Welcome! Here are the website rules, as well as some tips for using this forum.
Need to contact us? Visit https://heatinghelp.com/contact-us/.
Click here to Find a Contractor in your area.
Switch from Air Scoop to Spirovent
Options

salisboss
Member Posts: 34
I have a hydronic heating system that uses a gas converted combi-boiler. It is not piped for pumping away (was going to do it this summer but never got around to it so its on the agenda for next summer). I currently have an air scoop with only 6 inches or so of straight pipe (rather than the normal 18) so I am in a never ending cycle of purging air then the air introduced with the city water never gets eliminated by air scoop/aav. So eventually it sounds like a river and I purge again and start over.
To remediate this until I can re-pipe for pumping away I want to replace the air scoop with a spirovent. My question is what is the best way to remove the air scoop as it is threaded in place. A picture of the setup is shown. I presume I have to remove the tank etc first but not sure.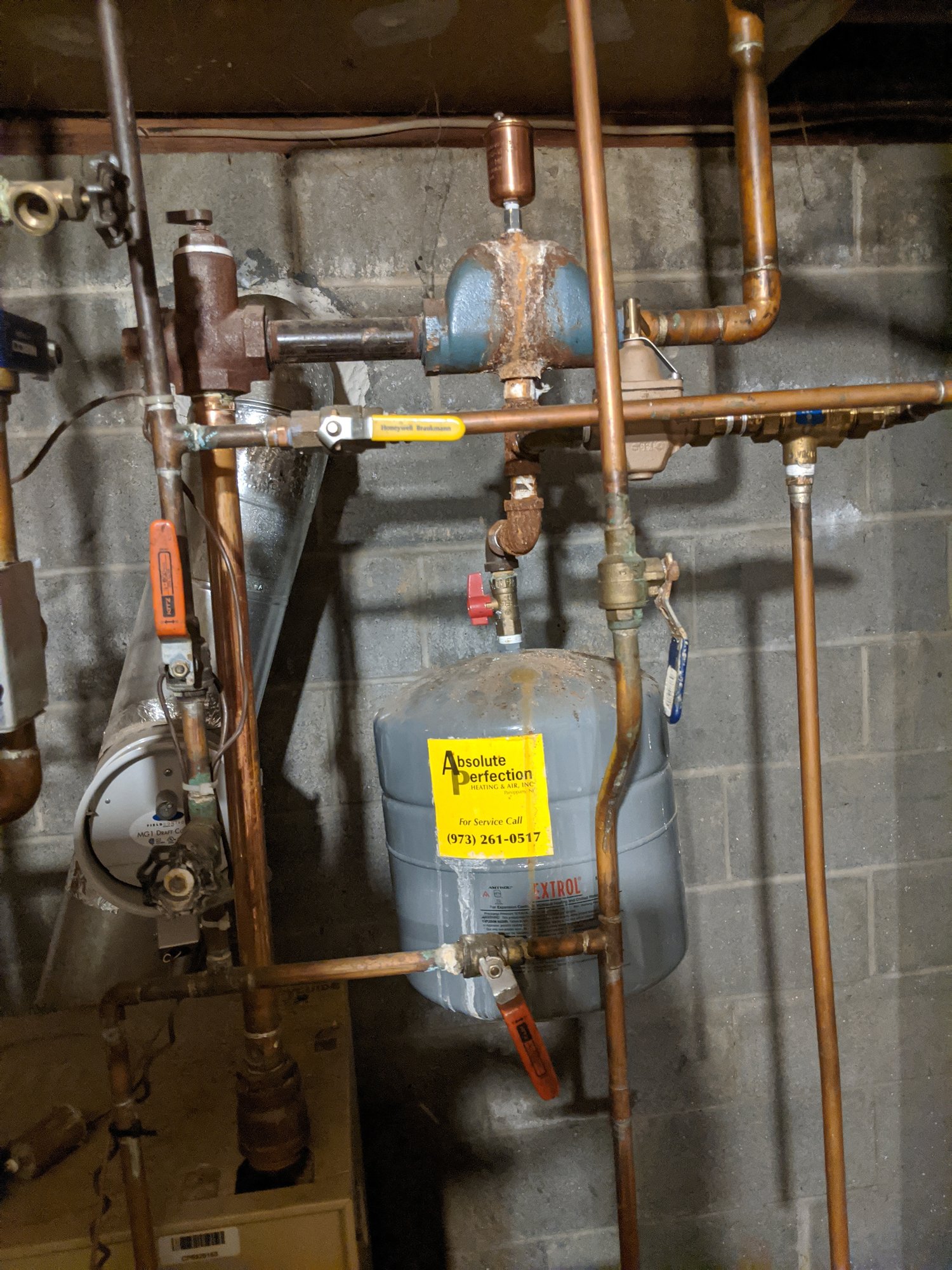
To remediate this until I can re-pipe for pumping away I want to replace the air scoop with a spirovent. My question is what is the best way to remove the air scoop as it is threaded in place. A picture of the setup is shown. I presume I have to remove the tank etc first but not sure.
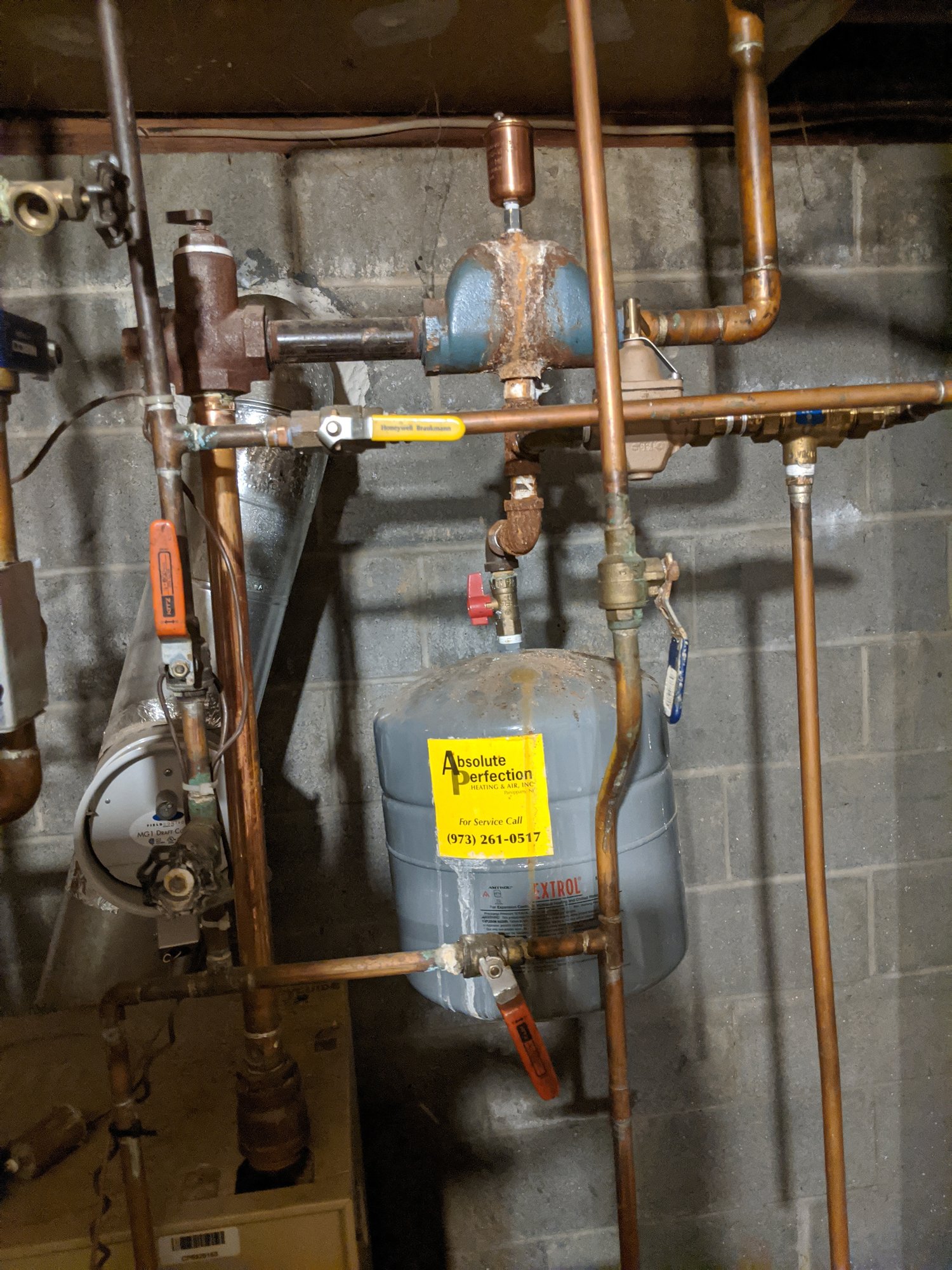
0
Comments
-
Do you have a press tool?
Cut the copper tube just past them scoop. Unscres scoop screw min Discal, muse press adapter, maybe a coupling depending on length.
Could be done with sweat adapter also.Bob "hot rod" Rohr
trainer for Caleffi NA
Living the hydronic dream0 -
Turn off the boiler.Close the fill valve.Drain what you need to in order to isolate the scoop. That may be the entire system. I can’t tell from the photo.Remove the tank and it’s piping.Cut the vertical copper to the right of the scoop. Disassemble from there.Install the air sep, the new piping, and the tank.Refill, bleed system, recommission.Steve Minnich0
-
-
STEVEusaPA said:If you're draining and cutting, good time to get that circulator in the mix for pumping away.0
-
Steve Minnich said:Turn off the boiler.Close the fill valve.Drain what you need to in order to isolate the scoop. That may be the entire system. I can’t tell from the photo.Remove the tank and it’s piping.Cut the vertical copper to the right of the scoop. Disassemble from there.Install the air sep, the new piping, and the tank.Refill, bleed system, recommission.0
-
-
I would absolutely add in two isolation flanges and relocate the circulator too! If you have a good microbubble resorber, it's not working as well as it could be if you start pumping away. I would change it to all copper, sweat or press. A spirovent will help, pumping away from the expansion tank with a spirovent will solve all your air issues.
Why would you want to alter the same part of the system twice? Always avoid draining the boiler repeatedly if possible.2 -
Man back in the day I would get smoked on here when I spoke bad about the " Air Scoop " ( or any product from them ). The air scoop is just as good just run a minimum of 30 feet straight to the inlet so I'm told.hvacfreak
Mechanical Enthusiast
Burnham MST 396 , 60 oz gauge , Tigerloop , Firomatic Check Valve , Mcdonnell Miller 67 lwco , Danfoss RA2k TRV'sEasyio FG20 Controller
1 -
Are you sure it's a bad scoop? A frequently air bound system would point me elsewhere first. And second, and third...
Just to the left of the supply riser out of the top of the boiler is a knockout in the top of the jacket. Underneath that, someone plugged the 1/2" opening that is meant for a 1/2 x 6 nipple, a 1/2 x 1/8 bell coupling, and an air eliminator like the one on the scoop. The Weil McLain GO has an internal air scoop in the block. It'll take you an hour and a half tops.
In a perfect world, you should be purging through the boiler. As it is, cold water feeds through the supply and purges through the return. Whatever is in the boiler is idle.
1 -
HVACNUT said:
Just to the left of the supply riser out of the top of the boiler is a knockout in the top of the jacket. Underneath that, someone plugged the 1/2" opening that is meant for a 1/2 x 6 nipple, a 1/2 x 1/8 bell coupling, and an air eliminator like the one on the scoop. The Weil McLain GO has an internal air scoop in the block. It'll take you an hour and a half tops.0 -
this is on a go -5 that is over 20 years old. Not my handy work !
No air in the system
Before Jason
0 -
high temperature, low velocity areas are the best way to capture air. In that boiler block would be a good spot to add a quality automatic air vent. Use one with a service check or iso valve as they do need occasional cleaning or rebuild.Bob "hot rod" Rohr
trainer for Caleffi NA
Living the hydronic dream0 -
Would I just drain all of the water out of the boiler to reduce pressure? I presume there is a plug or something blocking the end of the vent that I will tap into. Once the pressure is down I can remove that plug?hot_rod said:high temperature, low velocity areas are the best way to capture air. In that boiler block would be a good spot to add a quality automatic air vent. Use one with a service check or iso valve as they do need occasional cleaning or rebuild.
0 -
Cool it down reduce pressure and work fast! Have all the parts ready, pipe dope on them.salisboss said:
Would I just drain all of the water out of the boiler to reduce pressure? I presume there is a plug or something blocking the end of the vent that I will tap into. Once the pressure is down I can remove that plug?hot_rod said:high temperature, low velocity areas are the best way to capture air. In that boiler block would be a good spot to add a quality automatic air vent. Use one with a service check or iso valve as they do need occasional cleaning or rebuild.
I would start with a nipple long enough to reach down to the tap with a ball valve on it. Screw that in to have a connection point and iso valve for the vent. I'd use a 1/2" not the 1/8 size.
The Caleffi 5021 is one of the most common vents worldwide. Very easy to disassemble and clean.Bob "hot rod" Rohr
trainer for Caleffi NA
Living the hydronic dream0 -
salisboss said:
high temperature, low velocity areas are the best way to capture air. In that boiler block would be a good spot to add a quality automatic air vent. Use one with a service check or iso valve as they do need occasional cleaning or rebuild.
Would I just drain all of the water out of the boiler to reduce pressure? I presume there is a plug or something blocking the end of the vent that I will tap into. Once the pressure is down I can remove that plug?0 -
hot_rod said:
Cool it down reduce pressure and work fast! Have all the parts ready, pipe dope on them. I would start with a nipple long enough to reach down to the tap with a ball valve on it. Screw that in to have a connection point and iso valve for the vent. I'd use a 1/2" not the 1/8 size. The Caleffi 5021 is one of the most common vents worldwide. Very easy to disassemble and clean.high temperature, low velocity areas are the best way to capture air. In that boiler block would be a good spot to add a quality automatic air vent. Use one with a service check or iso valve as they do need occasional cleaning or rebuild.
Would I just drain all of the water out of the boiler to reduce pressure? I presume there is a plug or something blocking the end of the vent that I will tap into. Once the pressure is down I can remove that plug?0 -
I suppose it comes down to how much repiping you want to do
Certainly pumping away, add iso valves and a better purger would be nice
The circ is fine pumping the return into the boiler IF you move the expansion tank connection to near the inlet of the circ. Not sure which is easier for you.Bob "hot rod" Rohr
trainer for Caleffi NA
Living the hydronic dream0 -
So I went to remove the plug on the boiler to add the vent and it is a square bolt head. How do I get this off?I couldn't get it to budge. There is probably a specific tool. I tried regular channel locks but it is a tight squeeze.0
-
Also once I couldn't get the plug out I covered the boiler back up, opened the valves and turned it back on. However even though the boiler temp is down to 109 and I am calling for heat, nothing is happening. The burner controller isn't sensing any fire and nothing is happening.0
-
-
Thanks. Had a contractor come out. A probe on the thermostat came loose by coincidence so everything is running again. He thinks that I could have bad solder joints letting air in (I don't disagree, I don't have water leaks but do have some corroded joints). I am still going to try and put the vent on the boiler0
-
-
Never heard that one before. That’s not it.Steve Minnich0
-
Just repipe the near boiler and add the vent in the boiler block. Moving the circ, and adding an auto vent on the block will go a LONG way.Serving Northern Maine HVAC & Controls. I burn wood, it smells good!0
-
Ok. I am gonna do the block vent once I get penetrating fluid and a 12pt socket. I'll re-pipe in the spring. For some reason my boiler thermostat is saying low water all of a sudden. It shouldn't because the make-up water valve works fine. When I drained the boiler yesterday to originally try and do the vent, it filled back up fine as expected and the pressure is reading okay. Never seen this before but everything is working.Solid_Fuel_Man said:Just repipe the near boiler and add the vent in the boiler block. Moving the circ, and adding an auto vent on the block will go a LONG way.
0 -
Contractor came back out because the LWCO light came on. They think the probe is losing contact with the well. They recommended replacement so I ordered one to do myself.
However literally as the guy was driving away, the high temp light on the hydrostat came on. It never does. Could it be because I jacked up the heat to test the probe with him there?0
Categories
- All Categories
- 87K THE MAIN WALL
- 3.2K A-C, Heat Pumps & Refrigeration
- 58 Biomass
- 426 Carbon Monoxide Awareness
- 113 Chimneys & Flues
- 2.1K Domestic Hot Water
- 5.7K Gas Heating
- 109 Geothermal
- 161 Indoor-Air Quality
- 3.6K Oil Heating
- 70 Pipe Deterioration
- 994 Plumbing
- 6.3K Radiant Heating
- 389 Solar
- 15.4K Strictly Steam
- 3.4K Thermostats and Controls
- 54 Water Quality
- 44 Industry Classes
- 48 Job Opportunities
- 18 Recall Announcements