Welcome! Here are the website rules, as well as some tips for using this forum.
Need to contact us? Visit https://heatinghelp.com/contact-us/.
Click here to Find a Contractor in your area.
Air purge, stumped
Options

northlakes
Member Posts: 95
in Gas Heating
Trying to fill a hydronic system after replacing a number of sections of fin tube. I’ve read threads and watched YT vids on how to purge but none seem to have the boiler/hydronic configuration I do: Three floors with one zone each, zone valves and one system circ. No shutoffs or drains in the return legs. Only drains I can find are at each boiler, one in the bottom of an air scoop (which doesn’t do anything but a drip when I open it) and one drain at the end of one of the lowest baseboards in the system, about 10 ft upstream from where the returns converge.
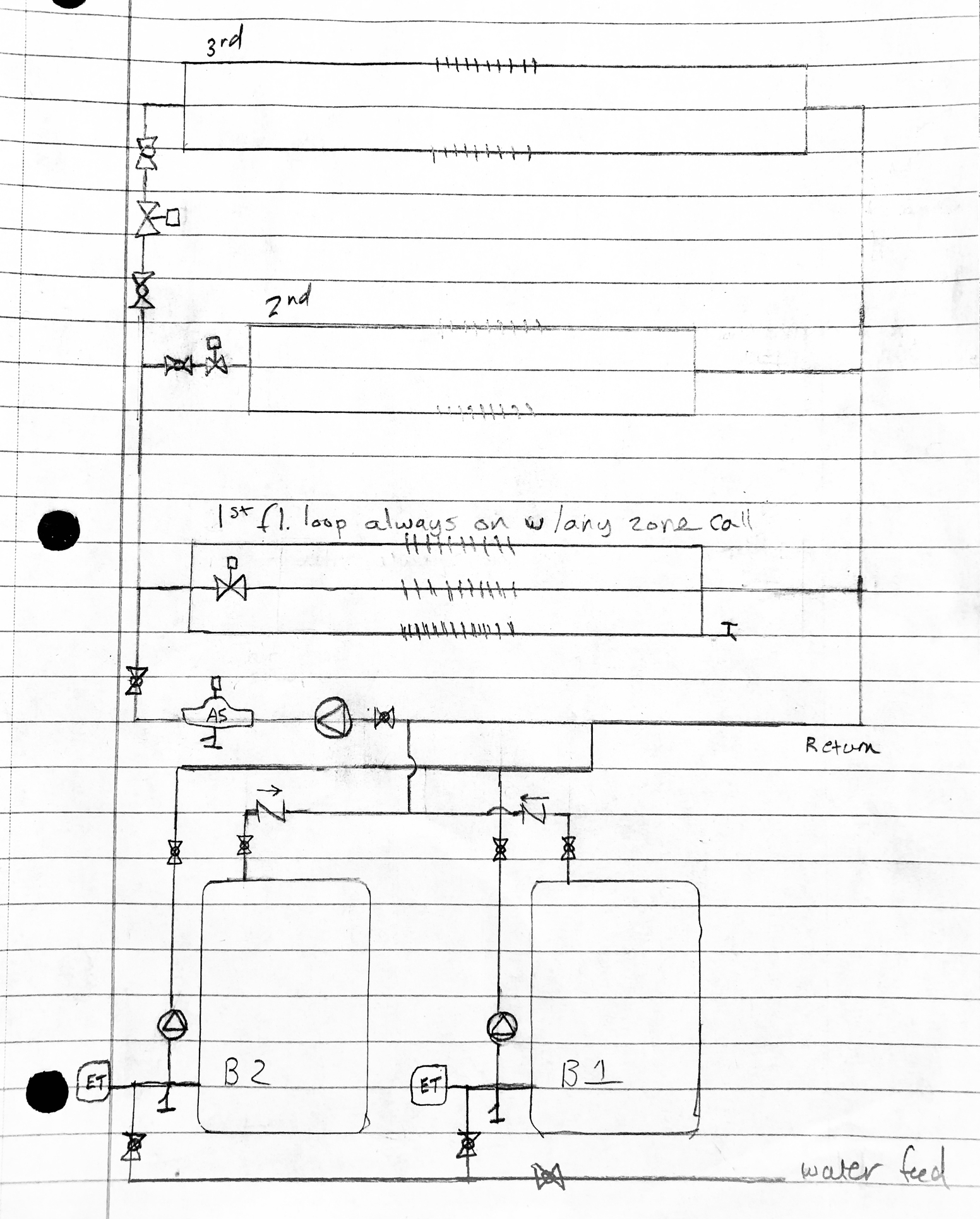
I have some bleeders in various locations in the system and three on top floor, but it seems maybe not at the highest point of the loop on that floor. I’ve tried filling and purging the system using the bleeders but they squirt water and it seems like I’ve still got an airlock somewhere, as when I fire it the heat travels far more slowly than I’d expect through pipes in all zones, and half the loop on top floor won’t heat at all. Circ is louder than I’d expect so it seems there is air. I hear trickling sounds sometimes but not always. Opened zone valves both manually and with thermostats, (just in case one isn’t opening?) but with no change.
The way each floor loop has a tee at supply and return makes me think I can’t really force air out where I suspect it’s stuck (assume the water can just divert around the other leg of the loop?) is there a way to purge air in this system without cutting into it?
Drawing is a bit clumsy but maybe it helps.
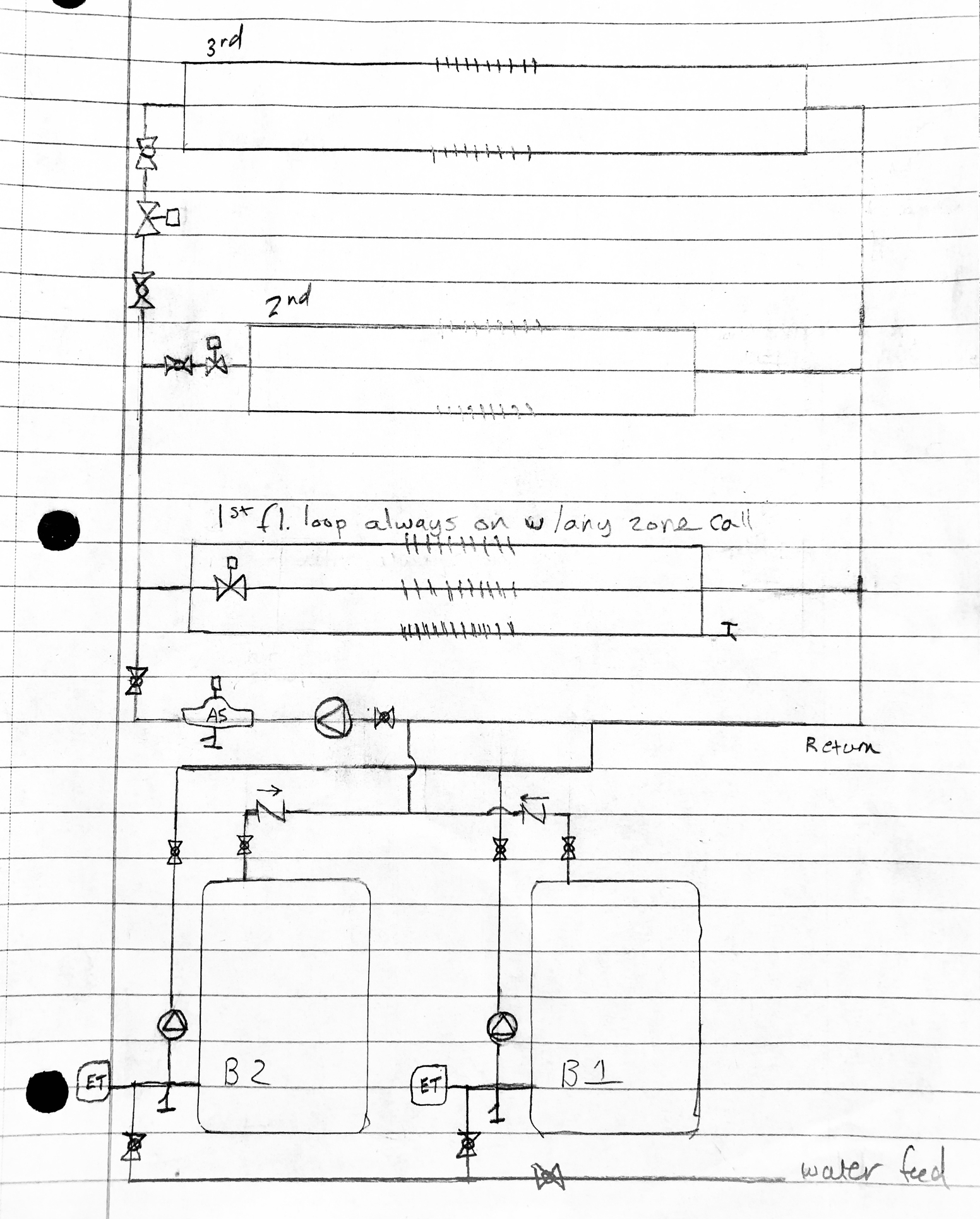
0
Comments
-
You should be able to close the valve just to the right of the system circ and air scoop and open the drain under the air scoop to purge, assuming there are no check valves not pictured. It would be flowing backwards through the radiation, but should push the majority of the air back down to the air scoop drain with enough pressure/velocity. Side note, I think your boiler circs are in backwards and if the expansion tank is connected under the scoop like most are, it's not exactly ideal and isn't helping your air issue. Also, why is the 1st floor zone always open?0
-
@GroundUp you’re correct my drawing has the boiler circs in backwards! Thank you. I’m used to seeing an expansion tank under the air scoop but a drain is connected instead. When I open it nothing comes out. Not sure if that’s an expected behavior but there is water in the scoop, I can manually release the vent up top.My best guess on why 1st floor zone valve was removed is to prevent freezing, it’s a perimeter run. (Does seem to have been done for a reason by previous owner.)0
-
-
@mattmia2 thank you, makes sense. Will give it a look.0
-
I would do as @GroundUp and @mattmia2 suggest. And are you disabling the regulator during the purge for maximum water flow ? If the regulator is too restrictive to create enough purge water flow maybe another DCW hose as a water input to a boiler drain. Also when you repair the plugged air scoop drain maybe replace the valve with a full port valve with a garden hose fitting (or adapter) for best water flow to carry the air down and out of the system. I would open up the air scoop vent when purging out the air scoop drain.
Also is the system pressure sufficient for a 3 story building during heating ?
National - U.S. Gas Boiler 45+ Years Old
Steam 300 SQ. FT. - EDR 347
One Pipe System0 -
@109A_5 I believe what I have is automatic fill valves integrated with expansion tank so I’m not sure the pressure there can be controlled,But once I get that air scoop drain open I can hook onto this boiler drain with a hose. Is there ever “too much” pressure from adding water like that? Should I keep the boilers out of that loop somehow, close supply shutoffs?
Confused how these tee’d loops can be purged if there’s no way to close one side of a loop. Is that a matter of enough pressure/velocity to equalize through both sides of the loop?Previous owner said they were able to heat top floor with the system, but I don’t know for sure yet I haven’t had it fully running yet. It may be unclear from this drawing that this is essentially a two-story with a basement storefront (building is backed into a hill)0 -
Follow that pipe that goes in to the tee with the expansion tank on it. There should be a pressure reducing valve(prv) that connects in to the domestic cold water somewhere. It likely will have a fast fill lever on it that will let you defeat the pressure regulator and allow as much flow as is available in.
When you pressurize the system manually with the fast fill lever or a separate hose you have to watch the pressure in the system so that it doesn't open the relief valve.
EDIT: It is possible that you don't have a PRV and the pressure is set manually by opening a manual valve until the system reaches the desired pressure.0 -
The system has too many problems.
That is the fill valve there at the x-tank and you will never get it to work properly. Drain the system, replace the fill valve, add a bypass for proper purging and install a proper purge assembly for easy purging now and in the future.
A new microbubble air eliminator, pump isolation valves, pressure and temperature gauges, etc. if you really want to get into it.8.33 lbs./gal. x 60 min./hr. x 20°ΔT = 10,000 BTU's/hour
Two btu per sq ft for degree difference for a slab1 -
Almost guaranteed that boiler drain under the scoop is plugged with yuck. I can often open them up with a piece of stiff wire or welding rod- once you get a hole through the gunk, it'll clear out fast. You need 1 psi of pressure to raise the water 27.72 inches, so in theory, if your highest radiation is 15 feet above the pressure gauge, you need 6.5 psi cold fill pressure to lift it there. I like to keep 3-5 psi above and beyond that number to maintain positive pressure in the event of a leak, cooldown, etc. Assuming your relief valves are 30 psi, you don't want to exceed about 25 psi during the purge or ever.
In conclusion, if you can get that drain under the scoop opened up, you should still be able to purge backwards as I mentioned above. If your PRV doesn't allow, you can probably hook up a hose to the lower boiler drain under the boiler circ(s) and do it that way. It really should not be that difficult with what you have drawn, these systems are not complex. While there are definitely better options for XT placement, scoop/circ relationship, purge valves, etc, this can be done without changing anything. Obviously it worked for the last 30+ years judging by the looks of the equipment, you shouldn't need to change a thing to get it going.0 -
Often when you flow backwards through a bib style valve you blow the washer off the screw. Then they do not seal tight anymore, it’s a one direction valve.
I’d drain he pressure off and put ball valves in both those places.With the pressure off you can do a flying connection switch, if you prepare properly🤓Bob "hot rod" Rohr
trainer for Caleffi NA
Living the hydronic dream0 -
@hot_rod saw this a bit too late, maybe I fouled the drains. If they don’t seal right, maybe I can replace them.@GroundUp thanks I was able to purge the top floor and get it to flow with no bubbles after about 15 minutes and many, many gallons. Lots of big burps and eventually sounded pretty good when I was done, a lot quieter, with only faint sounds.Then when I fired it up hot it was like I didn’t purge at all, sloshing all over the place, but top floor didn’t have airlock anymore. I tried pushing water up through scoop drain (forward through radiation this time) and out the boilers’ drains, alternating shutting supply and return thinking maybe air was hiding somewhere in the boiler loops. Still sloshed.I probably need to calculate if I’ve got enough pressure to keep that top floor happy but I think previous owner said it was working. As far as I know there isn’t a way to increase the pressure since it has these automatic regulator valves on the expansion tanks. Going to try again when I get the wiring issue sorted (another thread.)
Is this period of time with air in the system causing any damage? Feels like I’m probably a couple days away from the parts I need.0 -
What you have there is a fill-trol expansion tank setup. You will never be able to purge the system with one of these. What I usually do is connect the boiler to a water heater or some other hose connection that will deliver higher pressure water through the zones. Just keep the pressure under 30 PSI so the relief valve remains closed. Make sure to install a new air vent on the air scoop first or else you will end up with an air bound system again in no time.
Obviously the best thing to do is to ditch the fill-trol and install a pressure reducing valve and #30 expansion tank, but the procedure above will get you going.0 -
@SuperTech I’m going to replace the vents at scoop and boiler and try it again. I don’t know how I’d raise the pressure any more than I diid via adding water from another hose, in this case of course the fill-trol valve shuts down as soon as that other water is flowing in. Is it useful to restrict outflow drain valve during purge to increase pressure, or does that just reduce the velocity needed to get air moving through.I’m assuming when it’s done purging the order of closing valves with flow from return to supply is external water source -> boiler drain -> air scoop drain.
Once I open the valve behind the air scoop and circ, does circulating the whole system cold have any purpose, or does it need to be hot to tell if it worked? I’m guessing I had some air hiding in the boiler loops or accidentally introduced some via hose or vents last time, as it was flowing dead quiet on top floor at end of purge.0 -
circulating cold will bring some of the air to the air scoop or the boiler but you may need the heating at the boiler to drive the dissolved air out and the cooling in the system to dissolve more of the air pockets to bring some of the air back to the boiler. Air removal at the boiler is a lot more effective with the circulators pumping away from the boiler and a microbubble type air separator between the boiler and the circulator.1
-
Hello @northlakes,
Since you had the system open to replace things. And the present purge attempts and methods are problematic. I wondering if you find the high spot on the 3rd floor and add a vertical pipe above the high spot to collect the air and have a drain valve at the top of the added vertical pipe would make things much simpler for future maintenance.
National - U.S. Gas Boiler 45+ Years Old
Steam 300 SQ. FT. - EDR 347
One Pipe System0 -
@109A_5 @mattmia2I definitely need to consider some alterations while things are being replaced for an easier purge next time. These seem like great suggestions but admit I’m not so familiar with how to set up a micro bubble and my boiler circs do pump down through returns, the system circ is just a short distance ahead of boiler loops.0
-
UPDATE: went through what I thought was a logical purge sequence (following advice here) twice, was able to get all zones sounding very quiet, but upon firing and circulating it seems like no matter what I try, some air is hiding and it gets to sloshing again. I decided to let it run a bit and it seems with some time running and heating it works a good deal of the air out. I did replace three vents, one at boiler, air scoop and one at a tee on top floor. Still some faint air noise/trickle. MUCH better than when it first started circulating but after all that work admit I wish I could get it dead silent.1
-
Sounds like you might not be purging through a section of the piping. It should be completely silent after a good purge and a days worth of hot circulation.Bob "hot rod" Rohr
trainer for Caleffi NA
Living the hydronic dream0
Categories
- All Categories
- 87K THE MAIN WALL
- 3.2K A-C, Heat Pumps & Refrigeration
- 58 Biomass
- 427 Carbon Monoxide Awareness
- 113 Chimneys & Flues
- 2.1K Domestic Hot Water
- 5.7K Gas Heating
- 109 Geothermal
- 161 Indoor-Air Quality
- 3.6K Oil Heating
- 70 Pipe Deterioration
- 995 Plumbing
- 6.3K Radiant Heating
- 391 Solar
- 15.4K Strictly Steam
- 3.4K Thermostats and Controls
- 55 Water Quality
- 44 Industry Classes
- 48 Job Opportunities
- 18 Recall Announcements