Welcome! Here are the website rules, as well as some tips for using this forum.
Need to contact us? Visit https://heatinghelp.com/contact-us/.
Click here to Find a Contractor in your area.
Oil Nozzles and burners.
Options
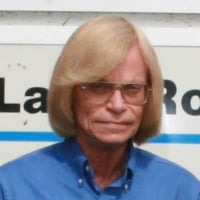
captainco
Member Posts: 817
in Oil Heating
Just for discussion and possible learning I am attaching technical information I assembled for oil combustion class. This part discusses nozzles only. I am looking for a good discussion on this. Agree or disagree we can all learn. I just want us to provide our or your customers the best HVAC service available, based on modern day testing. Maybe later we can get into Carbon Monoxide diagnostics on oil burners. Let's see how this one goes. I have no problem being called nuts!!
2
Comments
-
I agree 100% with the information in the attachment.
There are so many variables in combustion and techs get tunnel vision want to know EXACTLY how to set a certain burner and EXACTLY what combustion #s to expect.
It's all hogwash.
What works in one burner or boiler may not work in an identical unit. No two installations are the same. Even two identical boilers installed in the same boiler room may not perform the same.
My method was to try the manufacturers settings. If they did not work well or at all you throw them away and start testing and make it work and change what you have to change.
I have seen plenty of new equipment that wouldn't work with the mfg. settings
Combustion #s are a "safe range" to be in. Not an exact science.
Fuel and fuel temperature changes
draft changes
combustion air temp changes
Boiler and furnace combustion chamber temp changes
And as a result combustion and combustion #s change2 -
Not a bad start. But there's a lot more to this. CO is definitely part of today's testing protocol, but with oil it usually (but not always) is accompanied by smoke. What you did was what we call a "nozzle substitution test", standard practice for decades.
I was lucky to be able to do some of George " @Firedragon " Lanthier's classes, which were real eye-openers. I'm sure he's forgotten more about oilheat than I'll ever know. George is based in Massachusetts, and still does training but I would not be surprised if he's considering retirement.
@Alan R. Mercurio is another good oilheat trainer. He's in Pennsylvania, so might be closer to your home base in Ohio.
I think of these guys every time I go back to one of our oil customers and there's hardly any brushing or vacuuming to do, and the burner tunes up perfectly.All Steamed Up, Inc.
Towson, MD, USA
Steam, Vapor & Hot-Water Heating Specialists
Oil & Gas Burner Service
Consulting1 -
Great stuff Jim. I also agree with everything written.
Long before OEM spec guides, in the land of retrofit burners, the nozzle substitution test was the right way to determine the best nozzle and set up. Most techs aren’t given the time to do it, or may not have the knowledge or patience to do it. Especially if they work for a company that expects a tech to clean/tune 8 pieces of equipment a day.
A better tech spends all that time cleaning a boiler/furnace, and PM's the burner, then basically blows it not knowing how to set up the burner.
Another thing techs may not understand or utilize, is how adjusting the head (Riello, Beckett NX, or Carlin), or slightly tweaking the Z dimension on an AFG/AF, can greatly improve combustion. Along that train of thought, how about even checking the z dimension?
Another thing to improve combustion-pre & post purge, and better oil filtration.
And what happened to oil line/nozzle heaters that Carlin introduced? They were all the rage-for like a minute.
There was an error rendering this rich post.
0 -
George and Alan are two of the best I have read. I don't believe that either did the kind of CO studies and tests I have done on oil. Most oil burners that I have tested that make the most CO have little or no smoke. When the smoke is between #4 and #6 there is rarely any measurable CO. Above and below that you don't know what to expect. CO on oil is mostly some type of impingement or afterdrip. Underfiring oil is when I have seen the most CO at Zero smoke, I have 15 different CO patterns for oil burners, measuring the CO spike when they Light, the CO during the Run Cycle(3 readings) and CO spike when they Shutdown. Back in the 90's I wrote an article in Fuel Oil News, but back then I only had 12 patterns. I also submitted my finding to Tom Butchard at Brookhaven Labs. Right now i just want techs to know a little more about nozzle performance.2
-
The thing with nozzles is you sometimes get results you don't expect. We had a burner once that was building carbon on the chamber floor (old coal conversion)
Normally you would look at raising the burner, reducing the firing rate or a narrower spray angle.
None of this worked
I had Carlin come out to this job and he fixed it by putting in a wider spray angle.
Why? The new nozzle fit the air pattern in that boiler with that burner better,
But that burner had run a few years with no carbon so it was probably a difference in fuel that started the issue.1 -
I am not going to get into this discussion since I rarely worked on or serviced oil burner units with firing rates below 10 GPH. Any time I was involved with smaller commercial installations utilizing pressure atomization of the oil, I would recommend replacing the standard 100 psi oil pump with a 300 psi pump and down sizing the nozzle accordingly. This would usually allow the unit to get a much better atomization of the oil and better performance. It also allowed for 2 stage firing on some units keeping the burner from cycling off, especially on units that experienced pilot problems or lighting problems. We serviced a lot of very old "antiquated" units.0
-
@retiredguy
That was a common way to try and make an older burner burn better. Boost the oil pressure and downsize the nozzle. Smaller droplets of oil mix with air better
Took a lot of burner manufactures years to catch onto that trick. Iron Fireman was doing that in the late 50s with their Whirlpower burners running up to 300# at the nozzle when no one else was1 -
Categories
- All Categories
- 87.1K THE MAIN WALL
- 3.2K A-C, Heat Pumps & Refrigeration
- 58 Biomass
- 427 Carbon Monoxide Awareness
- 113 Chimneys & Flues
- 2.1K Domestic Hot Water
- 5.7K Gas Heating
- 110 Geothermal
- 161 Indoor-Air Quality
- 3.6K Oil Heating
- 70 Pipe Deterioration
- 998 Plumbing
- 6.3K Radiant Heating
- 391 Solar
- 15.4K Strictly Steam
- 3.4K Thermostats and Controls
- 55 Water Quality
- 44 Industry Classes
- 48 Job Opportunities
- 18 Recall Announcements