Welcome! Here are the website rules, as well as some tips for using this forum.
Need to contact us? Visit https://heatinghelp.com/contact-us/.
Click here to Find a Contractor in your area.
Steam Humidification Boilers - Wet steam under high demand? Fulton 40HP
Options
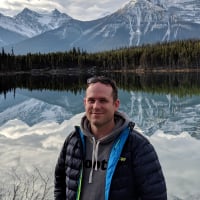
SuperJ
Member Posts: 609
My day job is a controls tech working on commercial HVAC systems.
I've got an issue with a some steam humidification boilers. The boilers are Fulton 40hp steam boilers (I think around 1200lb/hr), running at 11psi, they have a 5:1 turn down ratio. They serve several large air handlers for humidification. The issue I've observed is that at high fire with the humidifier valves open past 70% the steam quality seems to suffer. I observe a lot of water pouring out of the remote traps to drain, and my steam meter (I think it's a vortex) reading goes crazy. The remote condensate goes to drain (there is some tempering valves to add cold water).
The feed water has multiple softeners and de-alkalizers, and some sort of water treatment chemical systems. The boiler manufacture rep and the water quality rep both say everything looks good as far they are concerned.
If I run both boiler simultaneously and limit the valve position to 70% the problem goes away.
Since this is commercial steam at 11psi the best practices might be a bit different, but I wondered if any could comment on any red flags they see in the pictures. I could go back and talk to the mechanical contractor.
Two things I wonder about.
1. There is some sort of swing valve above each boiler (is it some sort of check valve?), is this ok and necessary?
2. The steam outlet goes up from each boiler, over to the left and down to a header. The two big pipes to the right on the header are the inlets from the boilers, the pipes to the left are takeoffs to feed the humidifiers. My concern is the condensate outlet (bottom right). It appears to go thru a trap, and then up and then into the feedwater tank. Is it ok to push the condensate up like this?
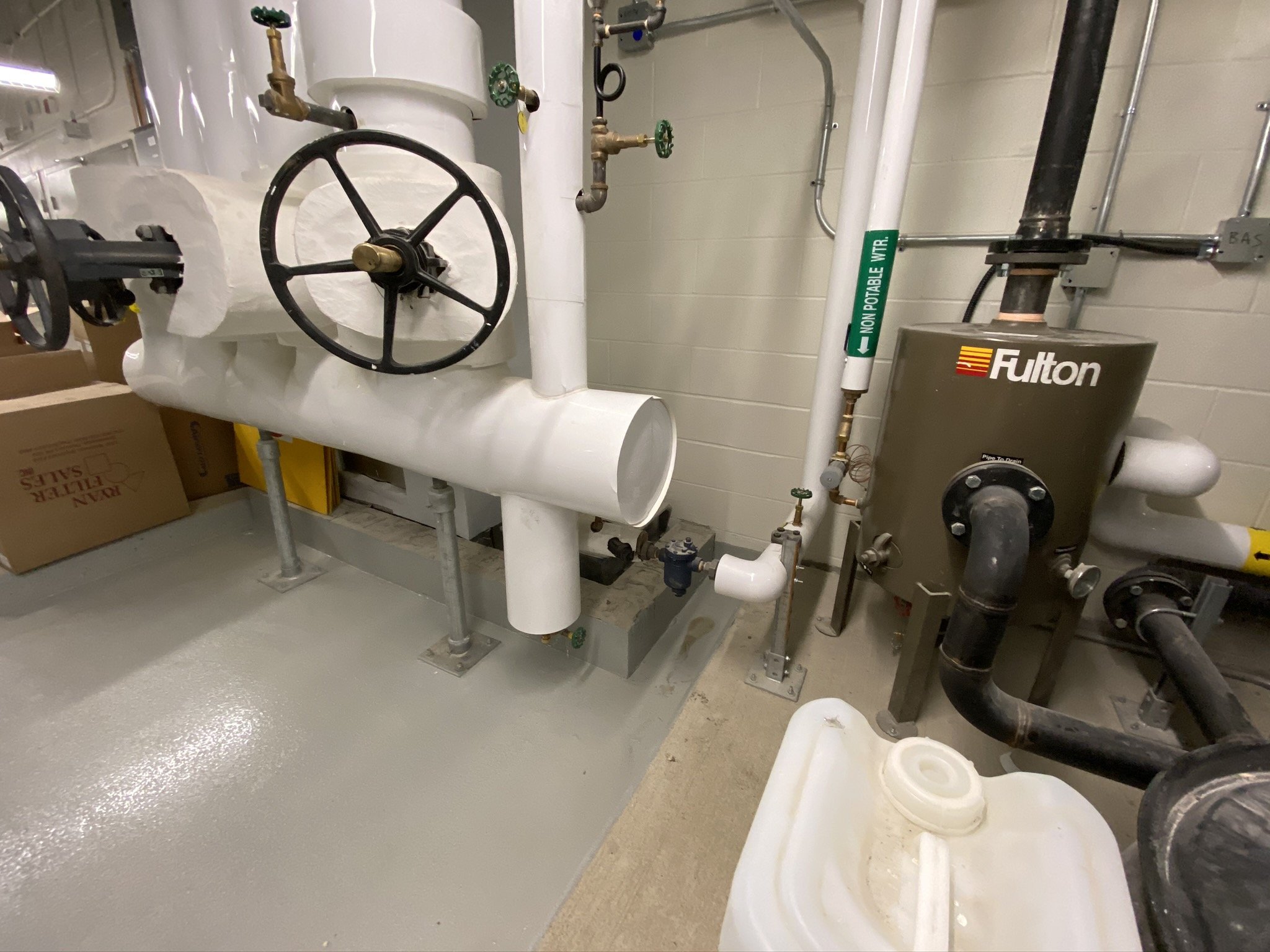
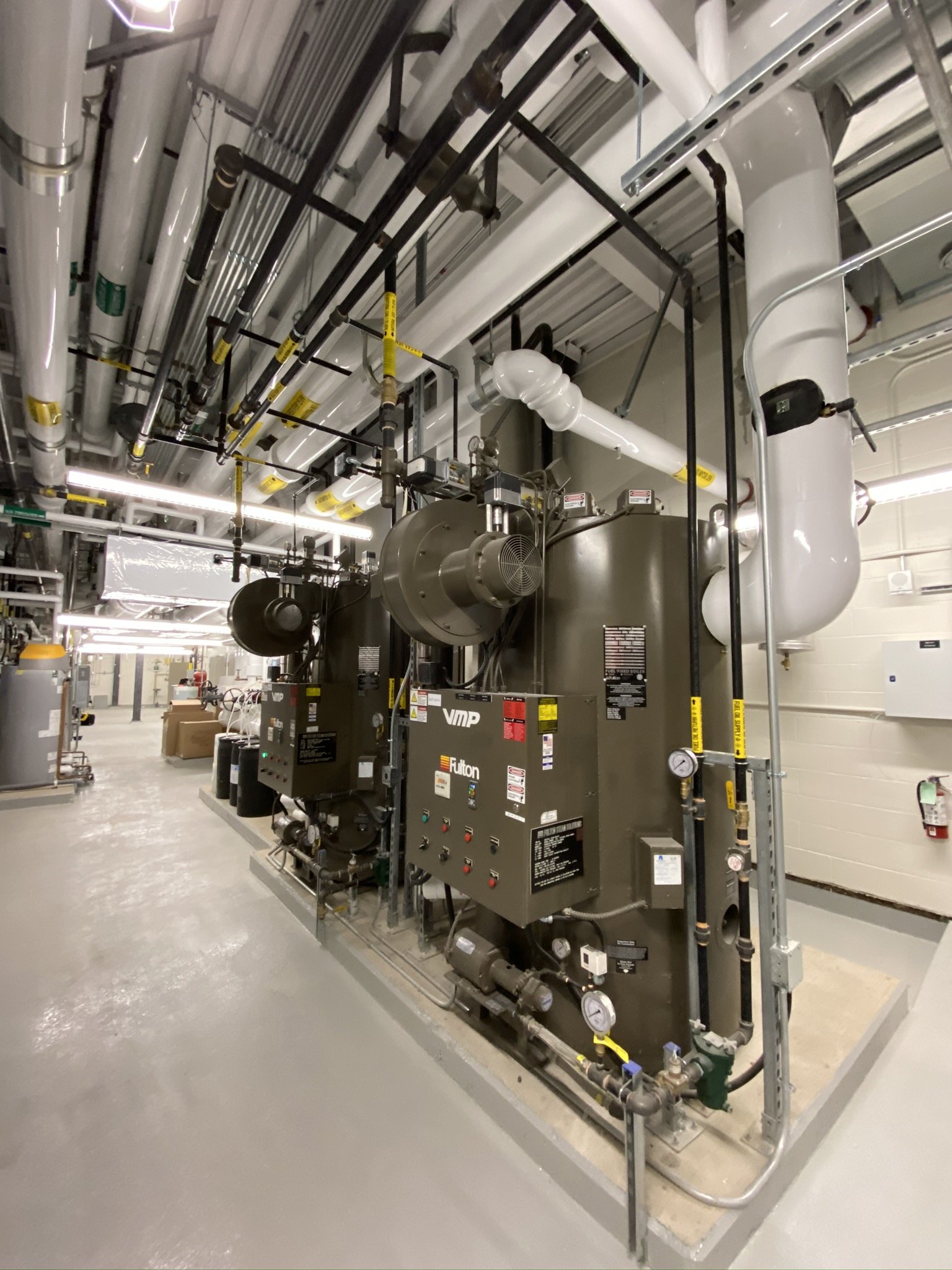
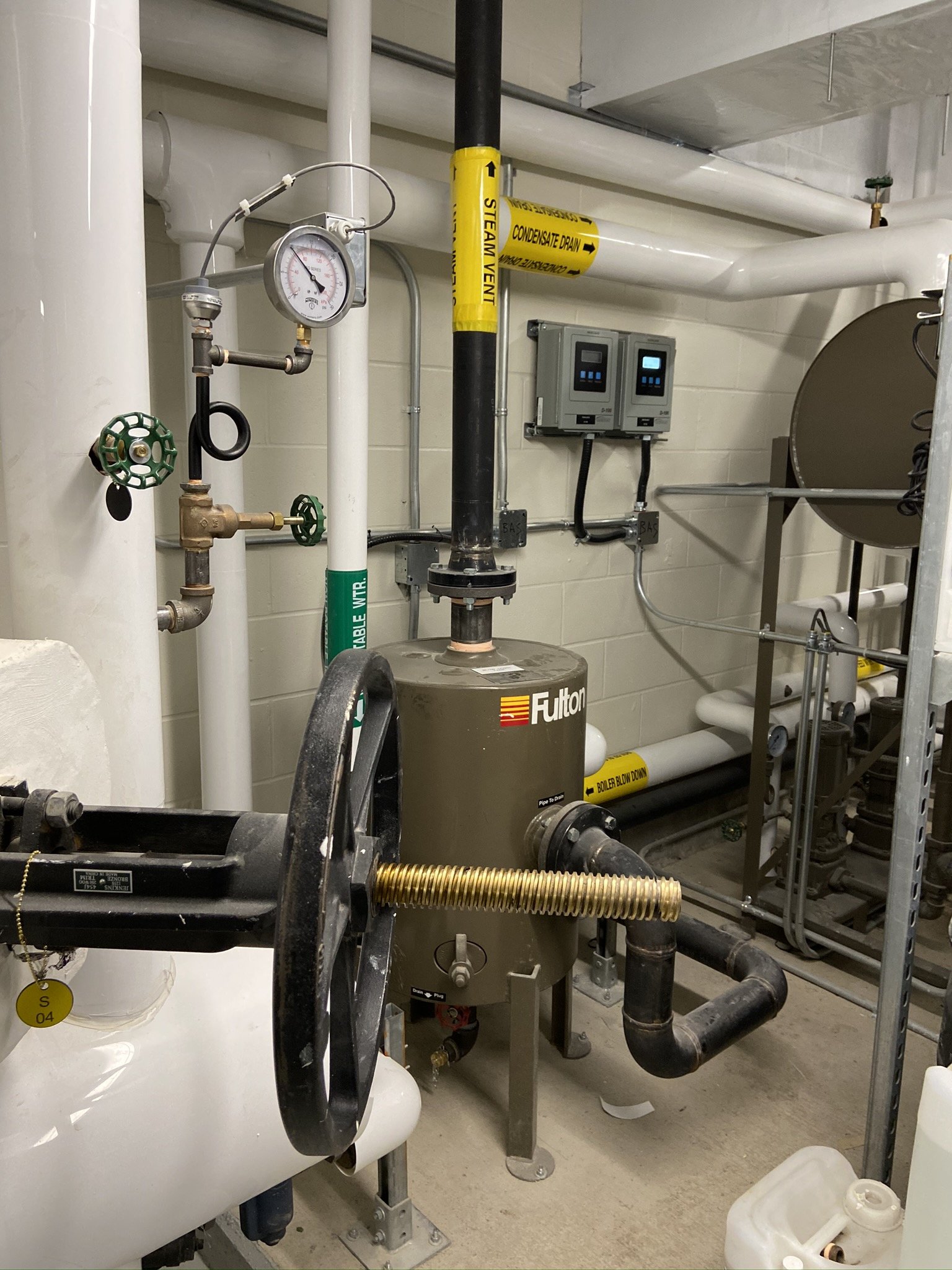
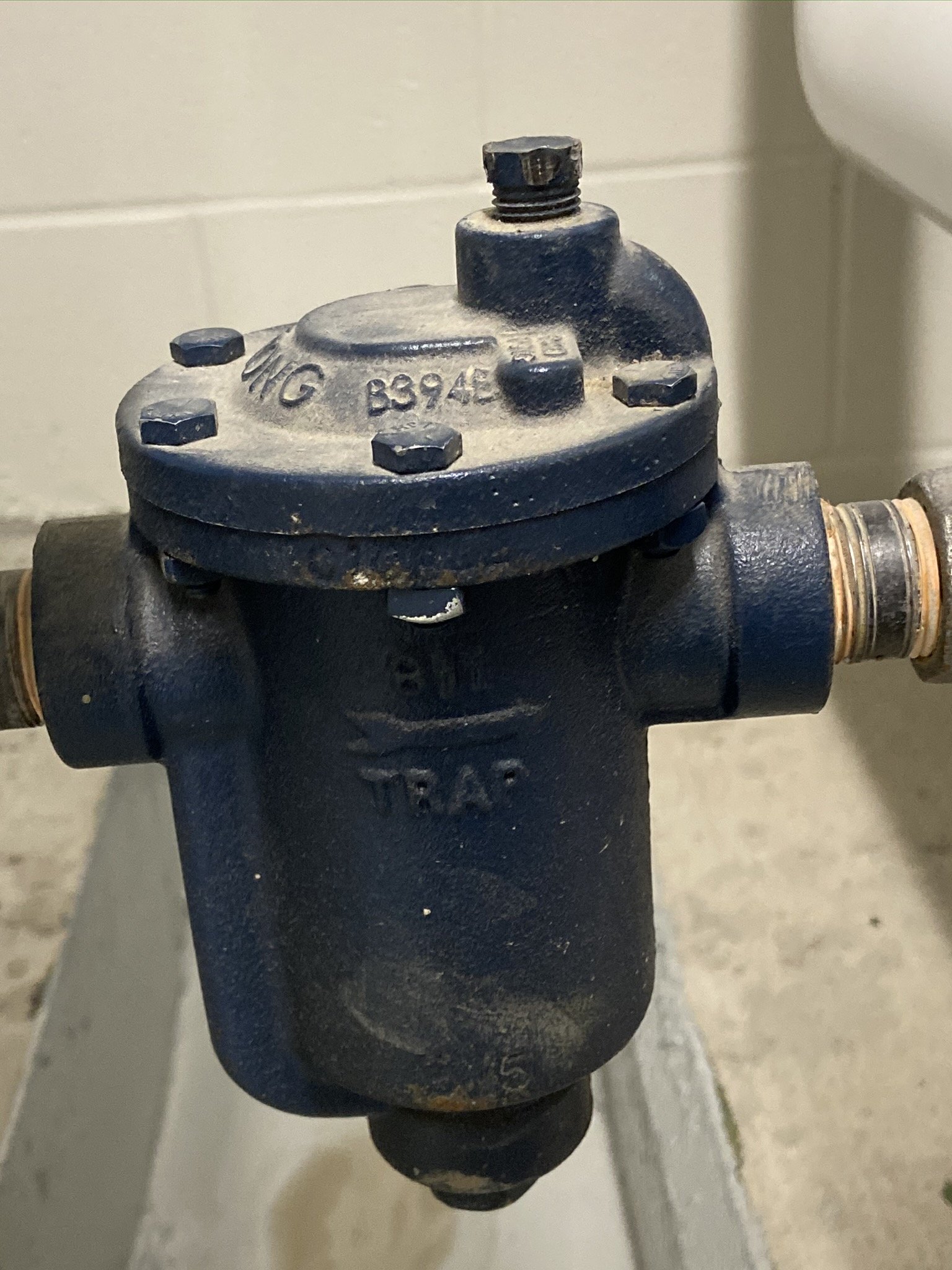
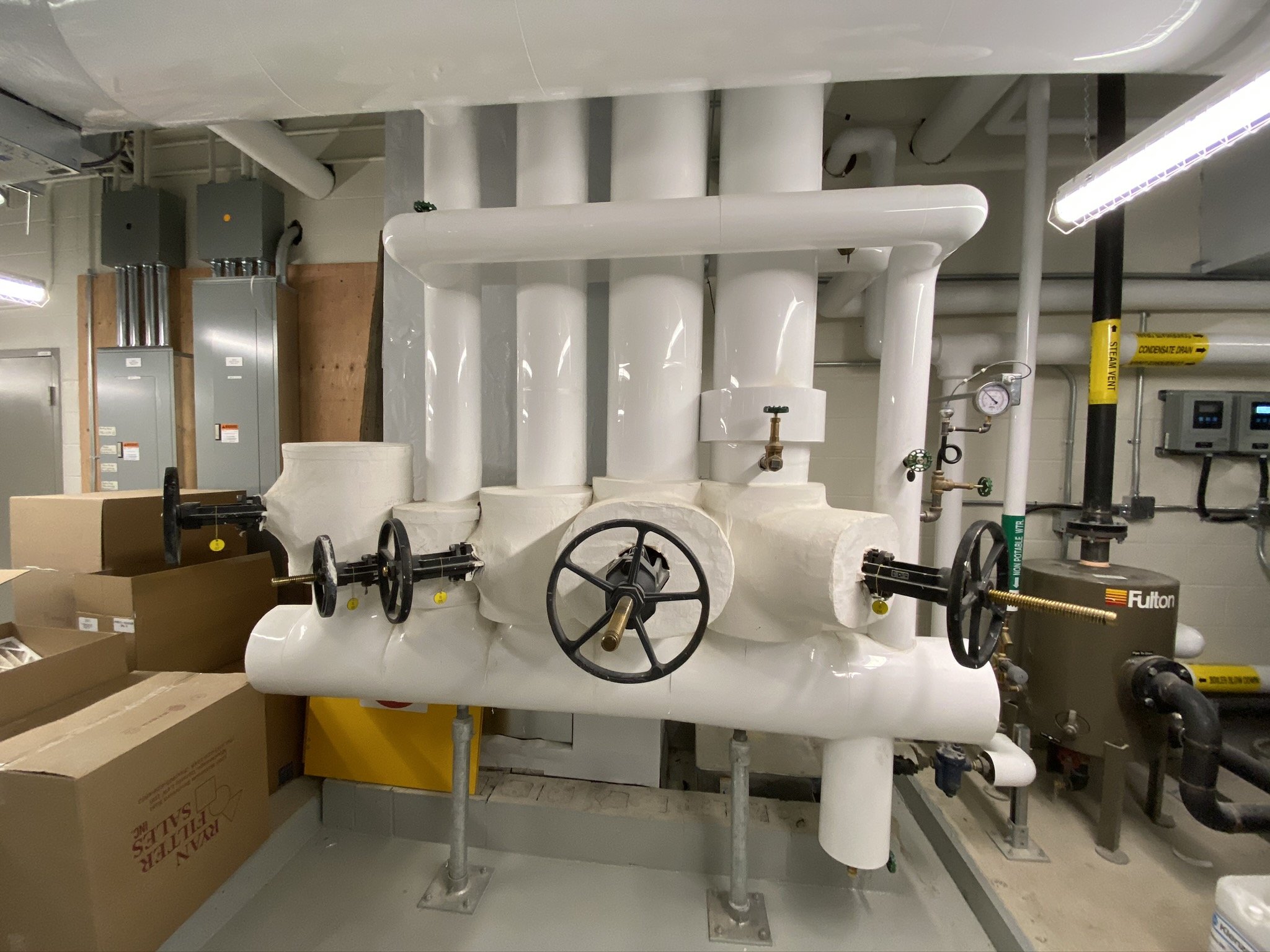
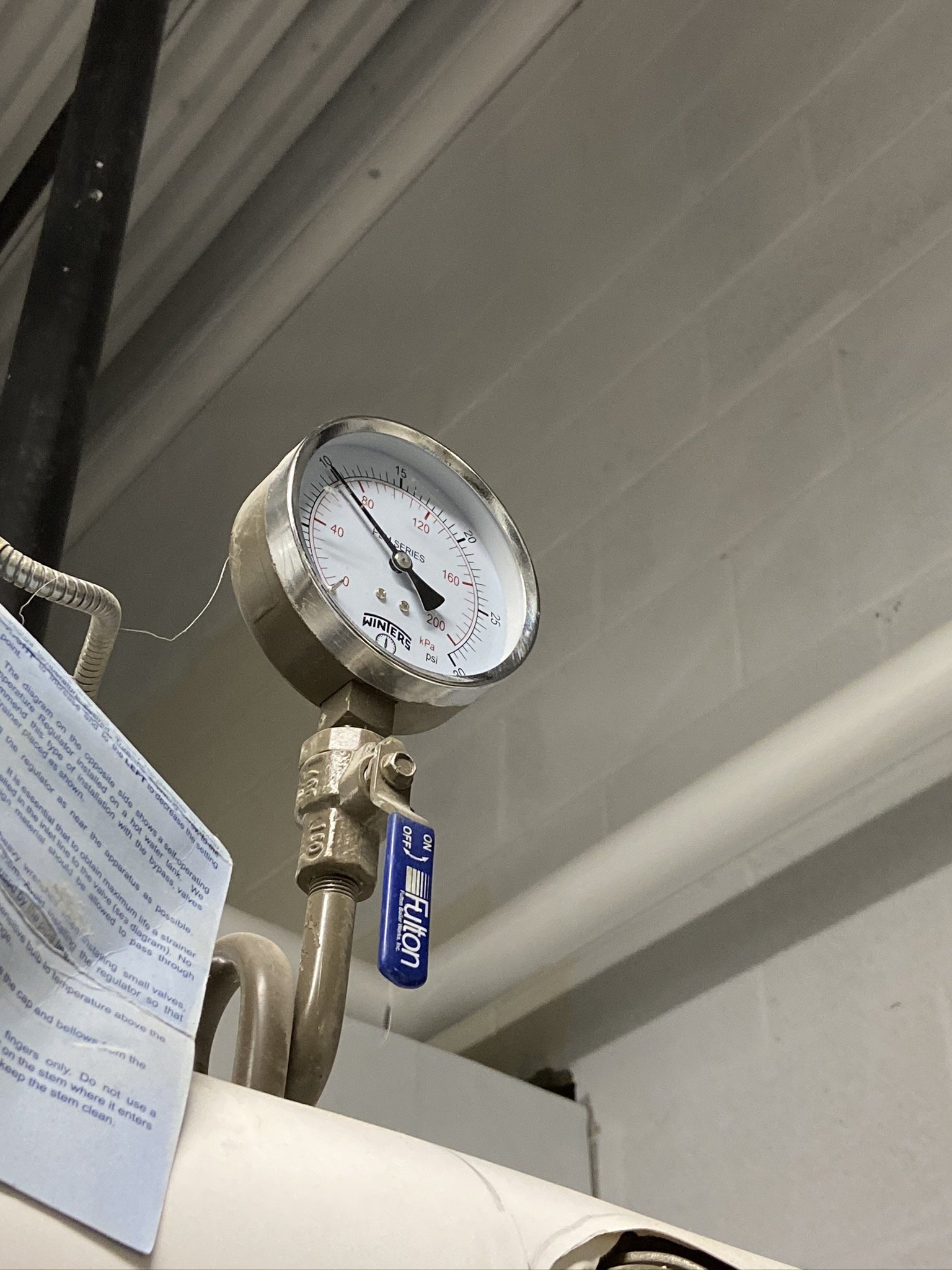
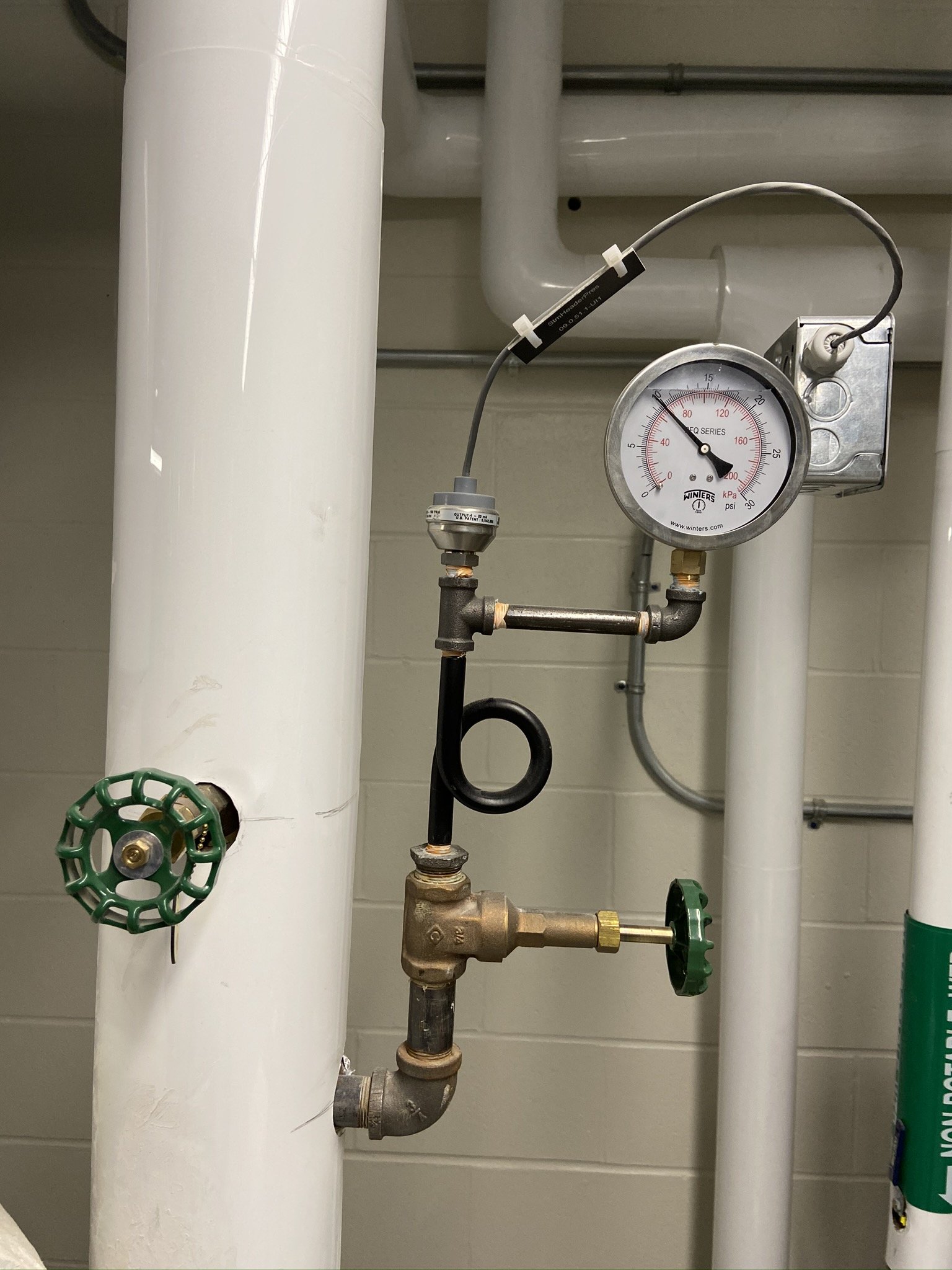
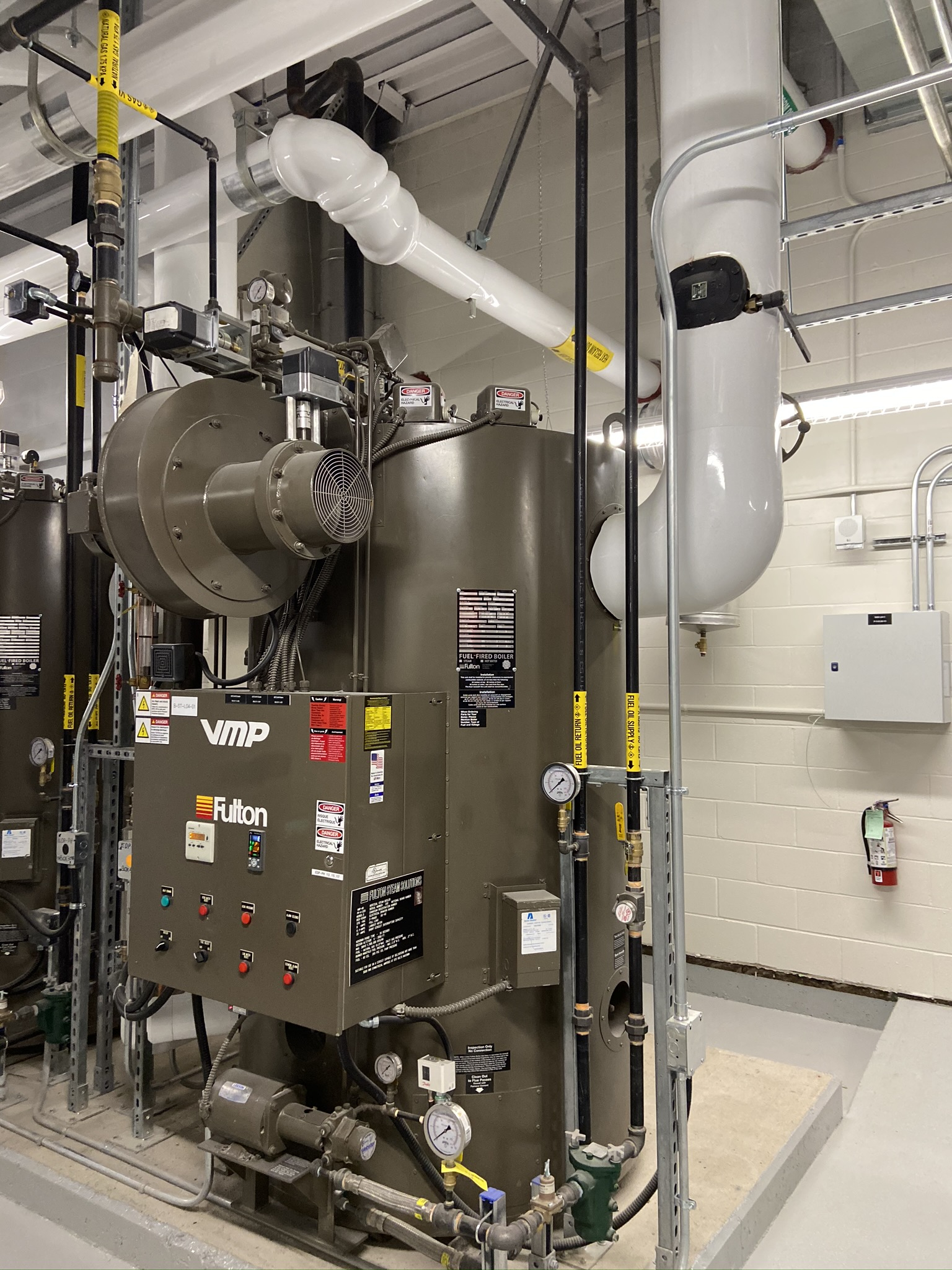
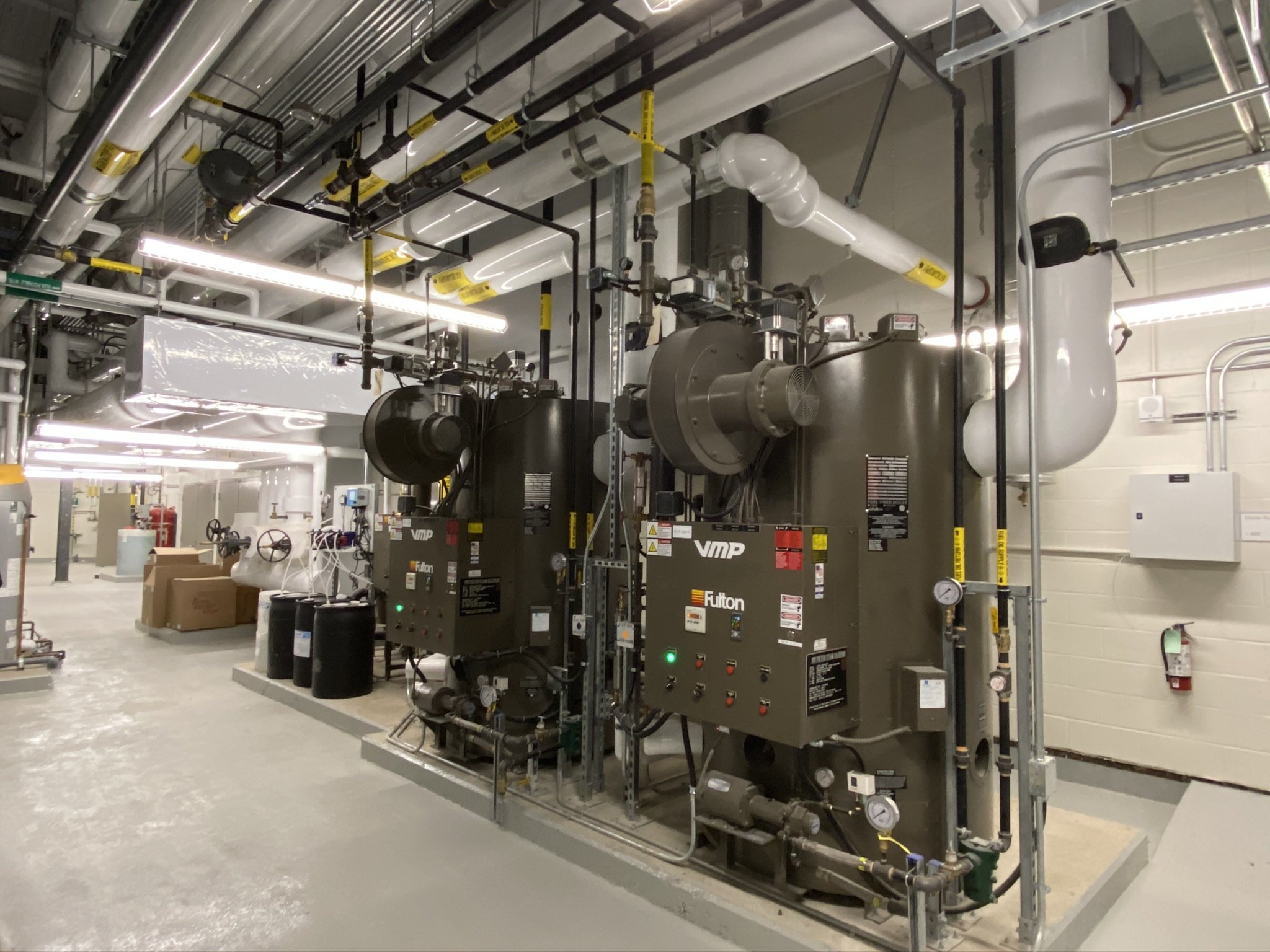
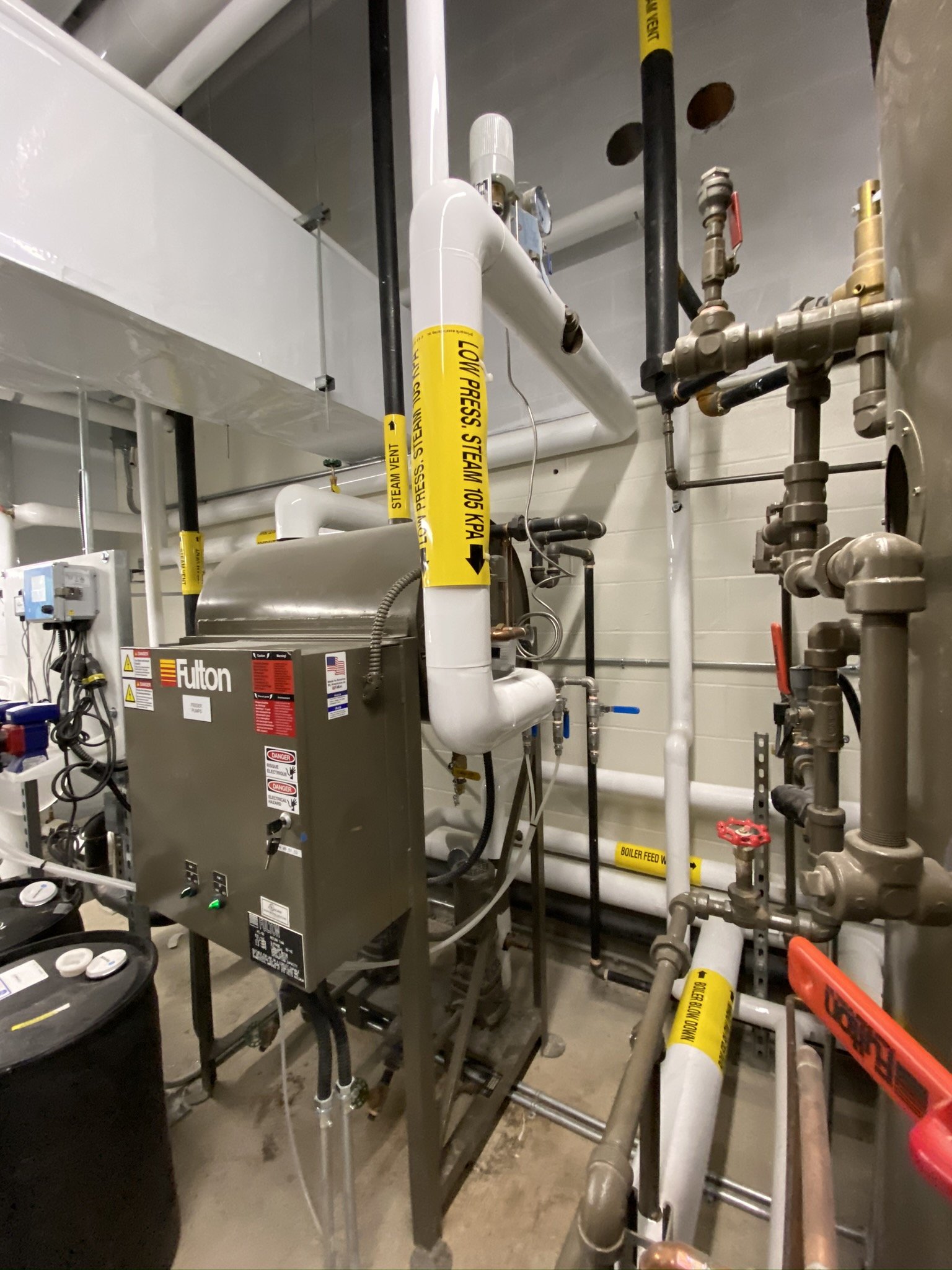
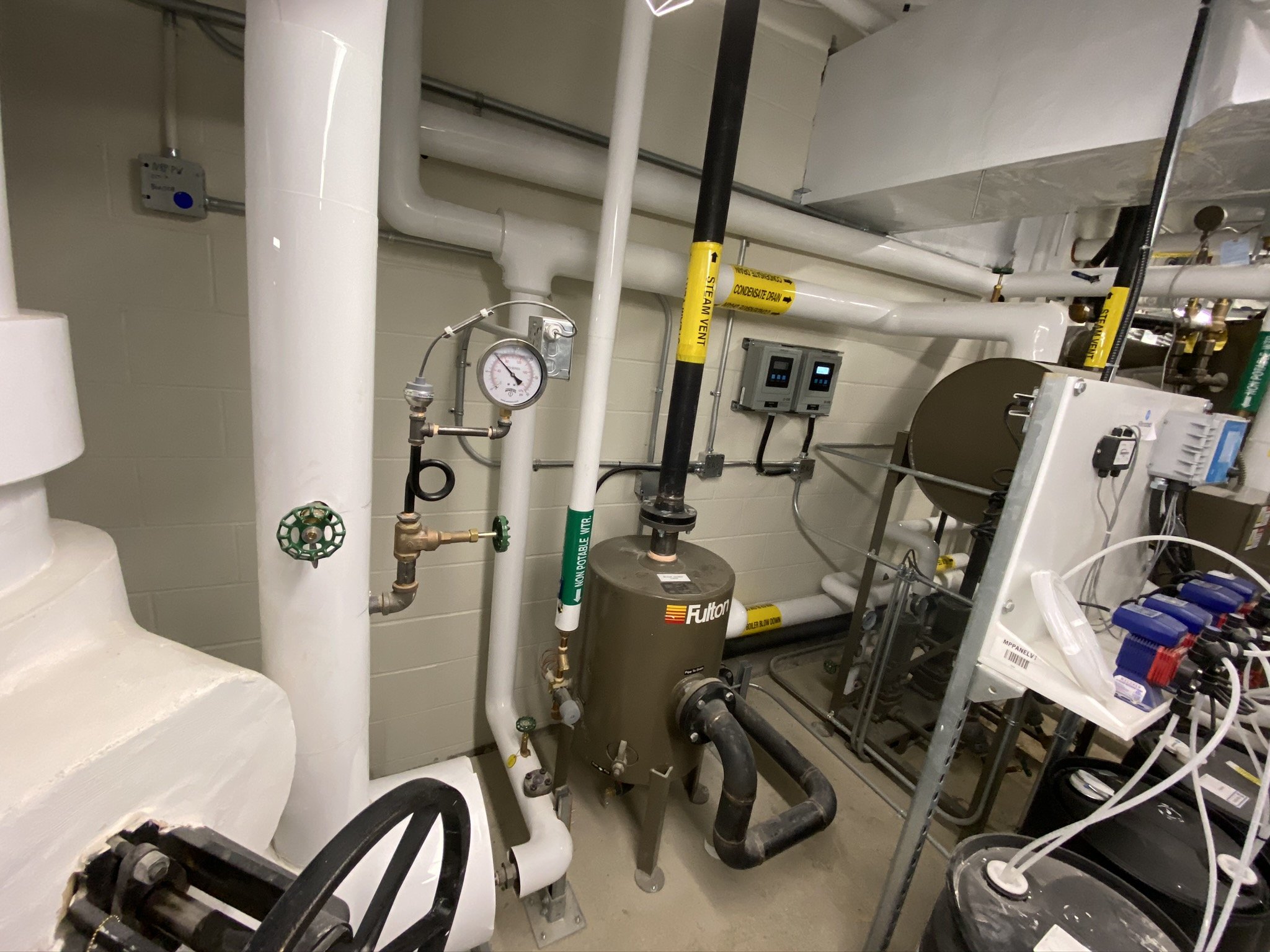
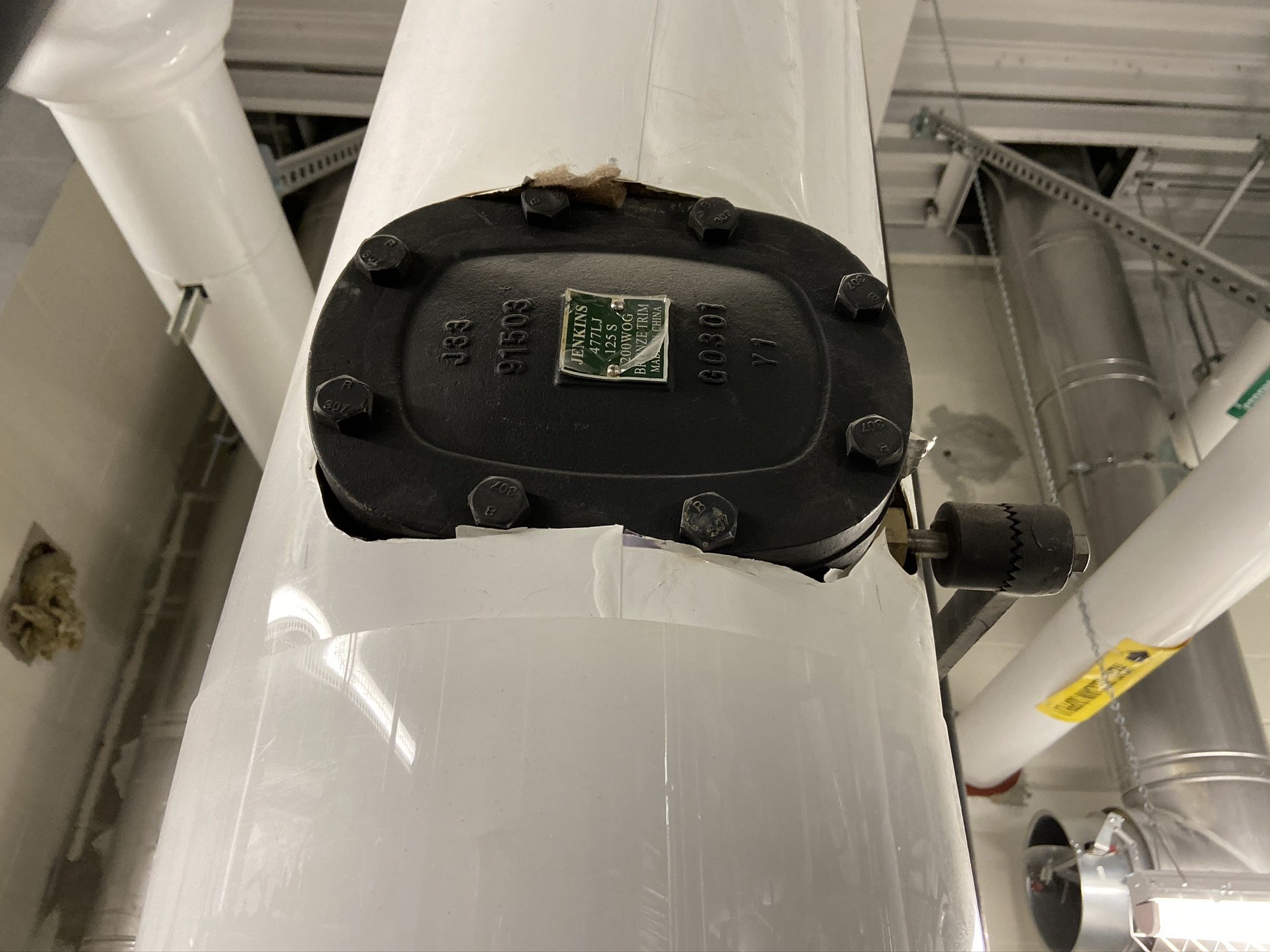
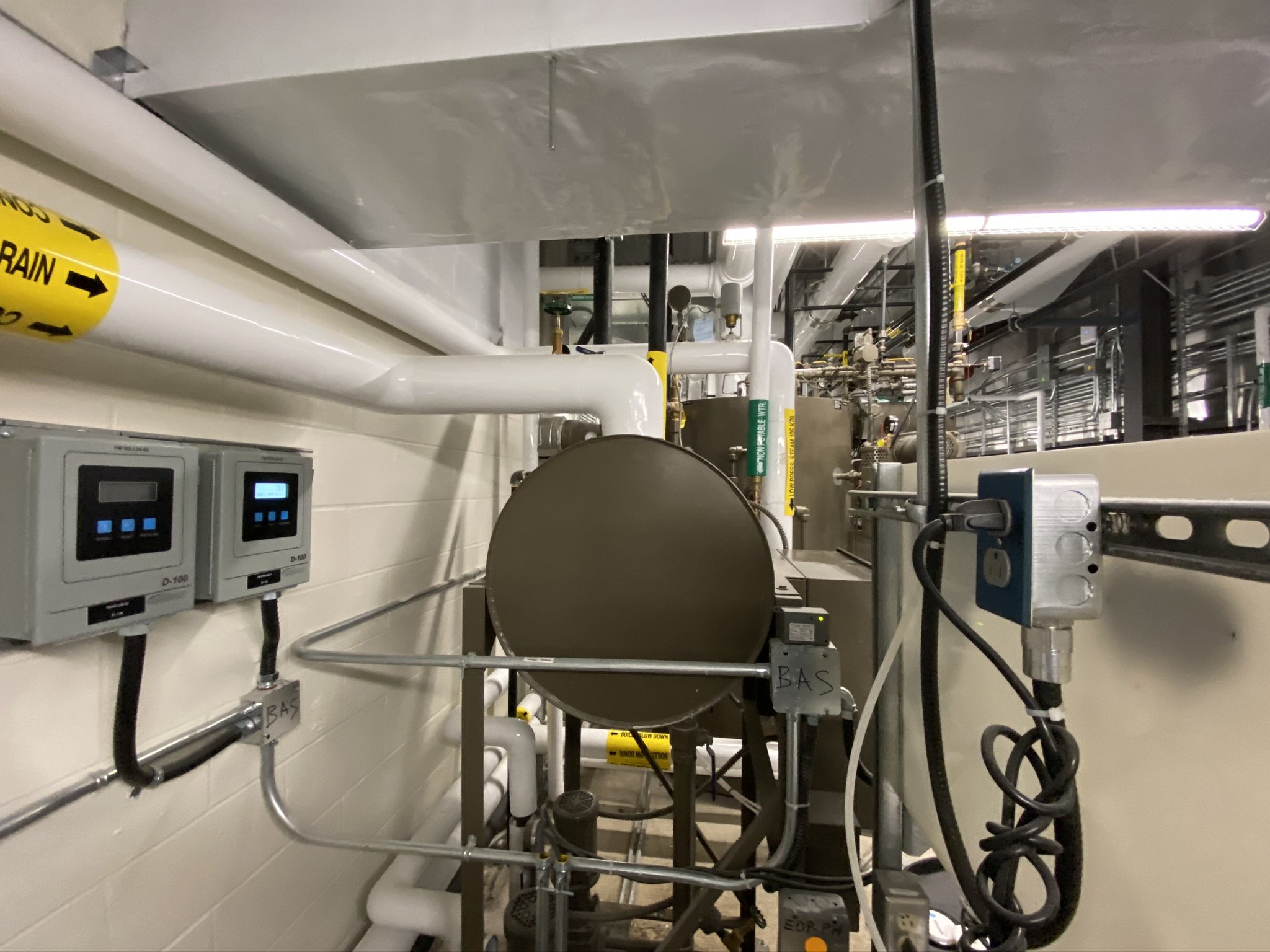
I've got an issue with a some steam humidification boilers. The boilers are Fulton 40hp steam boilers (I think around 1200lb/hr), running at 11psi, they have a 5:1 turn down ratio. They serve several large air handlers for humidification. The issue I've observed is that at high fire with the humidifier valves open past 70% the steam quality seems to suffer. I observe a lot of water pouring out of the remote traps to drain, and my steam meter (I think it's a vortex) reading goes crazy. The remote condensate goes to drain (there is some tempering valves to add cold water).
The feed water has multiple softeners and de-alkalizers, and some sort of water treatment chemical systems. The boiler manufacture rep and the water quality rep both say everything looks good as far they are concerned.
If I run both boiler simultaneously and limit the valve position to 70% the problem goes away.
Since this is commercial steam at 11psi the best practices might be a bit different, but I wondered if any could comment on any red flags they see in the pictures. I could go back and talk to the mechanical contractor.
Two things I wonder about.
1. There is some sort of swing valve above each boiler (is it some sort of check valve?), is this ok and necessary?
2. The steam outlet goes up from each boiler, over to the left and down to a header. The two big pipes to the right on the header are the inlets from the boilers, the pipes to the left are takeoffs to feed the humidifiers. My concern is the condensate outlet (bottom right). It appears to go thru a trap, and then up and then into the feedwater tank. Is it ok to push the condensate up like this?
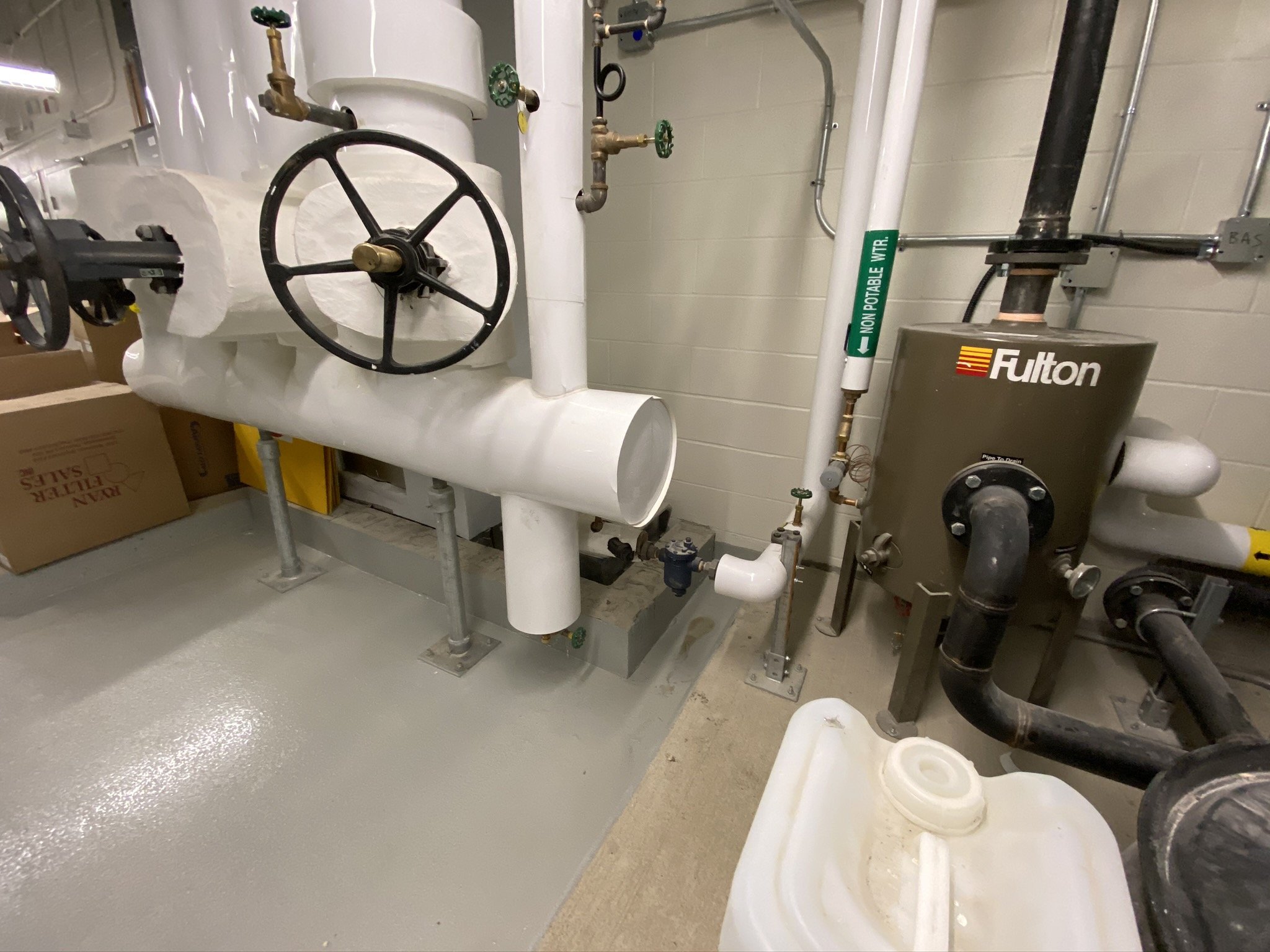
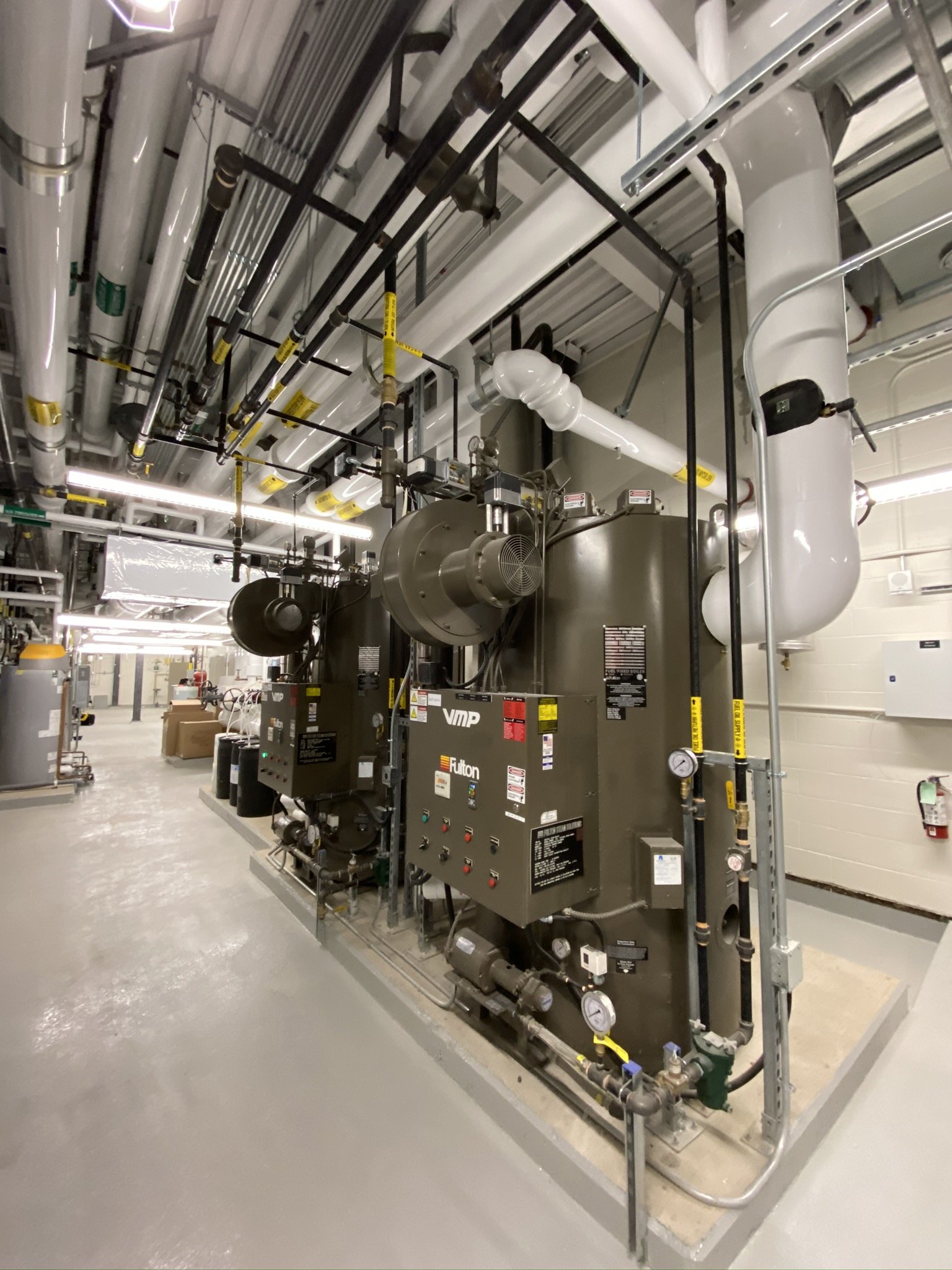
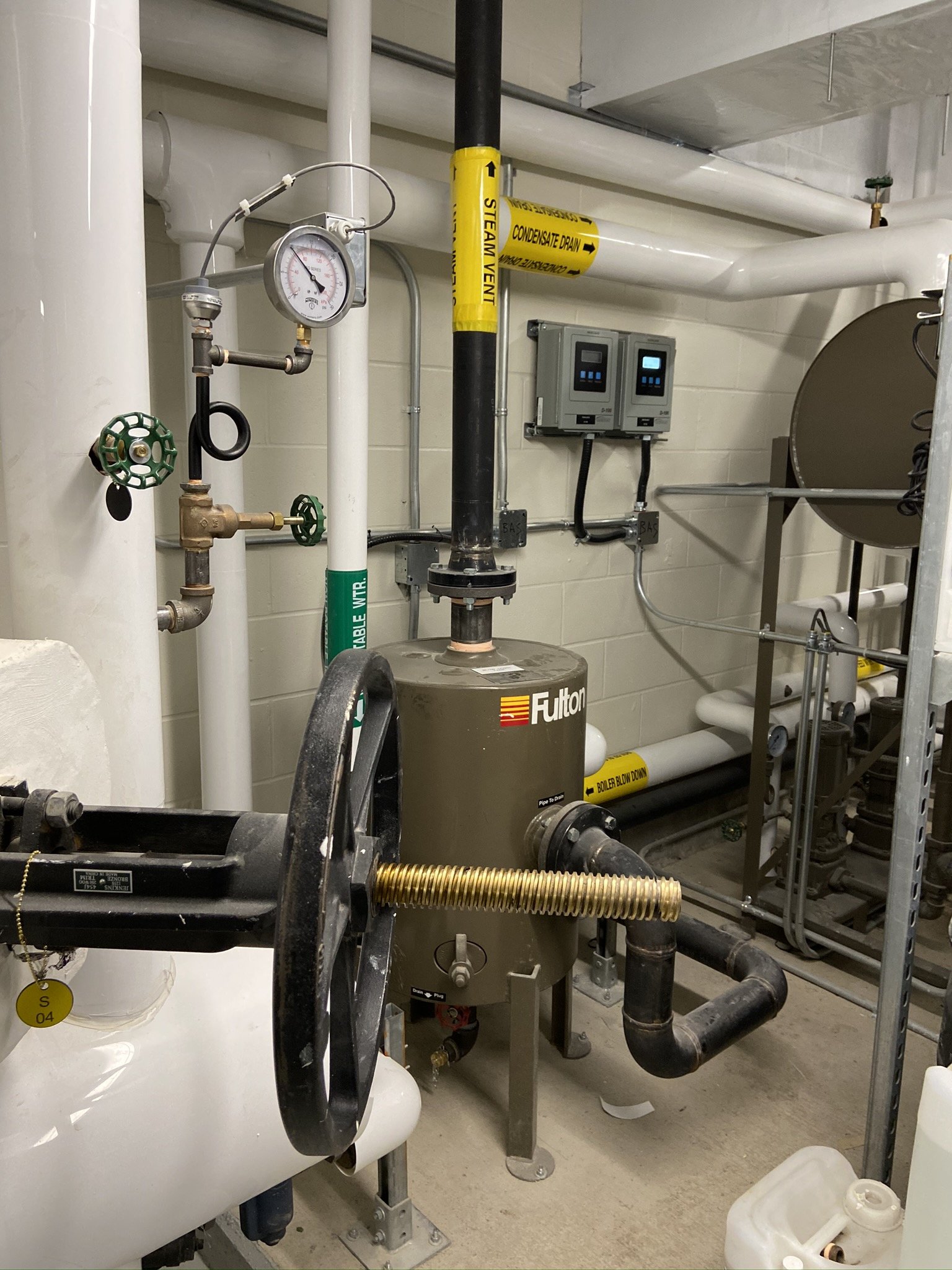
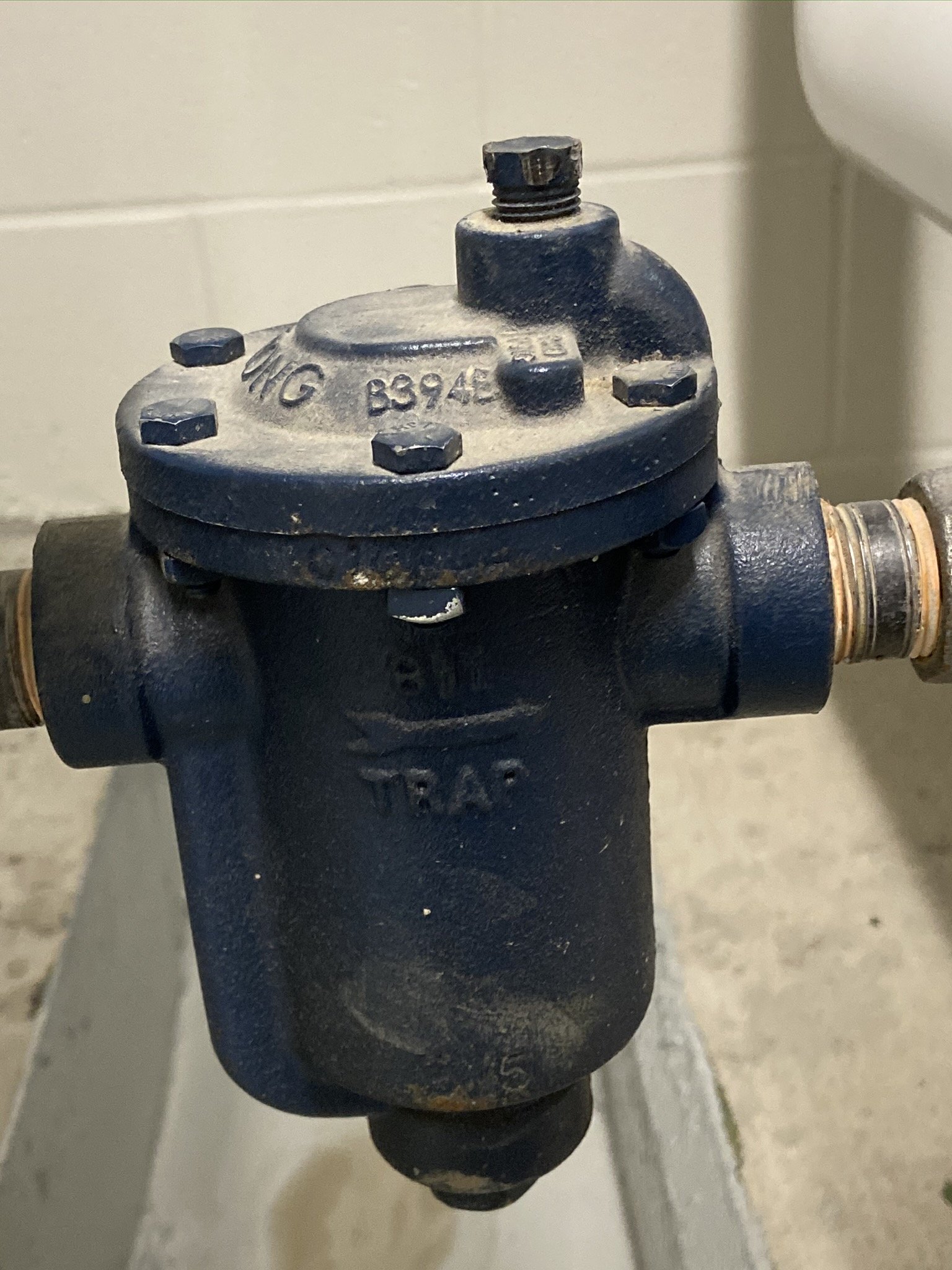
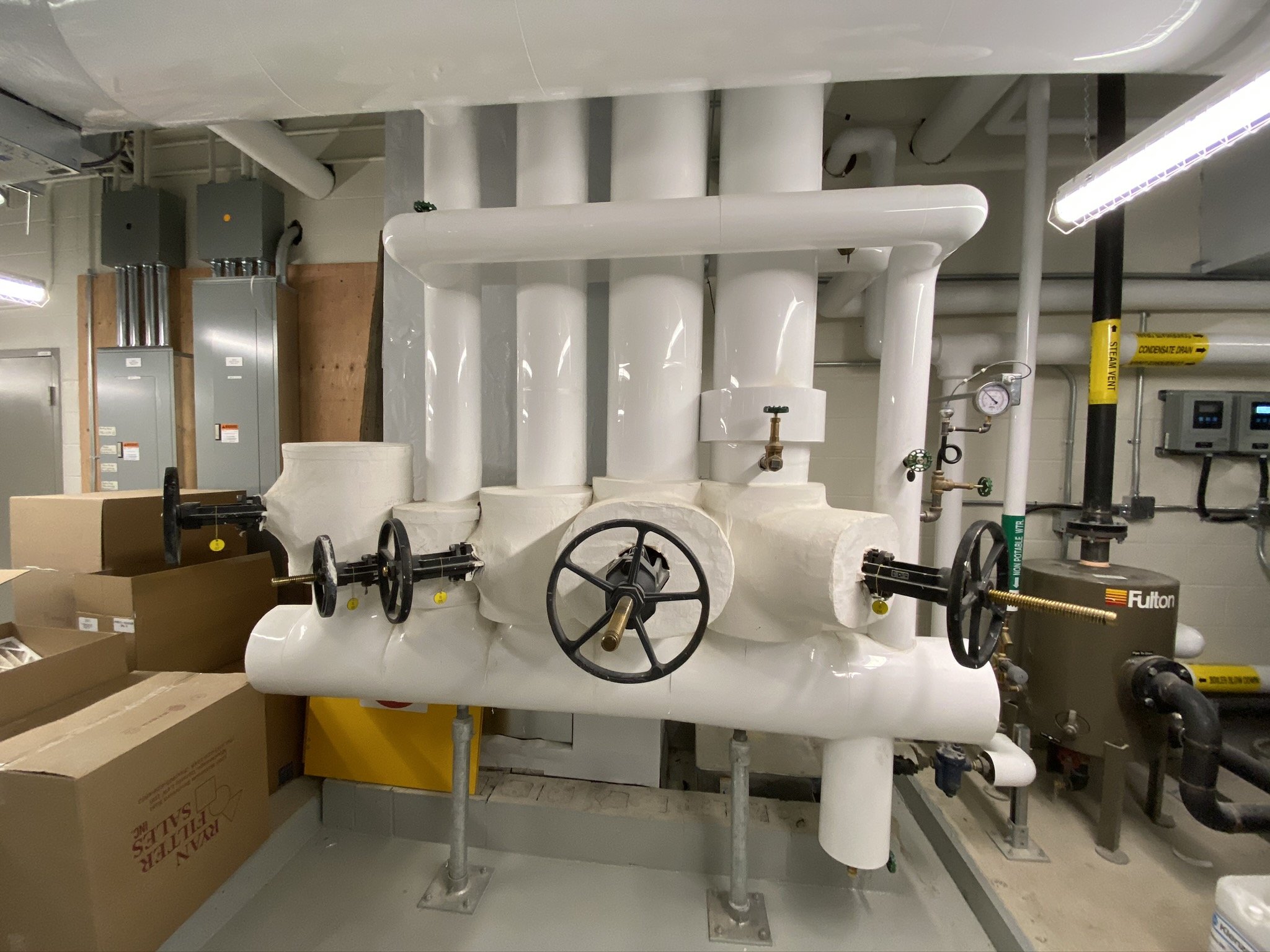
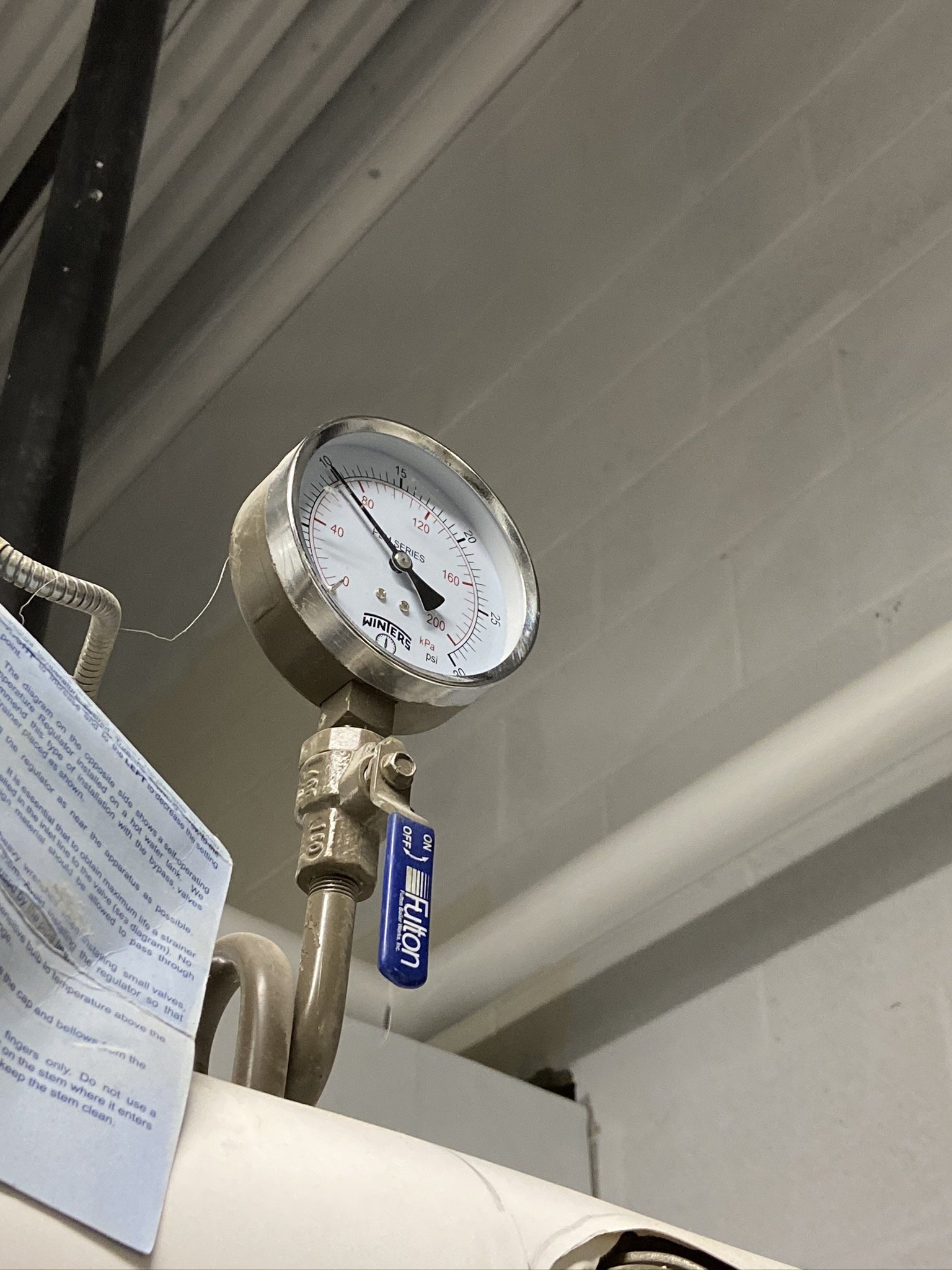
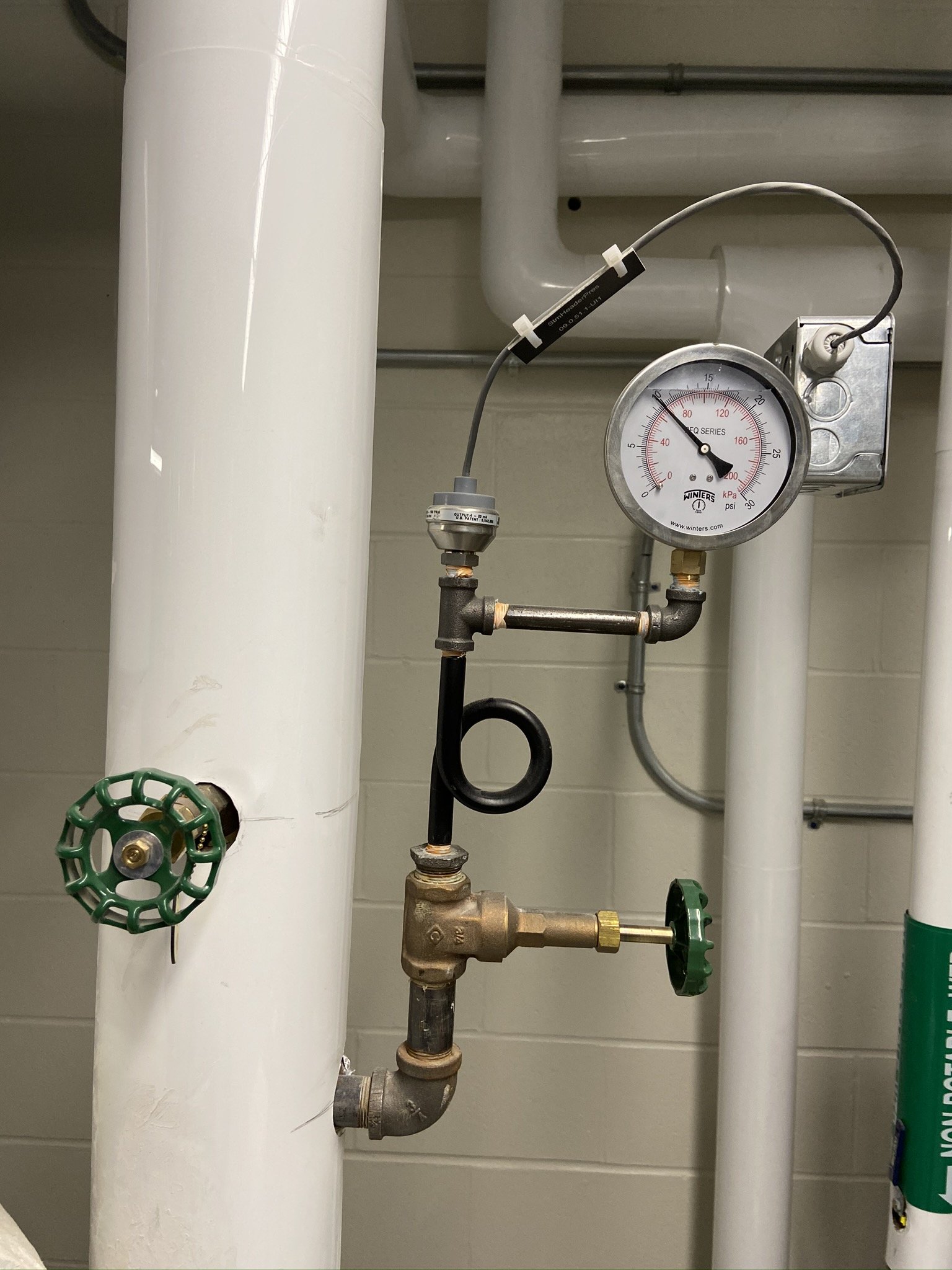
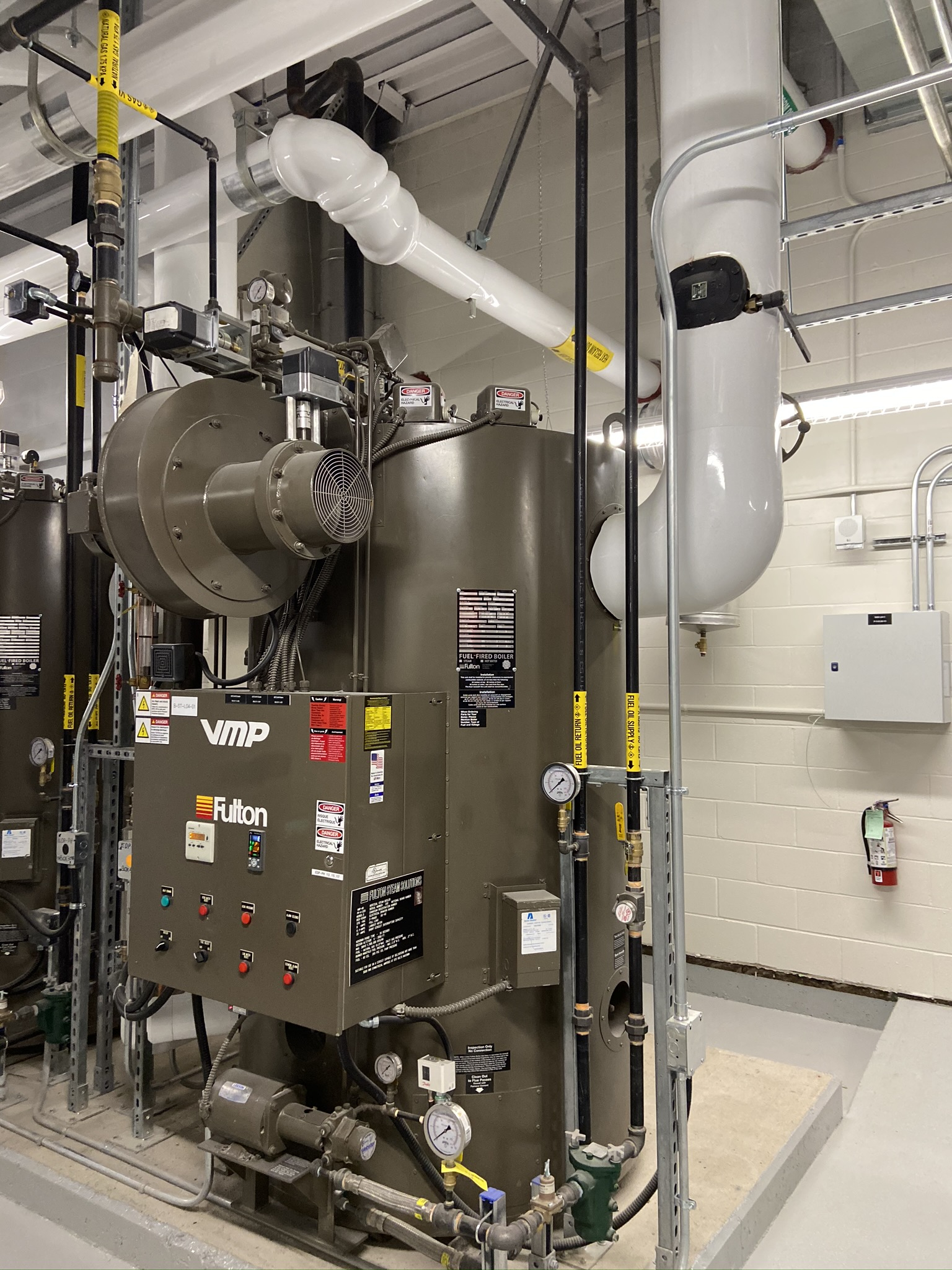
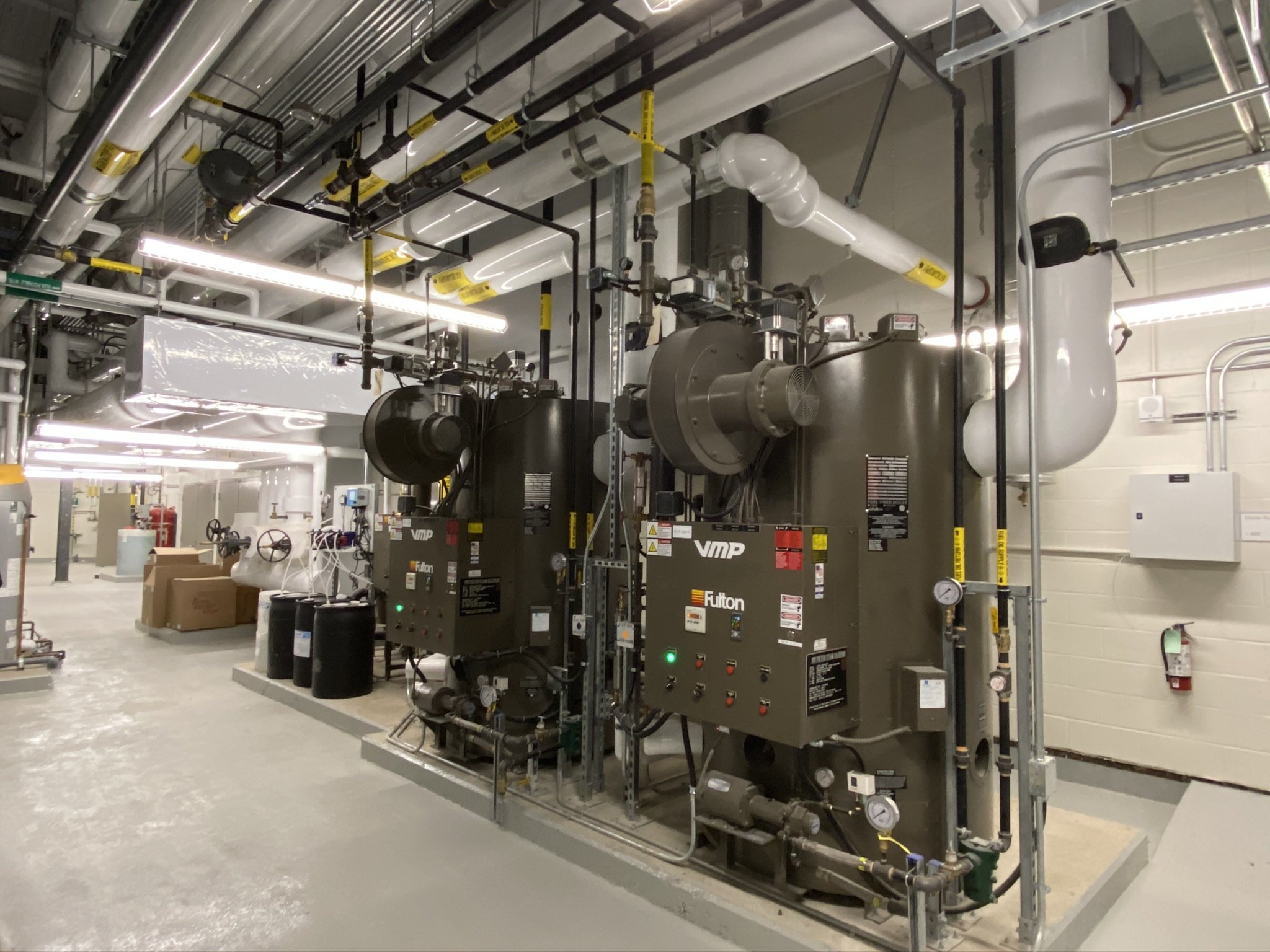
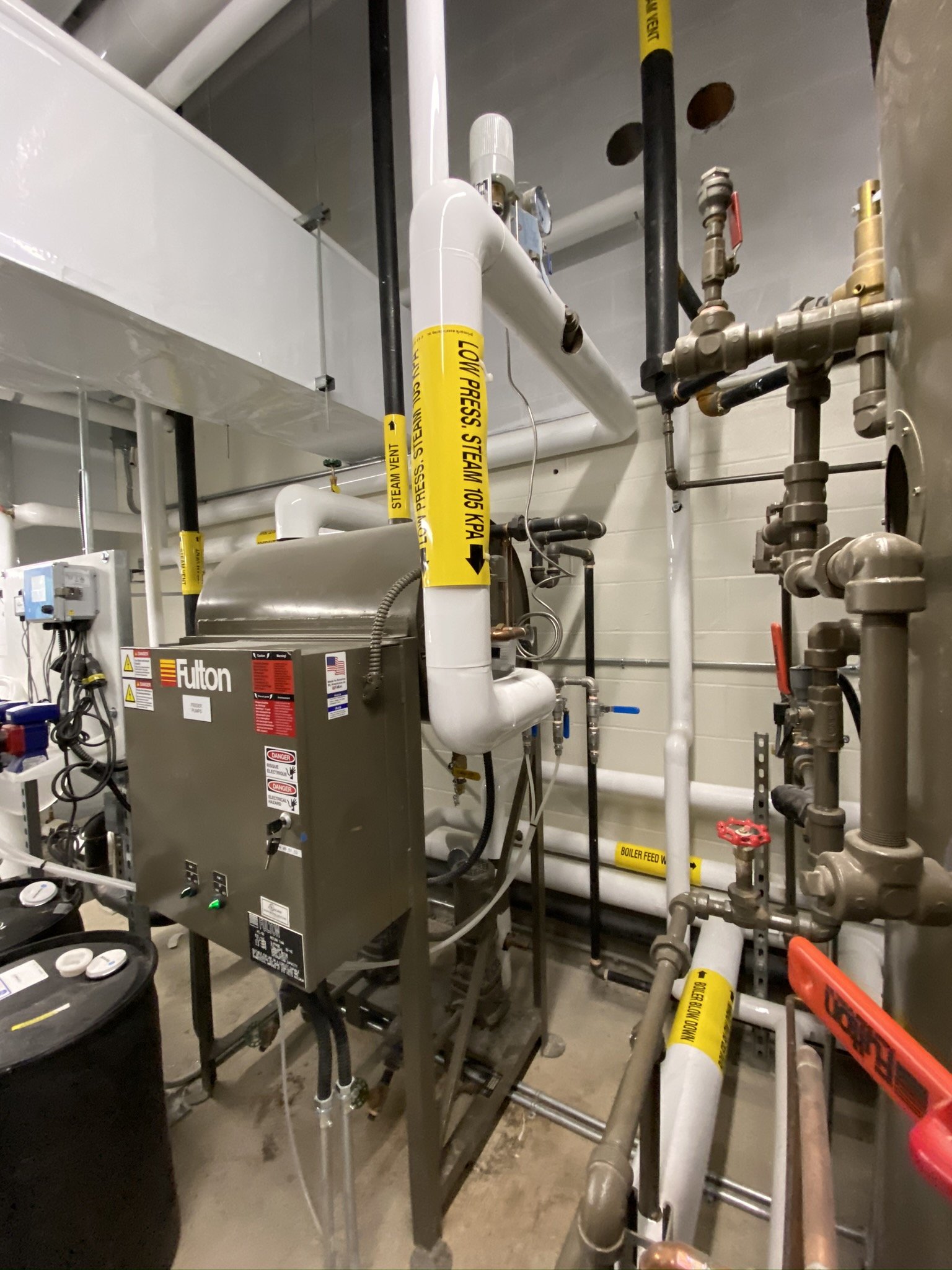
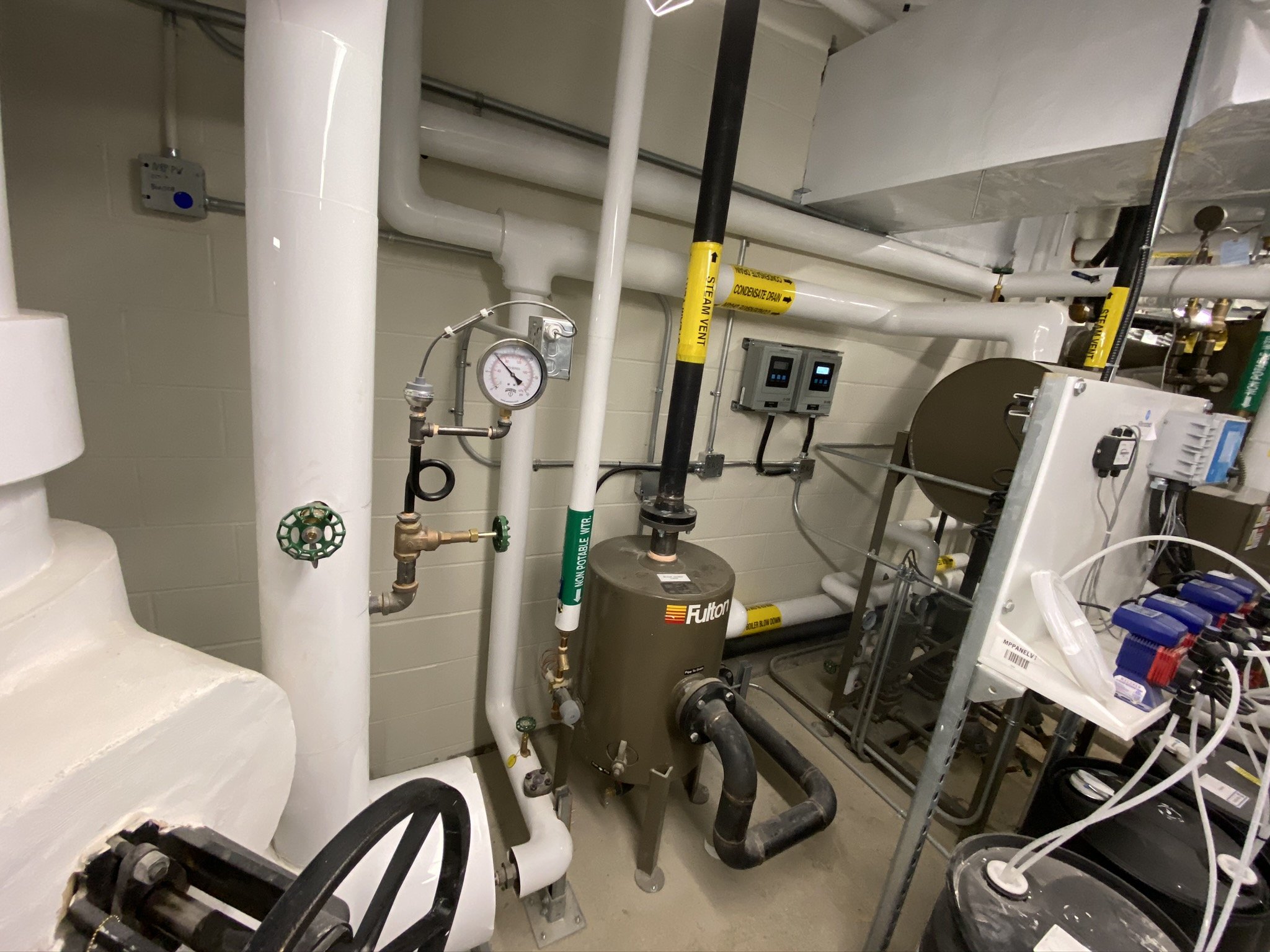
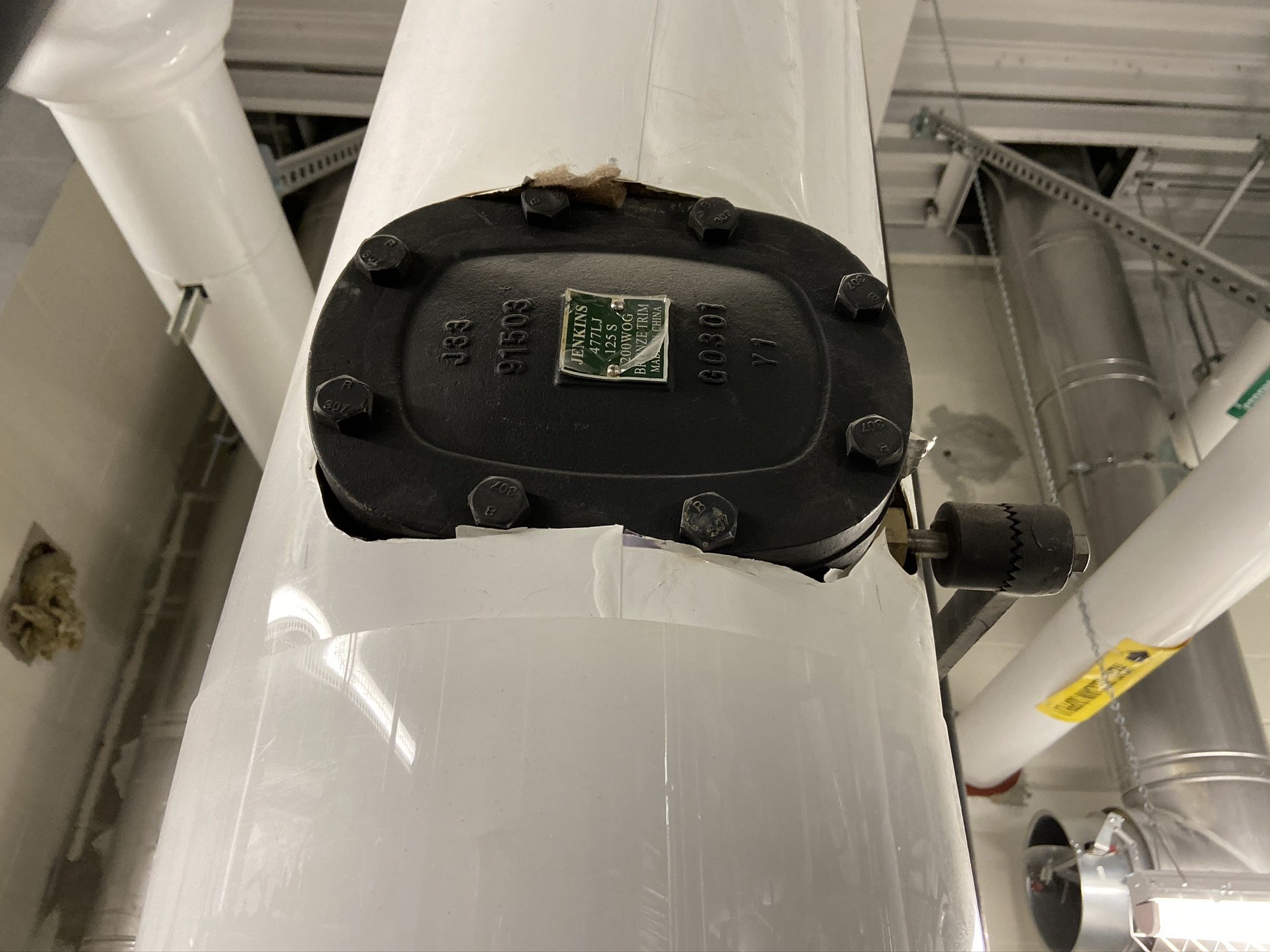
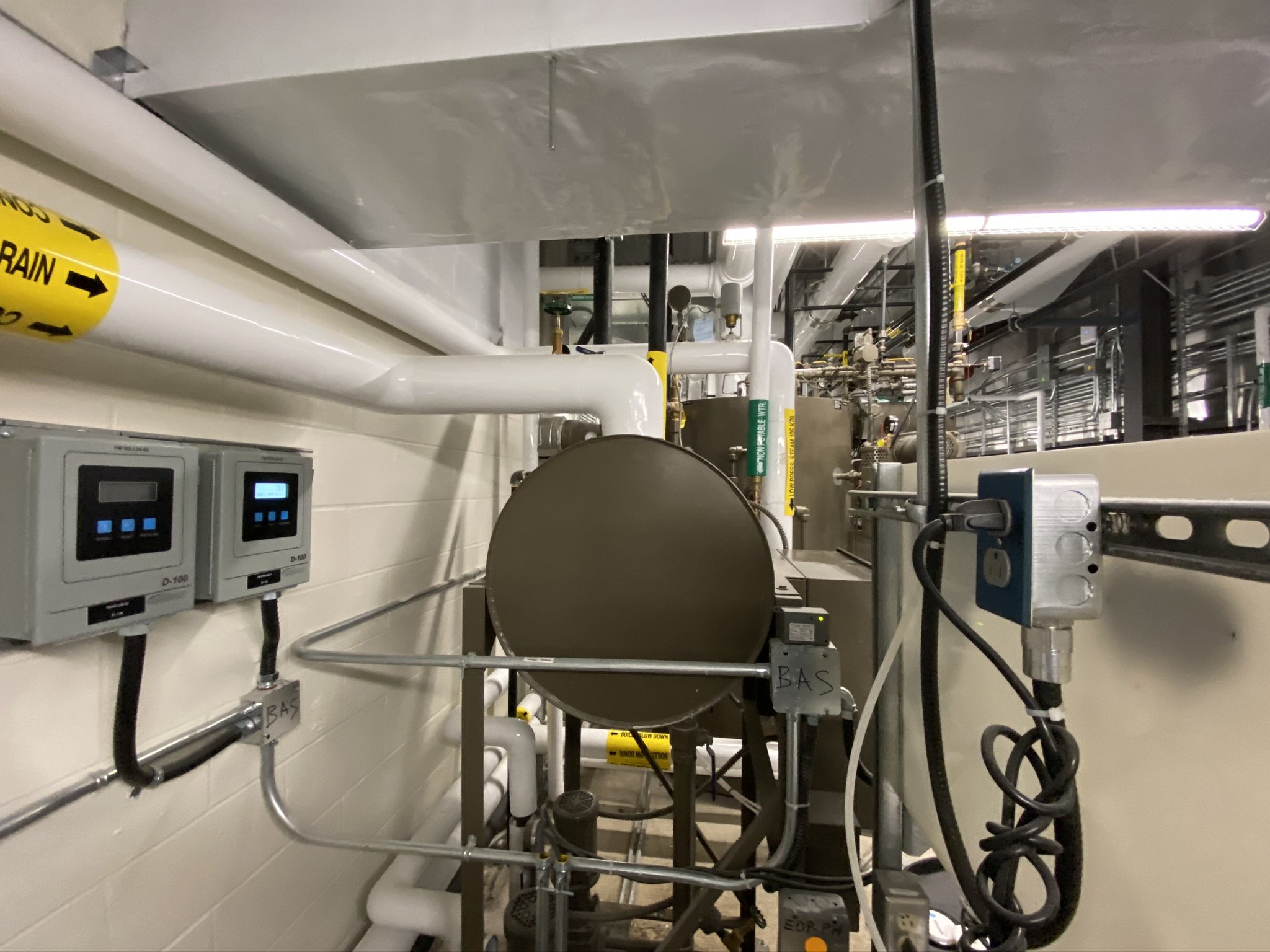
0
Comments
-
I need to ask a few questions since there is a lot that can yield what you are experiencing. First, how old is this installation and where are you located? It looks like a relatively new installation. Has the system ever run as it was engineered to run. Is the steam load constant or relatively constant or does it fluctuate a lot? Do the boilers cycle on/off, never, normally, or rapidly? If they cycle rapidly or short cycle what is causing the cycling? Is the normal steam load, as engineered, supposed to be handled by one boiler with the 2nd boiler to be used as back-up? Can you handle the steam load with only 1 boiler firing? Are the boilers being fired up to their normal maximum or could they be overfired (too much fuel input). Who did the set-up, the factory rep, factory tech or outside contractor? I can not comment on the check valves above the boilers that you mentioned since I do not know enough about this installation, however I can say that a swing check in the discharge steam line for each unit is not out of the ordinary, but I have never seen a "non-return valve" installed on a low pressure steam boiler. What is the design steam pressure of the boilers and do the steam safety valves match that pressure? I won't be able to "step-on" the engineers or the mechanical contractors feet but I may be able to add some guidance.0
-
The installation is new (done this year). It's located in Ontario Canada. I don't really want to say what the facility is exactly to keep things unofficial.
The only steam load is humidification for the air handling system (no heating). The load is inversely proportional to outdoor air temperature. We can barely keep up to the humidity setpoint mostly because I've limited the humidifier valves to 70% max open, if I allow them to open further I sometimes get a torrent of water, this seems to create a bit of death spiral where I lose capacity to heat up all the replacement feedwater. If running one boiler it rarely cycles, if running two occasionally a boiler will cycle off for a while. But the cycling rate seems healthy, definitely not excessive. The 5:1 turndown seems to help a lot.
The initial design was duty standby, but we've since changed the sequence to run both concurrently since it simply works much better (steam is drier, steam meter reading is stable, and less water going down the drain). Also the boiler specs show the boilers are more efficient by a couple percent at lower firing rates so if two can run with stability it's preferable.
We have natural gas meters and steam meters on the system and the input natural gas seems bang on (I think 1.3million btu), and the steam output and the steam load seems within spec (max load somewhere between 1000-1100 lb/hr).
The pressure reliefs are set at 15psi (as per the design), and the operating pressure setpoint is currently 11psi. But the pressure climbs a couple psi before it sets off if the load is low. I think initially the steam was running at 10psi, but has been turn up one 1psi to 11psi. The reliefs have never let go, apparently it's quite dramatic if they do.
The mechanical contractor did the setup (mech contractor is the same parent company as the controls company I work for, so where all one family who just wants it to work), but the factory rep has been out a couple times, as well as some other steam "experts." Everyone seems to say it all looks good, and can't point to any obvious problem areas.
My problem as the controls guy is that I'm left holding the bag at the end of the day, and my steam meter readings aren't stable at high loads, and lots of water pours out of the traps near the air handlers at higher loads. I think water is somehow being pulled out of the boilers.
It was mentioned by others the "non-return" valves are necessary, but shouldn't hurt. The only red flag that I could see was the condensate path out of the header to the left of the boilers. It appears to come out of the header about a foot above the floor, then it goes up about 7 feet before terminating in the feed water tank. Is the feedwater tank at atmospheric pressure or is it pressurized by the water/steam. It's heated by steam to somewhere between 160f-180f I think.0 -
As you have written your report, everything looks to be running as it should. Since I am not the service tech on the job I have to assume that everything is as it should be. I only have a couple thoughts. I would call Fulton and ask what the maximum recommended temperature is for that condensate feed tank and set the temperature to that setting. Me, I would prefer to see a temperature setting of 190f to 200f but that is up to Fulton to say. I should have asked before if the majority of the steam/condensate is returned to the condensate feed tank or is it dumped to a drain? Normally, if a boiler system is piped as it should be, the water quality is right on, all the piping is sized properly, and the boiler input is correct, the boilers should be able to be run at maximum rated steam output with very little water carry over. I am not making any assumptions or comments, just stating the facts. If you are getting carryover of water entrained in the steam flow, then that is out of your control. I would prefer if that were my job to reduce the boiler input 5-10 % just to see how overall system operation was affected. Remember, on most steam systems fresh make-up water and water carry-over is your enemy. It will greatly affect system performance. As far as the condensate return out of the header I would prefer that it was done differently but it may be OK. By the way, the boiler room and the installation look great. I tip my hat to the installers.1
-
Thanks for the comments. Our guys take a lot of pride in a clean install.
Regarding the condensate return, the steam is used directly for humidification (there is no heat exchanger). So the only condensate is, whatever steam is consumed to keep everything hot, every thing else goes into the air stream. All the condensate further from the boiler is to drain (with tempering). This also means that all the water is makeup water (about 180gallons an hour).
I'll inquire about boosting the feed water temperature. I think Fulton actually recommended a bit higher than we are running to "drive the oxygen out".
Since it's a modulating burner I will look into if the burner control signal can be limited temporarily for some testing.0 -
Another couple comments; #1) if you are running at a nearly 100% fresh water make-up, the quality of water has to be almost perfect, with as close to zero oxygen content as possible. #2) This is my opinion only and for your eyes only, -- vertical boilers are prone to produce wet steam when being fired to near maximum capacity. #3) make sure that the operating water line is as low as is recommended by Fulton and does not drift higher as the steam output/delivery increases especially at near maximum output. #4) This again is my idea and it may be how you have the firing rate set; bring on the lag boiler when the lead boiler input exceeds30% and limit fire rate of the boilers to somewhere just below where you feel you are still producing dry steam, probably 70% to 80% of maximum. Once you start to produce wet steam the boilers output capacity is greatly reduced. #5) One last thing you could mention to your BOSS (or someone who will listen that you can talk to) but only if you need but can't always produce the dry steam required, is that this installation could use a "steam separator". Watch who you say things too since System Designers and Engineers get very angry when they think that you think you know more than they do. I have been in that boat a few times. You may be smarter than they are but can never tell them that you are.2
-
@SuperJ
Non return valves are combination check valves and shut off valves if that's what you have. They are used when you have multiple boilers operating to keep steam from entering a boiler backwards. Usually they are only used on high pressure steam (above 15psi).
They do take some pressure drop to get the steam through them and can chatter.........I think this is why they are seldom used on low pressure.
The issue with condensate in your steam header seems that it could be your issue. Yes, you can lift condensate from a trap with steam pressure. But where you are using the steam directly with humidification they are sensetive to steam quality.
if you can't drain the steam directly by gravety I would use an additional condensate pump or a steam powered pumping trap would be a good choice to keep the water out of the header.
one thing to try.
Install a tee onto the inlet side of the trap that drains the header and put a ball valve on the branch. Then when the system is operating you can open the valve and see if your getting water out of the header.1
Categories
- All Categories
- 87K THE MAIN WALL
- 3.2K A-C, Heat Pumps & Refrigeration
- 58 Biomass
- 427 Carbon Monoxide Awareness
- 113 Chimneys & Flues
- 2.1K Domestic Hot Water
- 5.7K Gas Heating
- 109 Geothermal
- 161 Indoor-Air Quality
- 3.6K Oil Heating
- 70 Pipe Deterioration
- 995 Plumbing
- 6.3K Radiant Heating
- 391 Solar
- 15.4K Strictly Steam
- 3.4K Thermostats and Controls
- 55 Water Quality
- 44 Industry Classes
- 48 Job Opportunities
- 18 Recall Announcements