Welcome! Here are the website rules, as well as some tips for using this forum.
Need to contact us? Visit https://heatinghelp.com/contact-us/.
Click here to Find a Contractor in your area.
Swivel Flange Gaskets
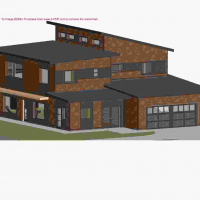
SENWiEco
Member Posts: 164
I have just started my mechanical room and have a Wilo Star for my buffer tank circulator. I have a set of Wilo 1-1/4 BV Flanges I will be using with this circulator (Art No 2705806).
These flanges came with both a flat gasket as well as a 'split' gasket. I have not previously used these type of flanges with a split gasket and not totally sure how to use. I reached out to Wilo, but they did not understand my question.
Can anyone look at attached photos and confirm I have used the split gasket correctly and have it facing the right direction on the flange. Also, should the split in the gasket be at any specific orientation (bottom)?
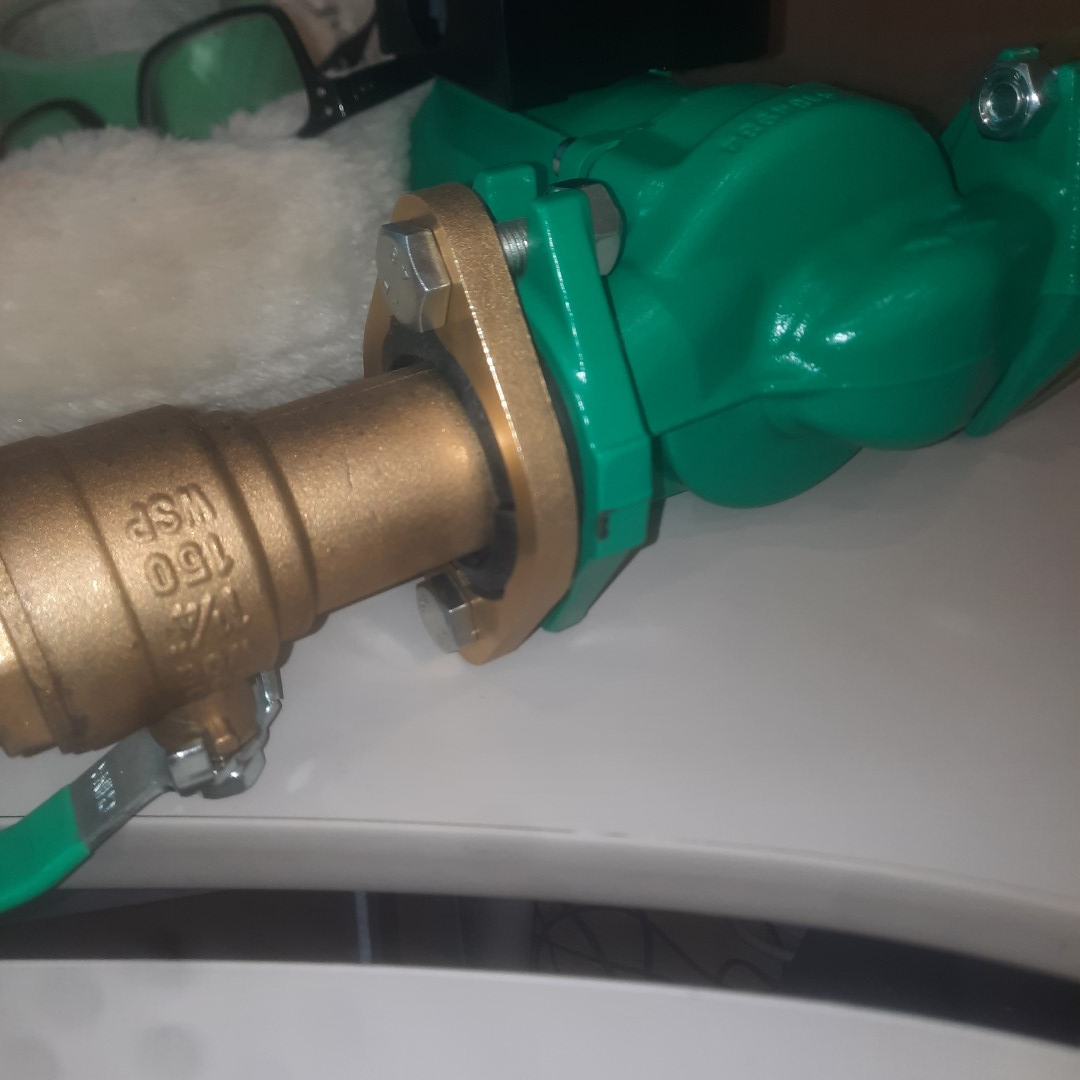
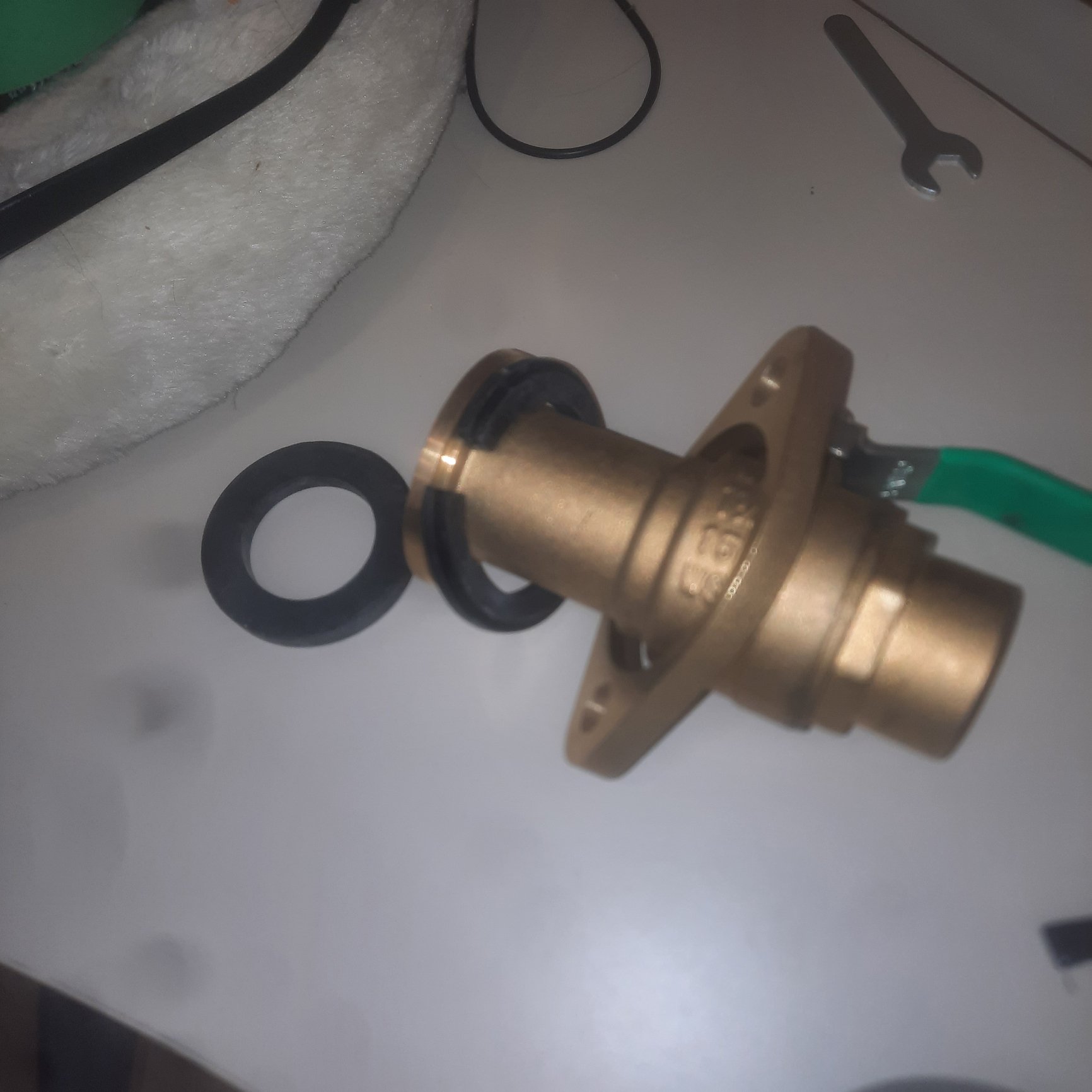
These flanges came with both a flat gasket as well as a 'split' gasket. I have not previously used these type of flanges with a split gasket and not totally sure how to use. I reached out to Wilo, but they did not understand my question.
Can anyone look at attached photos and confirm I have used the split gasket correctly and have it facing the right direction on the flange. Also, should the split in the gasket be at any specific orientation (bottom)?
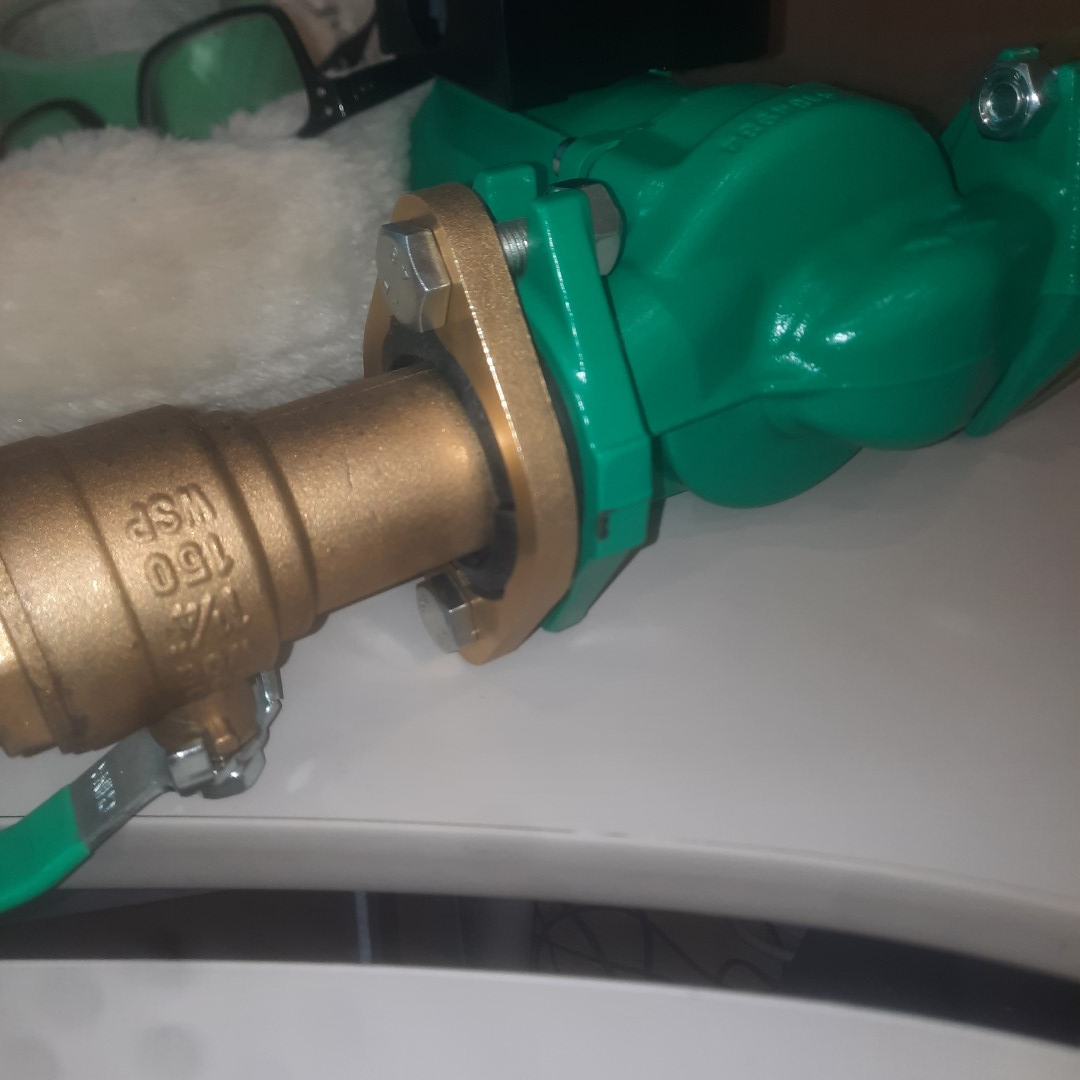
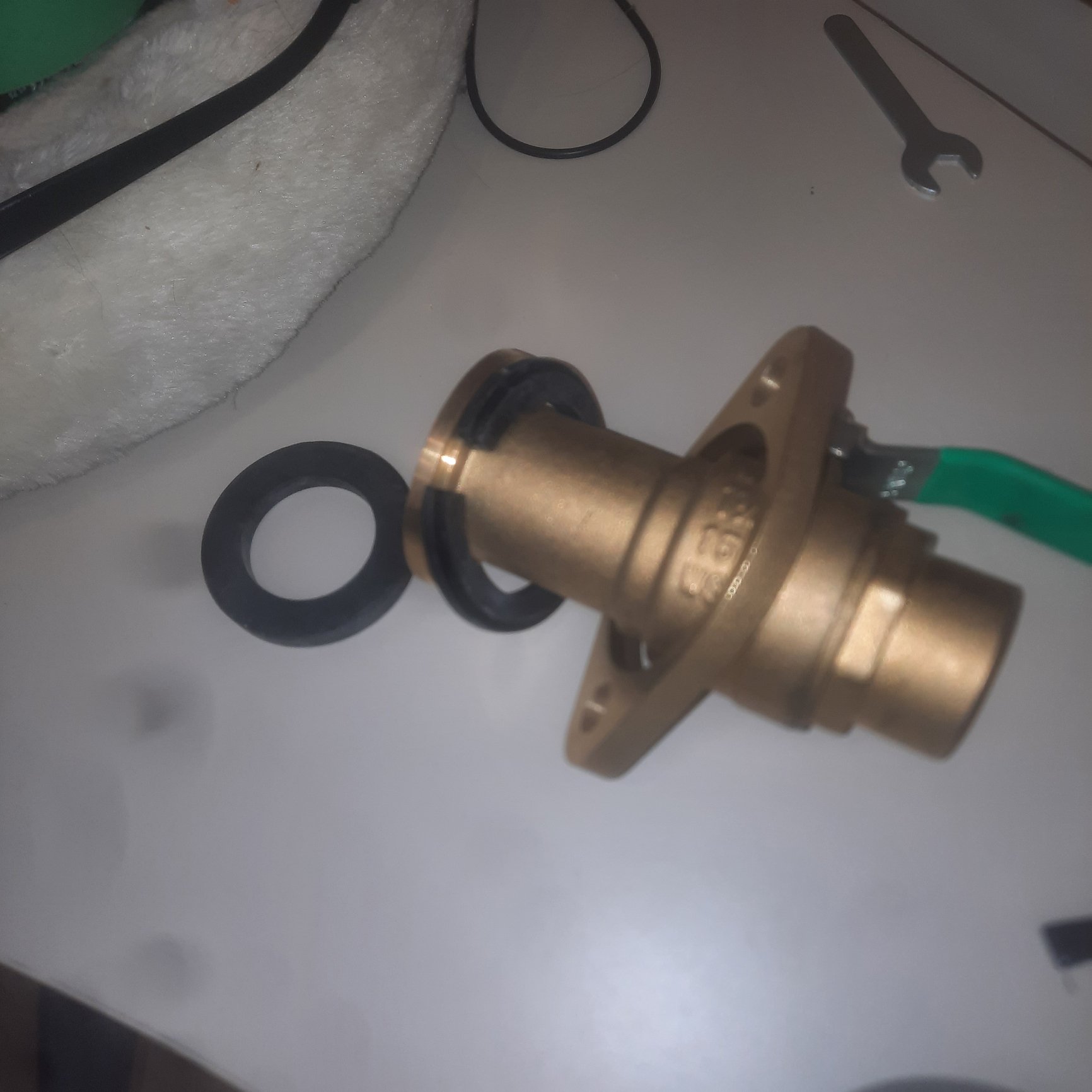
Sean Wiens
0
Comments
-
I have used that flange once before, not a fan! But I don't think that split gasket goes there. I could be wrong. The important gasket is the solid one. As long as you have it on the face of the flange valve body and the face of the pump, and the bolts are tightened evenly, it should not leak. The metal to metal connection (where you are showing the split ring gasket) does not need a gasket there.
Is the connection leaking? If not, then you are good to go!Edward Young Retired
After you make that expensive repair and you still have the same problem, What will you check next?
1 -
thanks @EdTheHeaterMan - I have just started layout of my mechanical room, so have not pressurized yet. Yes I will make sure face gasket is properly placed and flange torqued. The split ones were in bag, so clearly the Wilo intended for them to be used, but they could not explain 'how'. This circulator shows it can take flanges in the size range of 3/4" up to 1-1/2". So may be the split gasket is to ensure the pipe end of the flange stays centred on the circulator flange?Sean Wiens1
-
Does the rotating part of the flange stay on the part that connects to the pipe without that plastic ring or does that fit between the 2?0
-
-
@mattmia2 - the rotating ring does stay on the flange without the gasket. Without the gasket, parts are quite sloppy. The rotating ring can also be removed from the flange through the two cut-out ears you see on the ring.
Glad this was not a stupid question. I had not seen these before and felt like a fool not knowing what to do with it.Sean Wiens0 -
Could this be to create an acoustical barrier by providing a gasket between the pipe and the circulator? Wish I could get a response from WiloSean Wiens0
-
I think the ring isolates the metal flange from the brass valve, both a slip ring and dielectric ring. The flat gasket makes the seal. The flat ring should fit into a recess in the pump body to keep it in place, it's not just a flat gasket, but a ring sized to that pump.
Wilo uses a much larger ring compared to other brands, really no substituting.Bob "hot rod" Rohr
trainer for Caleffi NA
Living the hydronic dream2 -
thanks @hot_rod - that makes a lot of sense. And yes the flat gasket does fit nicely in the recess. It is surprising that that flange pack does not come with any instructions considering this is an unusual set-up and how important this dielectric gasket is. Thanks again for your help. You have assisted me greatly in my mechanical room design. I will post a photo once complete.Sean Wiens0
-
I know this design quite well (I was their North American Product/Project Manager back then). The single piece gasket is installed inside the recess in the pump volute. The split ring is intended to align and hold the pieces in place. Back then we didn't think we needed an instruction sheet.
The most interesting thing for me was, regardless if the design made sense and lowered the number of pumps a guy had in his truck, few were willing to pay a bit more for this feature. Hence the 4 bolt flange (that I personally think looks weird).
Let me know if you have any other questions about their product - I'm happy to assist.1 -
Thanks Steve - appreciate the info. Based on all the above comments, I think I have installed correctly and will move on. I have lots of soldering ahead of meSean Wiens0
-
Be careful when you sweat, the plastic ring doesn’t take much before it starts to squirm. It can be removed and replaced, but a bummer if you crack it in half🥲Bob "hot rod" Rohr
trainer for Caleffi NA
Living the hydronic dream0 -
thanks @hot_rod - assume you are meaning teflon seal in ball valves? Most of my valves/components have NPT connections so will be off when soldering. For the few sweat ones I have, I will be using https://www.supplyhouse.com/Refrigeration-Technologies-RT400P-Wetrag-Heat-Blocking-Compound-12-oz (have not used before, so looking forward to trying)Sean Wiens0
-
SENWiEco said:thanks @hot_rod - that makes a lot of sense. And yes the flat gasket does fit nicely in the recess. It is surprising that that flange pack does not come with any instructions considering this is an unusual set-up and how important this dielectric gasket is. Thanks again for your help. You have assisted me greatly in my mechanical room design. I will post a photo once complete.Bob "hot rod" Rohr
trainer for Caleffi NA
Living the hydronic dream1
Categories
- All Categories
- 87K THE MAIN WALL
- 3.2K A-C, Heat Pumps & Refrigeration
- 58 Biomass
- 426 Carbon Monoxide Awareness
- 113 Chimneys & Flues
- 2.1K Domestic Hot Water
- 5.7K Gas Heating
- 109 Geothermal
- 161 Indoor-Air Quality
- 3.6K Oil Heating
- 70 Pipe Deterioration
- 994 Plumbing
- 6.3K Radiant Heating
- 389 Solar
- 15.4K Strictly Steam
- 3.4K Thermostats and Controls
- 54 Water Quality
- 44 Industry Classes
- 48 Job Opportunities
- 18 Recall Announcements