Welcome! Here are the website rules, as well as some tips for using this forum.
Need to contact us? Visit https://heatinghelp.com/contact-us/.
Click here to Find a Contractor in your area.
Indirect radiation piping issue
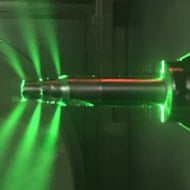
Lard
Member Posts: 115
I was installing some new vents (Gorton #1, previously Hoffman 75’s) on my church’s indirect stacks yesterday and noticed a deadman piping mistake. There are two stacks of two rows of Vento indirects fed separately, then dripped to a common return above the water line. 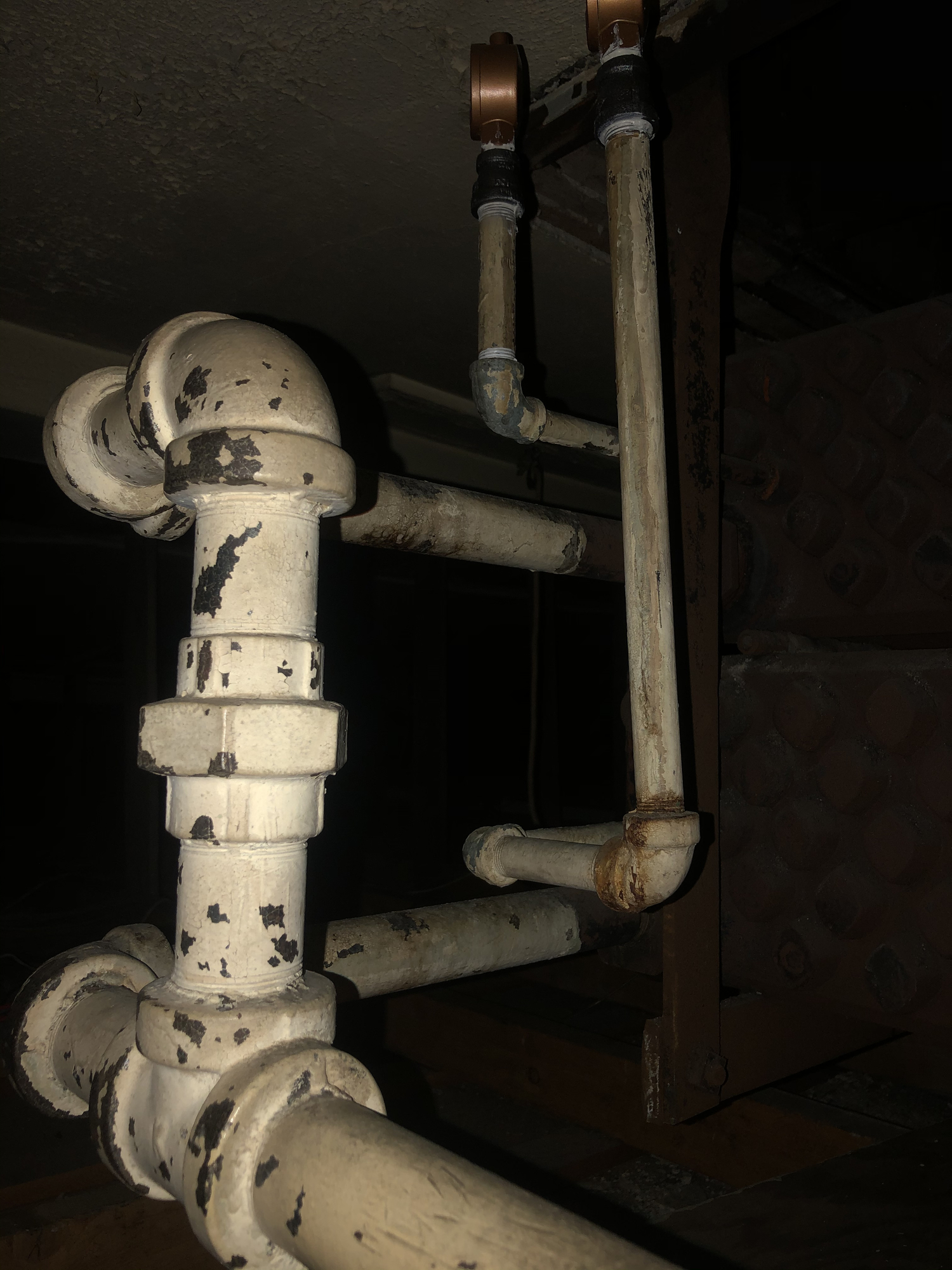
This is apparently how it has been piped since 1916. It is inside a ceiling, so my lighting is a bit poor in the photo. It is a two-pipe air vent setup on 237 EDR of ARCO Vento units in each stack and the piping shown is the drips for one of the stacks.
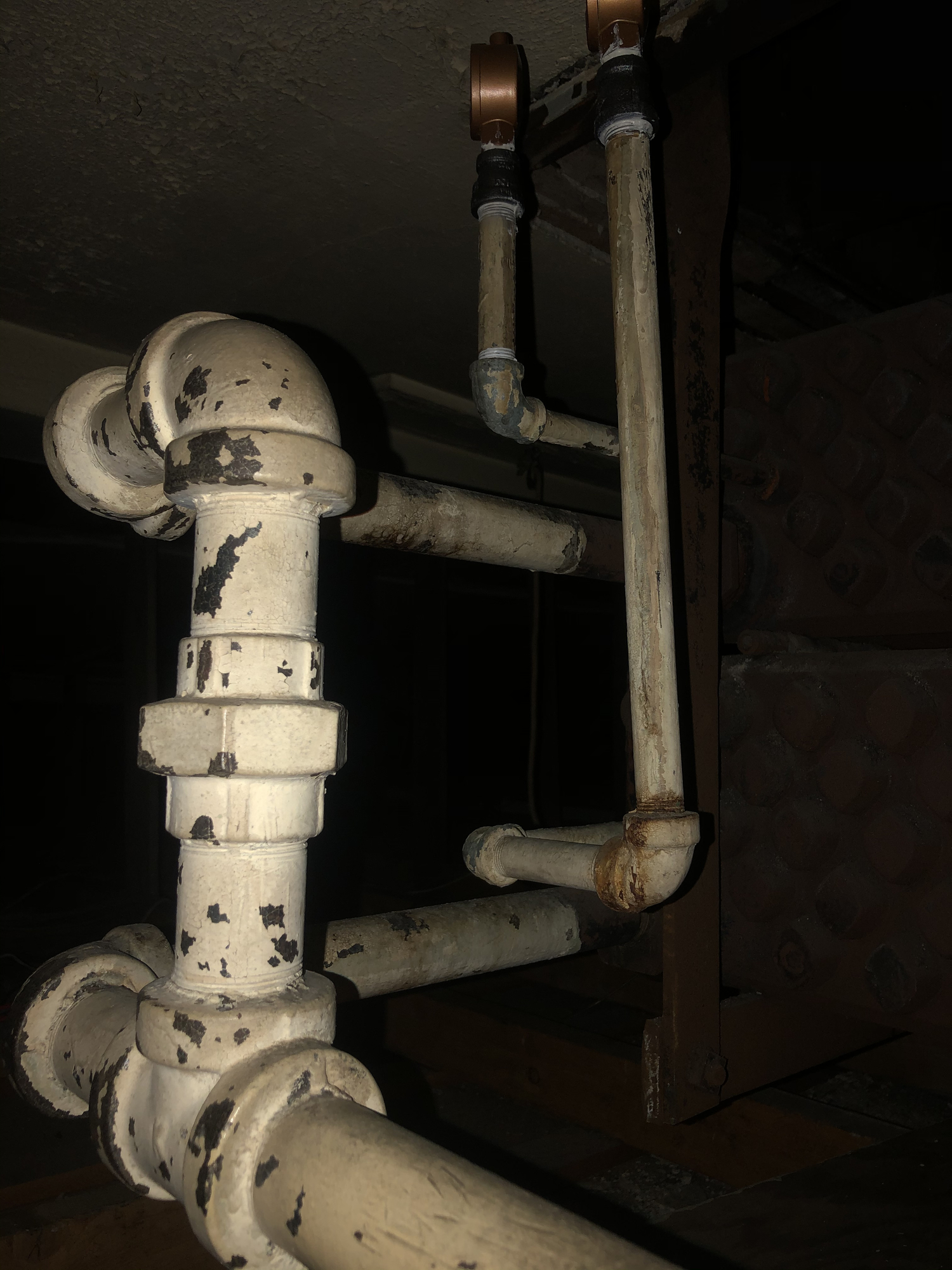
This is apparently how it has been piped since 1916. It is inside a ceiling, so my lighting is a bit poor in the photo. It is a two-pipe air vent setup on 237 EDR of ARCO Vento units in each stack and the piping shown is the drips for one of the stacks.
When testing the new vents, I noticed the obvious occurring. The top stack filled faster than the bottom due to getting preheated air from the lower stack and eventually short-circuited and closed the lower stack vent, trapping air in the lower stack. Steam also began flowing through the drip back to the vents on the other stack since all four drips are connected above the water line. The heavy venting is the only way we have found to get most of the air out before both vents close, and it generally works OK since it has drips to handle the condensate, but of course, I want to correct the issue and slow down the venting.
I have added it to the list of deficiencies to address in this system—I am looking for opinion on how to resolve it. My first idea is to put all four of the stacks on a 5’ loop seal since I have space to do so in an adjacent room. That said, the condensate transfer pump for this end of the building is also only 15’ west and 10’ below in that same room, so a thermostatic trap on each stack is also viable to make it true two-pipe with a dry return to the tank. The air vents have always been a pain on these due to elevation challenges and a decent condensate load since these two indirects total 474 EDR, so true two-pipe may help with that.
I have added it to the list of deficiencies to address in this system—I am looking for opinion on how to resolve it. My first idea is to put all four of the stacks on a 5’ loop seal since I have space to do so in an adjacent room. That said, the condensate transfer pump for this end of the building is also only 15’ west and 10’ below in that same room, so a thermostatic trap on each stack is also viable to make it true two-pipe with a dry return to the tank. The air vents have always been a pain on these due to elevation challenges and a decent condensate load since these two indirects total 474 EDR, so true two-pipe may help with that.
0
Comments
-
I gotta learn to read, everything, and better, before (s)thinking,
if the 2 pipe rads are trapped,
they are, aren't they?
and if your traps are good and functioning,
then no live steam should be in your dry returns, just condensate and vent air.known to beat dead horses0 -
@Lard, any chance that was one below the waterline?0
-
Danny Scully said:@Lard, any chance that was one below the waterline?
I restored the original water line at the return drop with a loop to stop a short-circuit from a main drip and that helped things immensely system-scale, but these four connections are only 2’ below the 10’ ceiling of the boiler room, so even with the old boiler (s), the water line never came close. The piping is clearly original as much of it passes through the original plaster/lath work.0 -
Loop seals work good if you have a way to do it. Big traps are expensive and when you include traps strainers and valves pipe and fittings are less expensive, no moving parts to fail.
As long as you can keep the pressure low enough so the water isn't blown out of the loop seal0 -
EBEBRATT-Ed said:Loop seals work good if you have a way to do it. Big traps are expensive and when you include traps strainers and valves pipe and fittings are less expensive, no moving parts to fail. As long as you can keep the pressure low enough so the water isn't blown out of the loop seal
For pressure control, stay tuned for the Lard IFMStat. I just ordered an IFM PN7007 programmable transducer to set up PWM using a Siemens delay-on timer (0.2s to 100h) that I have in my stash. The boiler is hopelessly oversized by 1700 EDR, so this will be a way to tame it. It should be a Weil Mclain 780, not the 1180 that is in place!
I currently have the pressure around 2lbs, otherwise the short cycling is too extreme and messes with venting due to vacuum forming and sucking air during pre-purge. The collapse/vacuum is also quite noisy, not desired in a church... A time delay restart on pressure using a reliable transducer or vaporstat is the only way I can make lower pressure work (or... actually have a properly-sized boiler...)0 -
I was able to run over and snap a few more pictures for better context.
Supply for the West stack in the foreground, return in center, and then supply for the East stack behind that with the two flange unions:Closeup of the return, left two are the West stack, right single is East stack which doubles up on the other side of the wall, four connections above water total. With punching one new hole in the wall, I can put a loop right below this. It must end up overhead again as there are two doorways to negotiate.Original abandoned 1916 wet return ell at bottom where this return used to connect along with a 2” drip from the main. The 1950’s wet return is 5’ to the right of this and also abandoned, loop for condensate transfer pump was formed using part of the 1950’s return where they put the elbow in to go to an alternate exposed route that was entombed in concrete in ‘89. Pictures in the dining hall from the 70’s/80’s show the previously easy-to-repair pipe before they did THAT silliness.I stuck a couple 3/4 full port valves on the loop to flush it. (there is another valve at the other side of the loop).0
Categories
- All Categories
- 87K THE MAIN WALL
- 3.2K A-C, Heat Pumps & Refrigeration
- 58 Biomass
- 427 Carbon Monoxide Awareness
- 113 Chimneys & Flues
- 2.1K Domestic Hot Water
- 5.7K Gas Heating
- 109 Geothermal
- 161 Indoor-Air Quality
- 3.6K Oil Heating
- 70 Pipe Deterioration
- 995 Plumbing
- 6.3K Radiant Heating
- 391 Solar
- 15.4K Strictly Steam
- 3.4K Thermostats and Controls
- 55 Water Quality
- 44 Industry Classes
- 48 Job Opportunities
- 18 Recall Announcements