Welcome! Here are the website rules, as well as some tips for using this forum.
Need to contact us? Visit https://heatinghelp.com/contact-us/.
Click here to Find a Contractor in your area.
Thinking about o2 in modern closed loop hydronic systems
Options
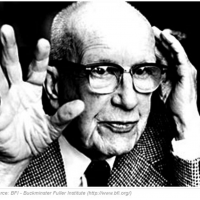
Teemok
Member, Email Confirmation Posts: 760
I did some google search reading in an effort to understand the risks of o2 in modern closed loop hydronic systems. Also to understand the need for mitigation of the resulting iron oxide byproducts in systems that I'm designing, installing and servicing. Context for this is residential and light commercial applications with little iron in them beyond pumps and radiators. I found a lot of hydronics 101 basics, industrial scale maintenance policy and efforts, trade articles and product manufactures edu-info-merial sales material.
The introduction of plastics into the industry caused problems. Oxygen was getting into systems that suffered when iron and oxygen do their thing. Mitigation of non barrier tubing and or the results bad design or poor or no maintenance is not what I'm interested in. I understand a lot of the industry is forced to deal with these things. Products and advice reflects that. Old compression tank systems also fall out side of this inquiry. I know a large portion of the market has lots of iron materials in use and are older with many years of magnetite built up in them. My exploration doesn't necessarily concern them but physics applies universally.
I'm interested in what is considered a good oxygen tight system. I want to know if magnetite build up is a real concern in modern well built system. Assuming they have good spec. water that's been treated. The low temperature design and heat pump movements in hydronics are pushing temperatures as low as can be and that makes getting o2 out harder. At the same time cooler water means slower corrosion rates from all causes.
Getting 02 out as fast as possible is a good aim but how fast is really necessary for a long lasting system? Is there a significant difference between reaching “dead water” / the lowest possible o2 levels in a system in 3 hrs.vs 40 or 72?
The best micro bubble separators installed in the right place (hottest up stream of the pump) work by using the water as a gas sponge soaking up gas in the system and ringing it out of solution at the hot low pressure separator vent location. That's the work they do. Old iron scoops do it too but not nearly as well. They do this job best in high temperature systems and if they prevent one air lock condition call back they are worth every penny. A good hydronic tech should be able to distinguish between a system that is prone to air problems and ones that aren't. Regarding all available hydronic components, blanket use of parts may make parts companies happy but it's not always smart or good materials use.
Achieving “dead water” has three levels of air removal: Pockets, bubbles and diffused gasses.
Pockets: Most well designed systems can be free of pockets fairly fast with venting, good purging, high temperatures and the right water velocities with or with out high performance air seps. There's a Goldilocks velocity range for transporting air from pockets and high points to vents. 2-5ft/s. Too slow and you can't move the air to the vent (it will eventually be absorbed if the system permits). Too fast and it will stay entrained in the flow missing the vent points. Pipe size is a factor.
Bubbles: They do come out over time. They come out easier with good design, higher temperatures, good circulation and collection points with vents. Hi performance separators are good at removing smaller bubbles in faster moving turbulent water. In many systems, even without a micro bubble sep, bubbles will eventually be expelled. This is where micro-bubble separators shine. Systems that let small bubbles cycle trough the loops can let bubbles group together and create an air lock and be a source of o2 causing corrosion. HP air seps. get bubbles out well and prevent air from redistributing and coalescing in places unwanted.
Dissolved gasses:
O2 in the dissolved gasses will react with available reactive materials in the system until it is consumed by chemical reactions. I don't think separators deal with dissolved gasses below a certain limit. Caleffi says: “Utilizes coalescing element to remove air and dissolved micro-bubbles in hydronic systems.” Is it dissolved gas they remove or micro-bubbles? I know dissolved gases are removed by the above mentioned sponge like process but there is a limit of effectiveness. Very small bubbles are what I know they handle well. Heating the water is a main driver of gas coming out of solution as micro-bubble formation. With cooler temperatures how effective are the small bubble catchers?
Diffusion rate /o2 intrusion/ permeation rate /how fast is o2 leaking into a closed loop water system?
We can't easily maintain a 100% o2 free system. After some hours of operation of a tight hydronic system, a near static state is reached, where o2 is slowly sneaking in and is reacting were it can, forming magnetite. This is an unavoidable fact. Inhibitors do help slow corrosion but the fact remains, o2 is continually getting in. The water in this state is as “dead as can be.” The rate that o2 gets in is very slow with o2 safe materials.
Yes micro bubble air separators do work faster and better at getting rid of bubbles. They are best practice but can they catch and expel the very small rates of o2 permeation into an oxygen tight system? Or are they ineffective at removing low level dissolved o2. Is that continual o2 intrusion into the system going to react with the iron regardless of the presence of a HP air sep?
The rate of system o2 permeation is a key factor in assessing corrosion risks. There's not much info out there I could find on this rate in systems using different materials. This very slow o2 intrusion in a tight system may be a real problem or it could be an industry paper tiger used to sell products. The ratio of o2 permeation to the available iron surface area can give a good idea of how long it might take for magnetite to cause problems. If the rate is so low that dead as possible water would take 30+ years to reach a problematic magnetite level or to breach a steel container, I'd say it's a non-issue for new tight low iron systems.
The introduction of plastics into the industry caused problems. Oxygen was getting into systems that suffered when iron and oxygen do their thing. Mitigation of non barrier tubing and or the results bad design or poor or no maintenance is not what I'm interested in. I understand a lot of the industry is forced to deal with these things. Products and advice reflects that. Old compression tank systems also fall out side of this inquiry. I know a large portion of the market has lots of iron materials in use and are older with many years of magnetite built up in them. My exploration doesn't necessarily concern them but physics applies universally.
I'm interested in what is considered a good oxygen tight system. I want to know if magnetite build up is a real concern in modern well built system. Assuming they have good spec. water that's been treated. The low temperature design and heat pump movements in hydronics are pushing temperatures as low as can be and that makes getting o2 out harder. At the same time cooler water means slower corrosion rates from all causes.
Getting 02 out as fast as possible is a good aim but how fast is really necessary for a long lasting system? Is there a significant difference between reaching “dead water” / the lowest possible o2 levels in a system in 3 hrs.vs 40 or 72?
The best micro bubble separators installed in the right place (hottest up stream of the pump) work by using the water as a gas sponge soaking up gas in the system and ringing it out of solution at the hot low pressure separator vent location. That's the work they do. Old iron scoops do it too but not nearly as well. They do this job best in high temperature systems and if they prevent one air lock condition call back they are worth every penny. A good hydronic tech should be able to distinguish between a system that is prone to air problems and ones that aren't. Regarding all available hydronic components, blanket use of parts may make parts companies happy but it's not always smart or good materials use.
Achieving “dead water” has three levels of air removal: Pockets, bubbles and diffused gasses.
Pockets: Most well designed systems can be free of pockets fairly fast with venting, good purging, high temperatures and the right water velocities with or with out high performance air seps. There's a Goldilocks velocity range for transporting air from pockets and high points to vents. 2-5ft/s. Too slow and you can't move the air to the vent (it will eventually be absorbed if the system permits). Too fast and it will stay entrained in the flow missing the vent points. Pipe size is a factor.
Bubbles: They do come out over time. They come out easier with good design, higher temperatures, good circulation and collection points with vents. Hi performance separators are good at removing smaller bubbles in faster moving turbulent water. In many systems, even without a micro bubble sep, bubbles will eventually be expelled. This is where micro-bubble separators shine. Systems that let small bubbles cycle trough the loops can let bubbles group together and create an air lock and be a source of o2 causing corrosion. HP air seps. get bubbles out well and prevent air from redistributing and coalescing in places unwanted.
Dissolved gasses:
O2 in the dissolved gasses will react with available reactive materials in the system until it is consumed by chemical reactions. I don't think separators deal with dissolved gasses below a certain limit. Caleffi says: “Utilizes coalescing element to remove air and dissolved micro-bubbles in hydronic systems.” Is it dissolved gas they remove or micro-bubbles? I know dissolved gases are removed by the above mentioned sponge like process but there is a limit of effectiveness. Very small bubbles are what I know they handle well. Heating the water is a main driver of gas coming out of solution as micro-bubble formation. With cooler temperatures how effective are the small bubble catchers?
Diffusion rate /o2 intrusion/ permeation rate /how fast is o2 leaking into a closed loop water system?
We can't easily maintain a 100% o2 free system. After some hours of operation of a tight hydronic system, a near static state is reached, where o2 is slowly sneaking in and is reacting were it can, forming magnetite. This is an unavoidable fact. Inhibitors do help slow corrosion but the fact remains, o2 is continually getting in. The water in this state is as “dead as can be.” The rate that o2 gets in is very slow with o2 safe materials.
Yes micro bubble air separators do work faster and better at getting rid of bubbles. They are best practice but can they catch and expel the very small rates of o2 permeation into an oxygen tight system? Or are they ineffective at removing low level dissolved o2. Is that continual o2 intrusion into the system going to react with the iron regardless of the presence of a HP air sep?
The rate of system o2 permeation is a key factor in assessing corrosion risks. There's not much info out there I could find on this rate in systems using different materials. This very slow o2 intrusion in a tight system may be a real problem or it could be an industry paper tiger used to sell products. The ratio of o2 permeation to the available iron surface area can give a good idea of how long it might take for magnetite to cause problems. If the rate is so low that dead as possible water would take 30+ years to reach a problematic magnetite level or to breach a steel container, I'd say it's a non-issue for new tight low iron systems.
0
Comments
-
ECM pumps are a part of high efficiency design. ECM pumps and magnetite don't play well. Are pump manufactures “bio-barriers” enough or are magnet filters a requirement even though there's not much iron or o2 in the systems?
An oxygen permeation rate of less than 0.1 gram per cubic meter per day is the German standard. If the best separators do nothing at those levels than most of the time they are just couplings like the old iron scoop vents are.
O2 is only one corrosion factor, acids, bases, galvanic and mineral leaching can be factors but o2 is the one I'm focusing on. Heat pumps and low temp boiler systems use buffer tanks. We are seeing more and more of them. They are a bit like large volume hydro-separators. They often see the hottest water. The water velocity in them can be very low allowing time for very small bubbles to rise and vent. Add a proper coalescing screen and manufactures might have some added value to charge for and we would have one or two less system components. Bubble collection port kits could be designed to be added to a buffer tank. The volume at the bottom of the buffer tank makes for a fairly large non magnetic dirt/magnetite catch for a residential sized system with little iron content. A floor sweep magnet used to clean or placed and retrieved.
A simple vented buffer tank system will reach a “dead as can be” state after the residual dissolved o2 in solution eventually reacts with the iron creating a protective magnetite layer, doing little harm. It will do this without a very small bubble remover in the system if design conditions are not extreme.
There are questions in all of this that are hard to answer unless you've done or read real science about it. I couldn't find much to read about. I do feel comfortable using steel radiators and iron pumps with o2 barrier tubing (pex al pex preferred). I don't think a few hours vs a day or two to reach dead as can be o2 levels makes much difference. I don't find small bubbles separators a necessity with a buffer tank in some configurations. If it is proven that HP air separators can reduce dissolved o2 at very low levels partially counteracting the systems continual o2 permeation than I'd change that opinion.
I welcome expertise, theory and science on the topic. Below are some excerpts from various adverts and articles I thought relevant or related. I'm sorry I didn't collect the sources but you can google them too.
As previously mentioned, oxide accumulation can impede further corrosion. If the initial oxygen level within a hydronic system containing iron is low, a relatively thin, protective magnetite layer forms, as shown in figure #4. Magnetite formed in this manner is ideal. It is dense, tightly adhering, conducts heat well and impedes further corrosion. Similar protective oxide layers form on other metal surfaces such as stainless steel,
A rule of thumb is that for every 20F rise in temperature, corrosion rates double. This is why chilled water systems are significantly less prone to corrosion compared to heating systems given equal water quality in both systems.
Germany’s standard is VDI 235. Similar to the others, VDI discourages the use of chemical additives and instead promotes water behavior understanding, sound system design/operation practice and treatments such as deionization that do not involve additives.
Corrosion in systems comes in many forms. The most common form of corrosion is caused by oxygen in the water. Oxygen
in water will cause oxidative corrosion. Other types of corrosion include galvanic corrosion, caustic corrosion and acidic corrosion. To combat each type of corrosion, different methods are used, such as pH control (see pH section), use of
corrosion inhibitors, effective monitoring, and system water control.
The latest recommendation is that some hard water can be used in closed loop systems. The reason for the change is that softened
water has the natural mineral balance disturbed. The disturbed water will try to re-balance itself by leaching the required
minerals from the metals back into the water; this leaching of minerals will cause a higher rate of corrosion.
In Closed loop systems there is a limited amount of dissolved oxygen available and magnetite formation will be negligible. Free magnetite in heating systems can be reduced with the use of magnetic filters. Magnetite will not be detected by a hardness test but will evidence itself in total dissolved solids,
conductivity, or iron specific tests.
Hematite or rust scale is reddish-brown in color and is found wherever unprotected iron is exposed to moisture and oxygen. Rust will form in heating systems when there is too much oxygen present. Oxygen is introduced in heating systems from inadequate air elimination, non-oxygen barrier components, and excessive make up water. Rust formation in a heating system requires immediate action to prevent system damage. Systems with evidence of hematite formations must be thoroughly cleaned and the water in these systems should be monitored closely for the several months to ensure that pockets of rust do not come loose and contaminate the fresh system water. Hematite is nonmagnetic and will not be picked up with magnetic filters.
Never fill systems with water softened with salt bed softeners!
Oxygen Barriers: Manufacturers offer synthetic tubing which incorporates an oxygen diffusion barrier which dramatically reduces the measurable amount of oxygen permeation to the point where it is no longer in question. The German DIN Standard calls for an oxygen permeation rate of less than 0.1 gram per cubic meter per day and is generally accepted as the measure of an oxygen tight radiant heating tube.0 -
My concern with air purgers and buffer tanks is there is no mechanism to quickly catch and expel the bubbles you cannot even see. Cloudy water like when you fill a glass at the kitchen sink. Moments later the water turns clear. Two factors, mainly you have taken the pressure off the water by putting it in an open container. Plus it warms a small amount. In a closed pressurized system you do not have that function working for you.
Microbubbles form on the boiler surfaces when it heats, they need to be captured quickly, easily. Microbubble devices assure that.
This hydrosep 4 corroded away in 18 months installed on a high temperature rubber tube staple up. The 20 year old home is on its 4th boiler. Either a plate HX, and non ferrous components seperation, or yearly chemical dosing is the only way to address systems like thisBob "hot rod" Rohr
trainer for Caleffi NA
Living the hydronic dream2 -
Reading all the various standards gives good insight to the corrosion issues. Dr Watson was on the IAMPO committee with us that led to the ASNSI standard we developed.
I felt the British standard BS 7593: 2019 revision was the most realistic.
https://www.boilerguide.co.uk/british-standards-introduce-new-code-practice#:~:text=A revised British Standard has been introduced concerning,7593:2006 which has been withdrawn with immediate effect.
I think a big part of corrosion protection is starting with a clean system. Both DI and chemical conditioners need a perfectly cleaned system. It takes a detergent to be able to assure the system is clean enough for treatment.
As you noted there are various corrosions possible, as the DIN standard notes.Bob "hot rod" Rohr
trainer for Caleffi NA
Living the hydronic dream1 -
I've been looking at corroded pipes for a good chunk of my life. Why some look like that after short years and others are 60 years old and look great is not what I'm after. There are reasons off topic for why they look like that. I'm not confused about how micro-bubble air seps. work. I got it in the 90's. I did describe their function and championed their use. I'm not questioning the superiority of coalescing media separators. That is clear.
My understanding is micro-bubbles form in hot boilers when there is gas in solution. In an o2 tight system the o2 part of the gas in solution reacts until it reaches a low limit stasis with new o2 leaking in and reacting with available materials.
This low level condition is reached with or without micro bubble removal in time. It did for decades before micro bubble removers existed and many of those systems are still distributing heat well.
The need for such expedience and efficiency in removing all micro bubbles from a system when it otherwise works well is questionable. 2 hours vs 2 days
Do micro bubbles form in "dead" water at normal operation temperatures?
Do Micro-bubbles form on ALL heat exchangers no matter the temperatures or gas saturation?
Does milky water persist long in a vented buffer tank system?
Does milky water lose its corrosive properties in short order?
Do MBAS's remove o2 in a low temperature system at the levels an o2 tight system has leaking in?
I appreciate the time and effort of all your responses. The British in-line filter requirement is what? magnetite filter or all particle filter? The water standards are good to have. The questions I had are unaddressed. I'm not expecting conclusive answers to them. Most people don't care about the details I'm interested in.0 -
Hydronic systems are like snowflakes, no 2 are alike.ihp.i
I think you would need to put some specific test equipment on a system, monitor it for a period of time to know exactly what goes on.
I have worked on rubber hose systems from almost day one. Some sludge within months, others ran years without serious sludge or corrosion. Same with the early RadiantRoll systems.
If there were answers to Those questions, I think the industry would know. It is still largely theory, as far as I know.Bob "hot rod" Rohr
trainer for Caleffi NA
Living the hydronic dream0 -
" It is still largely theory, as far as I know." That's what I thought. Rubber hose systems? Onyx? No I'm not taking about anything like that. You have probably had to deal with so many problem systems it's hard to considered what's going on in the best case one's. It's best design I want to know about. Modcon or heat pump with a buffer tank, pex al pex to LWT steel radiators with iron pumps is a standard snowflake. It's interesting that those questions are open. Maybe they have been studied and it's proprietary non commercial info. I suspect there are engineers or physicists who could answer most of those questions with decent authority with no tests. Dissolved o2 can be tested for cheaply. A light in a tank with a camera doesn't seem that hard. The answers to those questions and others would clarify real needs and magnetite risks in modern system conditions.0
-
The test for oxygen permeability through the tube is not so simply. I cleaned out a warehouse in Missouri that had a machine for testing o2, it certainly wasn’t a simple machine. It looked like something from Frankenstein lab
I think the key if finding how and where the O2 gets in. Not measuring the amount that has made its way in.
From a reputable source I heard 70% of returned ECM are plugged with magnetite. I’m not sure they get tracked back to the actual system they were installed in
A magnet in a separator device seems like cheap insurance. Since there is no definitive answers to o2 ingress questions that I k ow of.Bob "hot rod" Rohr
trainer for Caleffi NA
Living the hydronic dream0 -
Again with problem systems. Yes, yes, cheap insurance. I'm taking about o2 tight systems with no magnetite build up. The rate of intrusion is very slow. It barley gets into good systems. We know how it would get in. Not a mystery. The rate is the key to assessing long term risk of magnetite production in tight systems.
There are sample and reactant mix color chart o2 tests. Real time testing is lab equipment but not that crazy. It can be rented fairly reasonably if you have a testing /corporate/industrial need.
I was thinking, if you could identify a substance that is much more o2 reactant than iron, it could be placed in flow for a period of time and it's rate of oxidization could be measured. Anyway, testing is beyond what I want to do as a contractor. The industry has little incentive to answer those questions. Next standard snowflake system I start up I'll clean, de ionize and install a magnet and see what's on the hook in years to come. I've installed them on systems before that are pump iron only and have not found much to clean off. They and MBAS's have their place, no doubt.0 -
Richard in Colorado was documenting water samples from customers homes. Most every sample here has sludge/ magnetite. Cast iron section boilers become magnetite seperators also :)a
A pic of a large job where it took months of blowing down the DirtMag to eventually pull out all the magnetite.
Even air seps at some point capture the magnetite sludge.
This large Wilo circ is on our building in Milwaukee, built 2002. 100% copper piping, stainless boilers 30,000 feet of Kitec Warmrite tube, no leaks, no fill water added. I took this apart as the Wilo was spitting rotation error codes.Bob "hot rod" Rohr
trainer for Caleffi NA
Living the hydronic dream0 -
That Millwaukee Wilo case sounds like what I'd expect, 21 years. In pump designed protection and a dirtmag might be a 40 year set up. Of course pulling and cleaning the pump every 15 years is an option but it's still wearing the bearings. Funny, pumps are fouled by their own corrosion by-product. Won't some magnetite still get to the rotor as a dirtmag is not 100% single pass efficient and the particles are formed and enter the system at the pump? Once that rotor has it in it's field that's it. I know catching what you can is better than not catching any at all. It's mitigation not a solution.0
-
Actually the first one failed after 5 years. It was replaced without disassembling, the factory called it a software warranty. Two years later the second one seized. I happened to be up there so I took it apart to see thisBob "hot rod" Rohr
trainer for Caleffi NA
Living the hydronic dream0 -
One of the benefits of micro bubble air separators I didn't mention above is substantial.
Because I've been using them for most of my working life, remembering what system start up was like without them took some time and effort. Fresh fill water has a significant amount of saturated air held in it say 14% and as you start to heat it even to just 100F it rapidly comes out of solution until it's around 2-3%. 11+% of system volume must be vented. The expedience and efficiency we want from an air separator isn't a corrosion concern. It's because we want to go home and not be called back because of an air lock. The time of the greatest system gas intrusion rate is the cold off period. The longer it's off, the more gas gets back into the cold system and the next heat cycle that volume of gas rapidly comes out again as it heats up. Some well piped old school systems can handle that rapid de-solution of air well and others don't. I've never had problems with vented buffer tanks with no MBAS's because the buffer is very good at handling lots of air without letting much get in to the distribution loops. Any magnetite production reduction is a benefit but is not the primary reason for use.0 -
5 years. That's a problem. Did the mag filter fix it? The only iron was the pump? No fill water connected at all or just valved off? Is it possible the system has a negative pressure point that sucks in air? A massive expansion tank leaking into the system? What's the theory of what happened? Kitec related? That's not typical is it? I've been servicing more than a few, pumps are only iron, systems for many years now. The water looks good. Distribution pumps are Alpha's. They do have silver king in them.hot_rod said:Actually the first one failed after 5 years. It was replaced without disassembling, the factory called it a software warranty. Two years later the second one seized. I happened to be up there so I took it apart to see this
0 -
Found some more numbers from Spirovents patent.
The second marked block of text reiterates the important conclusion that the
Spirovent reduces the content of dissolved air to 0.4%. As 20% of air consists of
oxygen, it was concluded that a corresponding 0.08% concentration of oxygen is
too low to cause any corrosion damage.
The third and last marked text block describes the release and elimination of
microbubbles and the extraordinary air removal efficiency rate of 100% of the
free air, 100% of the entrained air and 99.6% of the dissolved air.0
Categories
- All Categories
- 87K THE MAIN WALL
- 3.2K A-C, Heat Pumps & Refrigeration
- 58 Biomass
- 426 Carbon Monoxide Awareness
- 113 Chimneys & Flues
- 2.1K Domestic Hot Water
- 5.7K Gas Heating
- 109 Geothermal
- 161 Indoor-Air Quality
- 3.6K Oil Heating
- 70 Pipe Deterioration
- 994 Plumbing
- 6.3K Radiant Heating
- 391 Solar
- 15.4K Strictly Steam
- 3.4K Thermostats and Controls
- 55 Water Quality
- 44 Industry Classes
- 48 Job Opportunities
- 18 Recall Announcements