Welcome! Here are the website rules, as well as some tips for using this forum.
Need to contact us? Visit https://heatinghelp.com/contact-us/.
Click here to Find a Contractor in your area.
closely spaced tees
Options
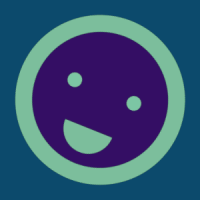
Snowmelt
Member Posts: 1,428
just thinking outside the box, would this be beneficial, working with a typical 150,000 btu boiler. instead of "just" going with the standard closely spaced tee's could I start the heating loop with 1-1/4 black pipe then go to a two inch x 1-1/4 reducing coupling then two - 2 inch x 1-1/4 tee , then back to a reducing coupling . then back to the boiler return in 1-1/4. what i want to do is get more volume and slow the water down. will that work?
0
Comments
-
Uhhh....... Why?0
-
1 1/4 pipe will handle the flow from a 150,000 btu boiler (is that input or output)? If you increase the pipe size to 2" the water velocity will drop.
No real advantage to this unless your venting air or collecting magnetic particles etc0 -
The only advantage would be a marginally smaller pressure drop between tees on the primary side. The close tee setup already minimizes the pressure differential between the outlets and achieves hydraulic separation. Yes, you would get very slightly better effectiveness for your separation, but I don't think it is anything that will ever be apparent in system operation. If you are going to that trouble, why not just use a hydro separator with dirt/magnetic/air separation built in. IMHO the extra cost of that one component is drastically offset by the labor savings of having to pipe and install 4 separate components to achieve the same result.2
-
Ok thanks guys, I was just thinking outside the box. Not trying to invent the wheel, but just trying different ways to achieve the primary secondary theory.0
-
If you are building a primary secondary set of closely spaced tees, the main pipe size just need to be adequate to supply the required gpm. 1-1/4 would be able to move 19- 20 gpm.
The distance between the tees is the key, and keeping that flow resistance as close to 0 as possible, adding additional diameter in the "tee" really has no advantage.
IF you are building a P/S like shown below with multiple circulators, and different capacity circs, then that "horseshoe" loop needs to be sized to the max flow rate when all circs are running. that horeshoe loop becomes a hydraulic separator of sorts assuring all pumps get adequate flow. The example tries to show different sized circulators to present the concept.
If you want to build a 4 port separator device, the key is to have the barrel size about 3 times the diameter of the connection ports. that assures the least amount of pressure drop, top to bottom, and assures both pumped circuits have adequate flow without conflicting.
Bob "hot rod" Rohr
trainer for Caleffi NA
Living the hydronic dream0 -
Hot Rod, very interesting how the first screen shot and the third screen shoot the tees are going the opposite. ( the bull head is going out to the heating loop in one screen shot, the other screen shoot the bull head is going back to the boiler). Let me ask two questions.
1 is there a minimum length after an elbow to place your closely spaced tees. ( like on an air scoop)
2 if I use black pipe to do my closely spaced tees. (1-1/4 pipe) can I use a shoulder nipple or do you want to go 4 x the pipe diameter in between the center of the tees.” 5 inches”
0 -
yes there is a grey area in the bull heading concept with P/S piping. Ideally you never pipe flow into or out of a branch in hydronics. i think some codebooks state that now, according to a post from Mark E a while back. But in the case of P/S you have flow moving thru the run of the tee also, so it is really kind of a a "blending" fitting.
Doesn't matter if you pump into the P/S tee assembly, or out. Fig. 6-4 shows a high head loss boiler, you want to always pump "into" that type of boiler so the added pump head shows up at the boiler and assures the pressure switch is "made" Be mindful of expansion tank connection location, pump away always, it gets complicated in multi pump P/S piping. another reason to use a separator
Fig. 6-1 shows a cast boiler perhaps, a wide open vessel, not concern about the pressure drop in that boiler.
I don't know of a specific ironclad rule for P/S piping, this is a good rule of thumb below.
With threaded pipe I alway used a close nipple between the tees. Be sure the burr is reamed out, it really does make a difference at this special tee.
With any Caleffi drawing, the visual also tells a story. Thin lines vs fat lines, blue lines vs red lines, bright red, vs light red.
Mod con symbols vs cast boiler symbol. You can learn a lot about the intent of the drawing without reading the text. These drawings have been a big help we feel to convey the story.
There are installers out there that may not read or speak english. When I train in Chicago for example I often have a Polish and Spanish translator in the room
But always read the textthe method to the madness is in the written word.
Bob "hot rod" Rohr
trainer for Caleffi NA
Living the hydronic dream1
Categories
- All Categories
- 87K THE MAIN WALL
- 3.2K A-C, Heat Pumps & Refrigeration
- 57 Biomass
- 425 Carbon Monoxide Awareness
- 116 Chimneys & Flues
- 2.1K Domestic Hot Water
- 5.7K Gas Heating
- 109 Geothermal
- 160 Indoor-Air Quality
- 3.6K Oil Heating
- 70 Pipe Deterioration
- 987 Plumbing
- 6.3K Radiant Heating
- 389 Solar
- 15.4K Strictly Steam
- 3.4K Thermostats and Controls
- 54 Water Quality
- 44 Industry Classes
- 48 Job Opportunities
- 18 Recall Announcements