Weil-McLain Eco 155 Piping problem
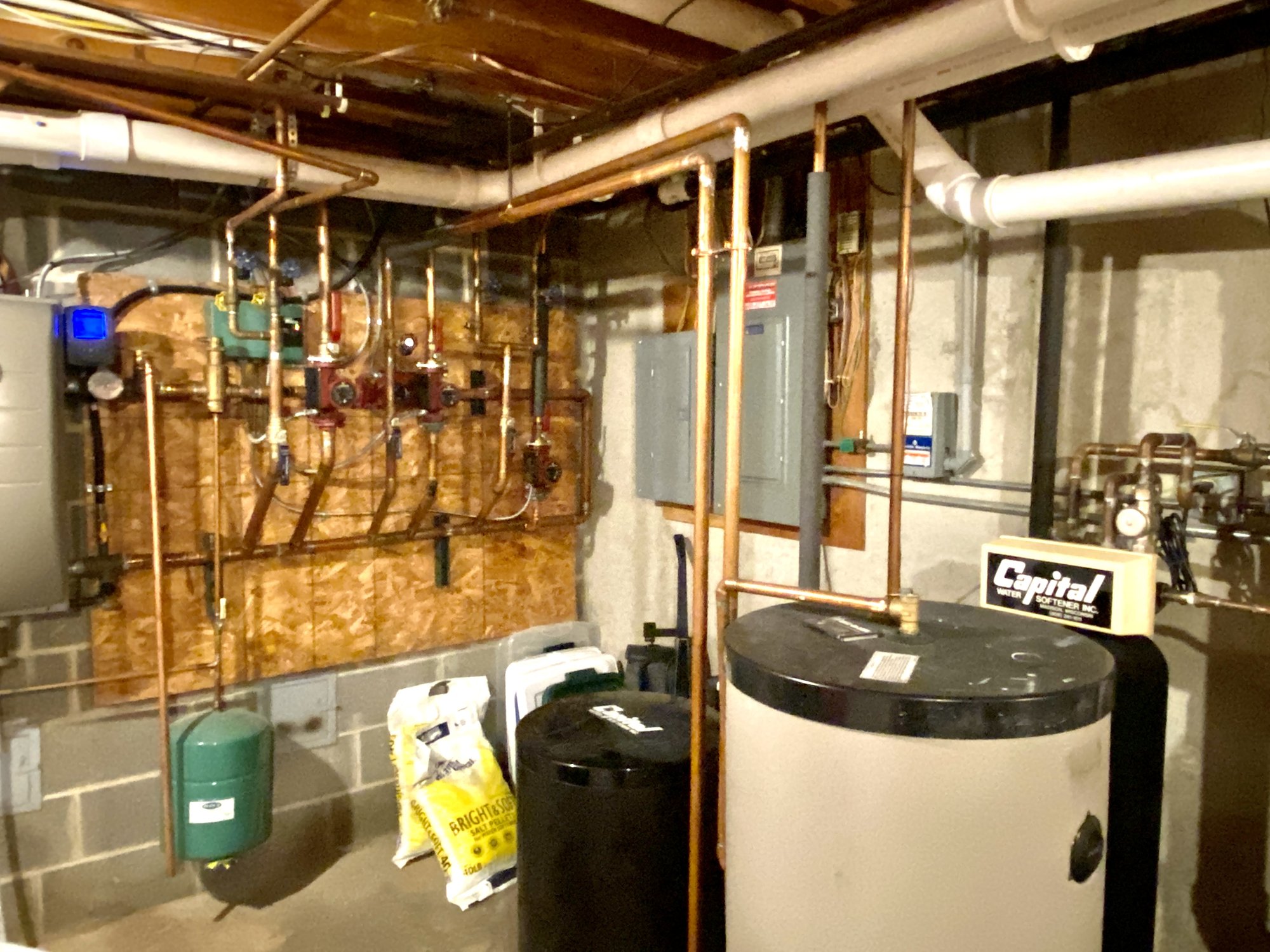
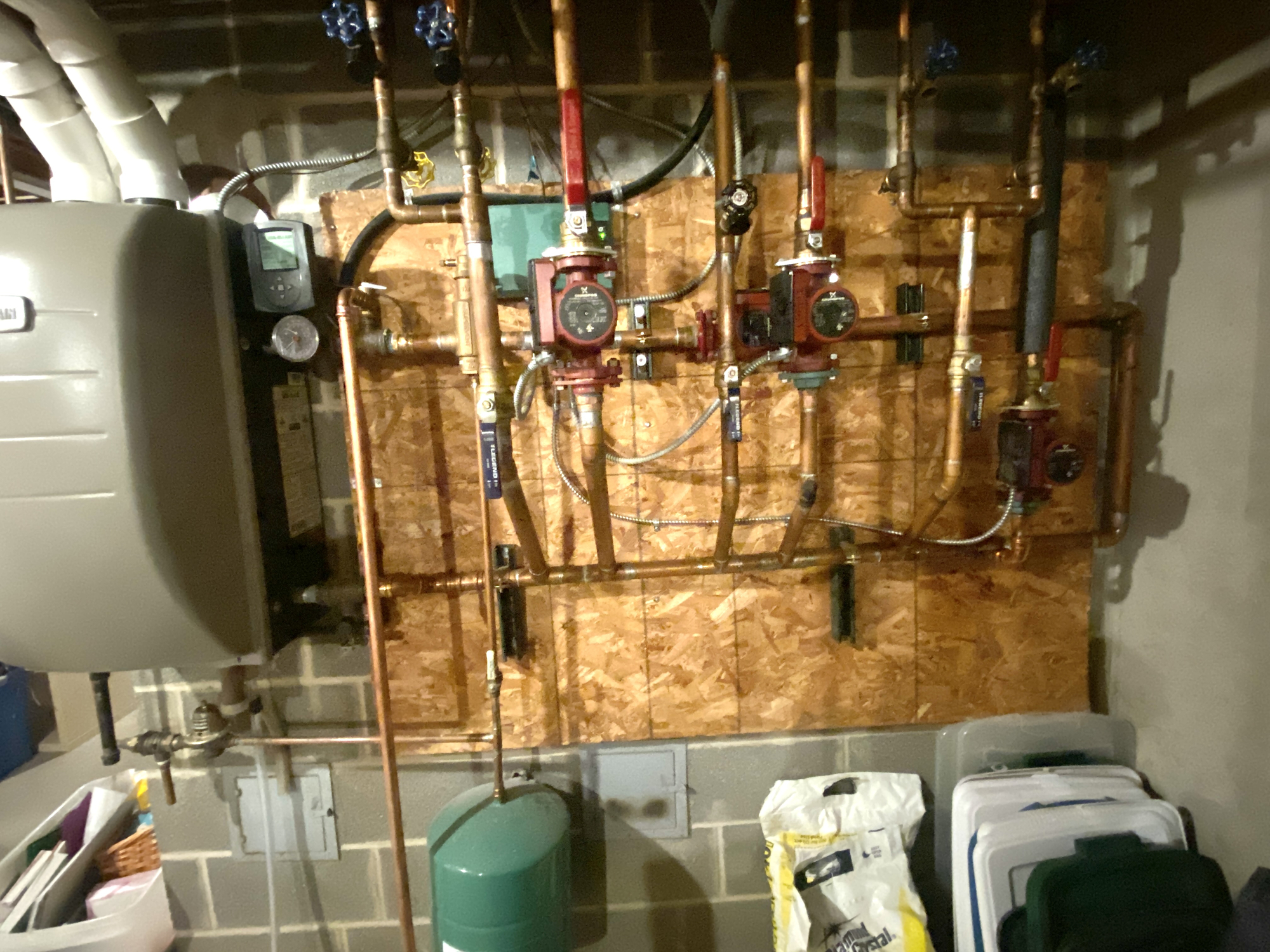
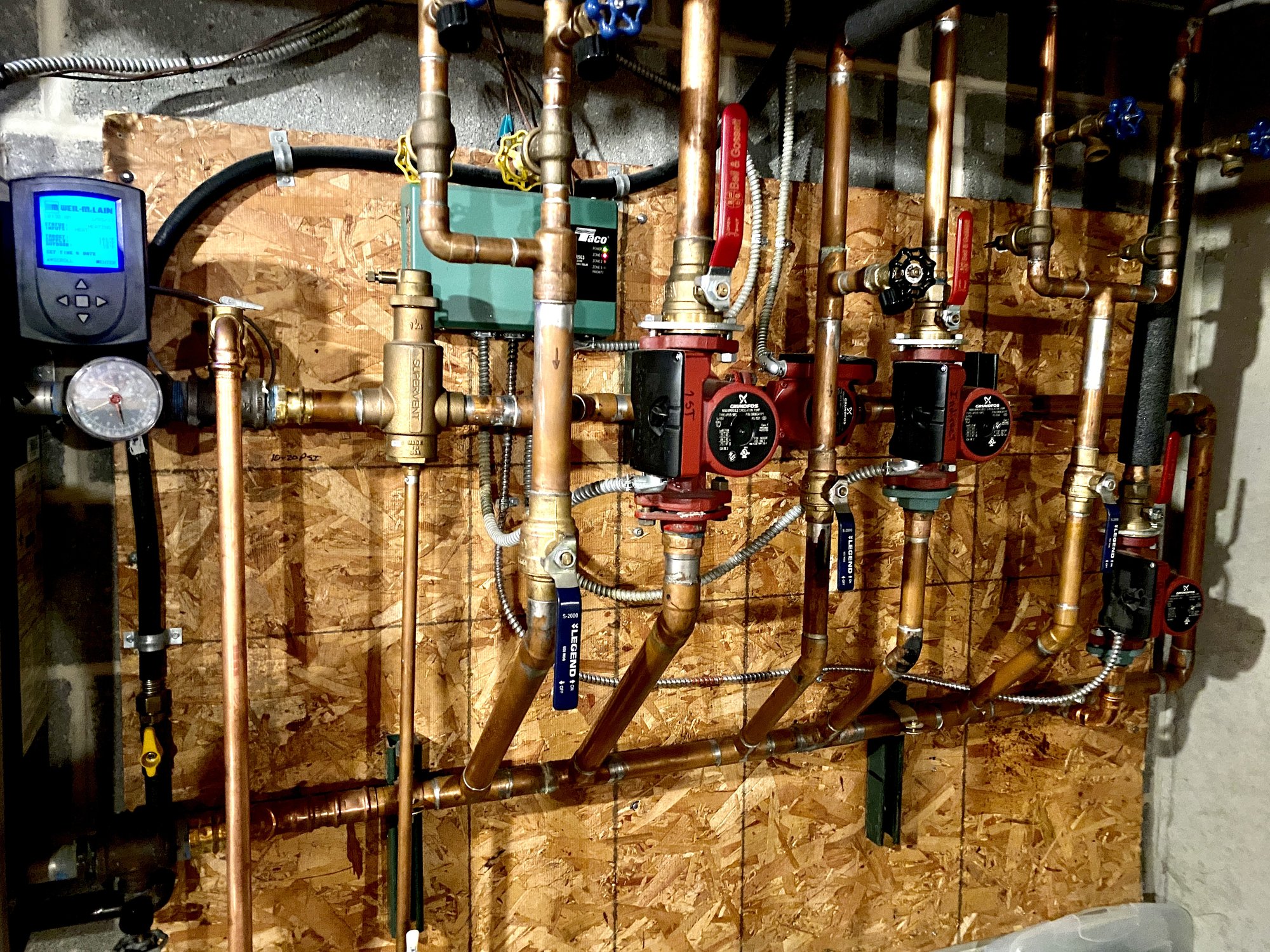
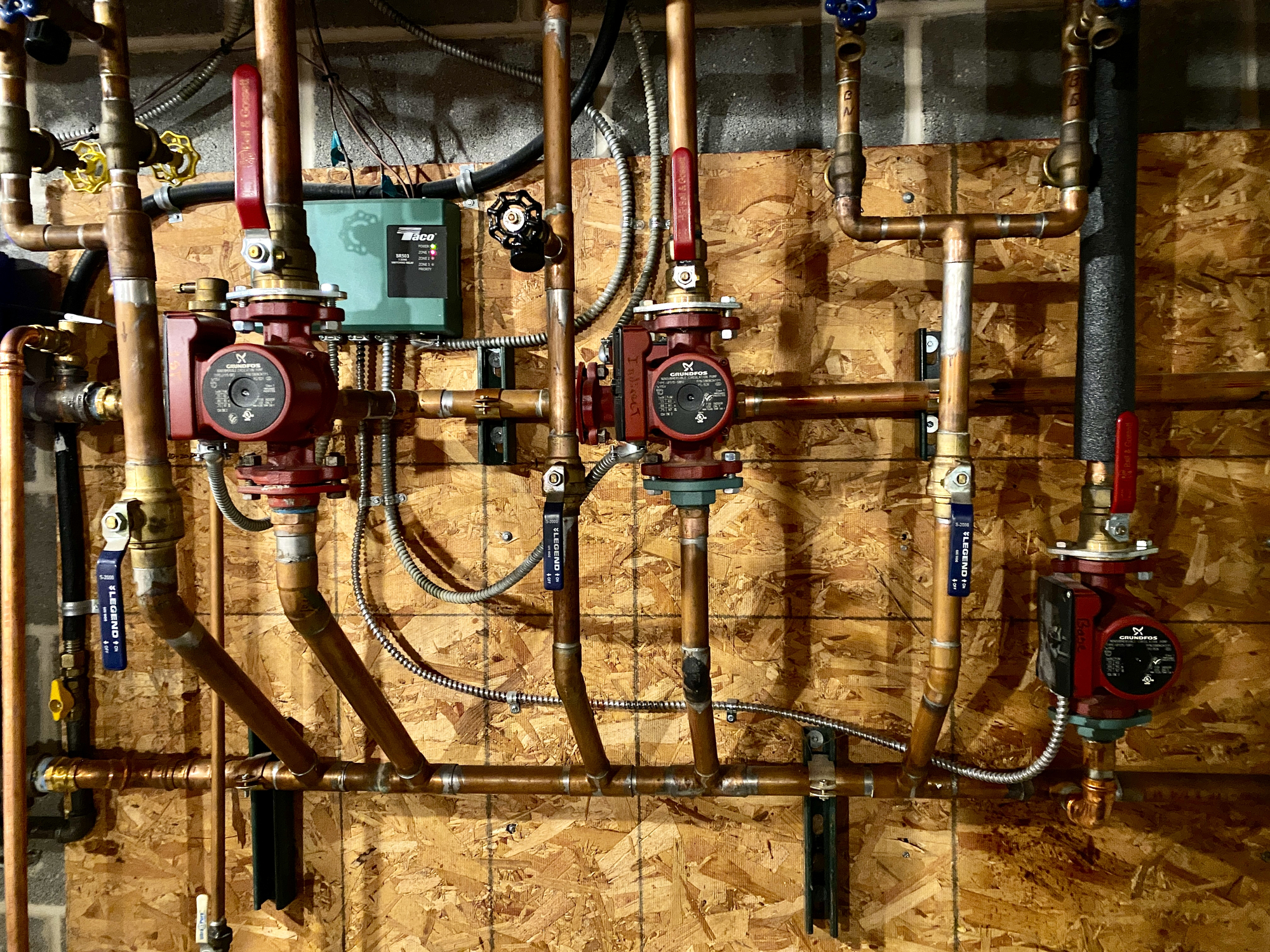
Comments
-
It appears the installer used the Direct connect piping design and each zone pump is a secondary loop. The Primary/Secondary design in the O/I manual illustrates the System side as the Primary loop and the Boiler as a secondary loop feeding the system loop.
There is more than one way to pipe the system (as more than one is illustrated in the manual) but there are several other correct ways and lots of incorrect ways. I would need to measure the inlet and outlet temperature of the boiler as different conditions happen.
for example:
What happens when only one system zone circ operates at a time? (each zone circ is a "system circulator" in your case)
What happens when only one zone circ is operating and another zone circ calls for heat?
What happens when the DHW calls for heat and nothing else is operating?
What happens when the DHW calls during one or both of the other zones are already calling?
If any of these conditions cause an excessive temperature drop at the return while the boiler is operating at a relatively high temperature (Like when the DHW is calling), then there may be an issue that is not in line with the design conditions of the boiler. Without those temperature readings from those tests, I would only be speculating. The existing piping design appears to be in line with accepted design criteria. @hot_rod might see something that I don't see here.Edward Young Retired
After you make that expensive repair and you still have the same problem, What will you check next?
2 -
Since both ways of designing primary secondary are included in the I/O Manual, Your installers design may be fine, but I would want to do the tests I described above to watch the boiler reaction to the possible extreme temperature changes.
The I/O manual actually has your setup (2 space heat zones and one DHW zone) in diagram 51
This would insure that the unusual temperature changes would not be a problem.
Edward Young Retired
After you make that expensive repair and you still have the same problem, What will you check next?
1 -
I think there is a Grundfos Alpha pump as the boiler loop pump, hidden behind the middle zone circ. I wonder if that is enough capacity for a 155? It shows 7 gpm, but not a head number?
The white powder on the combustion side could be from the burner not dialed in properly. Or is it sucking in and exhaust fumes from the vent recirculating, or chemicals nearby?
The control probably has some settings to prevent short cycling with all those zones you have. Do you have a list of how the parameters were adjusted?Bob "hot rod" Rohr
trainer for Caleffi NA
Living the hydronic dream1 -
Bob, I believe the boiler minimum 7 GPM is when the boiler is on the lowest fire and the 14.5 GPM is when the boiler is firing at max fire. The boiler pump flow rate must be controlled by the control that also modulates the gas input. The short secondary loop (AKA boiler loop) leaves very little pipe friction for that pump, I'm not sure what the Pump Head is but I believe it's at the low end.
Edward Young Retired
After you make that expensive repair and you still have the same problem, What will you check next?
1 -
This is the MAIN reason I like thermometers on the install at every Delta T junction on the boiler room piping. It takes alot of the guess work out of troubleshooting and reveals problem in Real Time. Mad Dog1
-
thank you for the replies. I have a technician coming out today to look at the set-up. I will show him this thread.
I feel like combustion tests were done at one point, but I don’t have any records.0 -
Here’s an update after having a technician out to look at things.
Technician from today 02/09/23
“Upon arrival evaluated system piping. Found that system piping is incorrect per manufacture. Examined the inside of boiler heat exchanger. Found no cracks inside heat exchanger, found stains, but no cracks. Ran system with gas off to look for any excessive water leaving the drain to see if there are any cracks within heat exchanger. If there was a crack we’d have a good amount of water dripping out. Found no water dripping from condensate drain trap. System is operating correctly at this time. Test ran boiler and performed combustion test.“
Technician (different company) from a prior visit a few months ago stating leak in heat exchanger:
“The leak is internal in the fire tube heat exchanger. Our technician diagnosed the leak by isolating the heat exchanger and performing a pressure test. After 10 minutes pressure in heat exchanger the pressure dropped from 15 psi to 5 psi. The water leaking from the heat exchanger is going down the condensate drain.”0 -
Maybe I'm not seeing the piping correctly? Looks like a series primary loop as per the manual? Supply out of boiler thru the air purger back into boiler return. Secondary circs off close tees. Air sep is at the hottest point in the system, no problem
If it is a 15-55 loop pump, that is a bit light if you are designed for 20∆, adequate for a 30∆
Your closely spaced tees are on the bottom part of the loop, is the only difference.
I don't see any strainers on the system?
I'd take the SuperVent apart see if it is plugged, they double as Y strainers sometimesBob "hot rod" Rohr
trainer for Caleffi NA
Living the hydronic dream0 -
Won't each supply side in each set of CST's in this setup get increasingly cooler water as the discharge side of each circuit empties into the return pipe to the boiler before it?0
-
hot rod, would you like me to take a few closeup pics, so you can see everything a little easier?0
-
This is how I’m seeing the piping. A common primary secondary series loop, the boiler is in the primary loop, 3 zone pumps as secondaries
There will be a temperature drop around the loop, I assume one zone is the indirect, so it should be a priority zone, meaning the other two zones will be shut off until the tank recovers. So only two heat zones are in series seeing some temperature drop on the last zone, when both are running
The loop should be at least 1”, possibly 1-1/4 depending on what the total load of the heating zones is.
If you do know the total heatload, that control can be programmed to that number, that really helps eliminate short cycling.
Another cause of short cycles or overheating the boiler, causing a limit trip would be a restriction. In the boiler itself or the primary loop piping.
That firetube boiler should last 15 years or more if it has good water quality and adequate flow.
It looks like the loop circulator is a Grundfos Alpha? So I don’t think it is a variable speed controlled pump.
Did the tech get into the control settings? They have a lot to do with how well that boiler runs and matches your systems needs.
ODR should be enabled, ramp settings, firing rate, etc The IO manual is written to be fairly easy to understand and adjust the settings.Bob "hot rod" Rohr
trainer for Caleffi NA
Living the hydronic dream1 -
If you have had 2 failed HX, maybe do a water analysis.
Not many places in the USA where the tap water is acceptable, from a hardness standpoint, 5- 7 GPG.
Chloride levels in some areas where a lot of deicer is used are, could be a problem.
Rocky Mt west water can be tough, both hardness and chloride levels.
Here is the Weil and Lochinvar water suggestion. Different opinions on acceptable GPG
Fix the water or buy some quality water to protect the new boiler.
Seen boilers fail in a few years from hard, high mineral content, fill water.Bob "hot rod" Rohr
trainer for Caleffi NA
Living the hydronic dream0 -
Hello again, I’m digging up my post from a couple months ago. A few significant events got in the way of my boiler investigation. I appreciate everyone who has chimed in with their thoughts. Although, I’m a bit overwhelmed trying to understand what to do next, as a non-hvac person.
I’m planning on contacting my hvac company to try and troubleshoot. On their last visit, based on some tests, they said the heat exchanger is cracked again and needs to be replaced. Now, the boiler makes a lot more noise when heating. Hard to describe, but it starts as a vibration, and the noise gets louder and faster. Video link of noise below.
If possible, I’d like to help the technician with some thoughts on next steps. Water quality seems like one thing, but what about the piping or anything else that I can add to the list to show him.
Video link of noise:
https://youtube.com/shorts/Y07nmyKx_4k?feature=share
0 -
Piped direct rather than primary-secondary there is a possibility of insufficient flow when only one small zone calls, and this could cause a hot spot in the HX.0
-
It doesnt appear to be direct piping. As HotRod mentioned it appears to be common primary secondary series loop, the boiler is in the primary loop, 3 zone pumps as secondaries. Not the ideal for some circumstances but will work fine if the math was done ahead of time. If you want to know if the Hx has failed, just have a tech pop the relief valve and install a gauge, shut off the valves to the zones and air test it.Tom
Montpelier Vt0 -
This is direct piped with closely spaced tees for the zones.
It's a hybrid, meaning piping is incorrect unless you add a closely spaced tee for a boiler loop, plus a boiler loop circulator before all other zones.
I think this piping layout would work fine for a high mass low resistance boiler, but not for the ECO 155.
And I think this part was missed in the manual
This system is zoned with circulators. So automatically, you should have a boiler loop primary secondary. This is missing. With it, then you can call it a complete series p/s piping.
0 -
Best I can tell from the earlier pics it is a series primary loop with the boiler within the loop?Bob "hot rod" Rohr
trainer for Caleffi NA
Living the hydronic dream0 -
I am waiting to get an appointment, set up with the technician, and I will show him this thread so he can review everyone’s thoughts. Let me know if you’d like me to take more close-up pictures if anything is confusing happy to do so and thanks again.0
-
Yes, it is (edit: reading up more, we call this a one-pipe primary secondary, and what I assumed to be the "only" p/s piping is a two-pipe primary secondary.)
but is it not incorrect to have the boiler in the primary loop when it is a low mass high resistance unit? So we have a separate boiler circulator
Or are we saying the current
systemboiler circulator could take care of this as long as it met the minimum flow rate the boiler is calling for?0 -
@dko
It is not incorrect to have a low mass boiler installed on a primary loop, remember whichever loop has the expansion tank is referred to as the primary loop. There is no "system circulator" in the installed photo, just a dedicated boiler pump (primary loop pump) If a manufacturer specifically does not allow this method, then I would say change it, in this case the installation manual specifically calls this out as an accepted P/S piping method, it just looks different from what people are used to seeing, and the piping method is not a preferred one in general. The system is however functioning correctly, the OP has stated they have combustion issues, cleaning out white residue from what sounds like the fireside of the heat exchanger, and moving the exhaust and intake (sounds like flue gas recirculation). If the system had exhibited the inability to heat particular zones I would recommend (possibly) a re-pipe, there will be a temperature drop between each secondary loop in this piping method
In the photo there are 3 (secondary) zone pumps (2 heating zones, and 1 DHW), and 1(primary) boiler pump. Assuming that the boiler pump has been chosen correctly per the heat exchanger requirements, (and that the close tees are correct, which they look to be), this piping strategy will provide hydraulic separation from the zone circulators, and would provide the correct flow through the boiler that is required. There are downsides to the piping arrangement that is shown, and for a typical residential install I would not choose to install it as shown1 -
Thank you for the explanation
0
Categories
- All Categories
- 87K THE MAIN WALL
- 3.2K A-C, Heat Pumps & Refrigeration
- 58 Biomass
- 426 Carbon Monoxide Awareness
- 113 Chimneys & Flues
- 2.1K Domestic Hot Water
- 5.7K Gas Heating
- 109 Geothermal
- 161 Indoor-Air Quality
- 3.6K Oil Heating
- 70 Pipe Deterioration
- 994 Plumbing
- 6.3K Radiant Heating
- 391 Solar
- 15.4K Strictly Steam
- 3.4K Thermostats and Controls
- 55 Water Quality
- 44 Industry Classes
- 48 Job Opportunities
- 18 Recall Announcements