Welcome! Here are the website rules, as well as some tips for using this forum.
Need to contact us? Visit https://heatinghelp.com/contact-us/.
Click here to Find a Contractor in your area.
Thread cutting oil?
Options
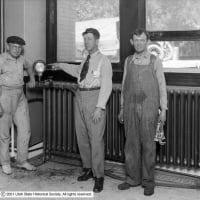
Timco
Member Posts: 3,040
Got my new very old threader working great. Didn’t have cutting oil at my shop. What’s the worst that can happen using motor oil mixed with some cutting oil?
Just a guy running some pipes.
0
Comments
-
From what I've seen working in a machine shop, almost any oil will work fairly good when cutting metal.
For example, even WD40 is 100X better than dry. Motor oil will probably cut threads 80-90% as good as proper cutting oil.
That said, I would still get some good cutting oil and clean the thing out.Single pipe 392sqft system with an EG-40 rated for 325sqft and it's silent and balanced at all times.
0 -
Back when I was a teenager, my dad and I installed a hot water heating system in our house. Sears designed the whole system and sold the whole kit; boiler, copper tubing, circ pump, baseboard rads, expansion tank, etc. Kit even included use of pipe vice, threading dies, and cutting oil. Back then the cutting oil was lard oil.
Today, you can get better cutting oil at any hardware store, although in a pinch melted lard or bacon grease would work okay.
Keep in mind that black pipe can be pretty nasty stuff to thread, compared to many steels that a machinist would see. Good quality cutting oil frequently contains sulfur and/or other compounds to help improve the machinability needed to get decent threadsDennis Pataki. Former Service Manager and Heating Pump Product Manager for Nash Engineering Company. Phone: 1-888 853 9963
Website: www.nashjenningspumps.com
The first step in solving any problem is TO IDENTIFY THE PROBLEM.2 -
> @Pumpguy said:
> Back when I was a teenager, my dad and I installed a hot water heating system in our house. Sears designed the whole system and sold the whole kit; boiler, copper tubing, circ pump, baseboard rads, expansion tank, etc. Kit even included use of pipe vice, threading dies, and cutting oil. Back then the cutting oil was lard oil.
>
> Today, you can get better cutting oil at any hardware store, although in a pinch melted lard or bacon grease would work okay.
>
> Keep in mind that black pipe can be pretty nasty stuff to thread, compared to many steels that a machinist would see. Good quality cutting oil frequently contains sulfur and/or other compounds to help improve the machinability needed to get decent threads
Black pipe is a joy to thread compared to 304 and 316 stainless. Unfortunately I get to work mostly with stainless.Single pipe 392sqft system with an EG-40 rated for 325sqft and it's silent and balanced at all times.
0 -
I used to swear by the "dark" cutting oil like Hercules. But lately our shop buys the Ridgid Clear. I used to have bad luck with this stuff but it seems to work really well for me now. Maybe they changed the formula.
Cutting oil works the best but in a pinch when I ran out I have used motor oil, wd40 etc with mixed results0 -
Every time.
Headed for real cutting oil and dies if I can find them. The seem sharp as hell but I’ll start over. When it bogs down I know it’s doing this.Just a guy running some pipes.0 -
We’ve had bad batches of 1 1/2 pipe before. every time it would do this.. picked up a new piece and everything cut fine0
-
> @SeanBeans said:
> We’ve had bad batches of 1 1/2 pipe before. every time it would do this.. picked up a new piece and everything cut fine
That's what I was thinking when I saw it. I had some that it kept ripping the threads off randomlySingle pipe 392sqft system with an EG-40 rated for 325sqft and it's silent and balanced at all times.
0 -
Lol. It’s the fluid. Motor oil just does not do it. Used actual dark cutting oil and it works great.Just a guy running some pipes.0
-
Joe's only guess was it's because an EG40 and EG45 are identical except the 40 has one less burner tube and a modified and baffled draft hood. I converted mine down to a 40 so I had the parts from the 45 here.
His guess was it was just pulling to much air though the block / burners because it's actually laid out and designed for another burner tube.
I don't know.... I just thought it was odd no one actually knew what the issue was. We did exactly what Tim and Jim said to do.Single pipe 392sqft system with an EG-40 rated for 325sqft and it's silent and balanced at all times.
0 -
Crisj,
The key to cutting stainless is to keep it cool, if you are drilling it, drill at slow speed, with lots of pressure, try not to drill pilot holes unless absolutely necessary, then drill a very small pilot hole. Avoid using abrasive cutting discs, as they heat the stainless.
If you are cutting threads, try to work slowly and use a lot of pressure, try to avoid making two passes, some people use water just to keep the material cool, which is more important than lubrication.
Stainless is very soft (like cheese) unless you allow it to work harden, then it crystallizes, and becomes hard as hades.1 -
> @nibs said:
> Crisj,
> The key to cutting stainless is to keep it cool, if you are drilling it, drill at slow speed, with lots of pressure, try not to drill pilot holes unless absolutely necessary, then drill a very small pilot hole. Avoid using abrasive cutting discs, as they heat the stainless.
> If you are cutting threads, try to work slowly and use a lot of pressure, try to avoid making two passes, some people use water just to keep the material cool, which is more important than lubrication.
> Stainless is very soft (like cheese) unless you allow it to work harden, then it crystallizes, and becomes hard as hades.
For threading stainless I've switched to form threading recently as long as the customer allowes it. So far, I like it.
Work hardening is something that took me a while to learn about and a lot of pain.Single pipe 392sqft system with an EG-40 rated for 325sqft and it's silent and balanced at all times.
0 -
@nibs is correct about stainless which is a P I T A. The slowest speed possible. I burned up a few drill bits and hole saws drilling on SS electrical disconnects before I figured it out0
-
> @EBEBRATT-Ed said:
> @nibs is correct about stainless which is a P I T A. The slowest speed possible. I burned up a few drill bits and hole saws drilling on SS electrical disconnects before I figured it out
Drilling stainless is easy.
I spend most of my time milling it.
The real fun comes when you snap a tap off in it.Single pipe 392sqft system with an EG-40 rated for 325sqft and it's silent and balanced at all times.
0 -
Jim Webb, an owner of Keypower Hydraulics in Richmond BC told me how to work stainless, in the mid '70's. I will always be grateful.0
Categories
- All Categories
- 87K THE MAIN WALL
- 3.2K A-C, Heat Pumps & Refrigeration
- 58 Biomass
- 426 Carbon Monoxide Awareness
- 113 Chimneys & Flues
- 2.1K Domestic Hot Water
- 5.7K Gas Heating
- 109 Geothermal
- 161 Indoor-Air Quality
- 3.6K Oil Heating
- 70 Pipe Deterioration
- 994 Plumbing
- 6.3K Radiant Heating
- 389 Solar
- 15.4K Strictly Steam
- 3.4K Thermostats and Controls
- 54 Water Quality
- 44 Industry Classes
- 48 Job Opportunities
- 18 Recall Announcements