Welcome! Here are the website rules, as well as some tips for using this forum.
Need to contact us? Visit https://heatinghelp.com/contact-us/.
Click here to Find a Contractor in your area.
Peerless Purefire PF-210 Lockout A01 Error
Options

D818
Member Posts: 19
in Gas Heating
Hello everyone - New to the forum and new to homeownership. We just moved into our first home a little over a week ago and have been having issues with our boiler from the start. Keep getting an A01 Ignition/lockout error, with an occasional A02 flame failure.
It was never completely out, just very inconsistent. The reset button used to typically fix the issue when the error would pop up. Had a technician look at it Tuesday, didn't fix it. Came back next day, and couldn't fix but said they may need some new parts and will give me an estimate the next day. I didn't have a good feeling they knew precisely what to do or that their work would be reasonably priced based on experience up until this point.
I researched the error and found the flame sensor and ignitor were common problems so i ordered the parts for $150 and had them overnighted. At this point the reset button is no longer fixing the issue and furnace has been off for over 24 hours. I received the parts Friday evening at 8pm. I changed the sensor and it fired back up. Great. Went to sleep and go the lockout error at some point overnight. I replaced the ignitor at 5am and it fired back up again and saturday it ran pretty much all day but went back out some time overnight into Sunday and wouldn't start back up . Heat has been off all day/night since, I took out sensor and ignitor earlier today, dusted off, and nothing. Left it alone and it just came back on about an hour ago and we're getting heat.
Elansp had a very similar problem but I just don't know how to get a technician that is familiar with this solution or specializes in peerless pf systems: https://forum.heatinghelp.com/discussion/comment/1684849
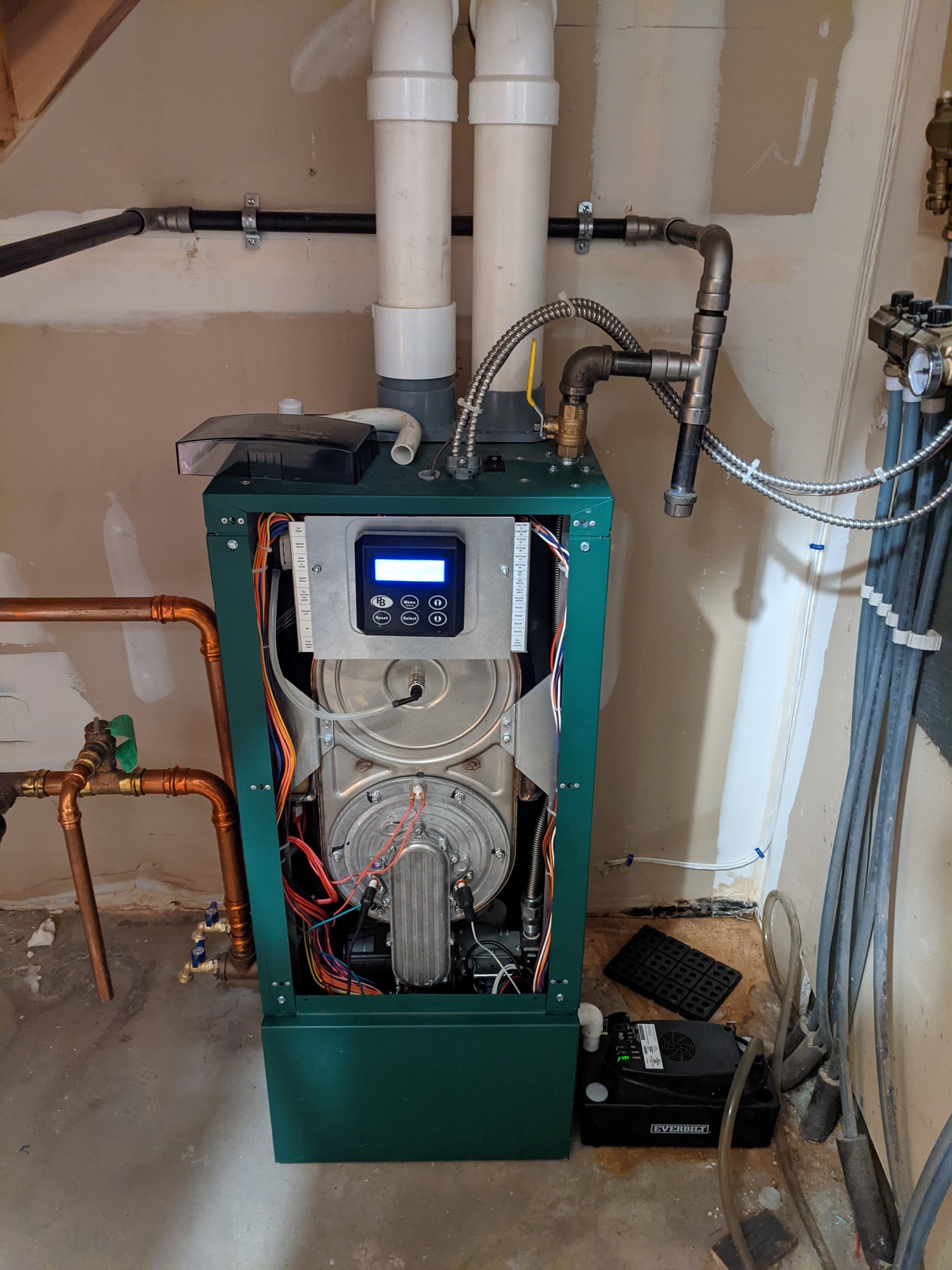
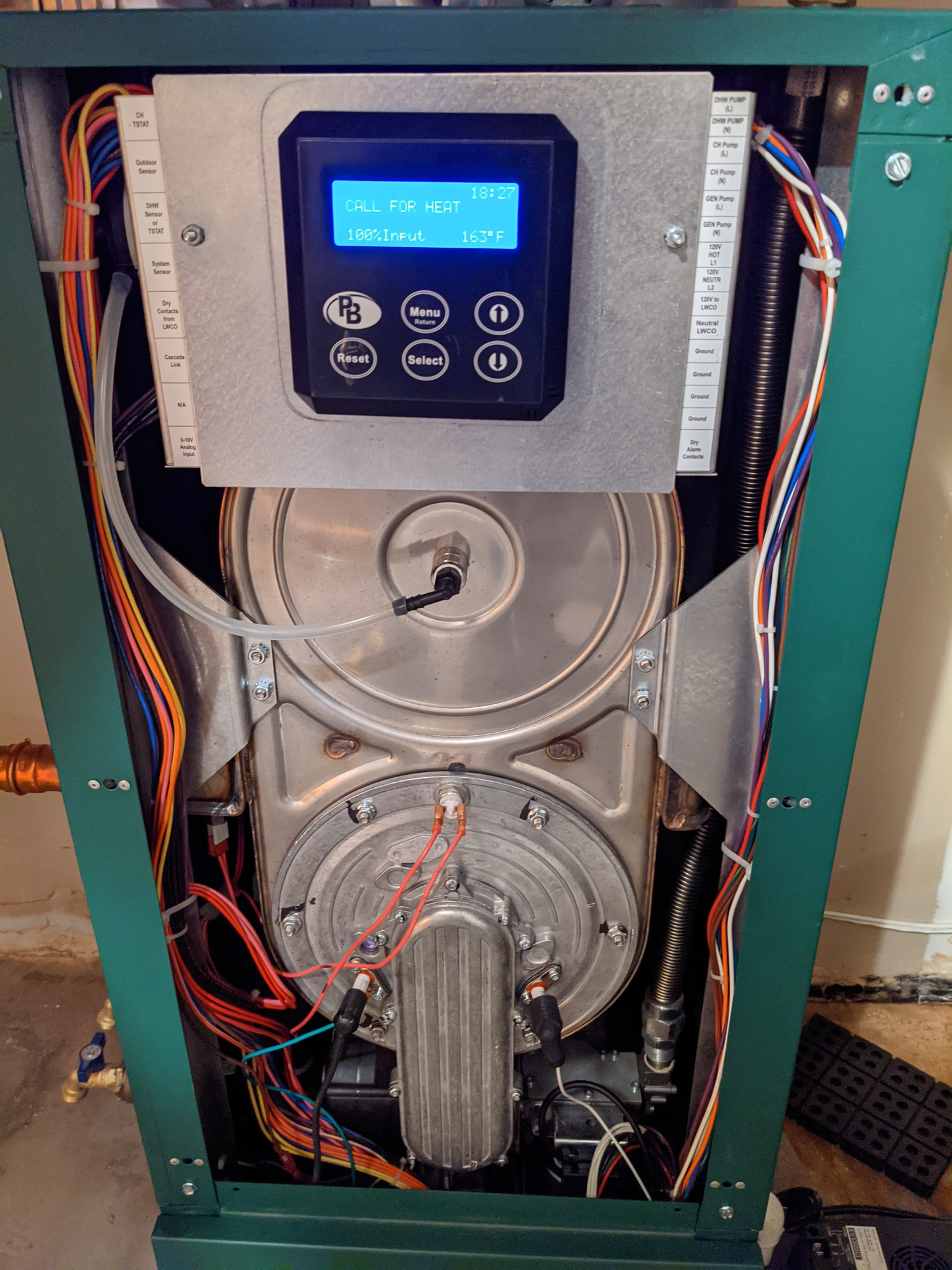
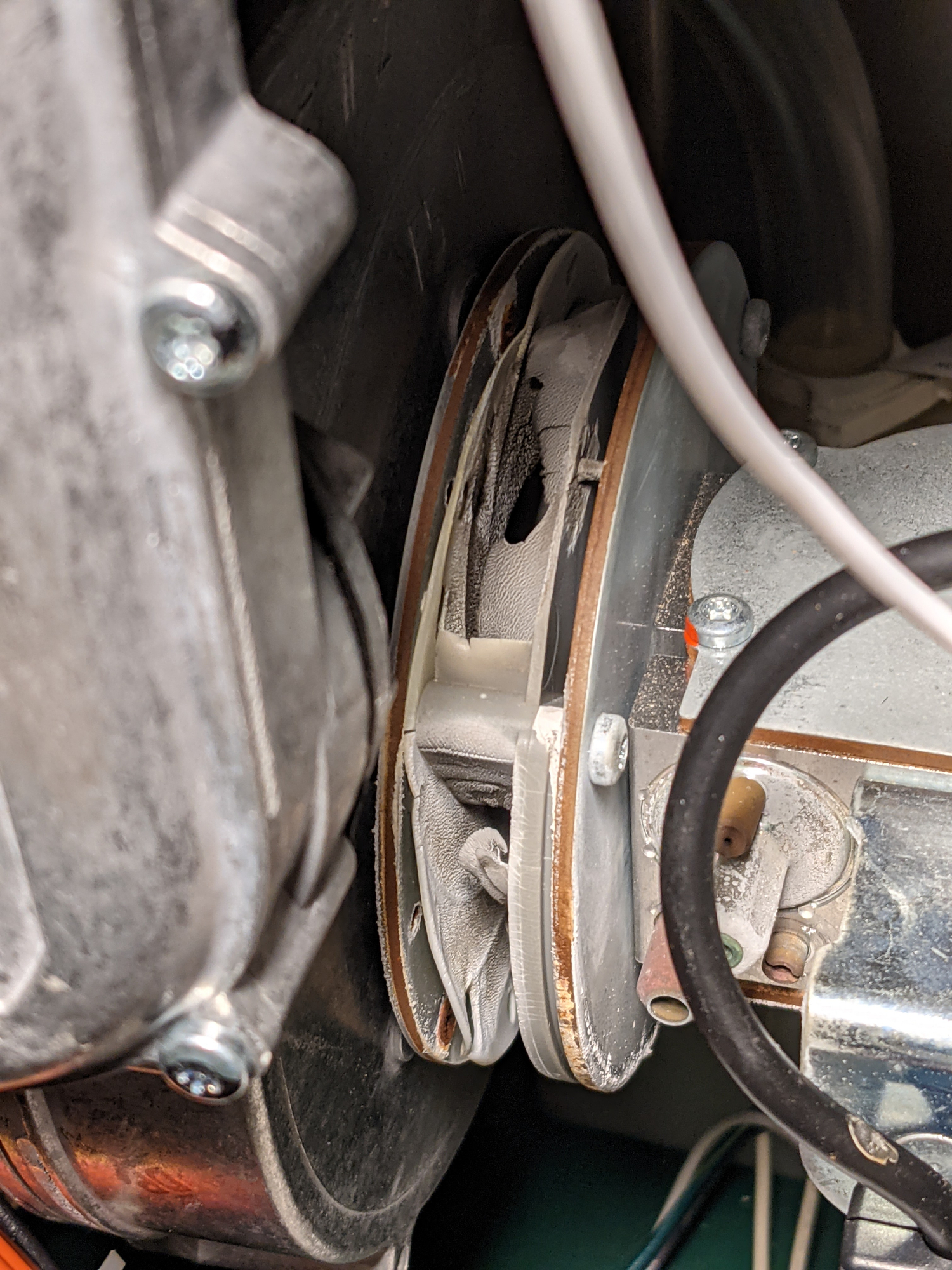
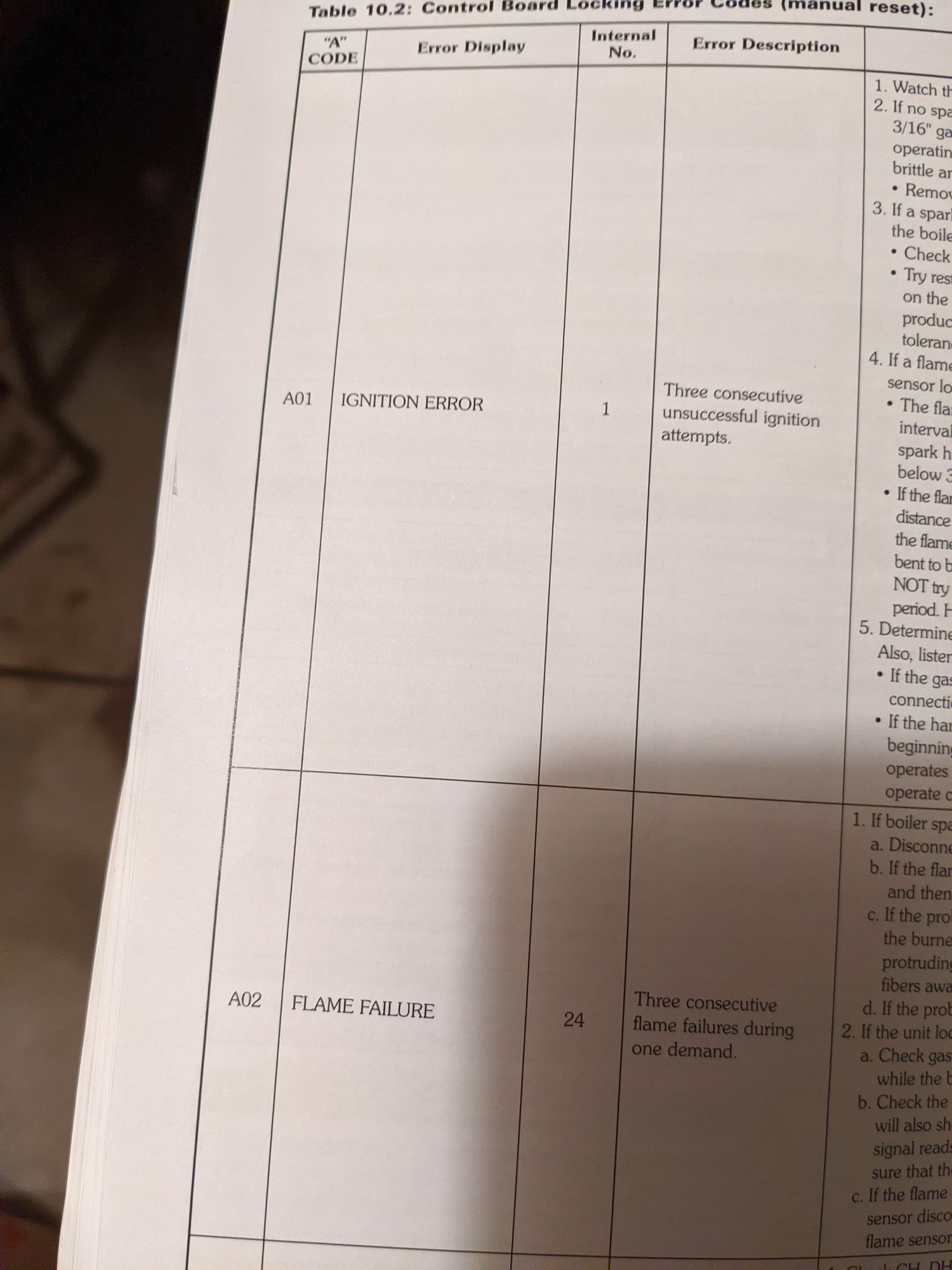

I wish I could clean it (don't have proper socket to unscrew) just to check that one off list but anything after this would need a professional. I've just have terrible luck with one I went to so far.
I feel like issue could be related to inconsistent gas or airflow given it is working intermittenly and not completely out. So i'd think most parts are in working order because if one was out I feel it wouldn't work at all. I also know nothing and have no experience so just guessing here and wondering if anyone has any thoughts or similar experience?
Related to elansp above, I took a picture of my gas valve and it doesn't look like its in good shape, does this look off to anyone? I'll paste some pics below and greatly appreciate any feedback people may have. Boiler is 3 years old btw. Thank you
It was never completely out, just very inconsistent. The reset button used to typically fix the issue when the error would pop up. Had a technician look at it Tuesday, didn't fix it. Came back next day, and couldn't fix but said they may need some new parts and will give me an estimate the next day. I didn't have a good feeling they knew precisely what to do or that their work would be reasonably priced based on experience up until this point.
I researched the error and found the flame sensor and ignitor were common problems so i ordered the parts for $150 and had them overnighted. At this point the reset button is no longer fixing the issue and furnace has been off for over 24 hours. I received the parts Friday evening at 8pm. I changed the sensor and it fired back up. Great. Went to sleep and go the lockout error at some point overnight. I replaced the ignitor at 5am and it fired back up again and saturday it ran pretty much all day but went back out some time overnight into Sunday and wouldn't start back up . Heat has been off all day/night since, I took out sensor and ignitor earlier today, dusted off, and nothing. Left it alone and it just came back on about an hour ago and we're getting heat.
Elansp had a very similar problem but I just don't know how to get a technician that is familiar with this solution or specializes in peerless pf systems: https://forum.heatinghelp.com/discussion/comment/1684849
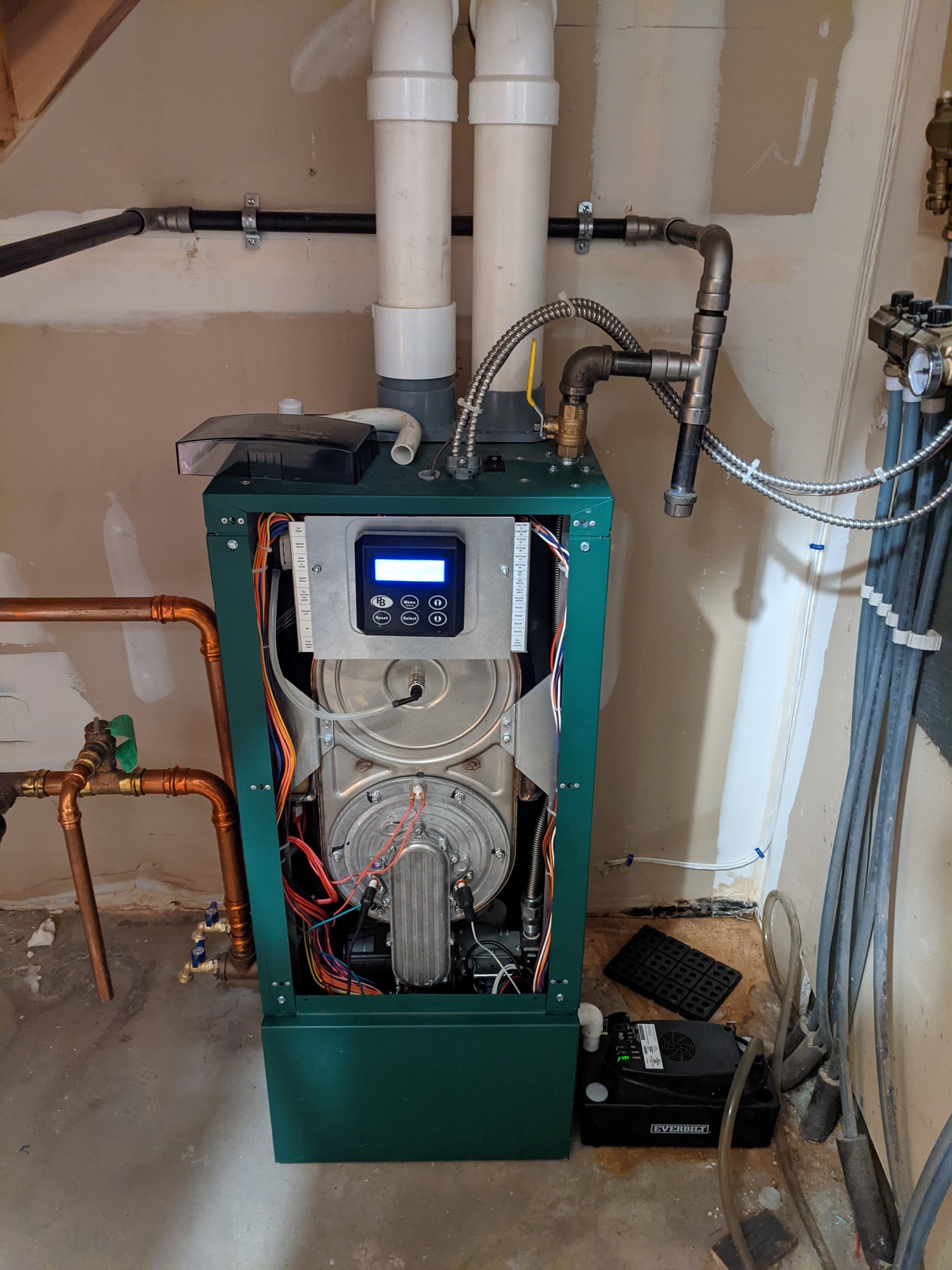
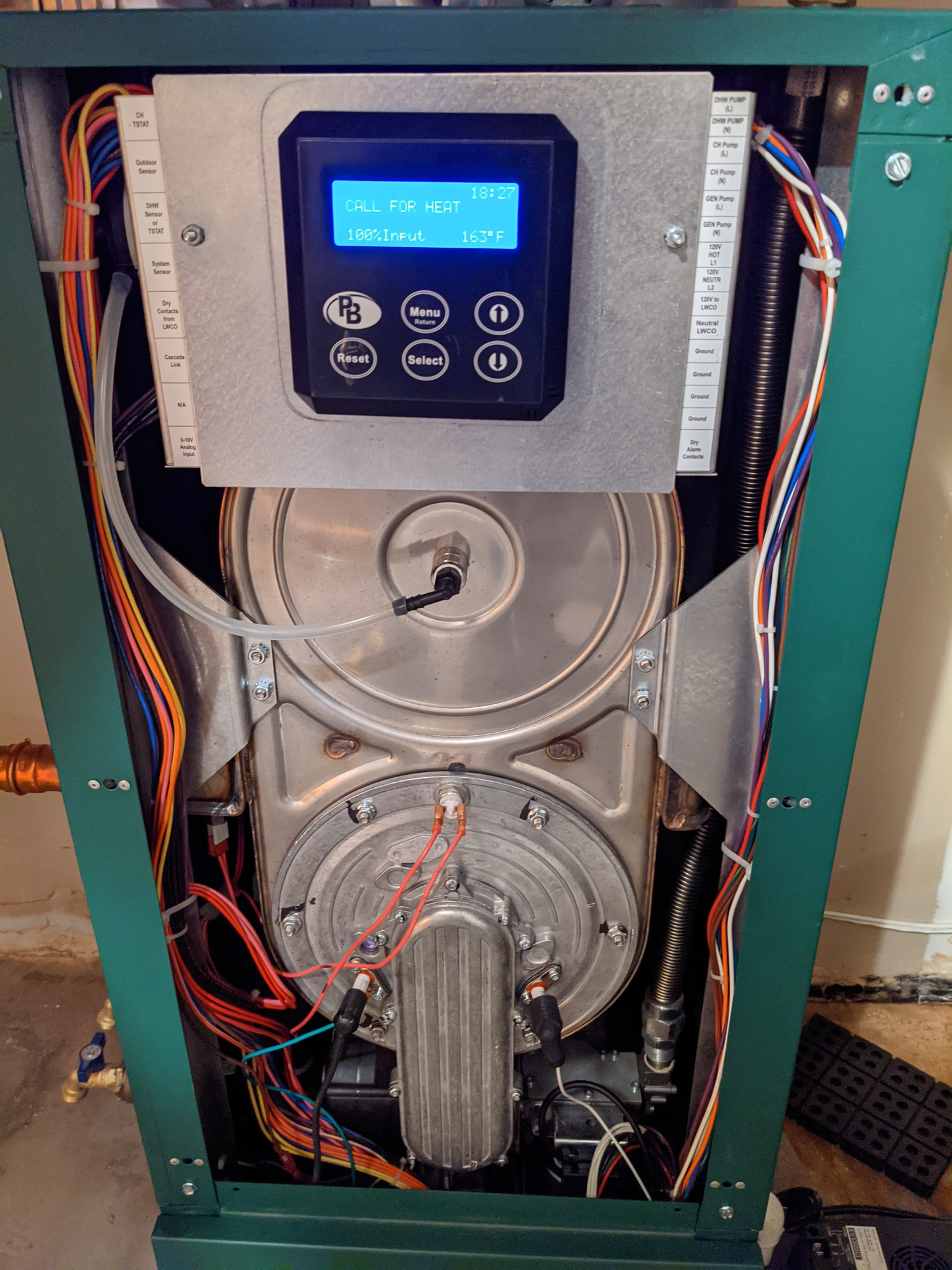
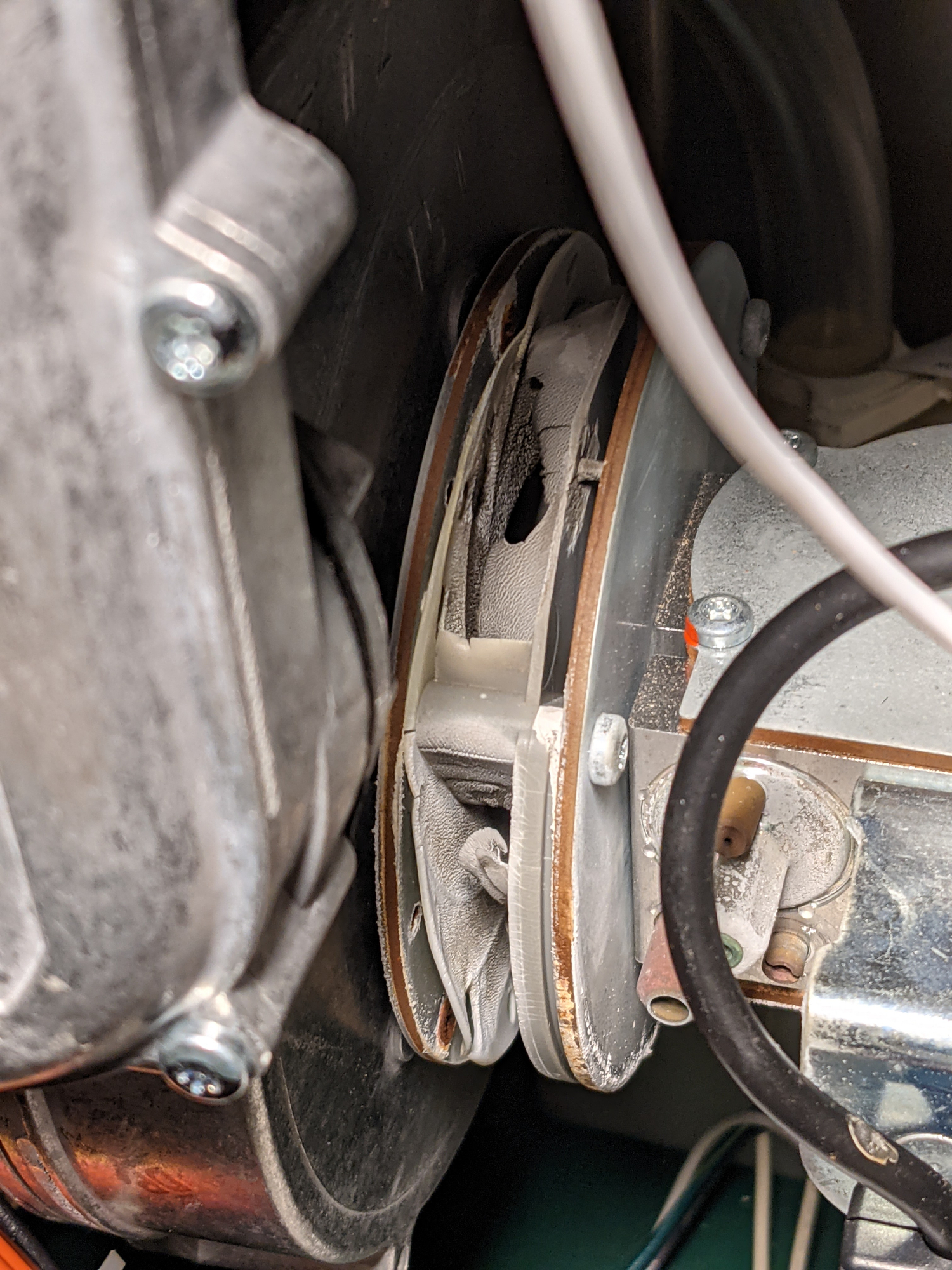
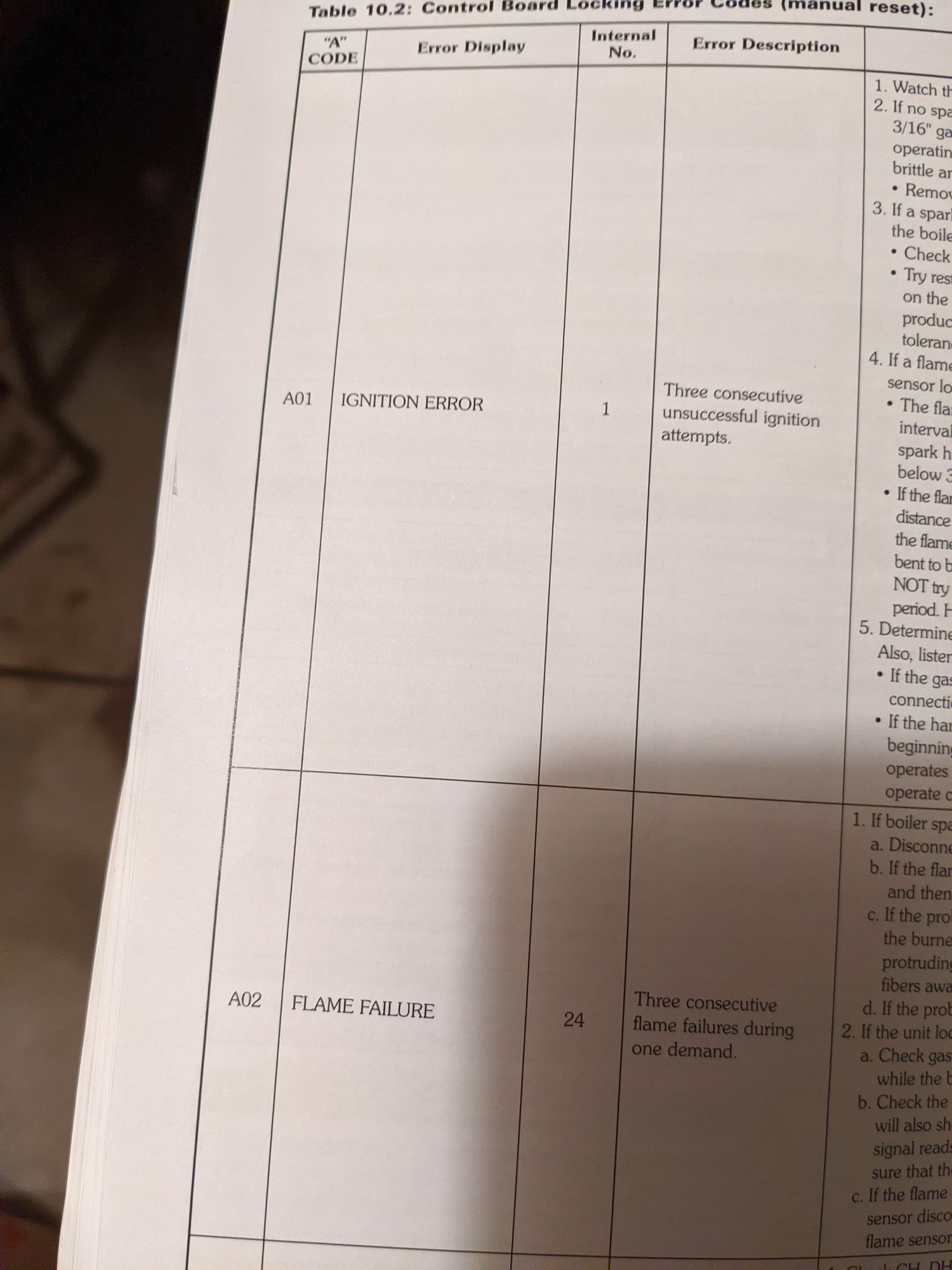

I wish I could clean it (don't have proper socket to unscrew) just to check that one off list but anything after this would need a professional. I've just have terrible luck with one I went to so far.
I feel like issue could be related to inconsistent gas or airflow given it is working intermittenly and not completely out. So i'd think most parts are in working order because if one was out I feel it wouldn't work at all. I also know nothing and have no experience so just guessing here and wondering if anyone has any thoughts or similar experience?
Related to elansp above, I took a picture of my gas valve and it doesn't look like its in good shape, does this look off to anyone? I'll paste some pics below and greatly appreciate any feedback people may have. Boiler is 3 years old btw. Thank you
0
Comments
-
Got about an hour and a half of heat before (thermostats didn't reach temp) before locking out - it has tried starting back up twice since and failed/lockedout each time0
-
-
Thank you Kcopp - its been locked but i just reset it and it fired back up after the second reset. Assuming the swirl plate is part of the gas valve in the pic i sent. Exhaust getting sucked back in, any telltale signs of that? It does make a vaccuum/sucking noise when it tries to start sometimes, like a whoosh whoosh sucking noise 3-4 times in a row. the vent is in front of the house, not sure where the intake is.
And curious, how can you tell exhaust getting sucked back in from the picture?0 -
-
Pics of the venting below - It worked for most of the night last night. Didn't start at all today after 3-4 tries throughout the day. I just got home, took the cover off, hit reset and it fired back up.
0 -
Hi D818-
Your situation looks much "better" than mine as there seems to be 2 obvious issues (other resident experts can opine). The peerless rep adjusted my gas valve and the unit locks out less frequently but has still locked out once since last adjusted almost 2 weeks ago and I've had over 10 ignition failures since then but onto your situation...
I use fine grit sandpaper (most tell you to use a dollar bill but after 3 years that probably wont be sufficient to get the build up off the ignitor/sensors) to scuff up both the ignitor and sensor. I'd do this when both are cool. Make sure to turn the unit off before you remove anything or venture further. Remember which plug goes to the ignitor and which one goes to the sensor - they look similar.
1st - you need to replace that swirl plate. If you are comfortable doing this, you will probably need the same torx driver (I think its torx from your picture and off the top of my head or its a screw driver).
2nd - from the external picture, that venting doesn't look look close to correct which is why the gas valve and other internals are rusted/falling apart. If you look in your manual you will see how to properly vent the unit.
The reason your unit starts back up is its a protection feature where after a 1hr lockout it will attempt to restart to avoid pipes freezing. If there are enough microamps read from the ignitor, the unit will fire back up and run until it fails to restart.
Here's my worthless 2c:
1. The intake should have a screen inside to prevent animals from entering and should terminate approximately 1 ft past your siding. Toss out that metal covering.
2. The exhaust isn't vented properly. As per the manual, since your exhaust is so close to your intake, You should add a 90 degree, add another minimum 12" of PVC pipe upwards (confirm in manual) then another 90 degree bend and finish with a few inches of straight PVC. Put in a screen inside that exhaust to prevent anything from crawling in there.
Good luck.
0 -
Here's a picture of the termination points that I was referring to taken from my Peerless manual. I believe yours should be the same but you may want to confirm...
0 -
I believe you have posted this before as others have stated , the swirl plate is obviously damaged and need to be replaced possibly w a new gas valve possibly ,most likely from re circ gases and the the vent termination needs not only a inlet screen but a extension on the exhaust to help discourage and possibly eliminate your re circ issues . With a damaged swirl plate the combustion number will never be right nor will the flame failure codes end, the combustion number is what’s causing the flame rods to become coated and weaken your flame signal thus coding your boiler off . The installation company should correct the situation being it’s been like this from the get go . I see that the gas was all done in mega press and I don’t see a union isnt that special ? Wonder if anyone has pulled the burner plate off and cleaned it or check the front and rear chamber refractory for damage . . I would assume your issues are directly related to re circ gases . I personally think this is a install issue and that the installation company should be responsible for the getting it right , repairing and ending the reoccurring issue ,I don’t think that there should be a charge being they installed the equipment and the answer that it only happening to you is bull hold tight to your guns and demand they end the issue . Just cause there a big company doesn’t mean there the greatest it just means they got a lot of over head and a lot on there heads . I also would verify the correct gas pressure and the pressure drop as the unit is starting and running in hi / low fire . Also any tech who shows up without a combustion analyzer to do any thing concerning the burner should be asked to leave , you need there top senior service tech no bull and it should not be drawn out into a on going issue ,talk directly to the service manager no secretary and tell them to send some who has experience w this specific boiler ,got to be some one who works there that has a clue other wise they should not be installing something that they are clueless on how to install ,program and service just because they think they can doesn’t mean they can and when they only offer a monthly billable service plan to get service I would suggest you find another service provider cause your money is just there to cover monthly overhead wout performing nothing and not straightening out your re occurring issues Peace and good luck clammy
R.A. Calmbacher L.L.C. HVAC
NJ Master HVAC Lic.
Mahwah, NJ
Specializing in steam and hydronic heating0 -
From the looks of it you are certainly getting recirc of ga products into the boiler. Concentric vents are prone to this... Also the distance off the ground and it looks like the area in front is not free and clear. Does it run up hill out In front?
Snorkel/ periscope both of them so there is 24" free and clear from both the intake and the exhaust as well as off the ground.
Fix the swirl plate first to get the lock out from happening.....
0 -
Hi All - Thank you for the comments. Just to give an update it was the swirl plate. It was replaced and the prblem was fixed. Too much outside air was moxing in preventing it from igniting. If i wrapped my hand around the holes/tears it would ignite which was the workaround I used until parts came in. I'll look into the exhaust and intake set, and yes it is slightly uphil, probably a few feet, 3 to 5 i'd say. Thanks again.
Regards,
D
0
Categories
- All Categories
- 87K THE MAIN WALL
- 3.2K A-C, Heat Pumps & Refrigeration
- 58 Biomass
- 427 Carbon Monoxide Awareness
- 113 Chimneys & Flues
- 2.1K Domestic Hot Water
- 5.7K Gas Heating
- 109 Geothermal
- 161 Indoor-Air Quality
- 3.6K Oil Heating
- 70 Pipe Deterioration
- 995 Plumbing
- 6.3K Radiant Heating
- 391 Solar
- 15.4K Strictly Steam
- 3.4K Thermostats and Controls
- 55 Water Quality
- 44 Industry Classes
- 48 Job Opportunities
- 18 Recall Announcements