Welcome! Here are the website rules, as well as some tips for using this forum.
Need to contact us? Visit https://heatinghelp.com/contact-us/.
Click here to Find a Contractor in your area.
Here’s to hoping I don’t mess this up
JShep
Member Posts: 23
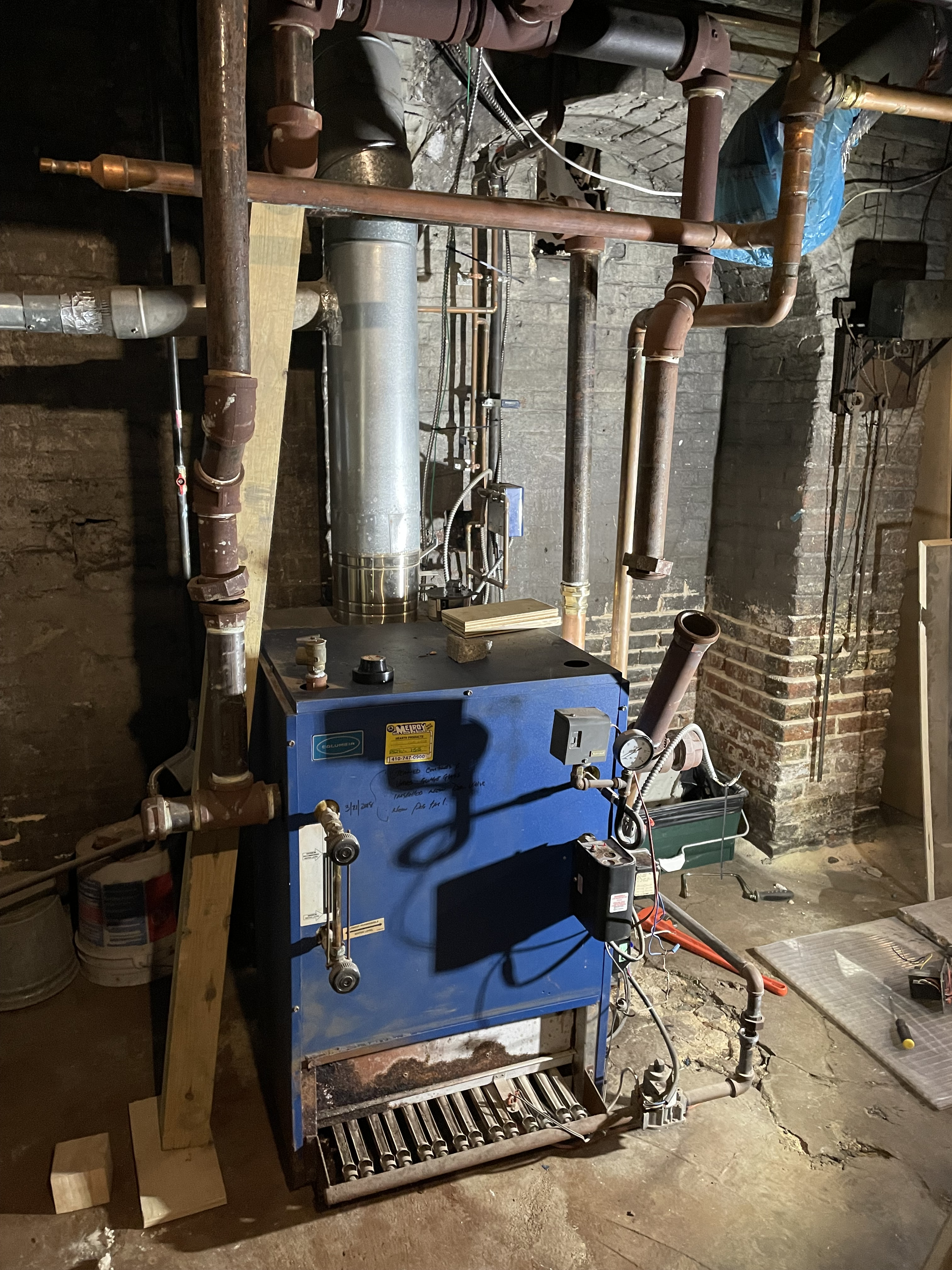
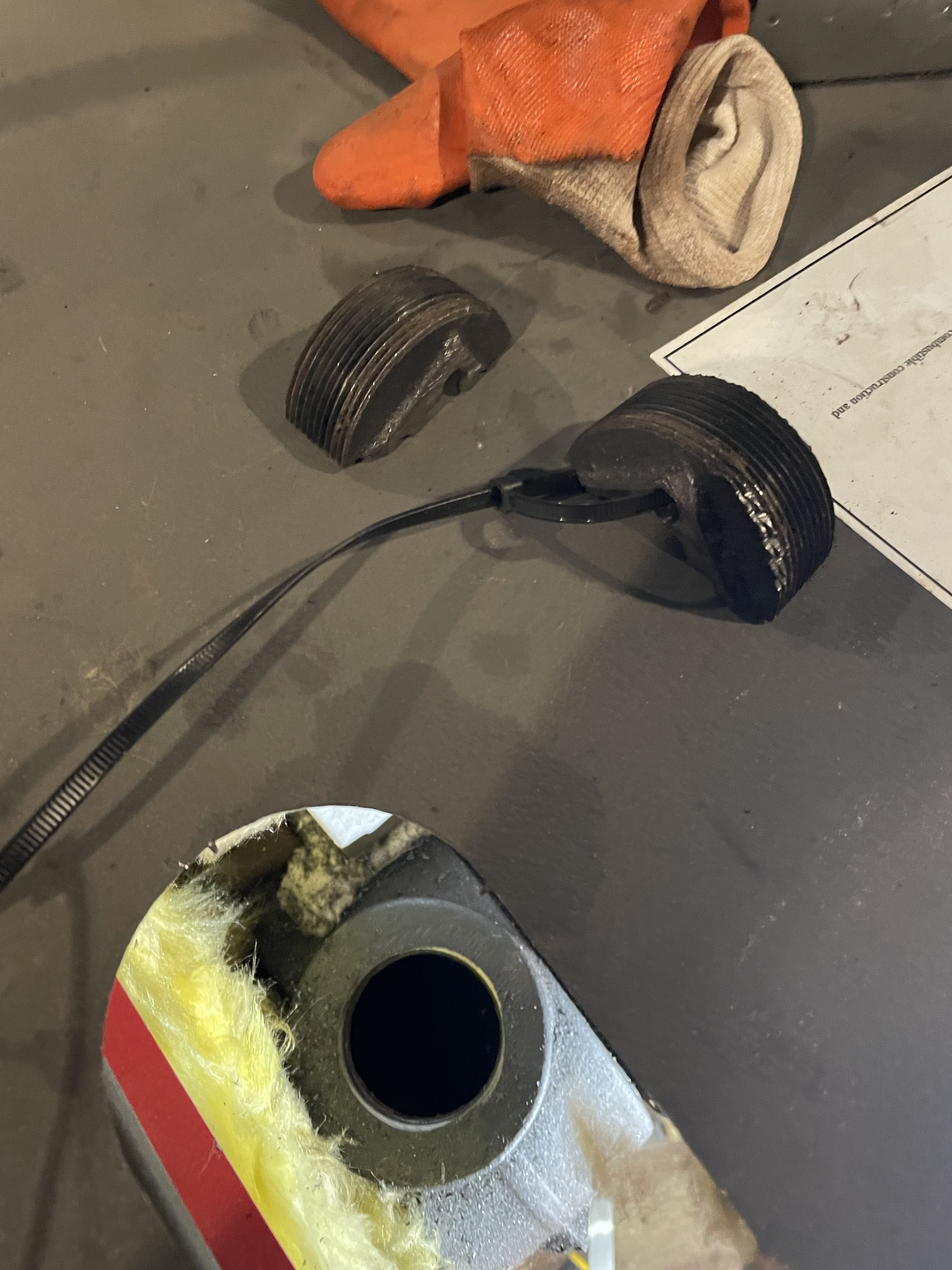
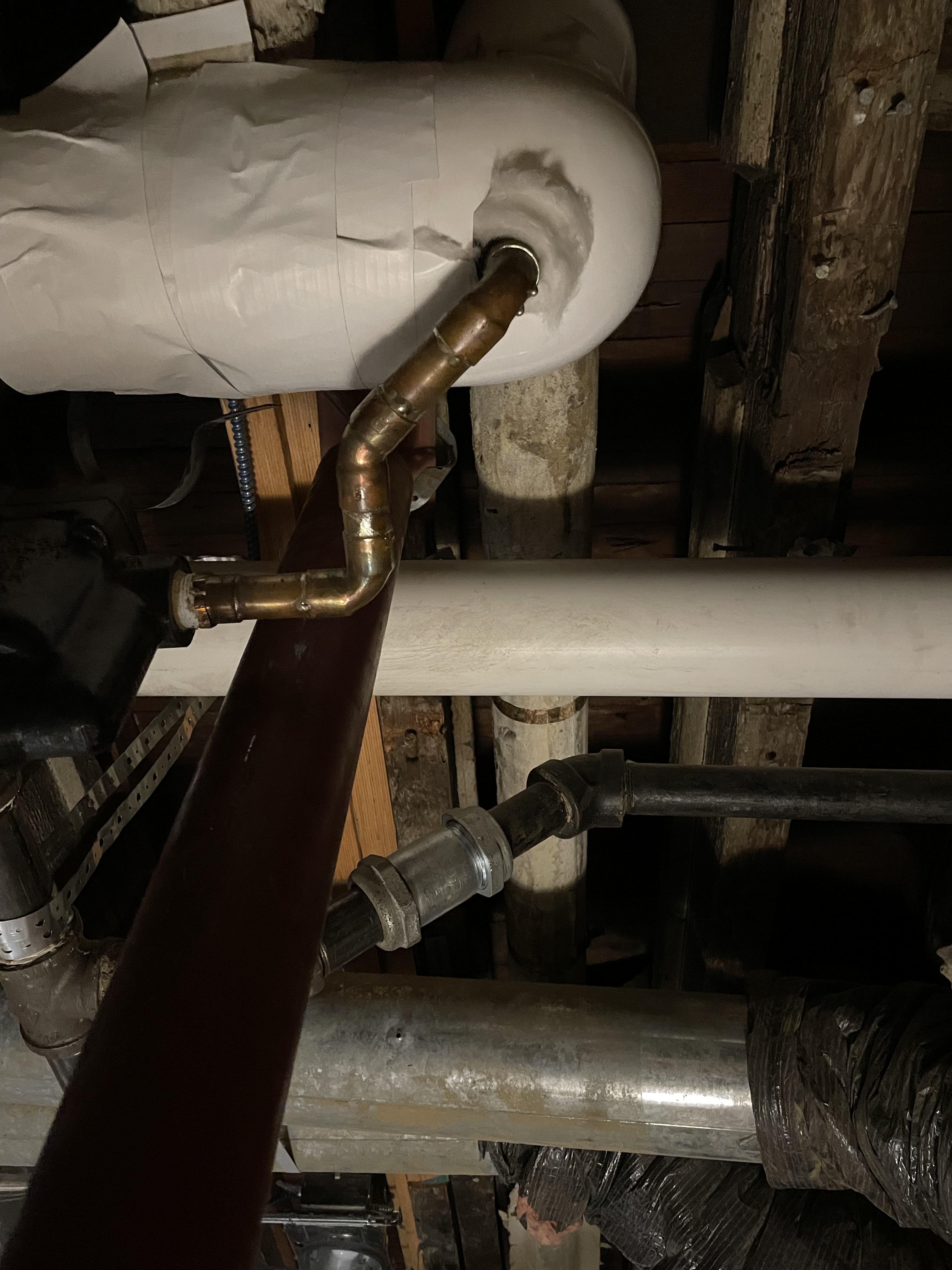
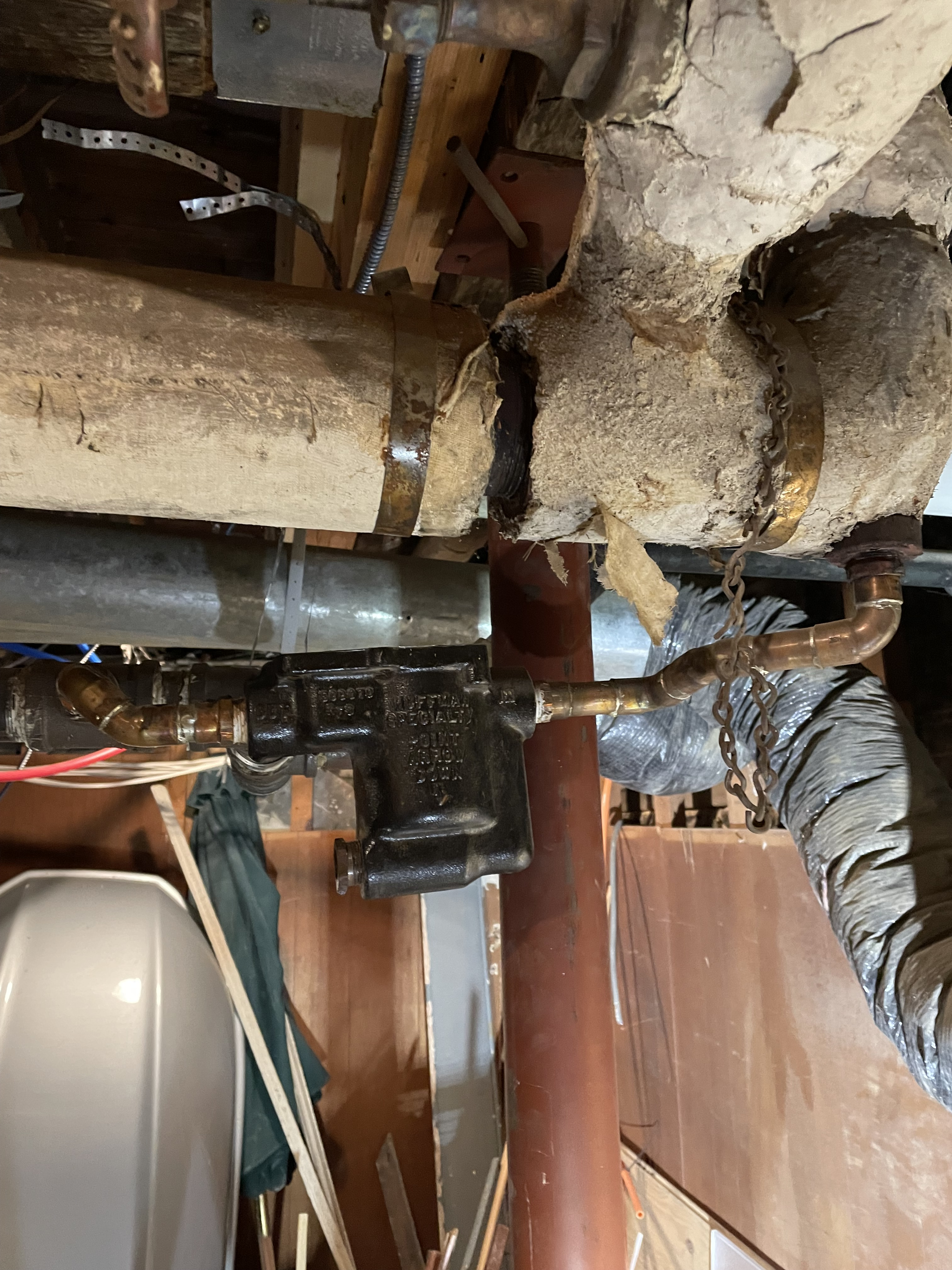
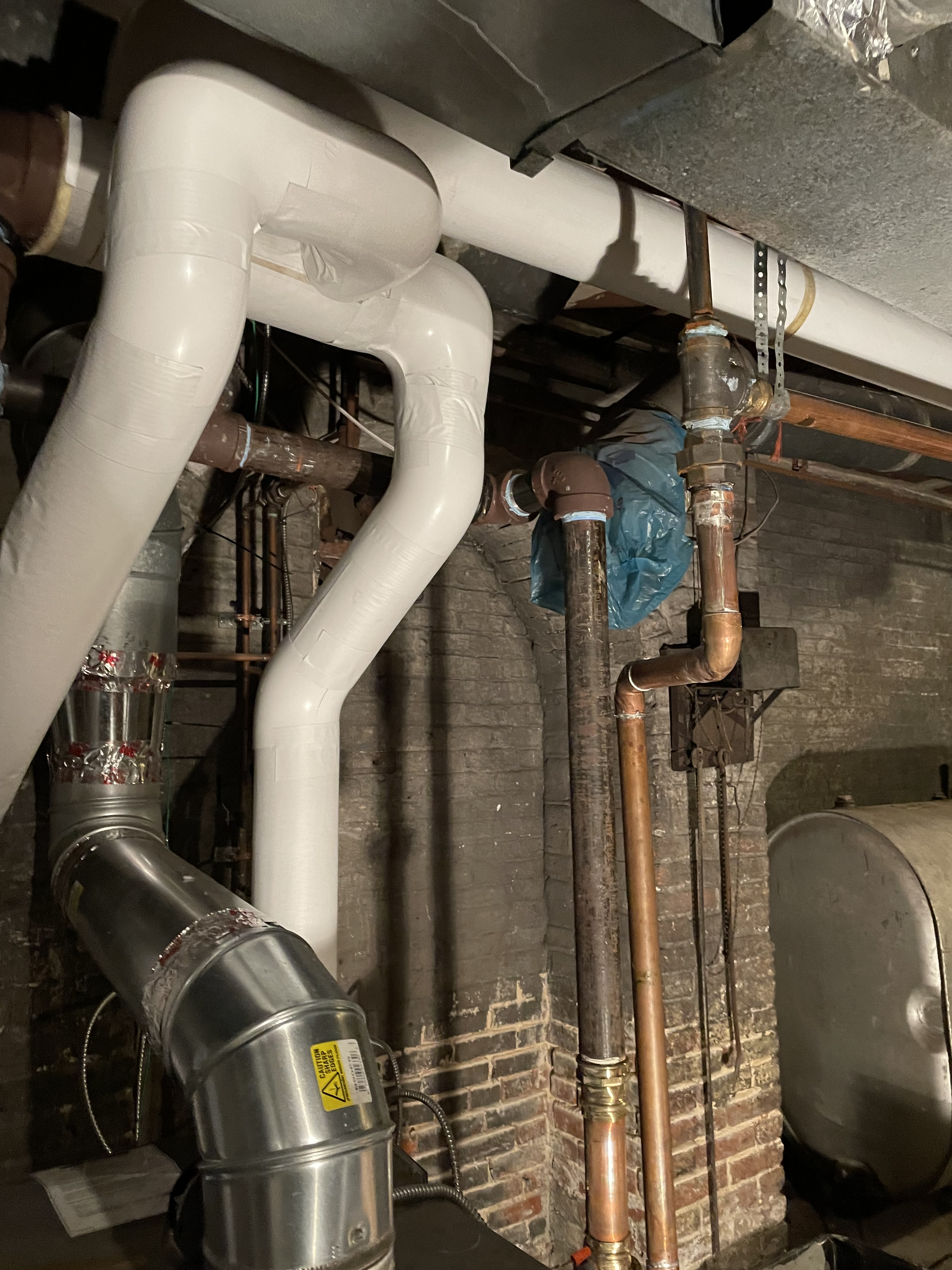
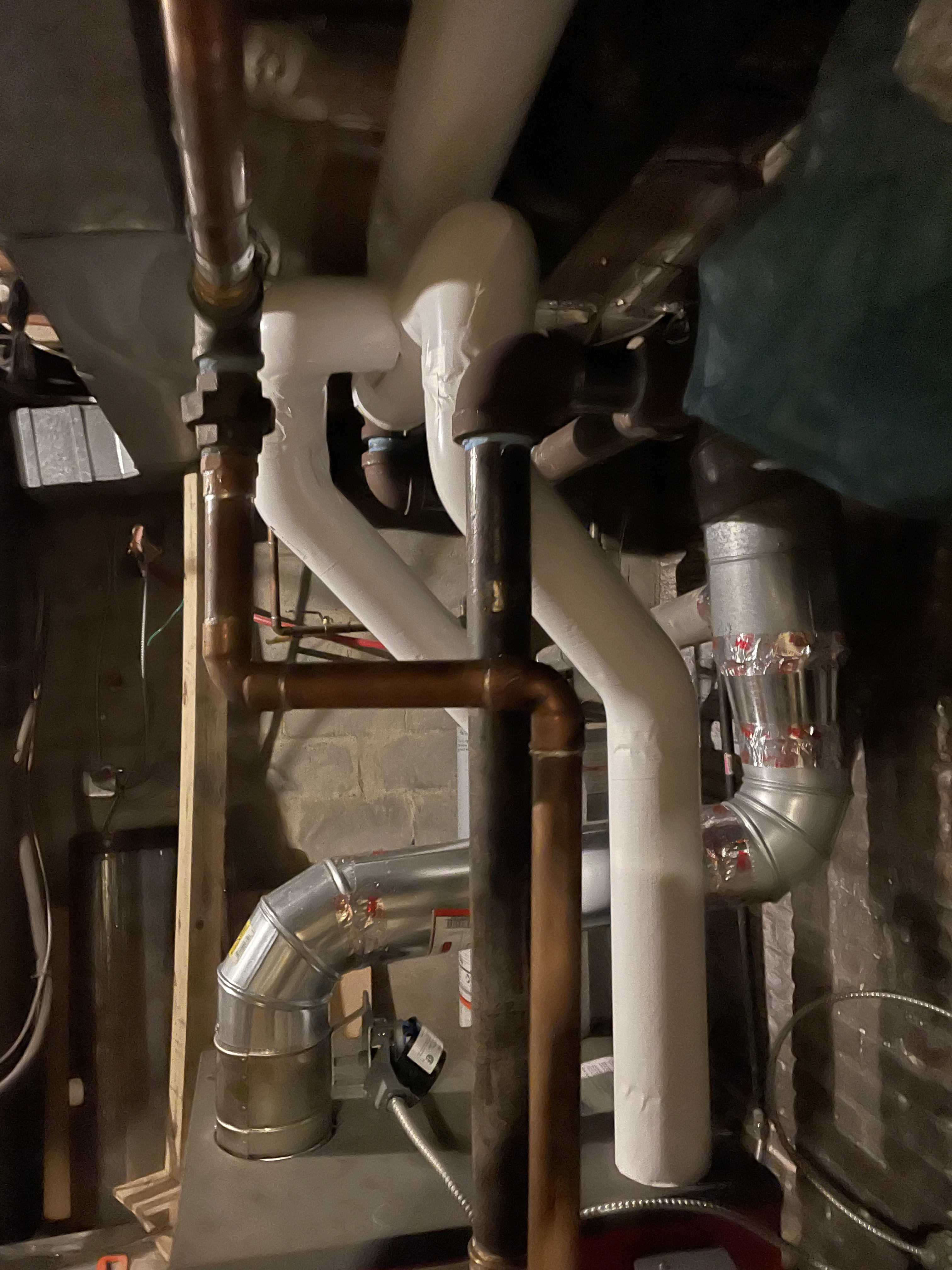
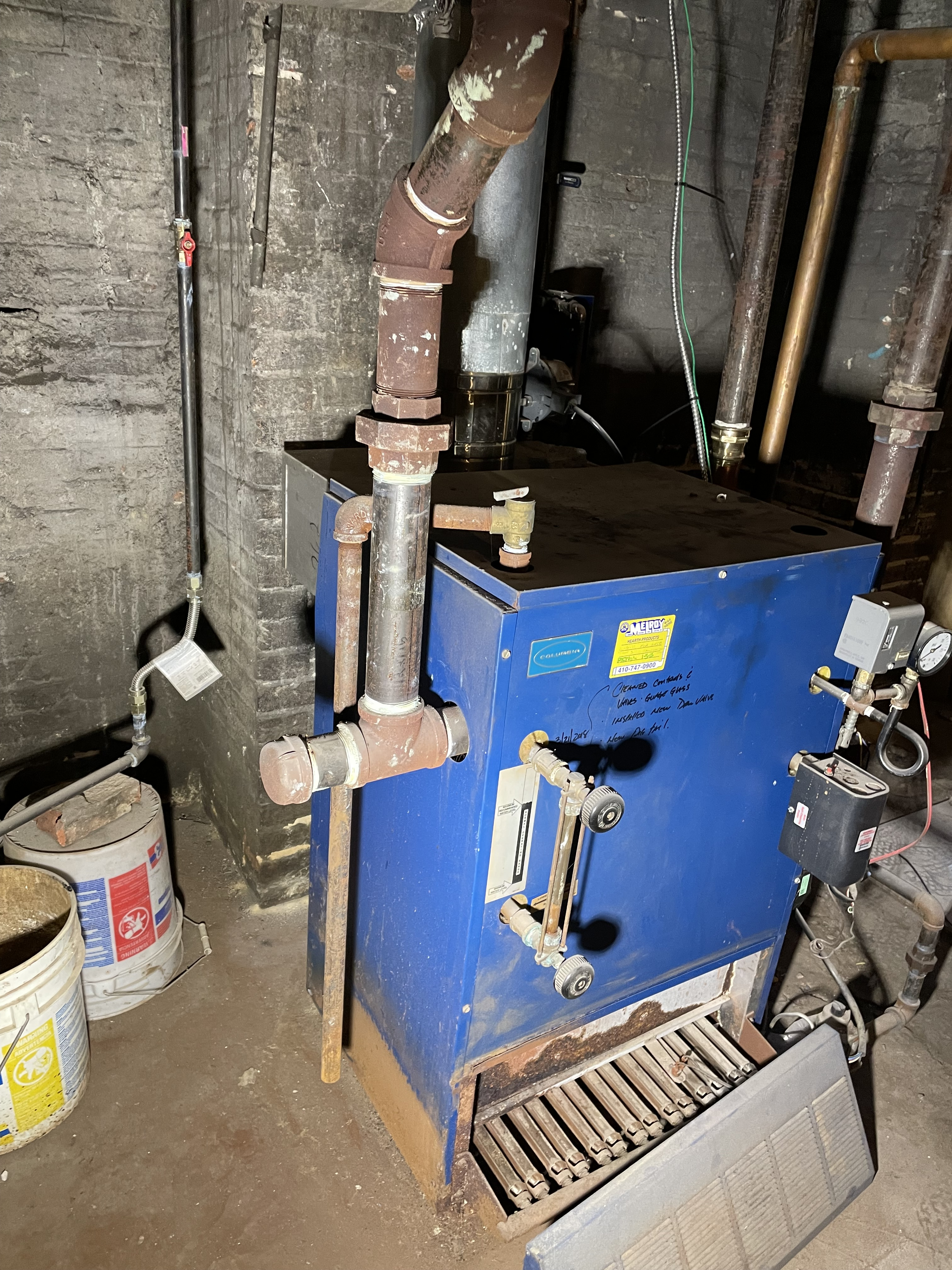

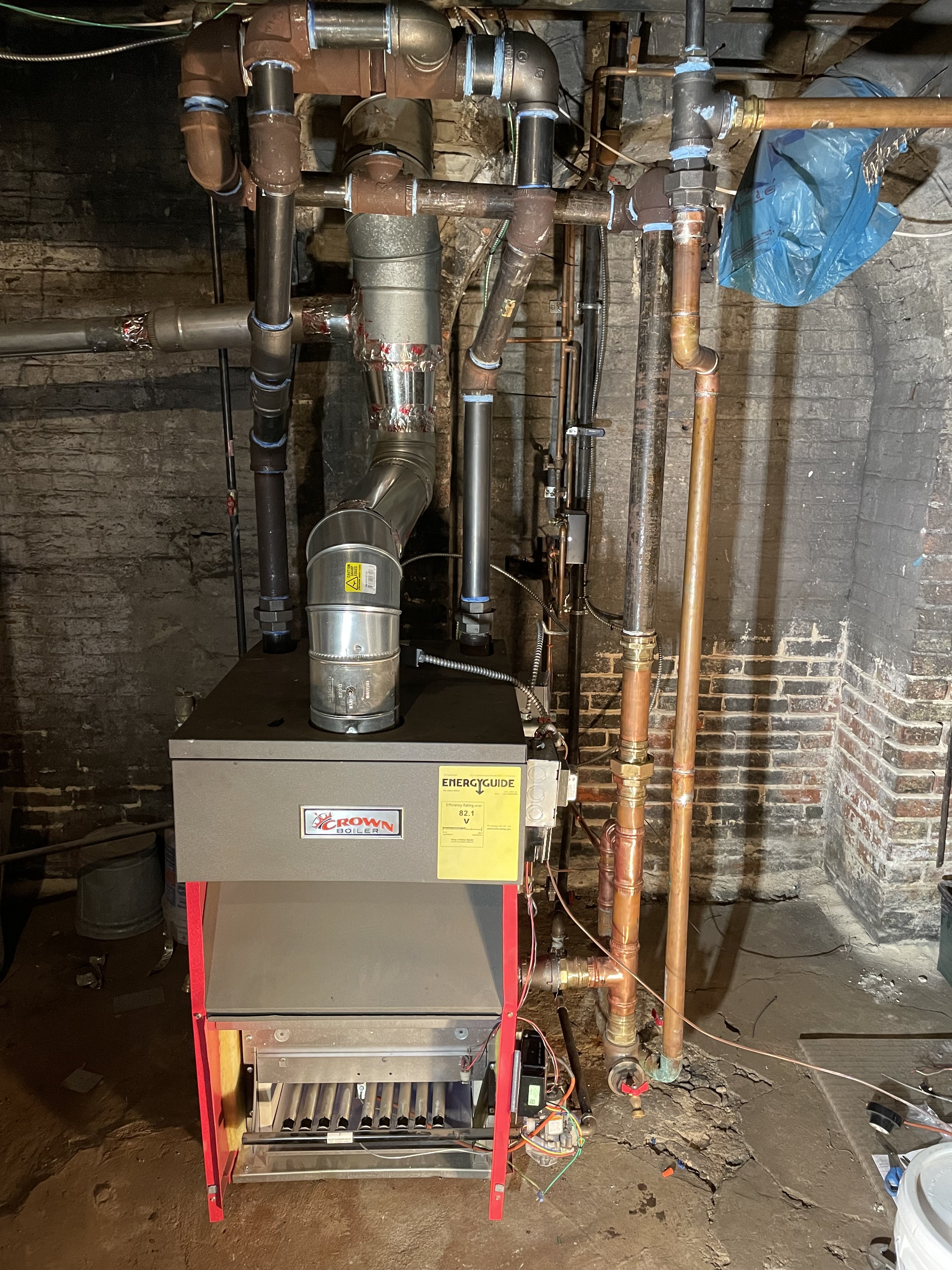
Last Thursday, following a same day call back from Gordon with him identifying an ignition wiring issue over the phone after I told him I replaced the ignition module with a universal Honeywell unit that apparently calls for different wiring than the diagram on the boiler… we have heat. THANK YOU GORDON.
Here’s where we are, and what I could use some theory help on:
- 6,000 sqft 5 story row house in Baltimore, built either 1845 or 1825 (city has both recorded), we bought in 2020.
- two pipe UVac (initial) steam system installed by UVac of Ellicott City in 1908. Excluding near boiler piping, 100% of the steam mains are original and 100% of the returns that run vertical are original, and the last ~50’ of the return line back to the boiler has been replaced with copper, seemingly over a number of years. The layout of the runs are still the same as the original plans.
-Crown Aruba 172k boiler (Mf’d 2018 I believe) that I got second hand and inspected with a plumbing camera.
I did the near boiler pipe work in the basic layout stipulated by crown (initial install on the boiler I bought was 1 supply, I dove back into summers plumbing with a dad and two uncles and had to break out the drill, cut, chisel method of removing the second cap to get the second main)… though short of having the ability to cut and rethread 115 year old 3” cast iron, I chose to leave the 90 that header feeds into well enough along meaning the new boilers layout had be about 10-12” offset from the header such that my risers have a pair of 45s (ignore the pair of 2” tees that I had and worked out so I could temp finish the repipe of the one riser and header return so I didn’t have to keep running all over while waiting for a 2” ratchet threader to arrive).
- three Hoffman crossover traps from the main to the return, one of which was replaced with an inverted bucket at some point. A Gorton number 2 at the end of the return before it falls back into the Hartford loop. Combination of Spirax, Hoffman, and a few other types of rad traps on each radiator, all of which either work (or possibly have failed open)
- heat is pretty well even, many original rads and original metered valves with wood handles… a handful I replaced that were previously mangled, had cross thread unions, etc, but I intend to do my best to find parts, turn new wood handles to replace the cracked ones, etc. probably 40 radiators in the house. We only live on the bottom 3 of 5 floors.
- if the system runs (2-3 cycles an hour) all day, we get mild hammer. If it gets warm enough outside that it sits for a few hours, we get real bad steam hammer.
- I believe my problem is that the previous owner had ball valves (just like… a normal ball valve) on the third floor to enable shutoff of floors 4-5 (which is ideal for us as well, as there is currently no plumbing run up to keep from freezing, and we are a good 5+ years around from diving back in to restoring those floors and using them… but) the setup doesn’t seem ideal for a two pipe system, because I’d assume much of the steam heading up a ~40’ vertical main from the basement to the third floor only feeds three small rads in one room on the third floor hits the valve and has no way out, eventually condensing and running back down three stories. Would a vent or a crossover trap be logical? I could in theory climb through the materials and storage… and literally everything the previous owner owned that’s stored up on the 4th and 5th floor to check the operation of the 15 or radiators up there such that I could fully open the system, but I’m not real keen on that in terms of regular visibility since everything up there is the original 1908 pipe and valves and traps (the prior owner seems to have fiddled with replacing some trap internals and he was pretty meticulous) as we’d also be heating unused parts of the house for no reason.
-I’d guess that for some period of time, this didn’t cause much of an issue until a first floor forced air conditioning system was installed what looks like 5-10 years before we bought the house which prompted an idiot to remove the iron hangers on a 2.5” main 16’ long such that I’m under sloped for condensate in the main that’s got 20’ of run past the last crossover trap. I can hear and feel the steam and a slug of condensate battling their way across that run.
- on top of that issue, at the end of that 20’ long 2.5” main, there’s a 3/4” drop fitting (looks to be part of the original elbow, but at some point fitted with copper and a Hoffman inverted bucket trap that was JAMMED with sludge; properly cleaned, drain, and checked every day for the past week) that as a result of a 24’ long 6x16” beam breaking free due to ages of water damage breaking the sewer main and shifting resting on the steam main (by old notes from the prior open, this happened in ~2010) which I believe the bucket trap was compensating for as currently the the return runs parallel to the main right there, such that the original crossover trap would have had to run uphill an inch to drain off, but ultimately condensate more than fills the bucket and settles above it.
my thought, or my question is, with so much condensate happening here due to a combination of bad slope, and inability for a solid column of steam to go anywhere other than back down the main since a lot of it is hitting a ball valve rather than going into a return, I see a few possible short term options to eliminate my hammer, but I’m real new to steam (I’m the son of a plumber, with two uncles and a cousin that are plumbers, stemming from a line of steam fitters before them… steams a different animal, but I’m not afraid to put in the work).
- would a vent or a crossover trap where the ball valve segmenting off the top two floors to give the steam somewhere to go be wise, and help the hammer? (And also, I’d assume replacing the standard ball valves with a proper gate valve would be wise?)
- the area the bucket trap is in the basement, at the same level as the return line so there’s no gravity win to be had… can I run that off to a secondary return so I can achieve proper slope below the existing return and tie it in below where the existing return falls into the Hartford loop?
- right in that same area, the main breaks off in two directions, with a 2” run headed towards the back building 15’ that’s capped off with no outlet (the back building main and return were buried in the dirt below the subfloor and crumbled in my hands when rebuilding the entire floor structure on the first floor. With 2 of 3 levels in the rear building being 3 season rooms… I abandoned the dead piping, and the prior contractor capped the line off with a 2” SS mega press… I know I ultimately need to remove the going nowhere 15’ long 2” main, but haven’t gotten there yet and plan to eventually re-run it through a seal chamber outside to get some heat back into the back building at some point… I just know it’s contributing to settling condensate fighting against the steam, so I’ll pull and cap it soon
pictures attached, tear me apart, help me out… but count me all in on being committed to steam. Three floors of having restored the 200+ year old floors, plaster, and more should help confirm I’m playing for keeps and trying to pay tribute to the old dead men that paved the way.
Jeff
Jeff
Baltimore
Baltimore
2
Comments
-
-
Nice job on getting that plug out.
The foil tape on the flue is not code complainant. There is no foil tape that is listed and labeled for connecting flue pipes. It should be 3 screws per joint, evenly spaced.
Whats with the flexible gas appliance connector being supported with a brick on a bucket? As far as I know, bricks and buckets are not approved materials to support natural gas piping.0 -
The foil tape was actually just a temp hold while I didn’t want to run out to pick up the right screws… prior install had the hot water heater vent tied into the same line by way of 4-5’ length of rigid duct pipe and a 1’ makeshift extension to cover the last mile made almost entirely out of foil tape… so even my short term foil tape to hold things together while waiting to grab screws was an upgrade.
The flex gas line runs to the hot water heater, thanks to whatever fool put it in for the previous owner back in 2014… the bucket/brick is actually just a coincidentally place bucket with a brick I kept tripping on top that looks like it’s supporting it, but there’s no vertical drop out for debris at the bottom of the run and you should get a load of the two past supply/outlet runs with the old galvanized pipe left in place with a fitting stolen from it presumably because the installer was missing a copper fitting, partially because the unnecessarily branches off a pair of 3/4” runs 20’ away from where they should have logically split from 1” to a pair of 3/4” lines. Not sure if it was Gordon or the original steam company I had out that at first said “yea… probably not going to come out because we’ve got years of recommendations with the minimal, ‘fix only the right-now problem’ approach being taken” … fortunately, with big long life projects (like the roof, and for the most part the electrical) the previous owners took the appropriate, full scale approach. The plumbing I’ve mostly fully redone the entirety of the past sins committed; the water heater is on the docket for spring to be replaced with a gas fired tankless unit at which point I will re-run it with all black pipe.Jeff
Baltimore0
Categories
- All Categories
- 87K THE MAIN WALL
- 3.2K A-C, Heat Pumps & Refrigeration
- 58 Biomass
- 427 Carbon Monoxide Awareness
- 113 Chimneys & Flues
- 2.1K Domestic Hot Water
- 5.7K Gas Heating
- 109 Geothermal
- 161 Indoor-Air Quality
- 3.6K Oil Heating
- 70 Pipe Deterioration
- 994 Plumbing
- 6.3K Radiant Heating
- 391 Solar
- 15.4K Strictly Steam
- 3.4K Thermostats and Controls
- 55 Water Quality
- 44 Industry Classes
- 48 Job Opportunities
- 18 Recall Announcements