"I've never had a Munchkin that I couldn't get fixed and operating."
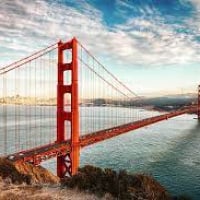
The burner will ignite, but the flame goes out within a second or two; happens three times and then locks out with an F09 error code.
I've:
- replaced the flame probe
- opened the firebox and it was clean
- made sure the condensate drains properly
- disconnected the flue to check for blockage
- checked the gas pressure; 8" static, 6" dynamic
The gas pressure dropped a bit too far. The owner called the utility and they came out and replaced the meter and regulator. And I can't get a reading on the rectification signal because the flame goes out too fast.
The only thing I haven't done is to check the burner screws to make sure they're clean and have good continuity for grounding, but we serviced the boiler a year ago and I cleaned them then.
I feel as though it's a rectification problem because the burner lights.
What have I missed?
Two btu per sq ft for degree difference for a slab
Comments
-
After the grounding is good, perhaps the board is not seeing the FS input?0
-
@JUGHNE Perhaps. We upgraded the circuit board to a 926 three years ago. Will go back and check the burner screws, but that's all I've got so far.8.33 lbs./gal. x 60 min./hr. x 20°ΔT = 10,000 BTU's/hour
Two btu per sq ft for degree difference for a slab0 -
is there a place you can put the manometer on the manifold to the burner? Sounds like the the pressure is falling on the outlet of the (i'm guessing it is a valve/regulator that regulates based on fan speed on these) valve.
I guess look at the power to the valve and see if the valve deenergizes before or after the flame goes out.0 -
Might need an analog meter to catch that.0
-
gas pressure is my first thought. A slack tube manometer reacts quickly to catch a quick, possibly momentary drop in pressure. You have eliminates all the other possibilities.Bob "hot rod" Rohr
trainer for Caleffi NA
Living the hydronic dream0 -
is there a place you can put the manometer on the manifold to the burner?I check the outlet pressure. It was -1.50" on prepurge and when the burner lit, it was -0.01 which is within spec.
I'll check VDC readings to the gas valve. Meter probes on the two outside prongs of the plug, correct?8.33 lbs./gal. x 60 min./hr. x 20°ΔT = 10,000 BTU's/hour
Two btu per sq ft for degree difference for a slab0 -
You'll have to look at the schematic. I'm just going on general logic of figure out if the control is shutting it off or if it is some sort of mechanical failure of the valve or the regulator. Being that quick I think it is mechanical since that is a really short time to try to prove flame(unless it was trying for a while before you saw flame, like the valve is slow to open).0
-
-
-
Where's Massapequa"s own, the Great Mike Jablonski?? He KNOWS the munchkins very well, has installed tons of them and they are still running today. He would know. Are you lurking Michael? Come out and play.... Mad Dog 🐕0
-
First, the 926 board should have been programed for a 100 sec post purge instead of the 25 sec.The only thing I haven't done is to check the burner screws to make sure they're clean and have good continuity for grounding, but we serviced the boiler a year ago and I cleaned them then.That has been the #1 cause of a F09 error code. The Burner tube should have been re-gasketed with the newer thicker gasket to the front plate. Rectification is thru those 4 bolts to the front plate from the flame on the burner tube. I use a socket to tighten those 4 bolts, good and tight. Make sure the ground wire from the front plate to the control and to the terminal strip is tight. Re-plug them if necessary. I think this is a rectification issue. The rectification probe clean and in good order?0
-
There were a bunch of modifications to that 925 control board over the years, starting in 2004 or 05?
Vision 1, Vision 2, Revision R allowed 194F. One of the Visions allowed two temperature, for indirect and the ODR function. The control setup and piping manuals changed also.
Usually in the bottom right corner of the manual it shows the date it was updated.Bob "hot rod" Rohr
trainer for Caleffi NA
Living the hydronic dream0 -
I felt certain that it was a rectification problem and measured 2µA at the flame probe which is not a strong signal. I replaced the probe with a new one and still got the same reading. Tech. support suspected that the burner didn't have a strong enough flame to generate enough signal to satisfy proof of flame and had me read the voltage at the gas valve plug; got about 19 VDC when it should have been 24 VDC and thought that it wasn't enough power to properly hold the gas valve open.
He said that it was a common occurrence that the wiring harness goes bad and doesn't deliver the full voltage to the gas valve. I'm going to order a new harness AND gas valve as a dying device can reduce voltage readings.
Previously, I removed the burner, cleaned the screws and burner surface and replaced the burner gasket. This did nothing to revive the boiler and I have yet to find this as a solution to rectification problems.8.33 lbs./gal. x 60 min./hr. x 20°ΔT = 10,000 BTU's/hour
Two btu per sq ft for degree difference for a slab1 -
-
I will tell you another story that happened a long time ago and since I have trouble remembering what I had for breakfast, I will give you the gist of the story.
I had an F09 error code on a 140M ( fairly new installation) that I couldn't resolve. I took volt meter readings on the rectification wire. I took readings on the board plug and the solder joint on the back of the board. Come to find out the Molex jack wasn't transferring properly to the board plug. I bought some molex jacks and soldered a replacement on the cable and that solved the problem. I never figured out the reason why that anomaly happened, but it did. I did notify HTP of the issue. A new cable may just be the fix.Tech. support suspected that the burner didn't have a strong enough flame to generate enough signal to satisfy proof of flame and had me read the voltage at the gas valve plug;You will have to explain that one to me. The flame doesn't generate signal, the board does. The flame just rectifies ac to dc. But what'da I know.
You did do a combustion analysis? I would suspect the flame to be correct. A correct micoamp reading on a newly cleaned Munchkin should be 4.1 microamps. 2 is totally inadequate. Are you reading the microamps off the display board or independently with a meter?0 -
The current is flowing though the flame. The control provides a source, the flame conducts it to ground but only in one direction so the size of the flame can affect the current if it is too small below a certain threshold.
Not sure how one does a combustion analysis if it only stays lit for a few seconds.
Sticking a probe in to the contact side of a connector can collapse it although just a little bit of oxide can affect the current at the types of voltages of the flame sensor. Contact cleaner probably would have worked as well as a new contact.1 -
How much time and money into a near 20 year old boiler?This little 50K boiler does both heating and DHW for the main house and a rental cottage. Downtime is a concern, especially in the middle of a California winter.
Thanks for your comments, @HomerJSmith and @mattmia2. I know very little about rectification.Are you reading the microamps off the display board or independently with a meter?I used a digital meter to read the µA. The control board readout was jumping all over the place.Not sure how one does a combustion analysis if it only stays lit for a few seconds.Early on, I played around with the throttle - blindly - thinking it was a combustion issue. I will have to dial it in with my analyzer once I get it running.
I also wanted to get a voltage reading for the gas valve directly off the board with the plug removed, but the same plug has the wires for the fan speed control and the fan went into high RPM and I wasn't sure if ignition would happen.8.33 lbs./gal. x 60 min./hr. x 20°ΔT = 10,000 BTU's/hour
Two btu per sq ft for degree difference for a slab0 -
I do a combustion analysis every time I clean a mod/con, about every 3 yrs. I charge a hefty sum on top of my labor to do the analysis. Gotta pay for the certification.
I cleaned any possible oxide on that molex jack and plug, to no avail. I'm stumped.so the size of the flame can affect the current if it is too smallI'm not so sure of that. If the flame doesn't reach the probe, ya. Look thru the sight glass does the flame look healthy?
If you can't get display readings that are stable, there may be something else wrong maybe with the display or controller. The advice that I was given is to unplug everything one at a time and replug it. That goes for the display cable, too. Plug your laptop to the controller and look for the error codes, might give you an idea.
This unit has been running for a long time, but I would want to check the polarity of the power supply that is the outlet and the connection in the switch box, just to be sure. Grounding is especially important.
-1 -
Well, that is a clue of some sort. Is the flame also jumping or is the flame stable while that happens? Also keep in mind a dmm only reads a couple times a second so it does a poor job of measuring something that is changing rapidly.
I used a digital meter to read the µA. The control board readout was jumping all over the place.
Did you figure out if the flame goes out before or after the voltage to the valve drops?0 -
There are a few sec for the flame to stabilize and if the controller doesn't see the presence of a flame with the rectification current, it will shut the gas valve down. It seems to me that if there is initial ignition that the gas valve is ok, but is being shut down. 2 ua would do it, I think. I have not ever come across a Munchkin with less than 2.5ua. Mostly in the 3 ua area and 4.1 ua after cleaning.
There were two designs of the burner tube, one with just holes and a later one with a fabric covering. The one with holes, I would just wire brush.
I am assuming it is Natgas and not LP.0 -
-
Did you figure out if the flame goes out before or after the voltage to the valve drops?The flame goes out before the voltage drops which indicates a weak solenoid in the gas valve, not enough voltage to the solenoid or something else.8.33 lbs./gal. x 60 min./hr. x 20°ΔT = 10,000 BTU's/hour
Two btu per sq ft for degree difference for a slab1 -
I'm usually all for figuring out what went wrong, but this thing is old and I'm guessing parts are not inexpensive:
0 -
You can try Jupiterheating.com Does it have the Dungs gas valve or the Honeywell gas valve? No dust, pollen, drywall or other debris plugging up the valve?0
-
I would find a way to supply my own 24volts to the gas valve at the appropriate time. Then you will know if the valve is good, and the gas supply is good.Serving Northern Maine HVAC & Controls. I burn wood, it smells good!0
-
It turned out to be a bad gas valve. The rectification signal went up to 5µA.
The voltage at the gas valve hasn't changed: 19.5 VDC when I'm told it should be 25 VDC. Perhaps the harness is compromised and still needs replacement down the line.
Thinking about it now, had I know the resistance of a good coil, I could have ohmed out the gas valve, no?
That's the first gas valve I've had to replace on a Munchkin. This was a Dungs, others are Honeywell. Both are extremely reliable.
Thanks to everyone for their suggestions. Finding the solution is such a relief.8.33 lbs./gal. x 60 min./hr. x 20°ΔT = 10,000 BTU's/hour
Two btu per sq ft for degree difference for a slab4 -
FWIW, I did change a board on the 2003 model.
There were 2 choices based on the color of the transformer.
Mine is a red transformer.
Book indicates the gas valve is 24 VDC.0 -
is there an "i told you so" button :-pIt turned out to be a bad gas valve. The rectification signal went up to 5µA.
The voltage at the gas valve hasn't changed: 19.5 VDC when I'm told it should be 25 VDC. Perhaps the harness is compromised and still needs replacement down the line.
Thinking about it now, had I know the resistance of a good coil, I could have ohmed out the gas valve, no?
That's the first gas valve I've had to replace on a Munchkin. This was a Dungs, others are Honeywell. Both are extremely reliable.
Thanks to everyone for their suggestions. Finding the solution is such a relief.
my guess is that the coil in the gas valve is fine and the failure is mechanical in nature like the diaphragm that modulates the flow based on the pressure or it is just binding0 -
The red transformer is the older 925 board. The upgrade 926 board has a black transformer.JUGHNE said:FWIW, I did change a board on the 2003 model.
There were 2 choices based on the color of the transformer.
Mine is a red transformer.
Book indicates the gas valve is 24 VDC.8.33 lbs./gal. x 60 min./hr. x 20°ΔT = 10,000 BTU's/hour
Two btu per sq ft for degree difference for a slab1 -
Could have been fine debris from gas piping was partially blocking inlet screen, take a look at if you kept old as a memento. Or the very fine dust that gets through coul have impeded the diaphragm inside valve just enough. Who know for sure but you won the battle. Gianonnis are a nemesis some times, especially the ones over 500mbh that you can’t reach all the way to the back of while cleaning. Rrrrrrrr!1
Categories
- All Categories
- 87K THE MAIN WALL
- 3.2K A-C, Heat Pumps & Refrigeration
- 58 Biomass
- 426 Carbon Monoxide Awareness
- 116 Chimneys & Flues
- 2.1K Domestic Hot Water
- 5.7K Gas Heating
- 109 Geothermal
- 160 Indoor-Air Quality
- 3.6K Oil Heating
- 70 Pipe Deterioration
- 994 Plumbing
- 6.3K Radiant Heating
- 389 Solar
- 15.4K Strictly Steam
- 3.4K Thermostats and Controls
- 54 Water Quality
- 44 Industry Classes
- 48 Job Opportunities
- 18 Recall Announcements