Check valve preferences for DHW and heating zones
I'm looking for recommendations for type, make, and model of check valves for my hydronic system.
I have a Buderus GB142-60 system, with a priority domestic hot water (DHW) zone to an indirect water heater and a heating zone consisting of a hydronic coil and air handler. The system was installed in fall of 2011.
The plumbing is similar to the attached diagram, from the GB142 applications manual, except for the air handler in place of the baseboard heating in the diagram.
At the time, I noticed that check valves were not installed in either loop. This causes the air handler loop to flow backwards when the DHW loop is active. This, in turn, mixes lower temperature water from the air handler loop with the 190 degree boiler water, such that I'm only getting 165 to 170 degrees into the indirect water heater.
I completely forgot about the missing check valves until recently when I installed a new water softener. I ran the system out of hot water so that I could get the newly softened water into the indirect tank. I was thinking about the system's ability to keep up with hot water demands. I did some measurements and found that I wasn't getting the heat I expected into the indirect water heater. I tracked it to the lack of the check valves again, as I had in 2011.
The system has been working fine the past 11+ years. I don't think we've ever noticed cold showers. Maybe I've had to turn up the heat during a long shower here and there.
I haven't tested for it yet, but unless there is a check valve built into the air handler pump, the same thing is happening when the air handler loop is active, with the DHW loop being mixed into it. It probably isn't varying the temperature to the heating coil as much as the drop of what is going to the water heater when its loop is active. However, I am guessing there could be a little waste possibly happening when the air conditioner is running in the summer, at the same time the DHW loop is active. It would be pulling some hot return water through the air handler, causing a fight between the heating coil and the AC coil.
I figured I might as well install the check valves this summer when I'm working on the system. My question is: What would people recommend for type, make, and model, and why? By type, I mean normal check valve, flow control valves, or actuated valves. I'd like something that isn't going to get stuck, won't reduce flow much, and something that won't allow much leakage when the alternate loop is operating.
Thanks for any recommendations.
David
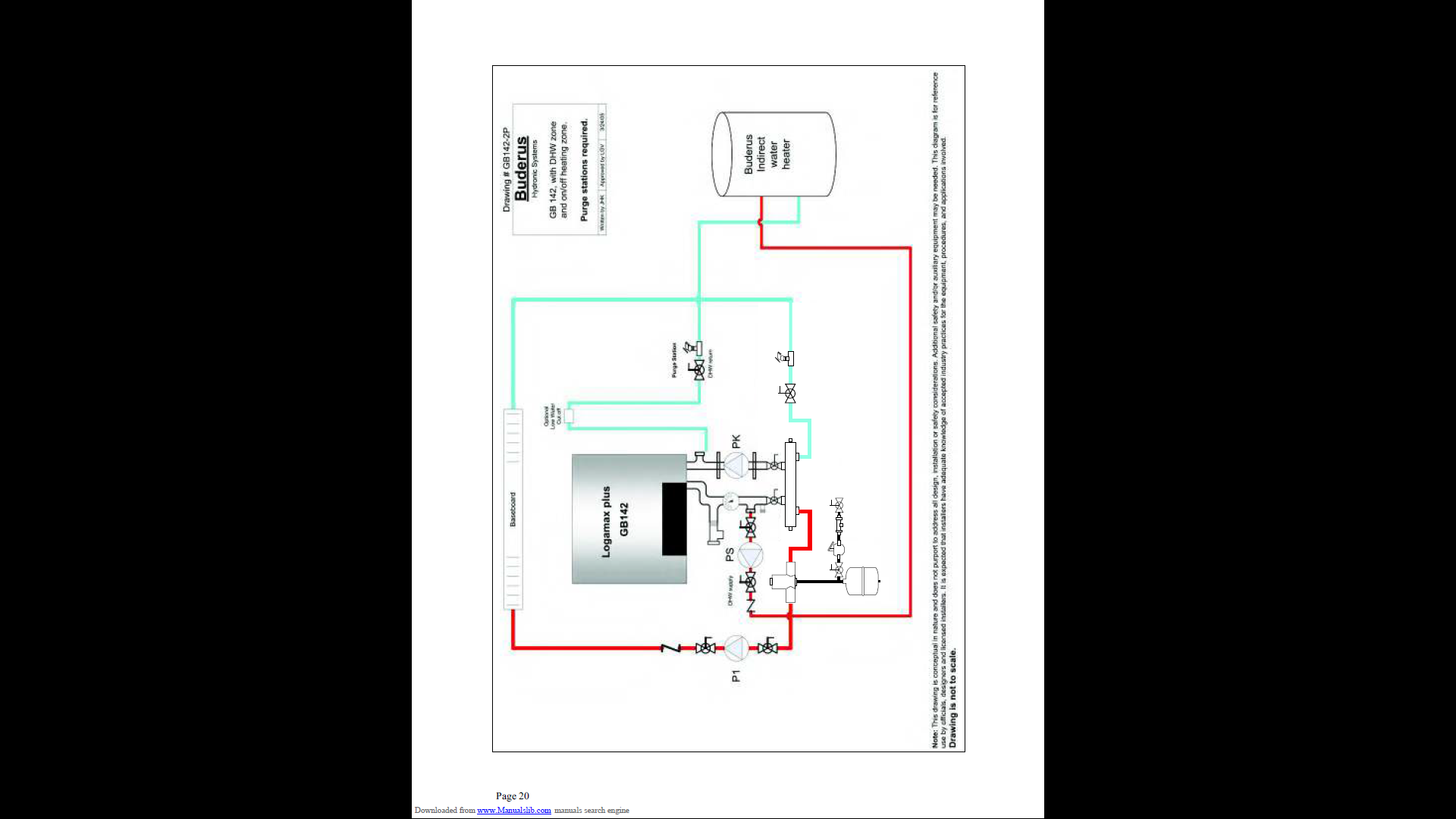
Comments
-
For hydronics you want a spring check, conical shape, soft seat. The Caleffi version is serviceable and available with multiple connections. Other brass versions are available from valve manufacturers.
Inside are the common Neoperl checks like you see in circulators, replaceable if needed.
If you use a check on domestic water it needs to be low lead, or stainless steel
https://www.caleffi.com/sites/default/files/file/01363-22_na.pdfBob "hot rod" Rohr
trainer for Caleffi NA
Living the hydronic dream-1 -
If you want a dead on reliable check with probably 60 years of proven design (assuming they haven't screwed them up) the Bell and Gossett SA flo checks are probably the most reliable out there.To learn more about this professional, click here to visit their ad in Find A Contractor.0
-
Keep an eye on the pressure drop in those weighted checks. A 3/4” spring check is about a 17 Cv, looks like about a 2 Cv on this 3/4 type.
So a big drop up around 6 gpm or more.Bob "hot rod" Rohr
trainer for Caleffi NA
Living the hydronic dream1 -
From your chart, Looks like a pressure drop around 3 ft of head for the maximum flow rate of around 3.5 gpm in 3/4 inch pipe. Shouldn't be running anywhere near 6 gpm on 3/4 inch pipe... that's 9 ft of head per hundred feet of black pipe (11.5 ft hd for copper) equivalent length and way beyond good design standards for quiet operation and piping wear.hot_rod said:Keep an eye on the pressure drop in those weighted checks. A 3/4” spring check is about a 17 Cv, looks like about a 2 Cv on this 3/4 type.
So a big drop up around 6 gpm or more.To learn more about this professional, click here to visit their ad in Find A Contractor.0 -
6 gpm in 3/4 M is under 4 fps, well within its hydronic flow range, so about 7’ head as I see itBob "hot rod" Rohr
trainer for Caleffi NA
Living the hydronic dream0 -
I'm going off the B& G system Syzer, which puts 6 gpm well out of its normal design range. I wonder what's changed since that was developed... maybe just higher head pumps, I suppose. 3/4 inch supply to feed a complete decently insulated 4,000 sq ft home at 42 degree north does seem pretty small to me( especially using U.S. standard 20F delta tee at design) I think the head would probably really be up there even with radiators as emitters.hot_rod said:6 gpm in 3/4 M is under 4 fps, well within its hydronic flow range, so about 7’ head as I see it
To learn more about this professional, click here to visit their ad in Find A Contractor.0 -
It would depend on what the 3/4 feeds, lengths, fittings, etc.
3/4 to a fan coil in an air handler, or a run to a remote radiant manifold, 60- 70 feet of fin tube.
This graph shows 100' of M copper.
So 6 gpm would fit nicely, mid
curve on a 15-58.
Here is another flo control option. The knob allows you to force open the check inside. Same Neoperl type spring check.
.Bob "hot rod" Rohr
trainer for Caleffi NA
Living the hydronic dream0 -
@hot_rod and @The Steam Whisperer (Formerly Boilerpro) ,
I really appreciate you taking the time to respond to my question. Not being in the trade, I guess I never thought about pipe erosion. I just thought it was a matter of having a pump curve that will overcome the friction and still give the desired GPM.
My copper is 1", type M, for the indirect water heater loop and the air handler loop.
Given your discussion about pushing too much through the copper pipe, I looked at the source of where hot_rod provided that table in his reply. It states,
"Water velocity in copper tubes should not exceed 8 ft/s (2.4 m/s) for cold water and 5 ft/s (1.5 m/s) for hot water (up to approximately 140oF, 60oC). If water temperatures routinely exceeds 140oF - don't exceed 2-3 ft/s (0.6-0.9 m/s)."
My water is *supposed* to be about 190 degrees into the indirect water heater. I'm losing a chunk of that due to the alternate loop mixing its water, as I mentioned before (hence the need for the check valves). Even now, I'm at 165-170 degrees into the indirect. If the above quote is accurate, that means I shouldn't be exceeding 2-3 ft/s. I believe I am, however.
This is where I have to ask a really stupid question. My indirect, which is a SuperStor Ultra 60 (SSU-60), calls for 10 GPM to maximize its heat delivery.
So my question is, why do they plumb this with 1" supply and return connections and design it for 10 GPM, if that is too fast for 1" copper pipe, at the supply temperature it wants (180-200 degrees)?
Going back to the flow rate table for copper pipe:
10 GPM would put me at 3.7 ft/s, which is above the 2-3 ft/s that I'm not supposed to exceed.
Maybe you can help me with this multiple choice.
With me being at 3.7 ft/s, I am:
A ) Not at risk. My DHW loop is only in use a couple times a day, and the above source is assuming continuous use. (that wouldn't explain how commercial tanks from SuperStor also come with 1" connections and want even more water pushed through, and are probably meant to be used very often)
B ) I am at risk. Even though they put 1" connections on the tank, they expected the loops to be made out of larger diameter pipe. And their heat exchanger wasn't a concern for them, because it is cupronickel, not copper, and that somehow doesn't erode as easily?
C ) I am/am not at risk for some other reason, and I'm missing some other aspects of this.
Going back to the check valves... @hot_rod, in the literature you provided for the Caleffi valves, it has the following:
I'm currently below 150 degrees for my air handler loop, but I could see me being at 190 degrees for more than an hour on the DHW loop, with back to back to back to back showers happening in the house. Is there another model that has a higher temperature rating?
I looked into my DHW pump a little bit more and it *might* allow me to add an integrated flow check. It is a Taco 008-VDTF6. I've found conflicting information online about whether it supports adding an internal check valve. Some sources say it is an option (as opposed to the -IFC model that ships with the check valve installed). Other places don't list the check valves as being compatible with my pump model. If I could put one right in the pump, that would be easiest. However, I'd still need one on the air handler loop, as that is the one causing me the big temperature drop when the water finally gets to the indirect water heater.
Thanks again for your help. It is greatly appreciated!
David0 -
2-4 fps is accepted velocity in hydronic piping, so no problem there. Some engineers are comfortable with 5 fps on intermittent loads
Without a flow meter you don’t know exactly what flow you have.Typically an indirect call is not more than an hour
I agree with extended runs at 190 a steel or brass check would be better on the indirect. Conbraco and Watts have all brass hydronic spring checks
Oddly enough the checks in circulators are those same rating, Neoprrl 150 continuously. that combined with having the right at the turbulent flow at the circ discharge, not ideal. I’d move the check 6” or more from the circ discharge.
in some cases you need checks on S&R as a hot tank and cold boiler will try to equalize
occasionally we see indirects with both a checked circ and a zone valve for 100% shutoff for thermal siphoningBob "hot rod" Rohr
trainer for Caleffi NA
Living the hydronic dream0 -
Ah, this is the type of thing where I don't have a good feel for what is a hard and fast rule vs something with some fudge factors built in. Thanks for clarifying that. I was a little worried after reading that other page, especially since the installer used the thinner copper pipe.hot_rod said:
@hot_rod said:
2-4 fps is accepted velocity in hydronic piping, so no problem there. Some engineers are comfortable with 5 fps on intermittent loads
Without a flow meter you don’t know exactly what flow you have.
Yeah, I don't know the true flow. When factoring in losses for the indirect and piping to/from it, but without factoring in losses from the boiler, the pump's curve shows that my 15 GPM pump is probably down around 10 GPM. So I'm probably a little below 10 GPM, and a little lower than the 3.7 ft/s from the table.
Thank you for the pointer on other brands of inline check valves. It would be fairly infrequent for us to draw hot water for more than an hour, but since it is possible, I didn't want to risk cooking the plastic check valve.
I wondered about the plastic in the integrated checks in the pumps too. I thought maybe they were made out of a different type of plastic? The Taco IFC pumps are still rated for 230 degrees, just like the non-IFC models, so either the checks are different in some way, or Taco is being less conservative on the temperature ratings (or Caleffi is being more conservative). When researching the IFC pumps, I found the following in the Taco literature:
"By locating the patented IFC inside the pump casing, a separate in-line flow check is eliminated,
reducing installation costs. The reduced pressure drop of the IFC, increases the 007 flow performance
up to 240% over in-line check valves."
Now I don't know if that is reality or marketing comparing a spring check valve to a weighted check valve? If it is reality, then the reduction in pressure drop might be worth seeing if the integrated plastic check valve holds up, since it is relatively easy to replace/remove if needed.
If I put in a brass spring check valve, how would you plump it so that they are easily accessible if they stick or need to be replaced? Would you put shut off valves on each side of the check valve? Would those add significantly to the pressure drop?
Good point. I'll measure the return temperature, over time, when both zones are inactive, to see if the heat from the water tank is bleeding over into the other loop.hot_rod said:
@hot_rod said:
in some cases you need checks on S&R as a hot tank and cold boiler will try to equalize
occasionally we see indirects with both a checked circ and a zone valve for 100% shutoff for thermal siphoning
It has been a while since I've looked into using zone valves. What happens to a pump if a zone valve fails in the closed position? Does it make the pump fail? Are there ways to have an alarm go off or an auto-shut off of the pump if this happens?
Thanks again for all the great information!
David0 -
Good questions about check valves, ratings etc. I'm not sure how this % is derived?
"By locating the patented IFC inside the pump casing, a separate in-line flow check is eliminated,
reducing installation costs. The reduced pressure drop of the IFC, increases the 007 flow performance
up to 240% over in-line check valves." Maybe Taco has the math? or they have a spec on the checks they use?
This goes to my point about the pressure drop difference between weighted flo checks and spring checks, maybe.
Neoperl does make HT high temperature versions, black in color, these are used in some of the Caleffi products. Hopefully the black ones show up in all the checks we offer.
From my understanding they are not a standard item in the size to fit in pump volutes, so you see the white ones. Usually when you see black plastic it is a higher temperature material, but check with the manufacturers.
Ideally the check is downstream from any pump discharge to avoid chattering. That is a trade off the pump manufacturers are willing to take.
I suspect chattering and excessive temperature leads to early, plastic check failures. One contractor tells me 5 years is about the plastic pump check life cycle from his experience. Again actual conditions play a part in the abuse.
A critical part of check valves is the sizing. Size them by Cv not pipe size. often a check is a pipe size smaller, looks funny, but it is the flow rate not the pipe size.
Take a common 1" spring check, 14 Cv maybe. If you only flow 8- 10 gpm the check may not be fully open, that is what can cause the chatter or excessive wear on a check.
Never use a swing check on a circ pump, swings need a delta P to close off properly.
Swing checks can be used for overheating applications as the check can open from the buoyancy of very hot water. You see swing checks on wood boiler over heat loops, for example.
Yes if you want the ability to service the check you would need isolation valves. But a properly appliec check, in a clean fluid hydronic system should be fairly maintenance free. It's teflon tape shards, etc from the first install that trips them up
Bob "hot rod" Rohr
trainer for Caleffi NA
Living the hydronic dream0 -
It is unfortunate they don't use the high temperature plastic check valves in the residential solutions.
That makes sense about the chatter. I never thought about how they might not open all the way. In my case, I guess that would be a risk. I'm using a 15 GPM pump, but it is being reduced to 10 GPM or less from pressure drops. So on the one hand, I'm not losing flow due to adding isolation valves, but if I use the white plastic IFC in the pump, then I may increase how often I need to service the check valve. In the pump, it is easy to service, but may need more frequent servicing. In a dedicated check valve, downstream from the pump, if I use a brass check, then less chance of needing to service it, but lose flow from the isolation valves. And if I don't install the isolation valves and the brass check does fail, then I'd have to drain the whole system.
I may try out the plastic check and see if it fails. If so, then I either consign myself to periodically replacing it, or I go with the alternate approach downstream.
The above only solves for the DHW zone, and preventing it from being sucked back into the air handler heating zone. I would still need to solve for the opposite (which is my main problem to fix), of the air handler zone water being sucked into the DHW zone. For the air handler zone, I don't have a pump that accepts an integrated check valve. I have a very old pump that is inside the air handler. It was left in service during the install of this new system (new boiler, new indirect, kept same air handler, same heating coil, same AC coil, same air handler control board). It is an older Taco pump.
It was discussed with the installer that the old Taco air handler pump should probably be cut out and moved to outside of the air handler, along with shut off valves, so that it could be replaced/serviced if/when needed. I could take this opportunity, when the system is down this summer, to do just that. Although I hate to decommission a working pump, it may be more prudent to replace it before it fails, and I can take advantage of lower power consumption pumps that are available now.
I am not as concerned about losing flow going through the air handler, because it can be a slower moving zone, with lower temperatures, vs the faster moving, high temperatures, to maximize the DHW zone.
I really appreciate you bringing up all these different variables. It is things that you, as a knowledgeable professional probably take for granted, but a lay person, like me, may not always be aware of.
Any thoughts on the actuated valves? What happens to a pump if a zone valve fails in the closed position? Does it make the pump fail? Are there ways to have an alarm go off or an auto-shut off of the pump if this happens?
Unless I end up with some thermal siphoning, I won't need them for these two zones. However, I have had a plan for a while to add another zone for in floor heat. Do you design for zone valve failure by having some sort of bypass loop, so the pump can always push water, even if a zone that should be open is closed? Or is there some other way to handle this situation?
If that's better asked as a separate post, I can do that too.
Thanks again!
David
0 -
I installed some temperature sensors on the supply and return lines to the indirect water heater. (sensors not insulated yet, so might be affected a bit by ambient conditions)
190 degree water at the boiler becomes 163 degrees or so into the water heater, due to sucking in water from the air handler zone. The longer it does that, the more that other zone heats up, and the temp creeps up a little into the water heater. But the max the other zone can get to is the return temp of the DHW zone (which is about 135-140 degrees).
Posting it here so others can see the effect of not having a check valve in a secondary zone, when the priority zone is running.
David0 -
@hot_rod,
I found and watched this tonight. Good stuff! Thanks for sharing your knowledge.https://youtu.be/23CQiEt5QWc
David0 -
Following up on this thread, for @hot_rod, or anyone else reading it.
As mentioned in another thread, my DWH loop pump died (or so I thought), and I just got it working again last night. I had thought that the 190 degree boiler water turning into 160+ water for the DHW loop was because it was sucking in water from the air handler coil loop, because there is no check valve in that loop. Likewise, no check valve in the DHW loop, so it is probably getting sucked into the air handler loop too. That's why I posted this thread, so I could come up with the best check valve solution to solve this issue.
However, I took a closer look at things today, after replacing the pump last night. Here is a photo I posted in the other thread, showing how things are piped:
What I am calling Primary Supply and Primary Return may not be technically correct. It is a priority loop that effectively becomes the only loop active (or it is supposed to), since the boiler primary pump it shut off during the DHW cycle. The DHW pump takes over and circulates water from and to the boiler. The low loss header doesn't serve a purpose in this mode, since it is trying to get as much heat as possible to the indirect water tank.
And that's where the problem was. It wasn't getting the 190+ degree water to the water tank. It was only getting 160-170 degree water to the tank. I shut off the secondary return valve (green in lower right) today. I have to leave the one on the lower left open (or at least leave one of them open), because my expansion tank hangs off that secondary loop in that direction. This should have stopped that loop from being sucked into my DHW loop. And yet, I was still getting water, from somewhere, tempering my water in that priority loop. I measured the temperature on the black pipe right above where the priority loop splits, and it was within a degree or two of what the boiler reported for temperature. But measuring the temperature on the black pipe where it Ts off to the priority loop, showed a 20 degree drop!
Lots of head scratching trying to figure out how in the world water could swirl around in the big, low loss header and temper my DWH loop. No way for that to happen. And no way for the return of the DWH loop to get into the low loss header, because there is a check valve in the black pump. I then shut off the valve below the black pump, and the temperature instantly shot up on my DHW loop!!!
Not only did the installer not put check valves in the DHW loop and the air coil loop, he also didn't install the check valve that came with the Grundfos pump, and that Buderus calls for in their design! Now, it is possible that he didn't want the integral check valve to fail and cause me problems down the road. So it may have been done on purpose. But either way, it has been reducing the capacity we get out of our indirect water heater for 11+ years. The true effect hasn't really been a problem. Maybe we have to bump the water a bit hotter during a long shower or if hot water is being used in multiple places in the house at the same time as the shower. It isn't like the shower turns ice cold.
It is the principle of the matter (that it isn't operating as effeciently as it could) that bothers me more than the real life consequences. 😁 It also means the house heat is deprived for a longer period, since it takes longer for the DHW loop to get the water tank up to temperature. Now, oddly enough, without the check valve in the air coil loop, I don't really have a full priority system. I have a mostly priority DHW loop, with the air coil loop getting a little bit of heat from being slightly sucked backwards into the DHW loop. I think the end result is still cold air at the heat registers while the DHW loop is active. But again, nothing that affects our comfort.
As mentioned in another thread, I intend to replace that mass of black pipe and low loss header with a cominbation magnetic dirt removal and hydraulic separator this summer. When I do that, I'll add a check valve downstream of the boiler primary loop pump, a check valve downstream of the DHW pump, and a check valve downstream of the air coil loop pump. I'll also move that pump out of the air handler and replace it with an ECM pump. It may be close to 30 years old.
Check valves for everyone!
Thanks again for your help, @The Steam Whisperer and @hot_rod. Much appreciated!
David
0 -
bear in mind that check valves may not solve everything you are trying to accomplish. if your air handler zone is calling when you get a call to make domestic water, the zone circ for the air handler does not shut off, only the primary circ on the boiler shuts off. you still have flow from the air handler zone going thru the boilers low loss header. the gb142 does not have a true priority for domestic as it only shuts down the primary circ so you will always have some degree of mixing going on if one of the heat zones is calling. but, nonetheless, each zone should have a check valve on it.
0 -
Th he black pump, does it have a check valve in it? If so turn off the red handle valve and see if that changes the temperature. when the indirect calls it may pull down the boiler temperature until that load catches up The load dictates the boiler operating condition, always. Measure both supply and return when the indirect runs
You are sure the black circ is off during DHW call?
Your DHW loop is a parallel loop.The green circ should have the motor horizontal, not vertical
Bob "hot rod" Rohr
trainer for Caleffi NA
Living the hydronic dream0 -
That's an interesting observation. I will have to take a look at how everything is wired for the air handler circuit. I am not sure if the air handler circulator is controlled by the boiler or controlled by my original control board from my old hydronic system. Either way, your point is that when the room thermostats are calling for heat, the air handler circulator will be on.
I will be adding some custom controls at some point, so I could probably set it up to shut off the air handler blower and circulator until the DHW cycle is complete. However, as I found out yesterday, that air handler loop only tempers my DHW loop by 1 or 2 degrees. The major effect is the missing check valve in the boiler pump allowing DHW return water to mix in with boiler supply water.
Thanks for bringing this up. I'll look into what it is truly doing and how.0 -
The black pump is supposed to have a check valve in it, but either the installer left it out or it has failed in an open state.
What you mentioned is what I wrote about above. The lack of the check valve in the black pump is what was tempering my DHW water. It was mixing DHW return water with boiler supply water. Instant 20 degree drop.
I am sure the black pump is off. That's how it is supposed to work (as per Buderus literature) and I can also hear it when it kicks on when the air handler cycle starts.
I noticed the green circulator orientation issue when I was looking at the system a month or so ago. I may have known it back in 2011 when it was installed too, but if I did, I forgot about it. I was going to change the orientation this summer when doing work on the system, and then the pump acted up last week, so I ended up taking it out and putting it back in. When I did that, I found that the shut off valve flanges rotate. So I was able to change the pump orientation without resweating the valves. The above photo was taken before I took the pump out and put it back.
What did strike me as odd is that the tip of the valve handle on the downstream side of the pump hits the flange bolt with the handle being aligned with the flange (which is the orientation needed to have the pump cylinder parallel to the floor). So even though they allow the flanges to rotate, that doesn't do me any good if I want the flange bolts to be at the same position on the clock as the valve handles (which are dictated by where they sit when sweated in). Is this a normal issue with those Taco valve flanges, or something odd about mine, where the bolts are larger than they should be?Because of the above issue, I couldn't put the pump parallel to the floor. I had to tilt it down slightly. So it may collect some gunk in it, but not as badly as if it was poining straight down. And it will not have water lubrication issues that it may have had when it was pointing straight up.
Thanks for poinint it out though. I appreciate it. Either the pump is a workhorse, or my water pressure was high enough to keep it lubricated (Taco allows that orientation if your pressure is 20 psi or higher).0 -
I've installed many a check valve over the past 45 years. I've seen the Germans use swing checks in the vertical position and wondered why? The Viessmann boiler showroom in Langley BC is piped entirely using swing checks.
I've had few problems over the years and have used soft seat spring checks or the pump IFC., but not both at the same time.
1 -
@Paul Pollets wrote:
I've had few problems over the years and have used soft seat spring checks or the pump IFC., but not both at the same time.
Thanks for the feedback. I appreciate it.
@hot_rod has me thinking that spring checks are my best bet too. I might be tempted to use IFC if the pump supports it, but I'll have to be sure to see curves for the pump with IFC installed. This seems to make a huge difference in flow for some pump models. For lower temperature, I'll probably go with these valves from Caleffi:
For higher temperature needs, I'll probably go with these HytroTrol valves from Bell and Gossett:
David
0 -
A few things about swing checks that make them less desireable for hydronics. The gate inside has a long travel length from full close to full open. So when flow stops that long stroke can cause a clap noise. Hydronic spring checks move 1/4" or less. A hydronic check should have a conical shape so you get smooth flow.
Swing checks have a Cv rating. The rating is with the gate wide open, if the flow is less than the Cv the gate is floating between open and closed position. Not a great flow path.
Lastly a swing check, unless weighted need a pressure differential to close and also to seal tightly. In hydronic application, the pressure is the same on both sides of the check when the pump is off. There is no pressure difference to hold it closed tightly.
swing checks are actually used in no power /protection loops as the hotter, more buoyant water will force them open to allow heat to leave the boiler. Commonly used on wood fired boilers for over heat dump protection.
Not all swing checks are able to be used in vertical and horizontal piping, check with the installation sheet
Bob "hot rod" Rohr
trainer for Caleffi NA
Living the hydronic dream1 -
I checked my wiring. My boiler primary loop pump and my air handler coil loop pump are both wired to the same relay. So when the boiler turns off the boiler pump, it also turns off the air handler coil loop pump. I even checked two possible states to be sure it is always true:
- If the boiler has no call for heat at all and then it has a call for DHW heat, it only turns on the DHW pump. The relay for the boiler pump and hydro air loop pump is not energized.
- If the boiler is in house heat mode (so the boiler pump and hydro air loop pump are running), and then it gets a priority call for DHW, it does de-energize the boiler pump relay, thus shutting off the boiler pump and the hydro air loop pump.
I believe what you stated would be correct if the air handler zone pump was being controlled separately. A separate control board wouldn't know that the boiler was giving priority to the DHW zone (unless it was monitoring the same sensor or talking to the boiler). As it is, the air handler blower is still controlled by the air handler control board. This means the blower doesn't shut off. It sucks the left over heat out of the heating coil and then blows cold air until the DHW priority call is complete.
I could probably rewire it so that the blower is also turned on by the boiler. I think I remember that the hydronic coil has a temperature sensor attached. I think when the thermostat calls for heat, the old control board would have normally turned on the pump first. Then the air handler wouldn't be turned on until heat was sensed in in the coil. But apparently it doesn't turn off the fan in that same method (when the coil goes cold). It turns off the fan when the thermostat stops calling for heat. And the air handler probably kept the pump running for a little bit after the thermostat stops calling, to not waste the heat in the coil. The GB142 does the same thing. It keeps the pump going for half a minute after the thermostat is satisified.
So the order of events, I think, is:
- Thermostat calls for heat.
- Boiler turns on hydro coil zone pump and main boiler pump and starts ramping up heat.
- When hydro coil gets above a certain temperature, the blower turns on.
- When thermostat is satisfied and stops calling for heat, the boiler keeps circulating water for about half a minute, and then shuts off the pumps.
- The air handler blower also delays shutting off for a bit, to suck out the rest of the heat in the hydro coil.
Allegedly, some year, I'm going to be putting together a custom control board that will modulate the boiler firing rate, and the ECM blower in the air handler (I replaced the PSC blower in 2020, but it is still being used at fixed speeds for AC, heat, and fan-on modes). The control board will also be driving an inverter on my (yet to be installed) AC condensers (currently have 2 fixed speed condensers). It may also be used to modulate ECM circulators I may get in the future. It may also control my air duct zones and register vents. In other words, I could have variable speed control over every single motor in the heating and cooling systems. The fun part will be coming up with algorithms to optimize everything working together! 😁
Thanks again,
David
0
Categories
- All Categories
- 87K THE MAIN WALL
- 3.2K A-C, Heat Pumps & Refrigeration
- 58 Biomass
- 427 Carbon Monoxide Awareness
- 113 Chimneys & Flues
- 2.1K Domestic Hot Water
- 5.7K Gas Heating
- 109 Geothermal
- 161 Indoor-Air Quality
- 3.6K Oil Heating
- 70 Pipe Deterioration
- 995 Plumbing
- 6.3K Radiant Heating
- 391 Solar
- 15.4K Strictly Steam
- 3.4K Thermostats and Controls
- 55 Water Quality
- 44 Industry Classes
- 48 Job Opportunities
- 18 Recall Announcements