Welcome! Here are the website rules, as well as some tips for using this forum.
Need to contact us? Visit https://heatinghelp.com/contact-us/.
Click here to Find a Contractor in your area.
Oil Drip..... can anything be done??
Options
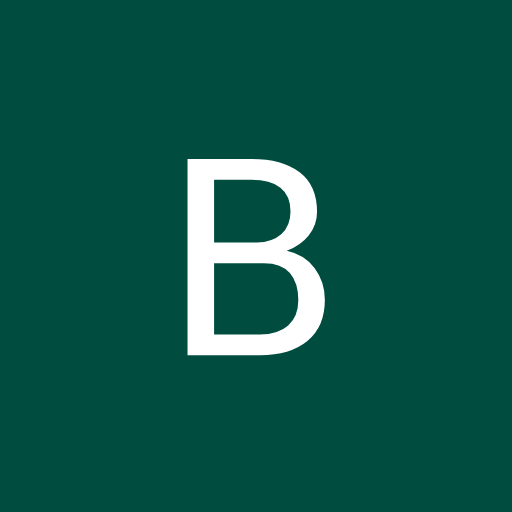
billcat
Member Posts: 3
in Oil Heating
Hello Guys,
We were called to a client that has an Intertherm Furnace with a Beckett gun.
It leaks oil back and eventually works it way through the casing and onto the floor.
Everything seems to have been tried. Pressure is good. There is a tiger loop on the system. We even tried a Delavan Protek nozzle. The drip keeps coming back.
The furnace is level but the gun is not even close, so it is back pitched. This is the cause that we see for that one drop at shutdown does not fall into firebox but goes back down nozzle assembly.
We have never seen anything about this. At a standstill.
Thank You for your help.
We were called to a client that has an Intertherm Furnace with a Beckett gun.
It leaks oil back and eventually works it way through the casing and onto the floor.
Everything seems to have been tried. Pressure is good. There is a tiger loop on the system. We even tried a Delavan Protek nozzle. The drip keeps coming back.
The furnace is level but the gun is not even close, so it is back pitched. This is the cause that we see for that one drop at shutdown does not fall into firebox but goes back down nozzle assembly.
We have never seen anything about this. At a standstill.
Thank You for your help.
0
Comments
-
-
Fix the leak.
Yes the burner should be at least level and probably pitched 1 or 2 degrees down toward the chamber, but there should be no leak.
Leak/oil showing at shutdown-lack of post purge, or bad cut-off on fuel pump.
Tiger Loop, different nozzle or correct pump pressure have nothing to do with it.
Other causes of an actual leak; Loose fittings, cracked flare, loose or over tightened nozzle, loose pump strainer, bad pump seal, poor over fire draft, poor combustion, plugged heat exchanger, wrong z-dimension, cracked/damaged/dirty end cone, cracked heat exchanger blowing oil back when the blower motor is running, loose bleed port, and on and on.
What actual diagnostic work did you perform?There was an error rendering this rich post.
1 -
@billcat
Take the burner off and shim it so it is pitched down use washers and seal the burner flange up with fiber rope if needed.
While you have the burner out check the z dimension, make sure the head is clean with the right nozzle. Check that the nozzle cut off is ok.
Sometimes oil trapped in the nozzle is heated by the combustion chamber when the burner shuts down...the oil expands and drips3 -
Agree , You need to pitch the burner blast tube into the chamber . I normally use a pipe nipple or cut piece of copper pipe under the burner housing to keep the downward inward pitch .. Air bubbles caught in the nozzle assembly can also cause an after drip..
There was an error rendering this rich post.
1 -
Thank you. Your help is Much appreciated. We'll pitch it, secure, & seal. Thanks again0
-
If you have a 150 psi gauge (or higher) with a 3/16" flare x 1/4" adaptor (or 3/16" flare x 1/8" adaptor depending on your gauge) you can install the gauge on the high-pressure line that attaches to the nozzle assembly. then operate the fuel pump. once the pressure is up to 100 psi (or whatever pressure your burner is supposed to be set) allow the burner to go off on safety.
once the burner motor stops... observe the gauge. it should drop about 10 to 15% of the operating pressure. this is called the cut-off pressure. the cutoff pressure should hold for at least 5 minutes.
If the pressure does not cut off at a minimum of 80% of the operating value, the pump is defective and that is where your fuel leak is. If the pressure does cut-off at something above 80% then slowly lowers over time... same problem... replace the pump.Edward Young Retired
After you make that expensive repair and you still have the same problem, What will you check next?
1 -
Follow up:
I find this tool very helpful during service calls and tune-up work. while the gauge is on the high-pressure line I can check to see if the transformer spark is adequate(1), adjust the pump pressure up and down to see that the fuel pump adjustment is operating properly(2), set the proper pump pressure for the burner(3), see if the cut off is operating properly(4) and see how long the primary control takes to trip off on safety(5).
In less than 5 minutes I completed 5 of the 16 items on our oil burner tune-up list.Edward Young Retired
After you make that expensive repair and you still have the same problem, What will you check next?
3 -
@billcat
If you still have problems you could put a solenoid valve on or change to a pump with a solenoid. Then any dripping would be combustion related0 -
-
That burner already has a CleanCut fuel unit.EBEBRATT-Ed said:@billcat
If you still have problems you could put a solenoid valve on or change to a pump with a solenoid. Then any dripping would be combustion related
The primary control looks like an R7184B. If the fuel unit is OK, changing to a primary with post-purge (a.k.a. motor-off delay) could cool the nozzle enough to prevent after-drip.All Steamed Up, Inc.
Towson, MD, USA
Steam, Vapor & Hot-Water Heating Specialists
Oil & Gas Burner Service
Consulting1 -
In addition to the advice here, check out this service bulletin from Beckett about nozzle drip.https://beckettcorp.com/support/tech-bulletins/solving-nozzle-afterdrip/Weil-McLain Gold P-WTGO-4 DOM 07/09/96, rated 1.25 GPH
Beckett AFG Burner DOM 05/23/96, F4 Head
Delavan 1.0gph 80° B solid nozzle
10 Micron Westwood spin-on1 -
And Tiger Loop's excellent diagram of why air in the line leads to drip... westwoodproducts.com/tigerloop_article.htmWeil-McLain Gold P-WTGO-4 DOM 07/09/96, rated 1.25 GPH
Beckett AFG Burner DOM 05/23/96, F4 Head
Delavan 1.0gph 80° B solid nozzle
10 Micron Westwood spin-on1 -
This is to billcat I learned this in a Beckett class in 1986. the Chamber heats up so hot, that on small chambers fine oil droplets push back up the blast tube and run backwards into the housing.
Beckett’s answer to this was to wipe high heat red silicone with your finger. Reach inside blast tube and wipe silicone from 9 o clock to 3 o clock position. This will stop oil from entering the housing and dripping oil under housing through weep hole.
I hope I have explained remedy well. Put heavy bead of silicone with pointer finger. Please let me know your result. This is 3 Rd time I ever heard of this problem. Thank you
Eric Haywood1 -
I don't see how that would work. The nozzle sits back from the end of the air tube (blast tube=old thinking). If it drips, it's suppose to roll out the weep hole, that's why it's there.
Post purge, and an oil valve will stop the drip, it that is what's happening. But the other things mentioned in my first post should be addressed first, including making sure there are no vacuum leaks (sucking in air) and a full power bleed.There was an error rendering this rich post.
1 -
In it's design it's always been a problem . Smaller nozzle assembly tube like in a Riello would work . Beckett redesign it's nozzle adepter with small top slot to help with the air elimination back the early 80's .. With the post WW2 burners we use to cut up metal coat hangers and shove the lengths into the tubes to to increase velocity to help remove air ..
There was an error rendering this rich post.
0 -
@Big Ed_4
Your right I have seen burners with a piece of welding rod inside the 1/4 or 1/8 nozzle pipe to take up space and eliminate air in the gun assembly which causes dripping. The nozzle pipe only has to pass enough oil that the nozzle will pass.
If the burner is pitched right (a lot are not), solenoid or clean cut and tight oil lines (here comes the tiger loop)0 -
Second nature to use now . After 40 years with the AF Beckett we know to pitch in inward . Funny that I remembered adding rods to nozzle tubes . I recall the old timers, when I was young saying to me "I forgot more then you know " Ok but now a days I forget where I put that fitting I just pulled a minute ago ....
There was an error rendering this rich post.
0 -
> @Big Ed_4 said:
> Second nature to use now . After 40 years with the AF Beckett we know to pitch in inward . Funny that I remembered adding rods to nozzle tubes . I recall the old timers, when I was young saying to me "I forgot more then you know " Ok but now a days I forget where I put that fitting I just pulled a minute ago ....
That's awesome! A phrase I remember from my first boss as now use myself. I guess it's a right of passage of sorts. If nothing else, I get to say it to my boys. His version was "I forgot what you don't even know yet. Now run up to 7-11, get me a Light No Sugar and 2 packs of Marlboro Red. And whatever you want."0 -
I guess all of us that learned from an old timer, the right of passage that opened the door to the knowledge we were taught, was first to get his coffee and cigarettes right. then he will teach.0
-
I learned by alot from old timers over the years and some of what they taught me were wrong to be honest ...You have two ears and one mouth so use your ears twice as much , Ask questions . keep a open mind , After a few years working on equitment . Take advantage of seminars . Besides the free lunch you will always pick up a tool call knowledge.
There was an error rendering this rich post.
0
Categories
- All Categories
- 87K THE MAIN WALL
- 3.2K A-C, Heat Pumps & Refrigeration
- 58 Biomass
- 426 Carbon Monoxide Awareness
- 113 Chimneys & Flues
- 2.1K Domestic Hot Water
- 5.7K Gas Heating
- 109 Geothermal
- 161 Indoor-Air Quality
- 3.6K Oil Heating
- 70 Pipe Deterioration
- 994 Plumbing
- 6.3K Radiant Heating
- 391 Solar
- 15.4K Strictly Steam
- 3.4K Thermostats and Controls
- 55 Water Quality
- 44 Industry Classes
- 48 Job Opportunities
- 18 Recall Announcements