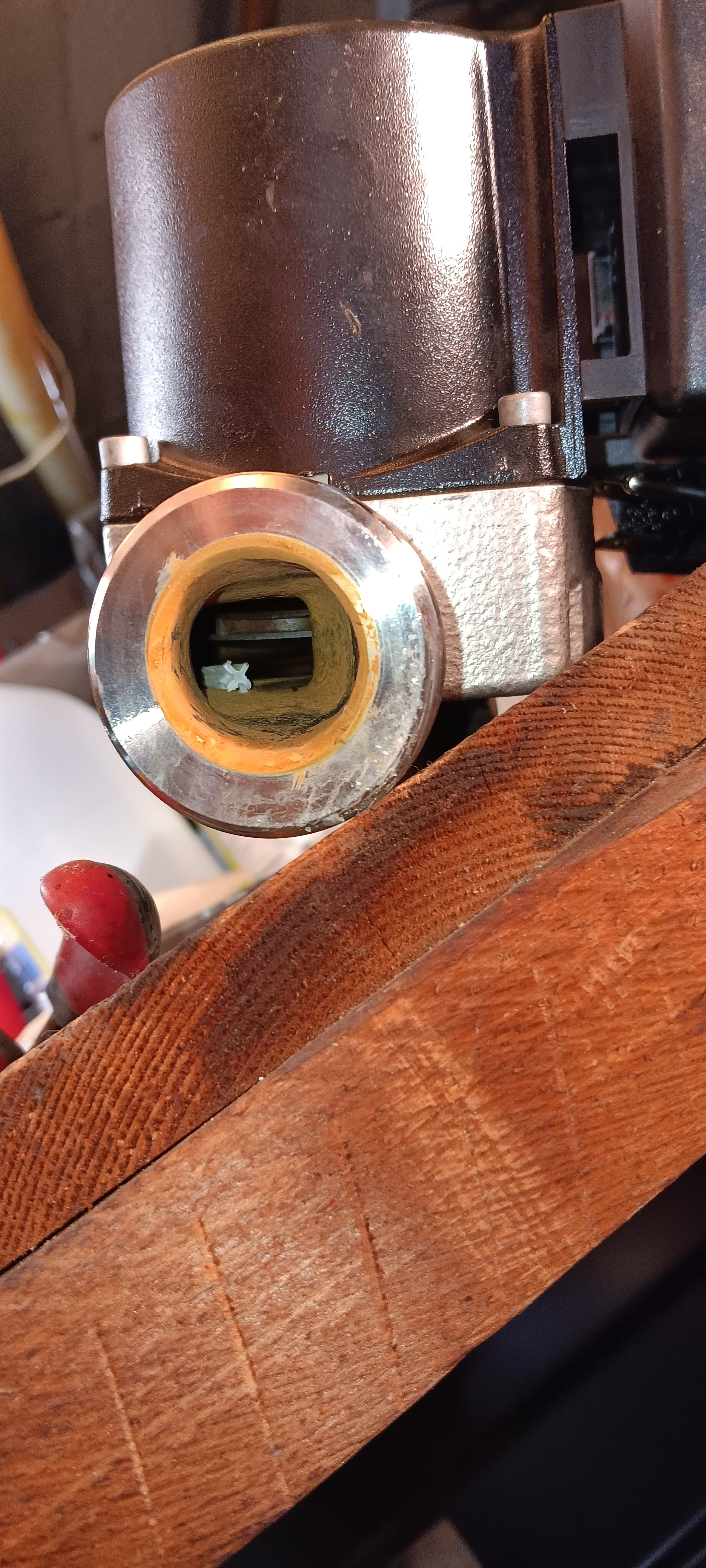
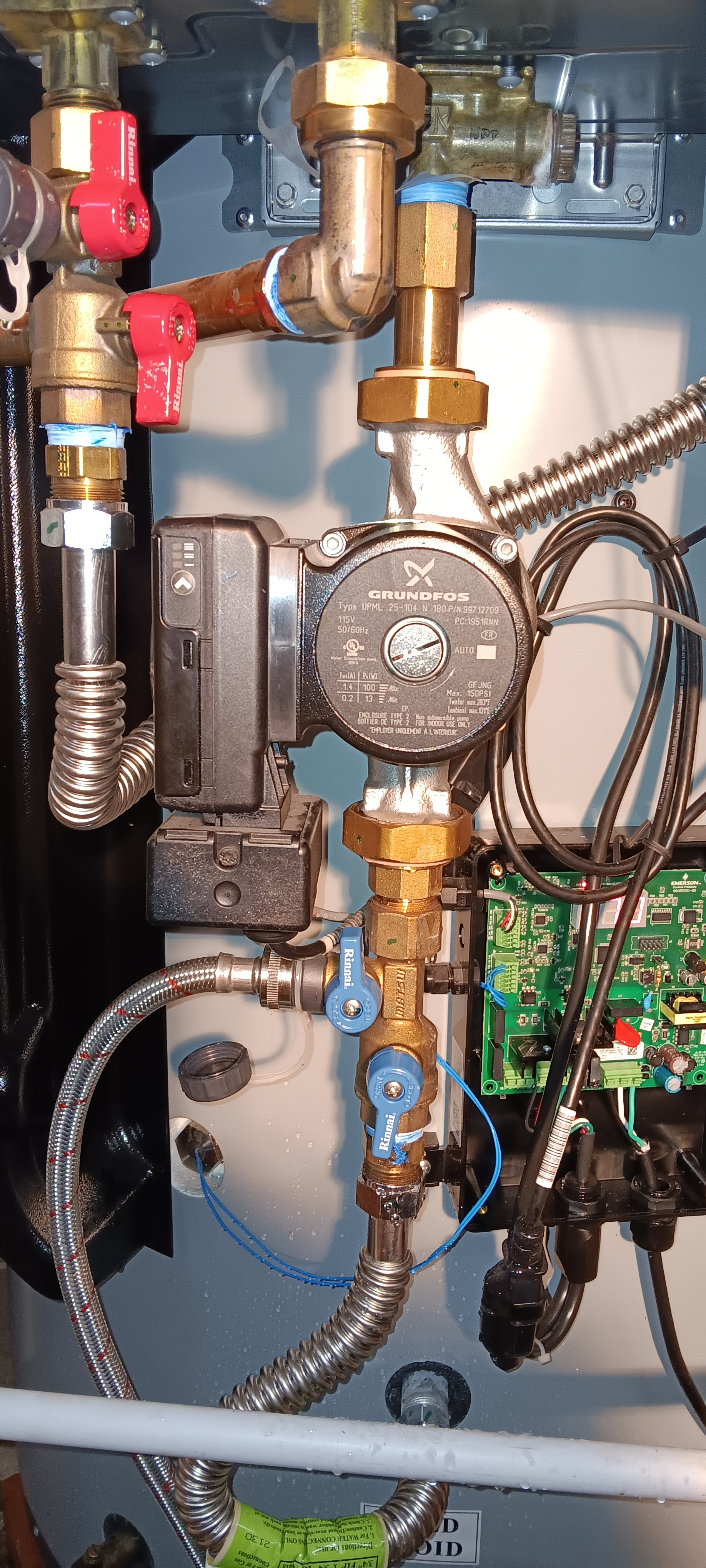
:
Under normal operating conditions, this check valve "sees" equal storage tank pressures (aprox. 65psi pressure) on both sides of its "in" and "out" ports ...... in a closed loop!
As the pressures are equal on both sides ...... there is no significant pressure stress on this check valve itself.
The pressure differential is null and cancelling. The check valve only needs to control the very low "closed loop" pressure differential generated by the circulator pump itself.
I suspect the reason for check valve failure is possibly one of two different scenarios.
One:
The service tec is there to perform the system vinegar "flush" and turns off the cold loop valve port and (out of recommended step procedure) inadvertently or seeing no harm in doing so, opens the cold water drain valve right next to it.
This now exposes the check valve to (65psi) water pressure on just one side, the flow blocking port side, the other side to only atmospheric drain pressure (14psi) and explodes into the circulator. I don't feel this check valve was ever designed to survive such pressures.
Two:
The pump that the service tec is using for system flush is way oversized (pump generated PSI and flow rate) and exceeds the check valve's pressure tolerance.
Please advise to this matter ASAP
Please call if I can be of any help in this matter.
Thank-you!
Comments
-
Very interesting... yes that check valve is broke! I really hope to hear from Ben! : ) soon, I want to hear what he has to say about this
Edward Young Retired
After you make that expensive repair and you still have the same problem, What will you check next?
0 -
Neoperyl builds checks for that application. It doesn’t seem like that pressure or temperature is excessive. The PR series even has a relief function.
I’m not sure about a vinegar rating?Bob "hot rod" Rohr
trainer for Caleffi NA
Living the hydronic dream0 -
mmmmmmm ......... the outer cylinder is made in two pieces! Look how it perfectly separated at the mating joint.
Bad ultrasonic or spinweld?? ...... they didn't glue them together I hope! : (
MATERIALS AND APPROVALS
All NEOPERL check valves are made from POM. This plastic is particularly suitable for continuous operation at 65 °C (149° F) and for short periods of time at 90 °C (194° F).
Check valves for use at high temperatures are made from NORYL plastic – a material that can withstand a constant temperature of 127 °C (260.6° F).
Our standard materials for seals in the drinking water sector are EPDM, silicone and NBR.
NEOPERL check valves meet all the relevant hygiene and mechanical approvals for use in drinking water and have been tested to DIN EN 13959.
I had set our twin units to "commercial temperature" mode running at set temps of 180 F
........ maybe the spring check that's in this heater is of the lower temp grade material??
I found our NEOPERL check valve on their website. This model DOES NOT have the self-retaining "claws" on this version (as do others in their product line) A separate retaining clip (by others) must be provided.
Also, this model was NOT designed to survive the commercial temperature range of our Rinnai CU199iN Duo units.
The plastic they used (POM) is of a max 140 degrees F.
Rinnai should have specified the use of the higher max temp version of 260 degrees F (NORYL high temp plastic ) for this check valve.
0 -
Not sure this is considered a closed loop, isn’t it designed to take the cooler water from the bottom of the tank, heat it up thru the tankless and put it back in the tank and then ready to go out to the fixtures making it an open loop system?
During the ‘flush’ the cold and the hot valves are shut off and the hoses connected to the service ports.. there would be no additional pressure added to the check valve during that procedure as the plumbing system would be isolated from the tankless.
That would be a very large pump to able to produce that much psi when both the cold and hot ports are open and circulating the flush solution out of a 5 gal bucket
I think they allow 150psi max on the supply side wouldnt think they would put a check valve in that’s rated less than that. Just my thoughts.0 -
........ I think I found the reason for this failure!
149 F degree Max!!! I'm working a set temp at 180 F
Looking at NEOPERL's website ..... it looks like the higher temp material NORYL (260 F max) and is gray in color.
Our check valve is bright white! : (0 -
@HillTown:
Not sure this is considered a closed loop, isn’t it designed to take the cooler water from the bottom of the tank, heat it up thru the tankless and put it back in the tank and then ready to go out to the fixtures making it an open loop system?
Its "closed loop" when no one is using water! ....... open loop if they are at that time.
During the ‘flush’ the cold and the hot valves are shut off and the hoses connected to the service ports.. there would be no additional pressure added to the check valve during that procedure as the plumbing system would be isolated from the tankless.
Agreed! ..... but as I stated in the event of one feed open and the other closed to pressure.
160PSI on closed side (Flow Blocking Port) ..... atmospheric pressure on open side.
I think they allow 150psi max on the supply side wouldn't think they would put a check valve in that’s rated less than that. Just my thoughts.
Agreed! ..... maybe just the wrong max temperature grade of plastic.
0 -
WOW!! .... I'm in total shock here guys! : (
Received our new replacement spring check valves and water filters for our Rinnai CU199 today.
This spring check valve gets slid into place and rests up against an internal stop ridge when fully inserted.
As you can see in the attached pics, there is a black "O" ring around its outer diameter for water seal around its body.
By simply applying the little force necessary to push this into its proper seated position, the entire check valve completely disassembled itself and fell into five separate pieces all over the floor !!!!!!
The two halves of this check valve are NOT in any way "bonded" together (ie: ultrasonic, spin weld, etc) as a one piece unit.
You can almost blow on one end and the entire check valve will disassemble itself! (NO JOKE!)
The attached pic here is NOT my "old" valve, but the NEW one that fell apart!
OK .... so I put all the pieces back together, and carefully slid the check valve into its proper position.
Then I realized something, the ONLY thing holding this check valve from sliding down directly all the way in into the circulator housing, is ONLY the little friction afforded by the black "O" ring !!!!!!!!!!!!!!!!!! : (
This is a major design flaw with extensive operational repercussions to the heating system.
Probable cause and effect conditions that invoke this failure mode:
Inadvertent or simply "burping" trapped air in this heating "loop" by opening the cold water side drain cock (this causes the back flow pressure to blow the entire check valve into the circulator)
Under normal operation, the "water hammer" caused by the quick "snap" opening and closing of the solenoid valves of our commercial washers will over time nudge and nudge the check valve down free of its poor retention and fall right into the circulator.
The normal thermal expansion of the water itself (even with the required expansion tanks working) exerts it's force to eventually unseat this poorly restrained check valve.
0 -
...... and in a related issue:
We also had to replace the water filters as well (see attached pic).
Were normally you would just have to clean them, the plastic rings and support arms retaining the screen mesh in place, experienced breakoffs of the plastic itself.
These filters small break-offs get to migrate throughout the entire heating unit (ie: heat exchanger, servo valves, etc).
So, when the check valve falls down into the spinning vanes of the circulator pump, in five separate pieces , it chews these pieces into smaller bits that passes back thru (in forward circulator flow mode) passing these plastic pieces past the filter mesh then throughout the system.
0 -
Wonder if those are the same checks in a taco IFC or Grundfoss, look of similar design0
-
The check is in the pump or the boiler connection? Those are the same checks as the pumps use.
I wish the circulator manufacturers would use the black high temperature versions. Although the check in a pump is in the worse possible location for turbulent conditions. I suspect many rattle themselves to death.
What type of transfer pump was used? It sounds like it failed from the cleaning procedure. A small sump type pump is all you need to circulate a cleaner. The one that comes with tankless kits may only develop 10-20 psi.Bob "hot rod" Rohr
trainer for Caleffi NA
Living the hydronic dream0 -
@HotRod:
What type of transfer pump was used? It sounds like it failed from the cleaning procedure. A small sump type pump is all you need to circulate a cleaner. The one that comes with tankless kits may only develop 10-20 psi.
Its a simple bottom suction type that you hook-up a garden hose to and the top outlet hose port.
Same like one would use to skim the water off your swimming pool cover.0 -
so, think about this:
Want to prove your check valve is working? (blocking back flow pressure)
Simply open the cold drain cock .......right? No water coming out, check is good!
..... well, in doing that test, the working check valve will unseat and pass back flow water out to the drain port!
Now , go looking for your check valve inside the circulator housing! : (
0 -
If the brass tailpiece can not captivate the check, usually there is a groove inside to use the snap tab version checks. The only way to remove these is to break them.
Maybe the wrong style checks were installed?Bob "hot rod" Rohr
trainer for Caleffi NA
Living the hydronic dream0 -
...... as I've noted before, there is a stop ridge inside the brass tubing where it resides. This stops the check from ever moving upwards towards the filter element.
...... but nothing to stop the check from dropping into the circulator pump housing!
Hard to believe I know! : (0 -
I'm curious what the logic for the check valve being there is?
Edit: No ideas? I guess this is my sickness, asking questions. I'll have to ask a Rinnai engineer I suppose. It looks pointless to me. Much ado about nothing.0 -
...... this should be an easy fix, if for when they are lathing in the internal stop ridge for this check valve, ....... they simply lathe in a groove at the insertion end of the brass containment tube for an internal snap ring for the check valves proper containment.0
-
There should be a groove machined into the brass for the NV style checks, if there is no other stop mechanism.
Maybe a batch were machined without the groove.
Hard to tell from here😏Bob "hot rod" Rohr
trainer for Caleffi NA
Living the hydronic dream0 -
...... there is only a stop ridge lathed in so it cant migrate upwards ..... but no groove for a snap ring to retain check when seated.hot_rod said:There should be a groove machined into the brass for the NV style checks, if there is no other stop mechanism.
Maybe a batch were machined without the groove.
Hard to tell from here😏
its just a smooth bore out to the insertion end.0 -
I doubt it was designed to have a check just floating in the nipple. Did you call tech support?Bob "hot rod" Rohr
trainer for Caleffi NA
Living the hydronic dream0 -
Where are you located they have factory reps and training centers in various location. The reps I know for that brand are very knowledgable.
Bob "hot rod" Rohr
trainer for Caleffi NA
Living the hydronic dream0 -
Bristol, PA
0 -
Rinnai engineering is looking into this issue as now.
Thanks!0 -
@RickDelta Did they say why it's even there?0
-
No ........ Their still looking at this issue.Teemok said:@RickDelta Did they say why it's even there?
I'll ask them.
The way this spring check broke apart, it appeared to be a simple heat flow restrictor at first (same as would see on many residential hot water tanks at the inlet and outlet pipes) ..... a disk to stop the idle state heat migration out of the tank.
Basically, I think this check valve is serving the same function and probably to negate any undesired flow influence from the external "keep alive" return flow circulator loop.0 -
I found a simple fix that strongly retains the spring check from ever dropping into the circulator again!
I got a fender washer from HomeDepot that fit perfectly inside the circulators union black sealing gasket.
This thin fender washer is thinner than the sealing gasket leaving plenty of seal compression left.
The fender washer center hole diameter is equivalent to the flow port size of the check valve.
This retainment fender washer now negates any and all conditions that would otherwise unseat this check valve into harms way.
Now all I need from Rinnai is this spring check valve in the available high temperature version so I can run this CU199iN in its commercial high temperature mode
0 -
If the intent is a heat trapper check, I’d be inclined to leave it out. That high temperature operating condition is not ideal for that version check assembly. What problem woulda small Thermo siphon cause? If it even would thermosiphon.
Typically thermosiphon happens with piping going up from a water heater. Hot buoyant water rises, cold falls. I don’t see that even being an issue.
In this installation, flowing down.
Again, assuming that is the intent of the check?Bob "hot rod" Rohr
trainer for Caleffi NA
Living the hydronic dream0 -
Hi Bob!hot_rod said:If the intent is a heat trapper check, I’d be inclined to leave it out. That high temperature operating condition is not ideal for that version check assembly. What problem woulda small Thermo siphon cause? If it even would thermosiphon.
Typically thermosiphon happens with piping going up from a water heater. Hot buoyant water rises, cold falls. I don’t see that even being an issue.
In this installation, flowing down.
Again, assuming that is the intent of the check?
I hear ya!
My thoughts on your rational into this, is that this highly compact, sensor loaded, sensitive servo controlled valves, etc , design of this unit, that "thermosiphon" may now play a significant factor in its ability to achieve its high efficiency.
Typically thermosiphon happens with piping going up from a water heater. Hot buoyant water rises, cold falls. I don’t see that even being an issue.
In this installation, flowing down.
I think you would agree that manufactures of today don't add a dime to the system costs on anything that's not needed.
I'm sure the engineers at Rinnai will be able to explain its design function and cost justification.
I suspect the reason might be that in this very compact area loaded with a ton of sensors inches from each other, the very high temperatures created in the heat exchanger, only inches away from the by-pass mixing servo and only inches away from the bottom of the tank cold water draw ..... that the second law of thermodynamics (heat migration to cold) now plays a significant disturbing factor in such a computer fast managed system.
....... and something else to think about:
Our conversation has been based solely just on the thermodynamics of heat in water only.
How about the thermodynamic effects in the metal piping within this unit?
Just put your hand on one of the pipes in there and you'll get a quick lesson in the heat conductivity in metal as compared to water conduction!0 -
It seem like a lot of stuff in the flow path to restrict any thermo induced flow?
It would be nice to know the purpose or problem that problematic valve is solving
An issue with the high temperature check is they are not available in all the sizes and configurationsBob "hot rod" Rohr
trainer for Caleffi NA
Living the hydronic dream0 -
"this highly compact, sensor loaded, sensitive servo controlled valves, etc , design of this unit, that "thermosiphon" may now play a significant factor in its ability to achieve its high efficiency."
Ahh... That's not real convincing. There's no logic for thermosyphon I can see. They put low temp plastic in high temp application. That's a mistake. It will be interesting to see what reason they come up with.
It's most likely this:
New engineer: Hey boss, the pump outlet union spud comes with a check in it. Should we leave it in it there?
Boss: Sure, why not.
New engineer: Done boss!1 -
Seems like it would have been easier to add a spring check under the flush port valve where the flex line connects..0
-
..... but that would not eliminate the catastrophic unseating of the check valve then entering into the macerating vanes of the circulator pump.hilltown said:Seems like it would have been easier to add a spring check under the flush port valve where the flex line connects..
0 -
UPDATE: Manufacture Fix
Hello Rick,
Apologies for the late reply.
I spoke the Rinnai Technical Services Department and they are recommending to replace the whole discharge fitting which will have the new check valve pre-installed. It is Rinnai part number 107000509.
0
Categories
- All Categories
- 86.7K THE MAIN WALL
- 3.1K A-C, Heat Pumps & Refrigeration
- 56 Biomass
- 423 Carbon Monoxide Awareness
- 104 Chimneys & Flues
- 2K Domestic Hot Water
- 5.6K Gas Heating
- 103 Geothermal
- 158 Indoor-Air Quality
- 3.5K Oil Heating
- 68 Pipe Deterioration
- 939 Plumbing
- 6.2K Radiant Heating
- 385 Solar
- 15.3K Strictly Steam
- 3.4K Thermostats and Controls
- 54 Water Quality
- 43 Industry Classes
- 47 Job Opportunities
- 18 Recall Announcements