Welcome! Here are the website rules, as well as some tips for using this forum.
Need to contact us? Visit https://heatinghelp.com/contact-us/.
Click here to Find a Contractor in your area.
Mod/cons in non-condensing operation and their PVC flue temperatures
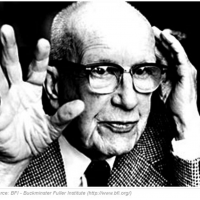
Teemok
Member, Email Confirmation Posts: 760
This topic was touched on in another discussion on the wall and I think it's an important thing to try to understand better. My smarter customers have asked questions about it. Saying it's complex is not a satisfying or confidence inspiring answer. I think I understand why we don't see melted PVC all the time with high temp mod/con use but it's always good to talk it out and hopefully I can learn something and maybe trash a fallacy. I love trashing fallacies.
A healthy properly installed mod/con will have flue gas temperatures that closely track the return water temperature RWT. Most mod/cons are limited to 190F or so SWT. If the RWT approaches supply you can bet the boiler has turned down close to it's minimum firing rate. There's either a steady state low burn achieved or we enter an on/off differential cycle. The cycle has cooling time so it's not really the biggest flue danger. I think a steady state burn for a long time would be the concern. This generally happens with cooler ambient temperatures and that means higher deltas between unconditioned air, structure materials and the flue pipe. Better flue pipe cooling.
The steady state might look like this: 189F SWT, 184F RWT and a near 15K BTU burn rate. I'm thinking the flue gases T's are just above RWT. Gases may not be condensing in the HX but some likely are in the flue. All that plastic is an extended heat exchanger. Heat is released by the vapor in the exhaust to the gases. The condensed vapor becomes condensate in contact with the inner pipe wall. It is an exothermic event. The heat of condensation is 2442J/g or 1095 BTU for every pint of condensate produced. I'm guessing the gases temperature goes up while the pipe has the cooler condensate in contact. The pipe loses heat via radiant, conduction and convection to it's surroundings. The condensed water temp is defiantly below the exhaust temperature. 135F is the typical dew point. There's some small cooling effect from the condensed water running back to the boiler through the hottest part of the flue.
There must be a temp dif. between the inner surface of the pipe material and the outer surface. I wonder if the velocity of the flue gas limits how much heat can be transferred to the pipe material. It doesn't have time to get absorbed by the pipe faster than the pipe is getting rid of it to the surroundings? All this is happening at in a continuous dynamic heat exchange, into and out of the PVC material. The outer material might be closer to the 140F safe spec. of PVC than we would guess. After all, we are 98.6F inside but only 85F or so on the outside. Also PVC might be able to handle higher temperatures more reliably than is being stated.
I can see there would be problems with fouled up HX's that have flue gases much hotter than RWT while firing on high and not hitting target outlet temp. That is why we have limit switches/sensors/ecos. I've seen a few cooked, should not be used again, first feet + of flue but never a catastrophic failure.
From the charts I found it looks like our high temp. low fire steady state boiler efficiency is near 84-85%. 16% waste heat going up the flue. The firing rate was 15K BTU, 16% of that is 2,400 BTU or 700 watts. A lot of it is ejected to the exterior, some drains back to the boiler and the rest is given off via the three transfer means to surroundings and the plastic is fine. Proof as they say is in the pudding. There are plenty of high temp mod/cons with no flue problems in service in the previous 20 years. I don't claim to know that the above is all solid science. I'm not an engineer. I might be wrong about some of it. If you can explain it better or correctly I'd like to understand.
A healthy properly installed mod/con will have flue gas temperatures that closely track the return water temperature RWT. Most mod/cons are limited to 190F or so SWT. If the RWT approaches supply you can bet the boiler has turned down close to it's minimum firing rate. There's either a steady state low burn achieved or we enter an on/off differential cycle. The cycle has cooling time so it's not really the biggest flue danger. I think a steady state burn for a long time would be the concern. This generally happens with cooler ambient temperatures and that means higher deltas between unconditioned air, structure materials and the flue pipe. Better flue pipe cooling.
The steady state might look like this: 189F SWT, 184F RWT and a near 15K BTU burn rate. I'm thinking the flue gases T's are just above RWT. Gases may not be condensing in the HX but some likely are in the flue. All that plastic is an extended heat exchanger. Heat is released by the vapor in the exhaust to the gases. The condensed vapor becomes condensate in contact with the inner pipe wall. It is an exothermic event. The heat of condensation is 2442J/g or 1095 BTU for every pint of condensate produced. I'm guessing the gases temperature goes up while the pipe has the cooler condensate in contact. The pipe loses heat via radiant, conduction and convection to it's surroundings. The condensed water temp is defiantly below the exhaust temperature. 135F is the typical dew point. There's some small cooling effect from the condensed water running back to the boiler through the hottest part of the flue.
There must be a temp dif. between the inner surface of the pipe material and the outer surface. I wonder if the velocity of the flue gas limits how much heat can be transferred to the pipe material. It doesn't have time to get absorbed by the pipe faster than the pipe is getting rid of it to the surroundings? All this is happening at in a continuous dynamic heat exchange, into and out of the PVC material. The outer material might be closer to the 140F safe spec. of PVC than we would guess. After all, we are 98.6F inside but only 85F or so on the outside. Also PVC might be able to handle higher temperatures more reliably than is being stated.
I can see there would be problems with fouled up HX's that have flue gases much hotter than RWT while firing on high and not hitting target outlet temp. That is why we have limit switches/sensors/ecos. I've seen a few cooked, should not be used again, first feet + of flue but never a catastrophic failure.
From the charts I found it looks like our high temp. low fire steady state boiler efficiency is near 84-85%. 16% waste heat going up the flue. The firing rate was 15K BTU, 16% of that is 2,400 BTU or 700 watts. A lot of it is ejected to the exterior, some drains back to the boiler and the rest is given off via the three transfer means to surroundings and the plastic is fine. Proof as they say is in the pudding. There are plenty of high temp mod/cons with no flue problems in service in the previous 20 years. I don't claim to know that the above is all solid science. I'm not an engineer. I might be wrong about some of it. If you can explain it better or correctly I'd like to understand.
0
Comments
-
A combustion analyzer give you a good idea of the temperature in the beginning of the flue piping. A temperature head on a multimeter would show temperature at the termination. I think DHW mode would show the highest flue temperatures.
Viessmann always cover flue gas expected temperatures in their trainings.
The issue with PVC is it is not officially rated for flue gas application, regardless of the temperature rating. Same for CPVC. Except maybe the Ipex product?
A time was when HTP sent a short piece of black ABS as the starter piece. Then you had to find an acceptable transition coupling. Fernco were commonly used. I suspect they are not rated for flue gas either.
Under the hood of some mod cons were Fernco looking connectors. Even reducing versions.Bob "hot rod" Rohr
trainer for Caleffi NA
Living the hydronic dream2 -
I've seen some brittle ferncos and no hubs. One company had a section of gray schedule 80 that had to be used as first section. The PVC issue comes down to the boiler manufactures. They are holding the liability I guess. The inspector defers to the manual and it states PVC is a flue material for their product. Not sure who's stamp makes it official but PVC is has been used for decades. PVC manufactures are just all CYA saying they don't make it for that and 140F is their integrity temp. You know some engineers and lawyers have done more than just talked about this. I'd like to understand the physics and logic that convinces most manufactures that they are safe to recommend PVC. I know it's a sales point they want. I'm thinking someone has done some math and studies. They aren't all just winging till something bad happens to sell more boilers that can use cheap and easy flues. There was a time when PVC was being blamed for the mysterious "coffee grounds". Chlorine off gas or in the condensate drain back was corroding the stainless till is was seen with other flue materials.0
-
My uft-100 came with a 6" or so piece of cpvc that has to be used as the first section out of the boiler. Were my connections with universal cement and a pvc fitting acceptable? Not sure.
The 18 year old pvc from the powered vent water heater it replaced did not look great on the inside.0 -
Oh yes it was the HTP UFT with the gray pipe cpvc. Is that a you glued it with the wrong cement excuse they could use to not be liable? I just haven't heard the horror stories of regular failures. I know some bad techs that removed the flue temp limit from Munchkins and had bad results.
Your PVC was dirty, deformed, integrity loss? You used it again so I couldn't have been that bad.
From Weld-on: "Yes. CPVC solvent cement technically will work on PVC piping. However, we recommend that the correct Weld-On primer and PVC solvent cement for the particular application should be used. Please note that PVC solvent cement, because of temperature limitations, is not recommended for CPVC piping."
The cooked fittings I've seen had solid glue joints. Maybe there's not much load on them so they didn't fail. I was more worried about pipe or fitting cracks, warping, bulging, collapsing.0 -
I have seen a few other manufacturers that used to approve PVC also now specify a starting equivalent ft length of CPVC or polypropylene. I have seen a few yellowed PVC vents out and about, I think generally the equipment where you see this happen is not running within spec. I can understand why code would switch away from PVC, but I also kind of understand the opinion that PVC would be OK when the unit is running within spec and installed correctly. My boiler is vented in UL listed CPVC for what it's worth (IPEX) I tend to prefer polypro from Duravent though0
-
-
I used System 1738 PVC certified PVC produced by Ayers couple with HTP UFT boiler and the 6” of CPVC provided.0
-
What no one realized and what the MFGs don't want to accept is that any equipment manufactured some time in it's life will be run dirty or out of spec so testing flue gas temps in a lab is a myth.
Stuff has to be built for worse case scenario's (maybe not for everything) but certainly for flue gas which can kill people.4 -
Mad Dog_2 said:
Is anyone still using PVC for mod con vents? Mad Dog 🐕
Here? Yes, I'd say the majority of contractors around here use PVC. I'm doing controls for a high end hill top, tens of millions, project and mechanical contractor has PVC buried in convoluted enclosed routes. I've used polypro duravent before. I've also seen it leak condensate from joints after some years and become disconnected from hard start puffs combine with uncaring installers or crappy joint locks or both. When installing for any high temp. application I think a safety first 10' ft of poly is smart. If it's 100% low temp closed loop I see no issue with PVC given proper installation practice and maintenance. Combustion appliances need checking on. Cooked pipe is a sign that something is wrong and it's easy to identify. There's a fair bit of fear mongering. What's the real scale of problem. Are the other materials really that much more idiot proof? Consider carbon fiber makers never "approved" a single mountain bike. 10 years without a skilled caring person looking at things is reckless. Safety with CO isn't a bad thing and rarely people die and court cases happen. Same with type II materials and others. Rusted out pool heater flues kill. I guess the science of it is so close to limits that only the mod/con lawyers get to hear about it from the PHD's they pay. This debate is so old now. We've been waiting for it to be settled for more than a decade. Same ol same ol. "you must be crazy to do that" "it's fine"1 -
I don't know that you will get the answer to your question here. It has been discussed many times on this site with no clear answers.
The inspector goes by the manufacturers installation manual.
I'm hearing some AHJs have prohibited non listed venting materials now. I think Canada requires the material meet the S636 standard.
That being said some of the engineered "approved" plastic/polymer products have failed also. PlexVent and UltraVent for example. Even some of the newest PP from Europe has had pipe and gasket issues.
It's rare to see a boiler in Europe run over 48C, about 120. Early Euro imports limited out at 167F, 75C. So they don't experience continious high flue temperatures like we do here.
Bob "hot rod" Rohr
trainer for Caleffi NA
Living the hydronic dream2 -
-
Where 1 in 8 Americans live. California. In the north, there's a difference.
0
Categories
- All Categories
- 86.9K THE MAIN WALL
- 3.2K A-C, Heat Pumps & Refrigeration
- 57 Biomass
- 425 Carbon Monoxide Awareness
- 110 Chimneys & Flues
- 2.1K Domestic Hot Water
- 5.7K Gas Heating
- 105 Geothermal
- 160 Indoor-Air Quality
- 3.6K Oil Heating
- 70 Pipe Deterioration
- 981 Plumbing
- 6.3K Radiant Heating
- 387 Solar
- 15.4K Strictly Steam
- 3.4K Thermostats and Controls
- 54 Water Quality
- 44 Industry Classes
- 47 Job Opportunities
- 18 Recall Announcements