Differential Bypass-Based Primary/Secondary

First, lets get the obvious out of the way: I'm aware that this was an ambitious project to take on, and if I had known at the outset how much time and stress I would lose to it (and that the pipe fitter friend who offered a hand would flake out), I probably would have hired a pro. It's questionable whether I could have found a pro to take the job on this year, but it is what it is. I'm an engineer who likes to learn new skills and work with his hands and doesn't get to do much of either at work, so I got in neck deep. Scold me if you feel the need - some guy at my local Ferguson already did when I tried to ask about products to address thermal expansion on long runs - I probably deserve it, but I'm too close to the end to stop now. I have redundant heat via mini-split heat pumps that are rated to -5F and am comfortable working slowly to get things right. I intend to have my work checked by someone qualified when I'm confident it's done.
I have disconnected my 2001 Utica MGB100HID (100k BTU) and 50 gal water heater and installed a Rheem RCBH199DVLN. (120k BTU heating, 199k BTU domestic hot water mode). I know this is a bit oversized, but I wanted to be sure the unit could supply enough hot water for 2-3 showers at once with the water coming out of my well at 45F. The 11:1 turndown ratio made me confident it wouldn't short-cycle.
The system works - it makes the house warm and the shower hot (Hot water sulfur smell - the original genesis of this problem-solving exercise - is totally eliminated, too) - but I tried to get clever and installed it as primary loop only, despite the manual warning me to only install it as primary/secondary. The manual said this was to prevent short cycling, and based on what I knew about the system, I was pretty confident that it wouldn't short cycle...
Well... I was right and it does NOT short cycle. What it DOES do is deadhead the pumps (I installed the original circulator - a Grundfos UPS 15-58 FC - as a helper, thinking this would solve a different problem. I'm no longer convinced this was really necessary) for a few minutes after the last zone valve closes, even if I manually set the pump afterrun time to 0 minutes. I don't know why the setting doesn't work and don't intend to find out. Time to fix it right. For now, I have locked one of the zone valves open and disconnected its thermostat to make sure the system can always flow, but this is not a permanent solution. Interestingly, despite several notes in the manual about needing to respect minimum flow rates "outlined in this manual", there are no minimum flow rates outlined in the manual. (Manual available here: https://images.thdstatic.com/catalog/pdfImages/a4/a48d4136-81f0-4437-ab77-5bb2565f9a32.pdf )
Here's a diagram of how the system is currently piped. Red X is so some poor sap doesn't find this pic without context via search engine and think this is OK:
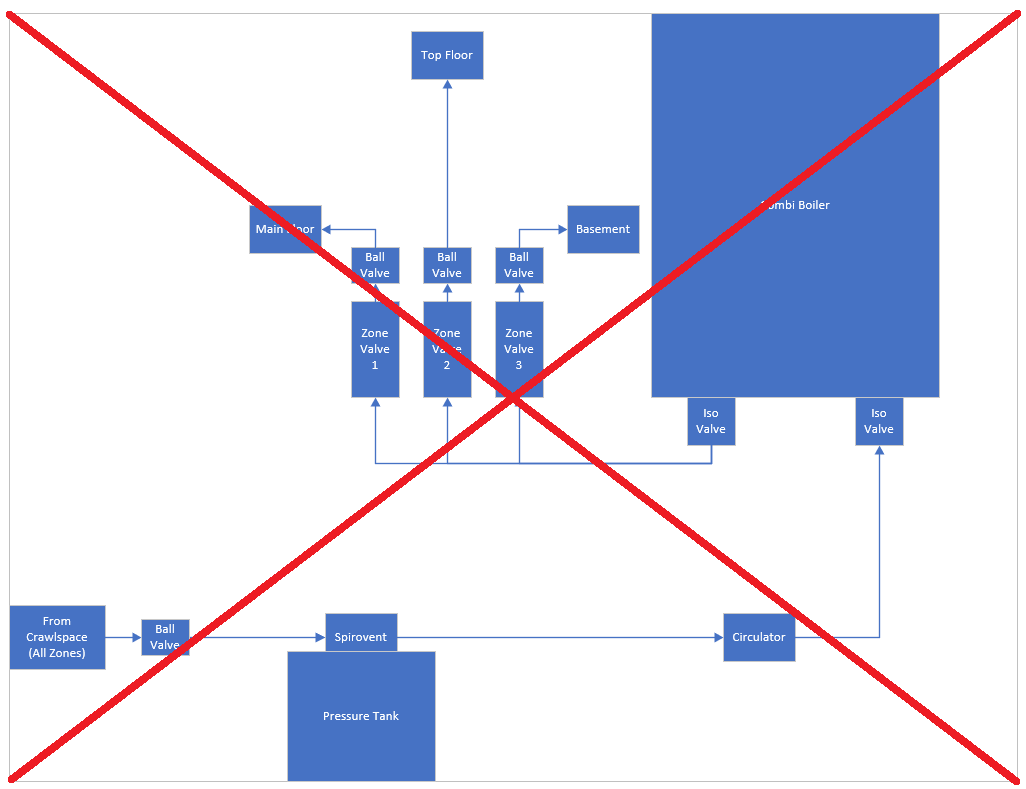
A "textbook" P/S layout isn't really possible, because the zones do not return to the basement separately, and I'm not too keen on doing that much surgery in my crawlspace unless it's absolutely necessary. I think I have two ways forward, both involving a differential bypass valve.
Option 1 looks like this - changes in green. I think that this is functionally identical to the diagram on page 35 of the manual, but I'm looking for some validation here.
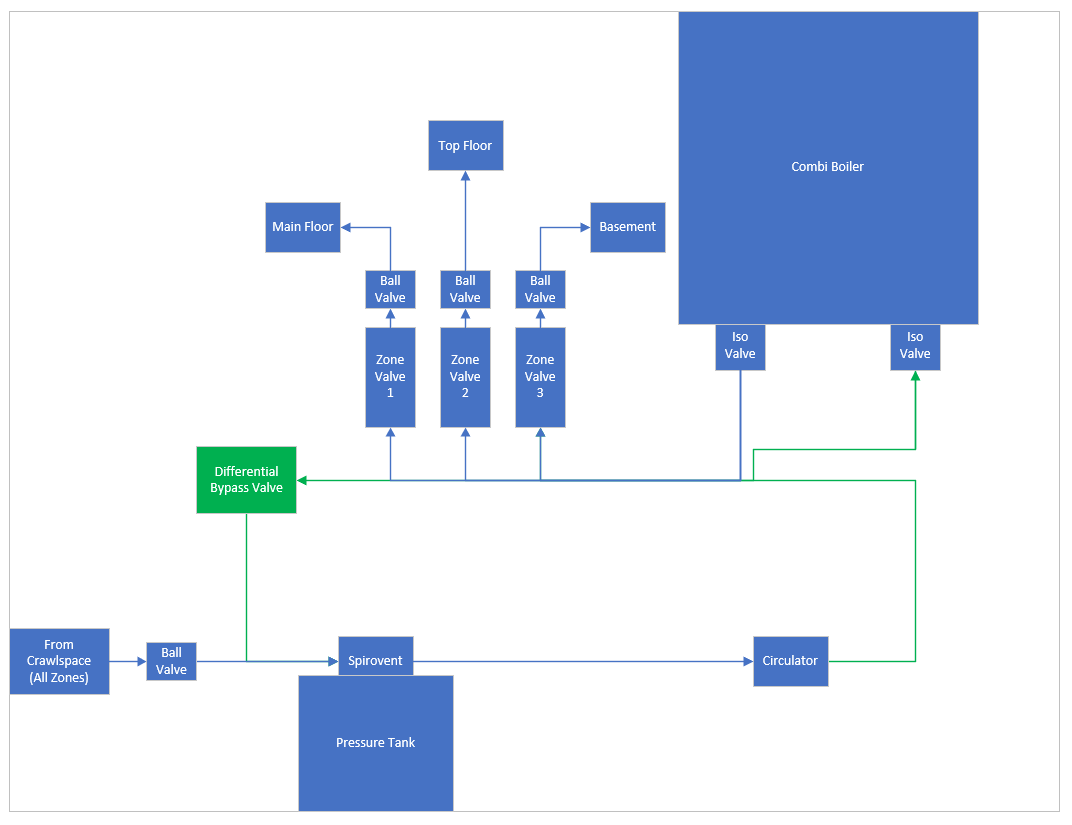
Option 2 would be simpler and maybe eliminate the need to have a second circulator consuming electricity all the time, but it feels like cheating. I think it would meet the system's need for always-available flow to the heat exchanger just as well as the close tee manifold Rheem sells for this boiler, but I'm don't think you can really call it primary/secondary. Looks like this:
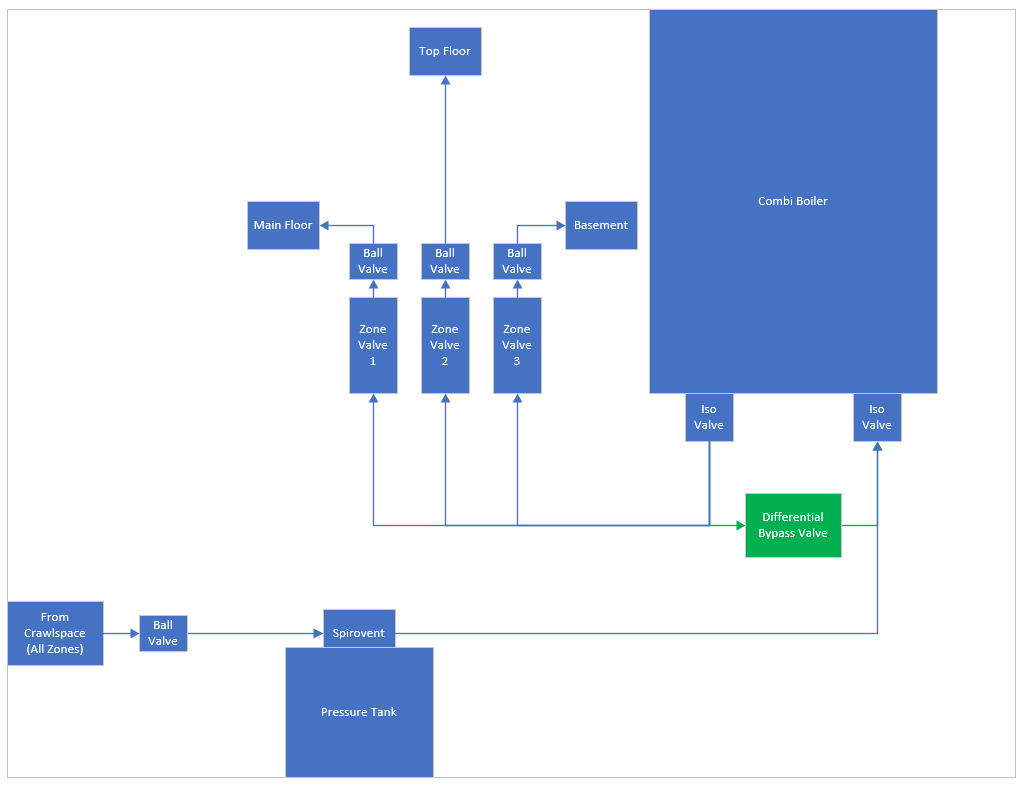
Question #1, if you've made it this far down: Is one of these options preferable to the other? Am I way off base and should do something else entirely? Perhaps I should be using a zone controller that will end the call for heat, but hold the valves open and continue circulating the water until it has cooled? That last option will send me back into research mode. I have never touched a zone controller.
Finally, a pic of the actual install. Please forgive the wiring I have yet to clean up. Outdoor reset isn't installed yet either, but it will be. The orange oxygen barrier PEX was supposed to save me time and money VS copper, but I suspect it did neither.

Any advice is much appreciated! I have a second question regarding a zone piping issue I suspect was introduced by a previous owner, but this post is already much too long. I'll make a separate one later
Comments
-
The primary secondary piping would not deadhead any of the circulators? Here are a few options for piping. No need for the PAB.
Any of these could be a single zone pump with valves. Instead of zone pumps.
I assume there is a circ inside the boiler? So the one you show becomes a zone circ. A delta P style ECM would be better yet for the system pump as it would modulate as zones open and close. They prevent over-pumping when a single zone calls.
With some careful planning and cutting you could salvage some of the current piping. Circ on the supply under the zone valves.
If you can, downfire the boiler closer to the actual heat load, if the 150,000 is too large?Bob "hot rod" Rohr
trainer for Caleffi NA
Living the hydronic dream0 -
I don't think P/S would deadhead anything? I'm not sure I understand what you are asking in the first sentence.
Yes, there is an internal circulator: a Grundfos UPS 15-78. I think it is "enough" pump to supply the zones, but with no minimum flow spec and no knowledge of the pipe network's flow restriction, it's a shot in the dark.
The problem I envision with your sketch is the same one I have now: The external pump is controlled by the boiler's computer, and the computer keeps the pumps on for about 5 minutes after there is no call for heat, regardless of how I configure the pump afterrun setting, so the pumps (both internal and external now, external only in your sketch) will be deadheaded for those five minutes every time the boiler shuts down.
Among your other diagrams, I think Figure 6-4 is the most appropriate for the situation, given that my zone returns come back all in one pipe. However, to use a single zone pump and valves, rather than individual zone pumps, would I not then need a PAB (this acronym is new to me, but I've gathered that it's a differential bypass valve. Please stop me if I'm wrong) to prevent deadhead when all zone valves are closed, but the pump still on? The manufacturers of these valves claim they should also be used to prevent over-pumping when one zone calls.
I will check for a setting to downfire the boiler, though the central heating capacity is only 120k, not 150k - 20% over the CI boiler replaced. With the water temp setpoint set appropriately, It has been modulating to stable output for very long heating cycles already (18ish hrs/day), so I'm not sure I would say there's a problem here.
0 -
Re-reading I see you mentioned the 5 minute post purge. See if you can adjust that down, or consider firing the heating pump from a relay box.
Really no reason to post purge if that heat cannot go into the system, so both circs need to run and a zone valve staying open. Your bypass valve is a good idea, I suppose it will dissipate some heat into the space going around that boiler loop for however many minutes.
I think the post purge is intended to keep the boiler temperature from creeping up after the burner shuts off, tripping a limit, and try to use that residual heat in the distribution.
Most mod cons run the fan for as period of time after a heat call ends, that also cools down the boiler.
The main use of a pressure activated bypass is to "flatten a pump curve" shed excessive delta P as valves close. It is a parasitic device. Here are some graphics to show how it attempts to work.
With todays smart pump, in delta P setting they just go into a no flow condition when all zones close, about a 7W draw. So they do continue to slowly spin, but not enough to cause problems against closed valves.
This type of circ just plug into a 120V circuit, no need to wire them through the boiler or remote relay. And they use 50% or less power across their operating range compared to PSC circulators.
It would be a nice upgrade for the post purge condition, and to save some electrical costs.Bob "hot rod" Rohr
trainer for Caleffi NA
Living the hydronic dream1 -
The only settings that I can reasonably interpret to determine the post purge length are here:
I have set all to 0, and also to 1 (my own field is controls engineering in an automotive context, and we sometimes interpret 0 as infinity for timers. So far that doesn't seem to be the case here). The result is that sometimes, the pumps shut down immediately, and sometimes they purge. I need to observe it for more cycles to be sure, but I suspect that it's related to recent burner activity for the reasons you mentioned. I have tried watching while allowing them to deadhead for the whole cycle, and the temp climbed from 160 to 175ish, at which point it started puking into a bucket from the pressure relief and I opened a zone. Running both circulators on high deadheaded against the closed valves pushes the boiler's internal pressure from 12 up to 28 PSI, all on their own.
I was lying awake last night and thinking about the delta P pump you had mentioned. I think you are right - if the manufacturers sanction running them deadheaded, it's the best way forward with the least moving parts to fail and will prevent me hacking up the piping more than necessary to boot. The pump I have in there now works fine, but is salvaged from the old system, of unknown age, and is probably most valuable to me in a spare parts box anyway.I'm looking around (mostly supply house, but also elsewhere) and finding lots of options for ΔT pumps, but none for ΔP. Is there different terminology I should be using? Do all the ΔT pumps have a ΔP mode that isn't well-advertised? Seems unlikely - I can't imagine those sensors being packaged in for free. Would you have a recommendation? Bonus points if it will mate up to the new flanges and gaskets I already bought for the Grundfos UPS 15-58, which will now be removed, but it's not critical.
I think what I need here is a Grundfos Alpha, which I think will bolt right into the existing flanges. Am I on the right track?
Is it important for a ΔP pump to have constant power to keep the controller up and running and maintain memory, or can I still wire it to the boiler's external pump terminal? I would prefer not to have it idling along all summer long while the boiler provides domestic hot water. Maybe I can rewire the outlet I installed for the boiler for split switched/constant.
New diagram for sanity-checking purposes:
I would really like to add a couple of temp/pressure gauges so I can see what the system is doing without digging through the boiler's menus, but I think I'm struggling to find fittings because I don't know what they're called. Are 1" copper sweat (or, less ideally, threaded) elbows, tees, and couplings made with 1/8' NPT ports in the side to add a gauge to? If I'm going to rework the zone valve assembly to add close tees I may as well make it the way I want it.
0 -
Here is some reading on the electronic circulators, how the various settings work.
https://www.caleffi.com/sites/default/files/coll_attach_file/idronics_16_na_0.pdf
Many installers buy the Alpha 2- 15-55 with the power cord, plug it in set to AutoAdapt and let it run. It goes to 5W in idle mode, so not much consumption during off season.
It is offered with a junction box also if you want to wire it to a relay, or for applications where condiut is needed. It really depends on the application and installer preference on wiring and control.
These constant run modes were originally designed for Euro systems where thermostatic radiator valves are the most common control, so there is not zone valve switch to call on the circ. The circ senses a valve opening and adjusts flow accordingly. A very simple efficient control strategy, non electric proportional temperature controls. So they stay powered all the time in those systems. Hydronically heated towel bars with TRV control are fairly common over in Europe also, so there could be a heat call year around.
I think you are correct in that the boiler sees excessive temperature and attempts to run one or both circs to dissipate that potential over-heat. Probably over-rides those time settings?
If the boiler has outdoor reset function try using that. It will prevent the boiler from running hotter then it needs to and may help that temperature overshoot, increase comfort by spreading out the boiler cycling, and possible some fuel savings.Bob "hot rod" Rohr
trainer for Caleffi NA
Living the hydronic dream0 -
Well that is a wealth of information, thank you - that's been saved for reference.
I had already moved on to exactly that pump since my last post, perfect. Unfortunately it seems the junction box version is backordered until the heat death of the universe, but I'm sure I will get by just fine with the power cord. 5W doesn't bother me, I doubt the pump longevity cares much about running twice as many days per year, and these are not catastrophically expensive or disruptive parts to replace. I now also see in the documentation that there is a manual summer mode which runs the pump for only two minutes per day to avoid scale build-up. Really should have researched these sooner.
It's interesting you should mention heated towel bars, as one of the reasons for this project is to open up some space for an eventual walk-out basement master suite, and I've always wanted one of those. In the Euro-style systems, what triggers the boiler to provide heat when the TRV is opened?0 -
In a word, "stubbornness". This project was actually kicked off in the spring. In the lead up, before anything was bought, I spent a lot of time reading about options. Here and elsewhere, I read that mod cons usually require primary/secondary, but I could find nothing in this one's documentation saying one way or the other (it was there, I just missed it. To this day I don't know how because it wasn't exactly hidden).
There was then a series of delays to repair moisture ingress issues discovered at the chosen installation spot before burying it in plumbing, due to some deaths in the family, and due to those delays putting me into conflicts with other scheduled tasks. When I got back to it I reread the manual and found the note, but I was far enough along and stressed enough about changing my plan that I rationalized until I was convinced it would work. I'm paying the price for that now, but it's nothing more than a little money and a little more time. A more than fair cost to learn something new and have complete familiarity with the systems in my home.
No balancing valves because the original system didn't have them. I could add them, but that strikes me as a solution in search of a problem.If you had read the rest of the thread, I think you would have seen I'm well on my way to what you've described.
Edit: This was somewhat combative and there's no need for it here. I do think I'm on the way to having this done right, with many thanks owed to those here.1 -
Enginerd said:
Well that is a wealth of information, thank you - that's been saved for reference.
I had already moved on to exactly that pump since my last post, perfect. Unfortunately it seems the junction box version is backordered until the heat death of the universe, but I'm sure I will get by just fine with the power cord. 5W doesn't bother me, I doubt the pump longevity cares much about running twice as many days per year, and these are not catastrophically expensive or disruptive parts to replace. I now also see in the documentation that there is a manual summer mode which runs the pump for only two minutes per day to avoid scale build-up. Really should have researched these sooner.
It's interesting you should mention heated towel bars, as one of the reasons for this project is to open up some space for an eventual walk-out basement master suite, and I've always wanted one of those. In the Euro-style systems, what triggers the boiler to provide heat when the TRV is opened?
Another wiring option if you do want to control the heat pump from a relay in the boiler is place a switched receptacle in a handy box and plug it in.
Keeping it powered 24/7 lets you use all the features like that exercise function.
To fire the boiler for any load, even summer loads, a few options. A flow switch in the piping that detects when the circ starts moving fluid, or an induction relay that senses current draw and closes a contact.
For a single room towel bar, consider electric, with the optional timer/ setback type control on it.
A hydronic towel bar is a very small load and will short cycle the boiler even with that 18,000 turndown
Bob "hot rod" Rohr
trainer for Caleffi NA
Living the hydronic dream0 -
Finally wrapped up! Was trying to wait for supply house to send the last valve (they threw the wrong one in my last order by mistake), but I got impatient and finished it up last night. Naturally, the valve showed up this morning
. The accident waiting to happen on the bottom right is my temporary work around until the one with male hose threads and a cap goes in:
One day, I'll have pretty copper sweat joints like the pipe fitters do, but that day is not today. Little tight but nothing a street elbow couldn't fix. I never would have guessed that I would start this project wishing I could do everything with PEX, and end it with a preference for soldering and cursing my PEX crimper for flaring up my shoulder injuries.
I want to reiterate my thanks: for the replies here, and the old posts elsewhere I've been reading though in archived threads - they're mostly from the same people... especially you, hot_rod.
A few final notes that may be of use to searchers:
1. The system purges more easily now - With a little patience I was able to get the air out without dragging the hose out for a real purge - just by filling and circulating. It's surely getting more flow now that the main system flow doesn't need to go through the heat exchanger. Surprisingly, the pressure in the boiler when operating still settles in around 22-28PSI (using default fill pressure of 12 PSI). I had thought it would be less now. Wonder what one would do if they needed to feed a much taller building?
2. When all the zone valves are closed and the pump in Auto Adapt mode, the Grundfos Alpha2 throttles back to around 10W, while indicating 0-1 GPM flow. I do not think any of the zone valves are leaking, but they are repurposed from the old installation and therefore suspect (maybe another bad idea I'll have to pay for, but at the beginning I was less confident I could build such a thing). 10W is no big deal and the pump is close enough to silent as to make no difference, but it's worth noting that in the constant speed & constant pressure modes, it does NOT throttle back when the zone valves close. Not sure if that would cause a long term problem or not, but I'd rather not risk it & I'll be adding a prominent label to the pump never leave it in those modes. Grundfos does not seem to directly address using the pump this way, even in auto adapt mode. If it dies, I'll dig this post up and update it.
3. So far, auto adapt is feeding my one weird zone with a subloop and no balancing valve a bit less /pressure flow than it really needs for the subloop to come up to temp. I'm going to give it some time to see if it does indeed adapt or if more air just needs to work it's way out. Very curious how the adaptation strategy works, at the controls level, but I think they're not likely to share that info.
4. I hope there are now enough keywords in this thread that anyone considering doing what I initially did finds it. DON'T DO IT! There were reasons beyond those listed in the manual to use P/S piping!0 -
Hmm. I had thought that the Auto mode (I have an Alpha2) was for a single zone scenario, and it optimizes for that. If you have one, two, three, or "none" zones open, does the Auto strategy not just keep changing all over the place (ie, never "learning") ?
30+ yrs in telecom outside plant.
Currently in building maintenance.0 -
Auto adapt is mainly for zoned systems. Originally designed with TRV systems, common across the pond. Those TRV are constantly changing flow rate based on the thermostatic element. Unlike on/ off zone valves commonly used in US systems.Dave Carpentier said:Hmm. I had thought that the Auto mode (I have an Alpha2) was for a single zone scenario, and it optimizes for that. If you have one, two, three, or "none" zones open, does the Auto strategy not just keep changing all over the place (ie, never "learning") ?
Mark does a good job explaining here.
https://video.search.yahoo.com/yhs/search;_ylt=AwrVrN5Nu5Rju0oAGgAPxQt.;_ylu=Y29sbwNncTEEcG9zAzEEdnRpZAMEc2VjA3Nj?p=grundfos+alpha+auto+adapt+youtube+videos&ei=UTF-8&type=q3000_A1BWP_set_bcrq&hsimp=yhs-st_mig&hspart=ima&fr=yhs-ima-st_mig#id=11&vid=bbbd2b27818a2d961a4103e72b7b8252&action=viewBob "hot rod" Rohr
trainer for Caleffi NA
Living the hydronic dream1 -
Thanks hotrod. So from that vid and some others on Grundfos's site, it seems that the auto learning is over the course of a few days. Its not clear if it saves that system profile in the event of a power outage, or if it has to relearn.
I will try it again. Last time, the beginning profile (middle of the auto-range) was insufficient heat.
Edit - duh when I realized of course it wont drop its learning on a power outage. We turn the power on and off to control these circs. It might have to relearn after a long summer off, but should be fine during the heating season.
30+ yrs in telecom outside plant.
Currently in building maintenance.0 -
My opinion is to leave that type of circulator plugged in. They were originally available with only power cords. Now you can get corded or junction box options
Some models have a summer exercise function, which needs power, of course. The idle draw is probably only 5-7 W.
Not everyone agrees that auto adapt is the best option. If you use thermostat setback, or turn down a vacation property, the learning curve needs to re adjust. Try the different options to see what works best for your application.
The biggest wins are modulating to various zone needs, the lower power consumption, and being DC motors, they have better torque, which can be handy if you have scaling issues from hard fill water, or some magnetite makes its way into the rotor can.Bob "hot rod" Rohr
trainer for Caleffi NA
Living the hydronic dream0 -
It seems to be learning... something. It's settled in to provide 3-ish (indicated) GPM per active zone. Takes a minute or so to adapt to a change in zone valve status (or maybe the display is filtered). Over the first few days, it seemed to learn to use a bit less power in any given condition for only slightly less flow - I get the impression that it is searching for a knee in the power-flow relationship and trying to park on it. No pressure- or flow-sensing hardware that I noticed when rotating the powerhead to horizontal, so it must all be based on impeller drag.
I actually went as far as running a patent search to see if the control method was disclosed, but found nothing in the first 10 minutes of looking. Grundfos's marketing materials don't say much - just a lot of "Finds the best settings!" and "Perfectly matched to your system!"
Ironically, now that the system is primary/secondary, sometimes the boiler short cycles! I think that with only one zone open and auto adapt mode on, the boiler's flow is greater than the system's, so it's feeding back into to itself, reducing the ΔT it "sees" and is unable to modulate low enough to stop overshooting the setpoint. Unless it adapts up to a higher flow with one zone open, I may have to run in constant pressure mode and interlock the pump... or just live with it sometimes cycling.
I've come up with one more question that maybe deserves it's own topic, but I'll not clutter up the front page unless someone tells me to make a new thread:
Do modcon boilers use the fan to provide extra combustion air for the purpose of diluting the exhaust gas to hit a target exhaust gas temperature? If so, this will lower the dew point of the exhaust gas and reduce efficiency, correct?
I'm currently vented though PVC, which the boiler manufacturer endorses, however there is a configuration setting to tell the unit whether the vent is PVC or CPVC. The manual states that with CPVC, higher exhaust temperatures will be allowed, but nothing about why that would or would not be desirable. I've noticed that the exhaust gas temp seems to always be close to the limit, and the max exhaust temp (150F) is lower than the max water temp (180F), so I suspect there's dilution air and I'm leaving efficiency on the table. It does not seem that 3" CPVC is available anywhere, but I can try to track some down, or maybe look for polypropylene pipe, though I've never seen it in any size. It's a very short vent and would be easy to swap.0 -
I think there has been a learning curve, probably on going with pressure controlled circulators. I would not bet the farm on the gpm readout, I have seen them all over the map when compared to a certified, accurate, lab quality flowmeter. I think it is calculated on rpm maybe? I'm not sure how it compensates for glycol at different % and temperatures?
Mod cons have negative pressure gas valves, so they ramp that fan speed up and down to increase and decrease the burner output.
Some brands and models have lamba sensors and can adjust the combustion also.
https://www.viessmann-us.com/en/products/vitodens/vitodens-200-b2ha.html
Flue gas should run a bit higher then the operating temperature of the boiler water. And yes PVC as a vent material has been very controversial. I believe Ipex is the only manufacturer of a listed vent CPVC product. PP and stainless are other options, listed for flue gas applications. Plenty of mod cons that run 180 constantly with discolored, browned, PVC vents
At some point if you have consistent micro loads, below the lowest turndown, expect the boiler to cycle.
There is no definition of what a "short cycle" is. Many suggest a minimum 10 minute run time. The control may have functions to lessen short cycles, a time function, step firing. limiting settings for example. For me it is the sound of a boiler on/ off multiple times an hour that drives me crazy, whether it is designed for that or not. I've added buffer tanks to many of my mod con installs.
Bob "hot rod" Rohr
trainer for Caleffi NA
Living the hydronic dream0 -
The cycle length with one zone on (now, with a 145F temperature setpoint and 35F outside) is much longer than 10 minutes - I probably shouldn't say "short cycle" but the output temp gradually climbs above the target until it hits the +10F cutoff, then shuts off the burner until the temperature drops to the -30F cut-on. With the current weather's low 145F setpoint, this makes the cut-on temperature 115F, and that can take a long time, since the baseboards more-or-less stop emitting at 125ish. It's captured my attention because before, the boiler was very good at modulating to hold temp. Now, if I change the pump to the medium constant pressure mode, flow through that zone increases to an indicated 4 GPM and the temperatures stabilize.
The good news is the cut-on, cut-off, and internal pump after-run times are all calibratable, so I should be able to get to an acceptable solution. I already changed the cut-on threshold to -25F to see how well that works. Wish it could be a curve to match the reset temp. There is an "interval time" setting cryptically explained as "This function is to set up the Interval Time in Heating Mode to prevent inconsistency of heating. If the selected time passes and the Combi Boiler’s inside temperature drops, this function will automatically reignite the burner in the Combi Boiler." Reads to me like it's meant to address this type of situation, but it seems to do nothing. By default it's set to 3 minutes.0
Categories
- All Categories
- 87.1K THE MAIN WALL
- 3.2K A-C, Heat Pumps & Refrigeration
- 58 Biomass
- 427 Carbon Monoxide Awareness
- 113 Chimneys & Flues
- 2.1K Domestic Hot Water
- 5.7K Gas Heating
- 110 Geothermal
- 161 Indoor-Air Quality
- 3.6K Oil Heating
- 70 Pipe Deterioration
- 996 Plumbing
- 6.3K Radiant Heating
- 391 Solar
- 15.4K Strictly Steam
- 3.4K Thermostats and Controls
- 55 Water Quality
- 44 Industry Classes
- 48 Job Opportunities
- 18 Recall Announcements