Welcome! Here are the website rules, as well as some tips for using this forum.
Need to contact us? Visit https://heatinghelp.com/contact-us/.
Click here to Find a Contractor in your area.
Pressure & vacuum tests advice on my oil burner setup
Options

belham
Member Posts: 32
Hi all,
I live in Europe, and am trying to do the majority of the oil burner service myself given our circumstances.
Here are basic pics of my system, and after I wanted to ask a few questions. It is a Weishaupt oil burner (virtually identical to Reillo setups in the States), a two-line setup (level lines, 21 feet length) to an in-ground 3000Litre tank. The system has an Afriso filter system (pic below) hanging on the side of the boiler for the fuel coming in and it uses a Danfoss pump (Danfoss and Sun rule home oil burner system fuel-oil pumps in Europe).
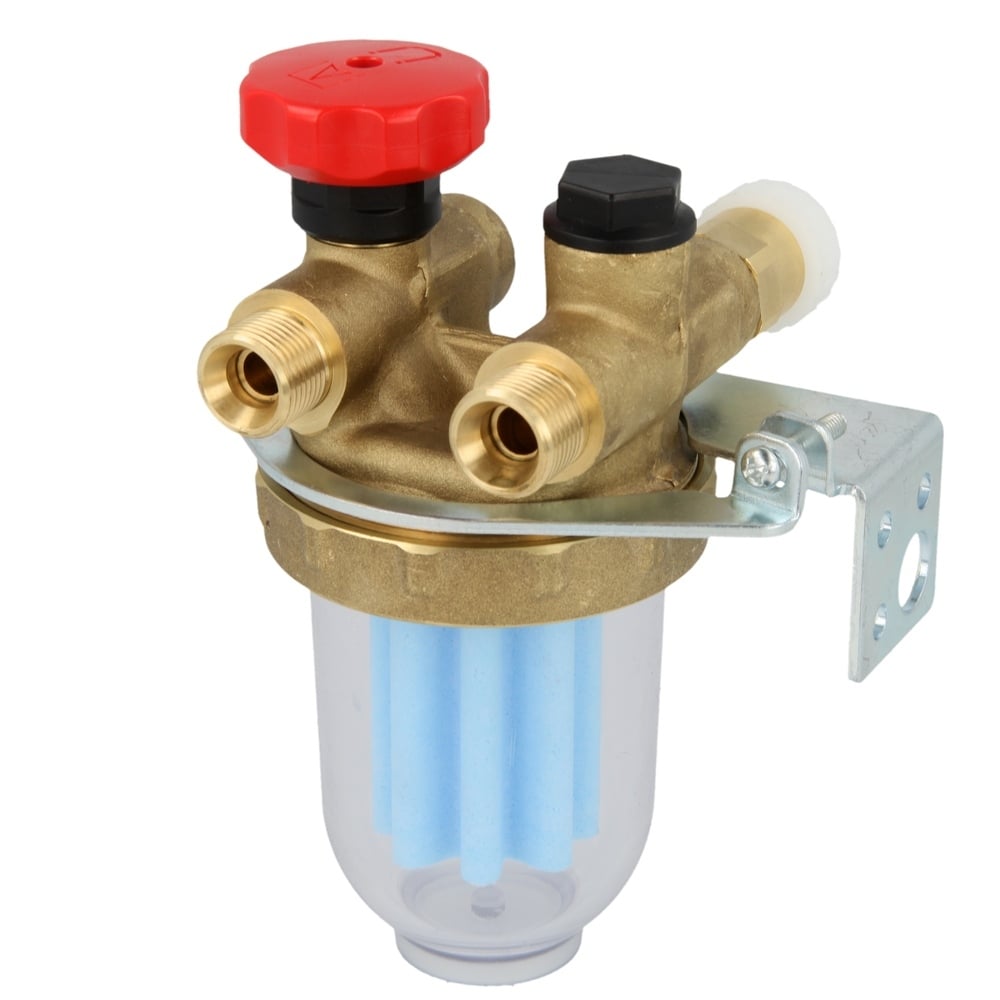
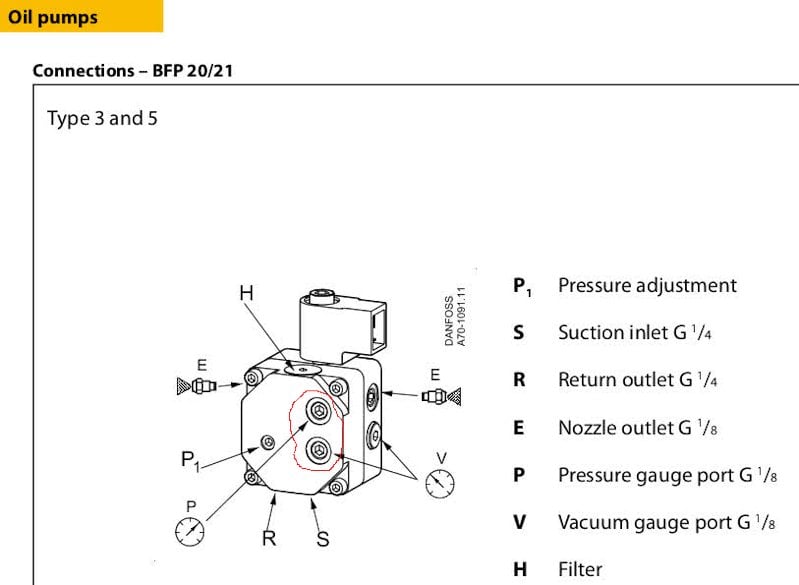
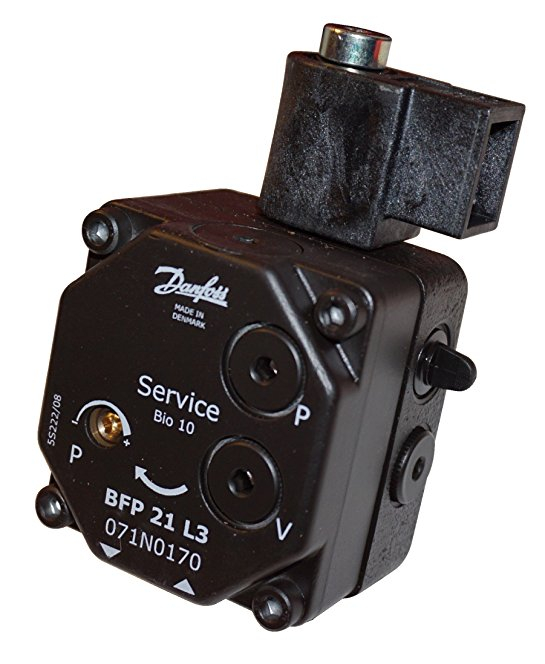
Ok, I recently acquired the below to add to my tool-chest for taking care of the burner. Here's are pics of what I added:
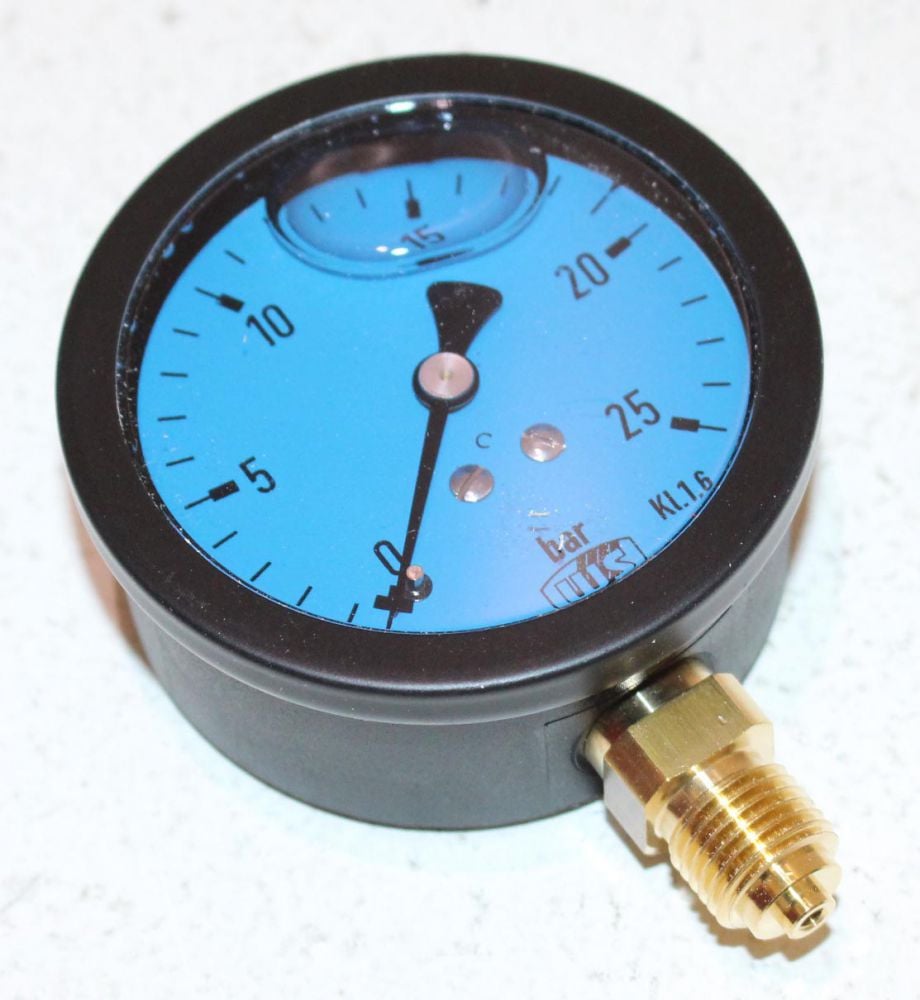
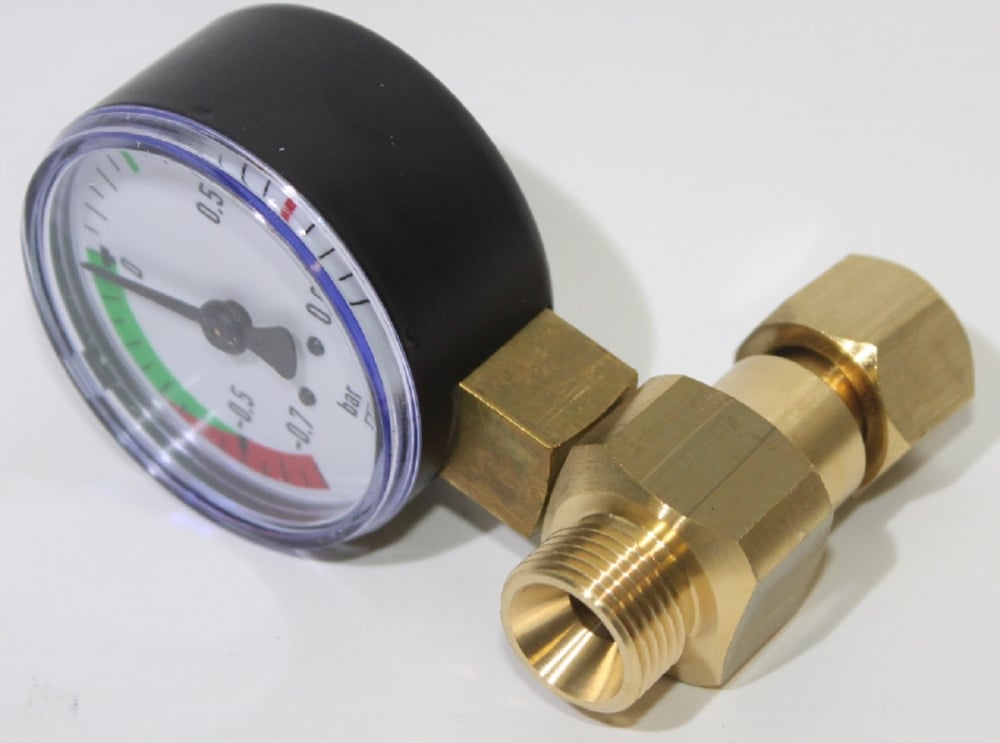
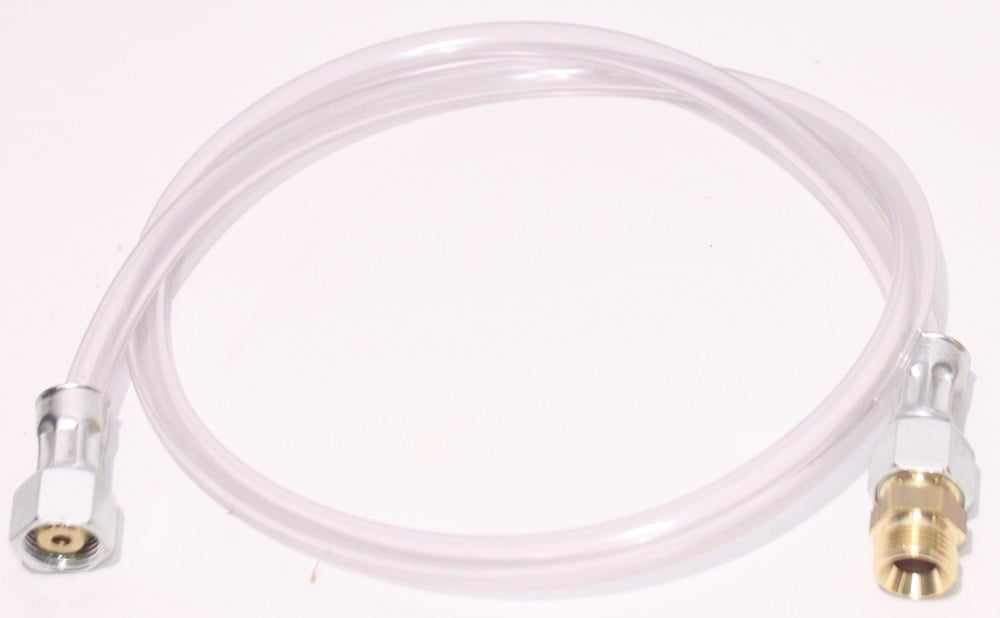
Here are the questions I am trying to understand (Danfoss manuals & language barriers are very real over here):
1) I want to first do a vacuum test. Given that Danfoss put a "vacuum-testing" port straight on the front of the pump, is there any reason I cannot just take the plug out of this front "V" port, screw-in tightly my vacuum gauge, and then run the burner a full cycle & watch the vacuum readings during and ~5 mins after? Please note that the vacuum gauge that I bought can be used in-between the connection of the Afriso filter (if you want to do a "sight" clear line hose test) and the suction line going to the Danfoss pump or by itself where you just un-screw the gauge & use it directly in a fuel-pump port like Danfoss provides.
2) Would it ever be possible that you can get "good" vacuum readings at the fuel pump, but yet if you go and do the "clear-hose-line" test, you might see "air bubbles" coming down the clear-hose & heading into the pump? And would it be possible you get 2 different vacuum readings from testing at the pump and then at the intersection between the Afriso fuel filter & the suction line going to the pump?
3) Is there any reason, again since Danfoss put a "pressure-testing-port" straight on the front of the fuel pump, that I cannot just remove the plug in that port, screw-in tightly my glycerine-filled pressure gauge, and test to make sure the pump is operating near or at the Danfoss-specified 145PSI (10 bar)?
What is confusing me on theheatingwall.com is reading past threads/posts (and indeed in another thread I posted a few weeks ago) where people are telling me to disconnect all sorts of things to do either the "pressure" and/or "vacuum" tests. Why do I need to disconnect anything on my two-line setup if Danfoss put the testing ports straight on the fuel pump itself??
Thank you very much for any help.
I live in Europe, and am trying to do the majority of the oil burner service myself given our circumstances.
Here are basic pics of my system, and after I wanted to ask a few questions. It is a Weishaupt oil burner (virtually identical to Reillo setups in the States), a two-line setup (level lines, 21 feet length) to an in-ground 3000Litre tank. The system has an Afriso filter system (pic below) hanging on the side of the boiler for the fuel coming in and it uses a Danfoss pump (Danfoss and Sun rule home oil burner system fuel-oil pumps in Europe).
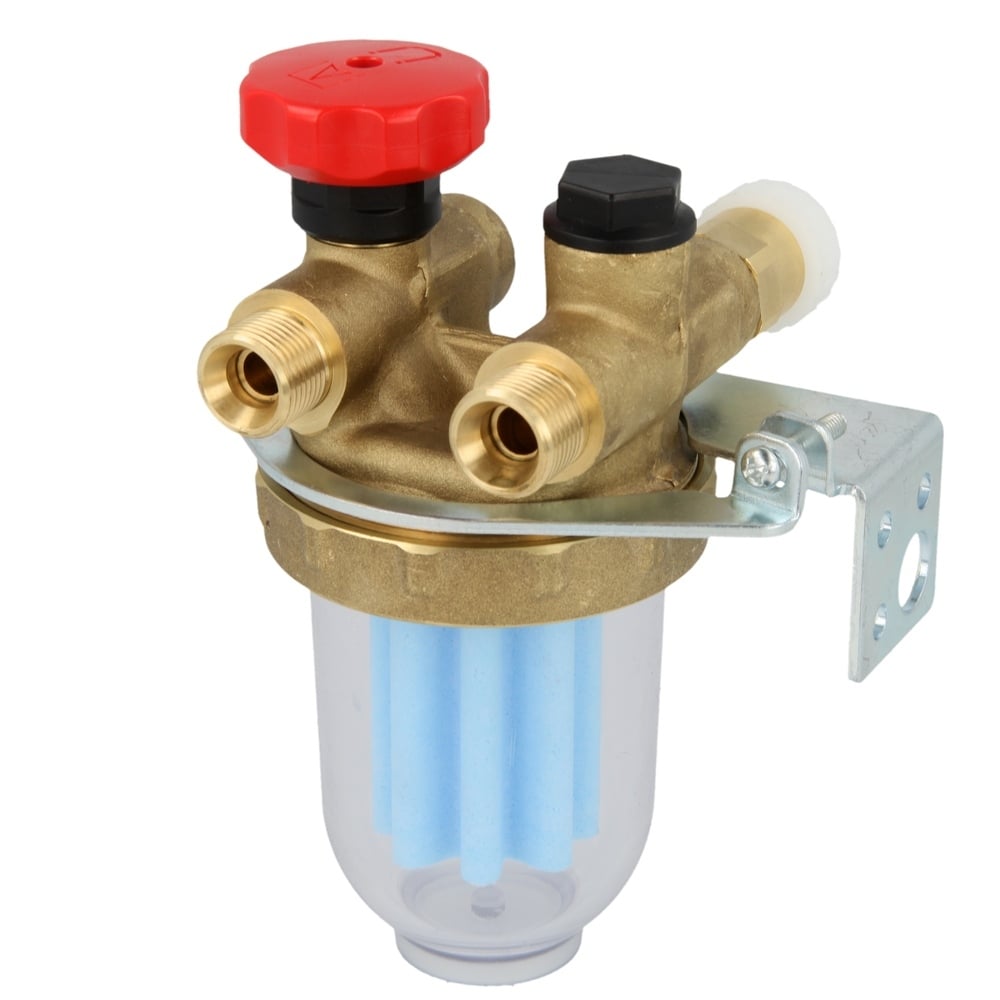
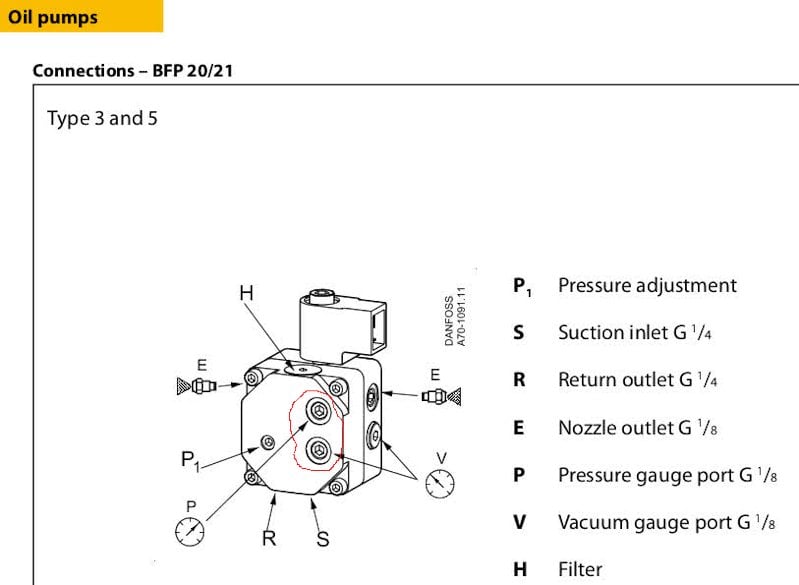
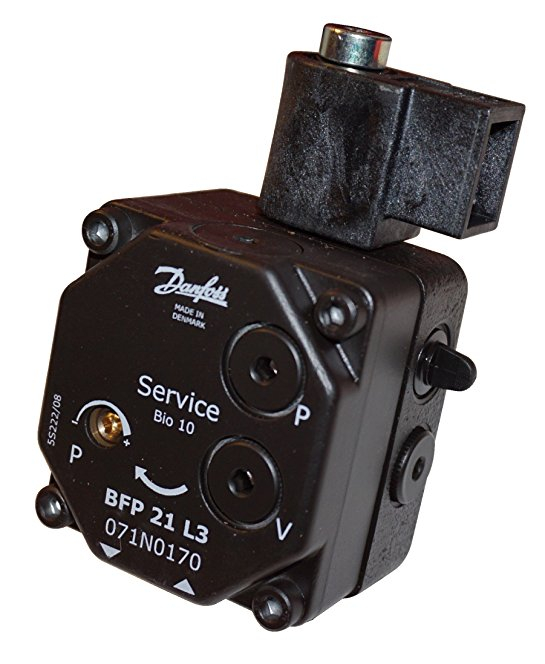
Ok, I recently acquired the below to add to my tool-chest for taking care of the burner. Here's are pics of what I added:
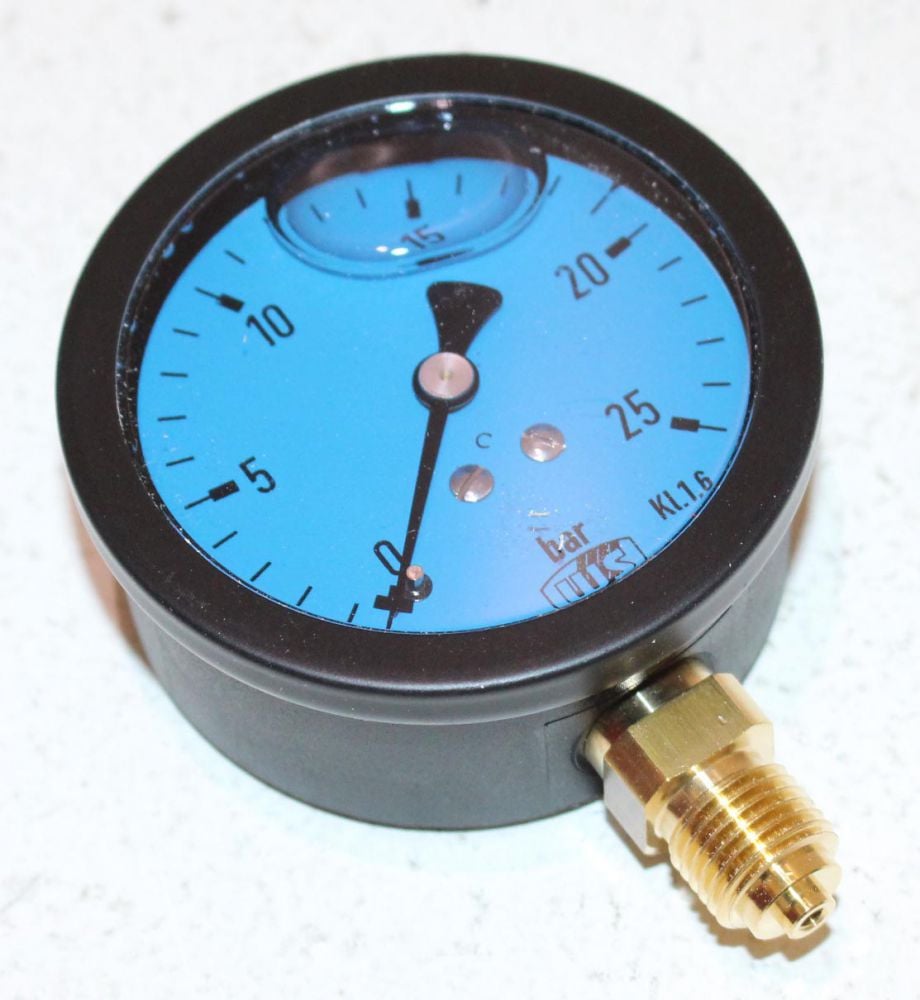
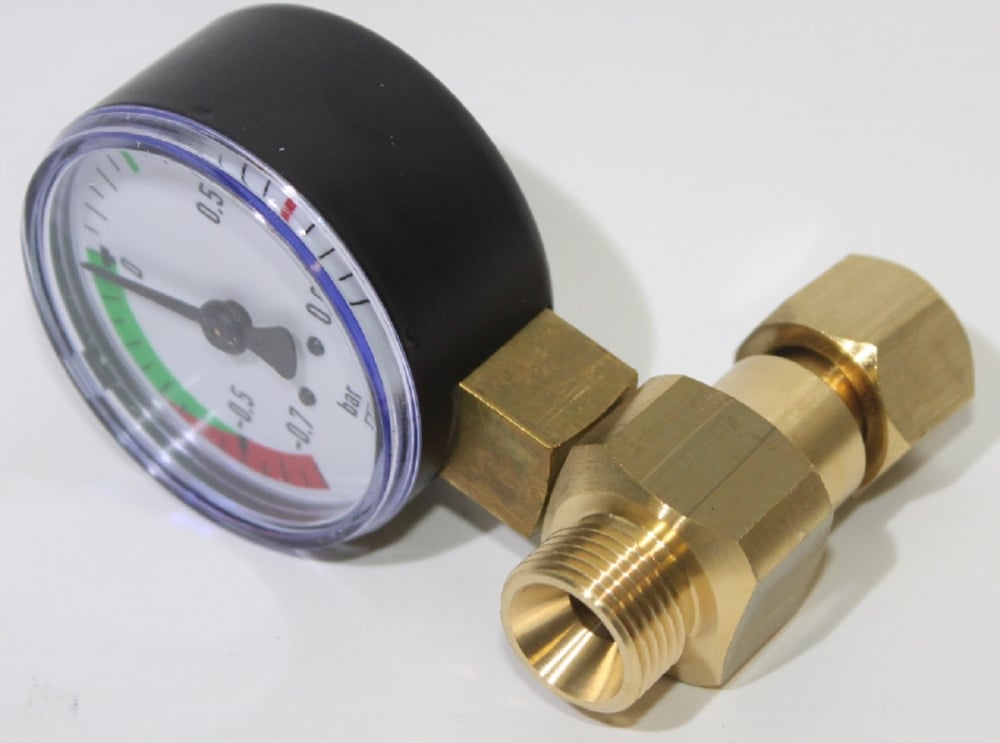
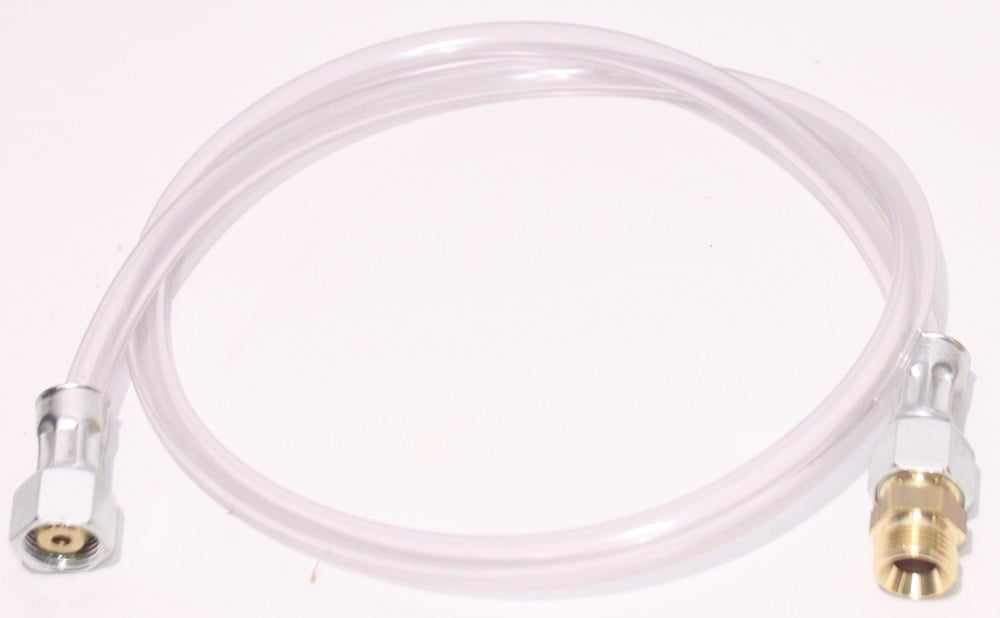
Here are the questions I am trying to understand (Danfoss manuals & language barriers are very real over here):
1) I want to first do a vacuum test. Given that Danfoss put a "vacuum-testing" port straight on the front of the pump, is there any reason I cannot just take the plug out of this front "V" port, screw-in tightly my vacuum gauge, and then run the burner a full cycle & watch the vacuum readings during and ~5 mins after? Please note that the vacuum gauge that I bought can be used in-between the connection of the Afriso filter (if you want to do a "sight" clear line hose test) and the suction line going to the Danfoss pump or by itself where you just un-screw the gauge & use it directly in a fuel-pump port like Danfoss provides.
2) Would it ever be possible that you can get "good" vacuum readings at the fuel pump, but yet if you go and do the "clear-hose-line" test, you might see "air bubbles" coming down the clear-hose & heading into the pump? And would it be possible you get 2 different vacuum readings from testing at the pump and then at the intersection between the Afriso fuel filter & the suction line going to the pump?
3) Is there any reason, again since Danfoss put a "pressure-testing-port" straight on the front of the fuel pump, that I cannot just remove the plug in that port, screw-in tightly my glycerine-filled pressure gauge, and test to make sure the pump is operating near or at the Danfoss-specified 145PSI (10 bar)?
What is confusing me on theheatingwall.com is reading past threads/posts (and indeed in another thread I posted a few weeks ago) where people are telling me to disconnect all sorts of things to do either the "pressure" and/or "vacuum" tests. Why do I need to disconnect anything on my two-line setup if Danfoss put the testing ports straight on the fuel pump itself??
Thank you very much for any help.
0
Comments
-
You can use the cover port or optional port to test the running vacuum of the fuel unit.
However, if you want to check the fuel unit for a seal leak, the only way is this on a 2 pipe system (from the manual):
1. Put vacuum gauge on inlet port, or plug port and use the cover port.
2. Remove return line.
3. Turn on burner.
4. When vacuum reaches 15in, plug return port and turn burner off. This is the step that's a problem to implement (for me). You're timing has to be perfect because you can't put the plug on while the unit is running, even for 2 seconds as you can blow the seal. And if you stop the burner and don't get the sealed plug on instantaneously, you lose the vacuum. So for me, I remove the bypass plug, and plug the port, and perform the vacuum test like a one pipe system (see below).
5. If the fuel unit can't obtain 15in of vacuum or hold that level for 5 minutes, repair/replace.
So I test it this way (one pipe). Make sure unit has oil in it.
1. Install vacuum gauge in the inlet port.
2. Turn burner on and open bleed .
3. When vacuum reaches 15in, close bleed port.
4. Turn burner off. If the fuel unit can't obtain 15in of vacuum or hold that level for 5 minutes, repair/replace.
For running vacuum, hook up your hose, bleed the unit, watch the hose and the gauge. You can see air bubbles if any of your connections are loose (especially the clear hose connections). You'll also see bubbles if you're pulling to high a vacuum.
For a system leak (one pipe)
1. Close the tank valve.
2. Pull a vacuum with the fuel unit.
3. Shut the burner off. Vacuum should hold for at least 5 minutes.
If it's 2 pipe you'll have to plug the return again at shut-down. Considering you don't have a high lift job, I would just remove the return line, bypass plug and plug the return port for all the testing.
Regarding your other questions, I would do all vacuum testing at the fuel unit. Keep in mind any air leaks during running vacuum, and you'll show 0 on your vacuum gauge.
Pressure testing/set up you can use the port on the pump for testing and adjustment. But you can't test pump cut-off unless you either put the gauge in the end of the nozzle assembly, use an inline attachment between the fuel unit and the nozzle assembly, or attach the gauge to the nozzle port.
There's nothing confusing about any instructions I previously gave you. This is the proper way to perform these tests.
You can also test your oil valve by ohming it out to see if it's in the manufacturer's range. I do not know the range for the valve you have pictured.
There was an error rendering this rich post.
0 -
Hi Steve,
Got my old laptop on top of the boiler right now, read your instructions like 20 times. I went with your "one-line" suggestion and did everything as a one-pipe.
Well, nuts, everything looked normal (I'm still dealing with the darn nozzle "after-nozzle--drip", trying to solve it) except when you wrote "if you're pulling too much vacuum, you'll see bubbles in the clear hose and a vaccum reading stuck at 0". Well, sure enough, as soon as I got things hooked up (and checked for tightness, especially the clear-hose), during a running vacuum test my vacuum gauge just sat at zero (0) the whole time the system ran....and little bast#rd bubble came down thru the clear line.
Since this Danfoss pump is brand new, and I have a spare brand new Danfoss pump, which I quickly swapped it in on the Weishaupt burner, and it too did the same thing on the running vaccum test. So, I know it is not the pump. I guess since it's pulling too much vacuum, it means I've got a leak somewhere from the tank to the old Afriso filter unit (my hoses are new). Dang, ugh, I was hoping to avoid this news.
My neighbor is standing here with me right now, telling me "let's hook up the new Afriso Flocop-2-De-Aerator" which I had bought awhile back intending to hook it up this coming summer (converting my two line system into a single-line). But heck, what is that thing going to do if I've got a leak in my intake/suction line somewhere or whereever the air is getting into things (maybe at the top of the tank in the ground?) . He says the new Flocop (essentially its a Euro-version of the Tigerloop), might let way less air into the running system, and my "after-drip" would die down. Which would allow me to nurse the system until warm weather comes when I can lay new copper from the Weishaupt bruner all the way out to the undergound tank. But I don't just don't know, how in heck would an aereator help with my problem?? if it is actually a small leak somewhere in the suction line and/or at the top of the in-ground tank? I don't get it
You know, staring at the old Afriso filter unit (like in my pic at the beginning of this thread) currently on my boiler, it makes me wonder. In Europe, for residential, they still spec their version of their compression fitting for for gasoil burner lines. Both the suction line and return line have them on mine. Granted it's their special version of a compression fit, where the inner ring is made differently, twice as long, with the fitting sealing end tapered into the fitting of the unit, but still, it is compression. Could that be where my air is/was getting in while doing a running vacuum test? I understand from reading that in the States we say it should always be using a flared fitting. But I'd have to hunt a special one down as they do not used flared fittings for this in Germany/France/Belgium/Netherlands/etc. Neighbor is telling me "NO" right now, saying that these special German compression fittings for gasoil lines are as strong and with as good sealing properties as any flared fitting in the world. Really? How?? Damn this language barrier!! I hate feeling stupid.....
Crap, lol, oh well, thanks again, Steve, for all your help. I was hoping this was going to be something in the house I could fix. Think I'm gonna put everything all back together like it was and consider what to do with the new Afriso Flocop-2 filter unit. I mean, it would mean not having the return line anymore, one less thing to worry about, I guess. But I'd still be dealing with 'after-nozzle-drip" that I've got to attend to once a week by pulling the Weishaupt burner out & cleaning the tube and nozzle up...unless this Flocop somehow magically stopped the after-drip. Anyway, here's a pic of the thing
0 -
Just to clarify, if you have too much vacuum, your vacuum gauge will show a high number, and you'll see bubbles in the clear tube (oil separating). A vacuum leak would show 0 as well as if you were on a gravity system without and restrictions.
Don't know about 'German' compression fittings, but they should be flared. They may use an o ring or something like that.
The oil de-aerator will help you with vacuum leaks before the de-aerator, and would be one way to try to cure the after drip.
Basically any air pulled into the de-aerator will stay in the unit and give you air free oil to the pump.
Does your burner do post purge?There was an error rendering this rich post.
0 -
I know the Reillo commercial burners I have worked on have something similar to a flare on the tubing that connects to the nozzle line. Perhaps that what they use over there. Termonology is a problem. It is some kind of "double flare" or "bubble Flare"or brake line fitting.
Reading Reillo manuals that have been translated to English took me a while to figure out with a modulating or 2 stage burner what we would call "low fire" and "high fire" they call "low power" and "high power"
Not a big fan of de-aerators, I would prefer fixing the leak, but as @STEVEusaPA mentioned it will probably work and save excavation and re piping.
Possibly this air is getting in the nozzle adapter and causing your after drip on shut down0 -
Hi Steve & Ed,
Far as I know, my Weishaupt does no after burn and/or purge. The Weishaupt burner---which currently goes through a run cycle great, no hiccups, strange noises or anything---just shuts off at the end of a cycle run (typically 5-10 mins each run, about 17-20 runs total throughout a normal day, it seems) and the solenoid piston inside the new Danfoss pumps just drops down and seals the pressure off. I ohm tested both new Danfoss pumps' solenoids, and everything is good there. I really believe the 'after-drip" is because of the air uncompressing (in the nozzle) after a burn run. You can watch the darn nozzle, right at the point where the fuel squirts out during a burn run, develop one little bubble after another immediately after the burn run stops (the tube/burner is cool enough to pull out and watch this, which I've done many times, and there is no draft problem and/or heat blowback onto the nozzle).
I also swallowed and paid a burner tech to come out a few days ago to only (took some negotiation to agree to this "only" part)run a combustion & smoke tests. Near $350 for him being here maybe 20 mins tops. Grrrr....especially since he ended up adjusting nothing, and said the system is running like new despite being 20 yrs old. I showed him the little bubbles of fuel that comes out of the new nozzle (have tried 3 new Danfoss nozzles) after a burn run, which ends up being 1/2 tablespoon accumulating a day in the burner tube (which doesn't burn off), and he said "yeah, comrade, you've got luft (air) coming in..." and pointed at the Afriso fuel filter unit hanging on the boiler and at the incoming/outgoing lines coming in from outside. But then he says, watching the nozzle, that the "luft" is not too bad, and that he himself would wait for "..stay-at-the-beach-surfing..." his way of saying to wait till warm weather before laying new lines out to underground tank. I told him no kidding!
Regarding new lines and fittings to the Afriso filters, I know in the U.K. they do flared fittings, something I would prefer, so I am going to do some research and see if I can find something for these current fuel lines coming into the house. My lines coming in from outside tank are 12mm, but the Afriso filters (both the old one on there, and the new one I bought) are 3/8" fittings. Go figure. So I need a "flared 12mm x 3/8" adapter", I imagine they are made. Saw something like one on Ebay, made in China, but not sure if they will fit these European threaded systems. I've been warned about making sure anything I do in this house overall that all thread types are correct, and nothing is mismatched between different countries--especially the USA. The U.K. have their own thread standards, the Germans have theirs, the French have theirs, the Italians...well, you get the picture. It is a regular nightmare over here concerning this stuff, and you realize quickly why we in the U.S. were able to economically leapfrog everybody for so many decades. How in heck they got by existing like this, which still occurs even a bit to this day (though standards have changed past 20 years and have become uniform in W. Europe, at least), is surreal. How they've still managed to grow like this, economically, is just plain crazy.
Anyhow, thank you both so much again. Hopefully, I can get the nerve to put the new Afriso (Tigerloop) device on, but that means I'd have to settle for those compression-like fittings (I'd prefer flare if it is possible) and I'd also have to have the nerve to mess with these 20 yr old copper pipe that currently come in from the outside undergound tank. From watching vids on Youtube (are those your vids on Youtube, Steve?, if so they are the best!)...anyhow, from watching the vids of burner systems worked on in the States, I am a bit perplexed that whomever put the system in this house back in year ~2000, they sure did not leave me much in the way of a service loop at the Afriso filter. I've got maybe, maybe 4-5 inches copper tube to play with, so I can't screw up putting the new Afriso fuel filter unit on. Otherwise I will be, if I screw it up, be digging up the basement floor, the outside wall and out to the buried tank in the middle of winter to lay new copper lines.
Thanks again guys. This adventure in Europe continues.....should start my own cable show: "This Old House from Europe!", or "Watch the American Go Insane Working on His Old House In Europe" while I scream & rip my hair out at the wild pricing & taxes, and the fact that owning 1, just 1, Home Depot or Lowes here, and I would be a billionaire. Socialism--which is what Europe is---- has done none of these countries any favors
P.S. Last night my crazy neighbor said to me everyone here prefers two line systems, despite the push to one line craze & regulation (which Europe is doing too). Reason? Number one is moving stuff over distance, which he says two lines are better for. And second, he says that tanks (and fuel) are better taken care of since in two-line systems the fuel is constantly moved around and recycled through the burner and filters. I just nodded not understading why and/or how while drinking another of his Hefeweisens0 -
Hi again Steve & Ed,
Just wanted to follow-up and give you a picture of what the standard fittings for fuel oil/gas lines are in Germany. Here's a diagram of them exactly, which is for the incoming-suction-line from the outside tank and goes into the Afriso 3/8" fuel-filter unit:
*The very left of the pic is the actual 3/8" opening of the Afriso filter unit for your suction line coming into the house---it is exactly what it looks like when you look into any 3/8" Afriso fuel-filter opening for fuel filter lines (the outgoing, if you have an old 2 line Afriso, like I currently do on the boiler, looks exactly the same).
[the German in the pic basically says:
with soft or semi-hard copper tube, a neck sleeve must be used (not part of the delivery)!]
Of course, being the Germans, they do not give you the inner sleeve parts & force you to hunt them down when using their products---even on the new one I ordered.
A bit of good news (I think) though: after searching Ebay sites specific to European countries, I then tried just plain ole USA site and found this:
https://ebay.com
It is a 12 mm flared with a 3/8" male BSP (a Europe standard) threads. Already ordered it & am hoping they'll fit this new Afriso 3/8' opening. I'm going to have to hemp/permatex thread seal it (or just use pipe dope on top of the hemp instead) to make it a secure, tight sealed fitting--------there's no ridge on the 3/8" BSP threaded side for putting a crush copper washer to seal it against the Afriso's 3/8" inlet suction opening.
Question: assuming this works, is there any problem in flaring old copper tube? The 12mm copper tube coming into my house is 20 yrs old, and the small section exposed--that doesn't have the required grove sealing cover around the copper (4-5 inches worth)---is discolored to blacks, browns etc after all this time. Can I just use a plumber's tool (the wire brush circular gizmo), burnish it up, and then flare it after cutting it? Or should you never, ever flare old copper tubing since it might split or something? Like I said, if I screw this up since I've only 4-5 inches to play with, this is going to turn into a nasty, very bad job to lay new copper back out, through the wall, and out to the underground tank. House wall is near 1 meter thick brick where I'd have to go through, and the ground out there is like cement in winter---frozen solid tundra stuff!
Thank you for any advice about whether or not to flare the old, existing 20 yr old copper tubing currently coming into my house for the burner lines. I think the Ebay 12mm flare gizmo will take 2 weeks to get here, so I've got time to think this through whether to do this or whether wait for spring/summer before doing anything & just keep up the cleaning out the burner tube once every 7 days of unburned gasoil because of the nozzle after-drip (if I let it go past 7 days, there might be problems, big problems, me thinks).
P.S. Here's a pic of the exact 12mm copper seal-covered piping, for both incoming & return lines, I have coming into the house from the outdoor underground tank (of course, this shot is of new pipe, but mine is essentially identical, except it is 20 years old and the exposed part of the copper is all discolored from age):
0 -
Two lines are bad. Create too much velocity and cavitation which releases air bubbles. 2-lines are pump the oil 18 to 25 gph instead of what the nozzle requires. This can cause some dirty to suck right through the filter and definitely can clogged the filter quicker. Also, during the off=cycle the oil in the lines indoors get warmer which will make it burn better. 2-lines take the warm oil back to the tank and bring in cold oil.
When you suspect a line or fitting leak you go through the vacuum process that Steve recommended. Then one by one you take heavy grease and spread it on a fitting and re-test. When you hold vacuum you will know you found the leak. Oil filter canisters can leak also, so the whole thing needs to be greased.
Tiger Loop will remove the air. When you watch a Tiger Loop you are seeing the air separation that high velocity creates also.
0 -
@belham , yes I believe the incoming air is causing you afterdrip when the air compressed by oil pressure is re-expanding in the nozzle adapter on shutdown.
Just a couple of things, and, I don't know if they apply to your burner.
1 burner manufacturer I know used to "slug" the nozzle line by inserting a piece of welding rod into the nozzle line before the nozzle adapter is screwed on the nozzle pipe. The reason for this? Just to take up space in the nozzle line so that it held less oil on shutdown. The hole in the nozzle is very small. Most burners use 1/4" ips pipe for the nozzle line which has much more capacity than is needed. less oil=less oil to dribble
Also I believe some (maybe all) nozzle adapters are made so that the oil enters the nozzle adapter in the center of the nozzle adapter but the oil transfer from the nozzle adapter to the nozzle adapter is made above the nozzle adapter centerline to keep the nozzle from dribbling. Could it be possible you nozzle adapter is installed upside down?
Yes, flaring old tubing can split, it seems to harden over time. What I do is clean and ream the tubing. When using the flaring tool instead of flaring in one motion, tighten it a little...back it off...tighten...back it off. Keep doing this until flared and it will seldom split. use alittle lube oil on the flare cone.
The alternative is to heat the tubing to anneal it, but a torch on oil lines connected to a tank is a NO NO.
I am probably one of the very few on this forum that prefers 2 pipe systems.0 -
Hi Ed,
Hope you see this post.
Here's pics of my St-Couvain boiler (dimensions 18" wide, 34" long, 34" height), the Weishaupt Wl-20-A oil burner, & the gun-burner assembly (plus) nozzle on the Weishaupt (these are the best pics I could find/do). On my WL-20-A version model ( ~1998-2000) they pretty much made it idiot-proof as it can only be installed "one-way". There are both notches and a screw preventing anyone from installing it except like it is supposed to be. Please note in the 2nd pic, my version model does not have the warming chamber, that happened on the late-2000-2003 mostly for people who needed it (with outdoor, exposed tank and living in the Alps & very cold regions of Germany--something I do not need where I am in the Benelux region, plus my tank is underground). So in the side-view pic, the "vorlaufleitung & Leckolleitung" is one line, but it comes dead into the center of the assembly, with the fuel line (from the Danfoss pump) attached right there at this center point of the assembly: (again, apologies about the pic size---it is/was the best I could do):
I was wondering, since you're the only person I've really found on the Internet who actually likes & prefers 2-line for their oil burner systems, could I ask you some questions I've been thinking about? Should I do it in this thread, or start another thread & title it something-like "Whether to Convert my 2 line to 1 line & other questions about my Oil Burner". (jeez, what a mouthful). Anyhow, what I am trying to avoid are the people who are inflexible about their thinking, always saying about how bad 2-line systems are, how any Tigerloop device is the best thing since sliced bread, and so on. Yes, i bought one (the Afriso Flocop device, Europe-German-version of a Tigerloop device), but I am not so sure it will solve my problem of "after-drip" (it may or may not). What I'd really like to have is a rational discussion about 2 line systems without getting lectured & yelled at, and this forum is the only place I've found that is relatively civil. Also talk about nozzle size (like my current 1.00 60 S vs possibly going to a 0.75 or even 0.50 60 S to help with atomization on this old unit), along with increasing fuel pump pressure a bit, currently at 10 psi, to around 12 bar (Danfoss fuel pump & Weishaupt overall burner is spec'd for operation at 8 to 15 bar...Danfoss sends their pumps out at 10 bar). Other forums I tried to do these things, but wow & holycow, they were just bad bad BAD--yelling & lecturing me from the get-go about my current 2 line setup and making feel bad for asking questions I didn't understand. So, could/should I do it here in this thread? Or should I start a new thread? What do you think would be, uhmmm, well, you know, would be the safest? ;-)
0 -
Where I went to school it was very simple.
#1 If the burner oil pump is below the level of oil in the fuel tank use 1 pipe gravity feed with a single stage pump.
#2 If the burner pump is above the level in the oil tank (lift) use a two pipe system with a two stage pump.
#3 Outside buried tank, always use a two pipe system
My theory is with two pipe it keeps the oil moving and less likely for sludge to settle out.
The MOST important thing with oil lines is they must be 100% tight. One of the old books I used to read said "there is no substitute for a tight suction line"
Minimize the # of fittings and flare the tubing correctly and make the threaded fittings up tight.
The "tiger loop" has been around for a long time. As much as I don't like them I have seen jobs where they saved from digging up and replacing oil lines and kept the burner running.
But, if the lines are tight you don't need them
I don't like trying to "lift" oil with a one pipe system
Just my opinion. Others will disagree0 -
"...Anyhow, what I am trying to avoid are the people who are inflexible about their thinking, always saying about how bad 2-line systems are..."
If almost everyone thinks they're bad, sans Ed, why are you discounting their opinions?
I like Ed. Top Notch professional all the way. Maybe one day I'll get to bump into him at a trade show and buy him lunch.
I disagree with ever using 2 pipe, for all the reasons Jim mentioned.
I agree with:
-100% tight
-Minimize fittings. Which really can go unsaid because if piped to code there are no extra fitting, i.e no unions.
-Limited use for Tiger Loops
I'd be curious if the oil de-aerator helps your after drip, as that seems to be what this thread is all about. Ed pointed out the reasons for your after drip-it's either air, bad cut-off, solenoid not closing fast enough, or the chamber stays super heated at shutdown causing the expanding oil.
Are you actually seeing after drip? Or are you running your burner for a few cycles, pulling it apart and noticing oil? Unburnt oil can also be caused by improper draft or combustion, nozzle assembly to far forward or back, or a deformed connection between the nozzle and the nozzle line from over tightening. Or you might just see oil in the air tube because it drips out when you remove the oil line.
Now my posts are starting to get as long as @belham 's...lol
There was an error rendering this rich post.
0 -
Thanks, Ed. Like those rules. LOL, Steve!
I don't think I can write a short post. Ok, here goes, will try my best:
1. Installed a permanent vacuum gauge, on the incoming line just after it leaves the current old Afriso filter unit (2 pipe)
2. During a full burner run (a run typcially last 5-7 mins), the vacuum gauge reads the whole time -0.5 bar (-7.25 psi), firmly in the middle of its "red" zone ("red" zone only goes to -0.9...crap....pulling way too much vacuum, I guess
3. When burner is "off", vacuum gauge reading sits right at -0.1 to 0 bar (1,5 psi), right at the beginning of the green zone (again, check pic earlier).
What do you guys think? (remember, in-ground tank, 3000L, 2 pipe system, both pipes enter the 'top' of the tank, right beside each other, and other than the 1 - 1/2 meter lift coming out of the tank, it's a 20' feet level run for both lines, through ground, house wall, under house floor/cement & tiles, and into a 10 inch rise up to burner Afriso filter hanging on side of boiler).
With this 'vacuum reading', you guys think it is "ok" to nurse this Weishaupt burner & St Couvain boiler to summer when I can lay new pipe (10mm) and/or install the Afriso Flocop (Tigerloop) device? Other than the nozzle 'after-drip', the dang thing runs like crazy. Also, the old 12 mm safety-covered copper lines (covered) coming into the house are +20 years old---am worried as heck I start messing with them, they ain't gonna re-seal and/or flare properly. Then I am screwed. It is winter here. Plus the goofs who installed everything 20 yrs ago didn't leave me a service loop on either incoming or outgoing line---I've got maybe 4 or 5 inches to play with, for both).
All that said, am "equally" worried that if this vacuum problem is bad (because of a line air leak somewhere back to the tank and/or at the tank), and it is going to cause a fuel pump failure or something like that, then damn am I going to have to dig up frozen tundra & bust the house wall up to lay new copper pipe in the middle of winter??
LOL...that's as short as I can get, Steve! It ain't possible, too many languages running around in my head
[UPDATE:]
Think I just found, through Google, an answer:
Even though I have a Danfoss pump, Suntec pumps are virtually identical (and can be used on my Weishaupt burner). So my -0.5 vacuum reading during a run equates to -14.75 inches (HG), which is more than the max of 12 inches (Hg) states. If I am reading & understanding things correctly. Ugh..0 -
-.5 bar vacuum is just way too high. It would point to a restriction-partial plugged or kinked fuel line, valve not fully open or bad FiroMatic valve, check valve mostly stuck (hopefully no check valves). This will kill you pump in short order. The bubbles you are seeing (as mentioned earlier) is from the oil separating.
This will kill your pump seals.
Your 2 options:
TigerLoop (or equivalent).
Replace supply line.
As a check, before your filter, if you put a fuel line into a clean bucket of fuel, bleed the pump, you should read almost no vacuum. If you still have vacuum, the restriction is between that bucket and the inlet of the fuel pump.
If you had a push/pull pump, and no check valves in the supply, you could blow the line back to the tank. Then bleed the line and see what you are reading.
Edit: If you install the TigerLoop, and put your vacuum gauge on the pump cover, you'll see low or no vacuum.There was an error rendering this rich post.
0 -
Well, that s#cks to hear.
As I've been trying to say, it is dead winter here, ground is rock hard frozen tundra and it is an underground tank. There's no way to lay new pipe until spring thaw, which is 3-4 months away.
For installing the Afriso Flocop Tigerloop device, equally I mentioned I have to mess with the 20 yr old sheathed copper supply coming into the house (from under the tiled basement floor). There is no, zero, nada, service loop to make a mistake, so I cannot risk flaring the pipe. Thus I would have to settle for slicing an inch off the old pipe, and using the German compression fitting (which they actually spec, and say to not use flared fittings---they really hate flared fittings in Europe, and after watching GreyFurnaceMan on Youtube, I understand why now) ..anyway, I'd have ot do that and then hope it all works on the old copper (the exposed part I can work is not shiny, new copper anymore).
I checked Danfoss website for my pump, they say my model pump run fines from 0 to -0.3, and will still work ok from -0.3 to -0.5, but anything above -0.5 vacuum bar & you have to start sourcing & fixing the problem. Given I am right at -0.475 to -0.5 during a run, I guess my brand new Danfoss pump I just put on is utterly doomed & cannot last for 3-4 months until I could properly lay new copper & forget about the Afriso TL device.
Crap, absolutely don't know what to do now. Feel like I am damned if I do, and damned if I don't. The burner runs so good, the burner overall + pump makes no weird noises, no hiccups, no stutters, starts instantly, but I understand this could all be an illusion.
This was the worst news I could get today.
0 -
Get a good, modern flare tool like the one pictured here. Never once had an issue with a bad flare with this tool. And I used on a four inch piece of 50 year old pipe sticking out of a concrete floor from an underground tank.
Then put in the Tiger loop. It's a fantastic device that has saved my customers countless headaches. All your problems will be solved.
I've never regretted putting in a Tiger loop. There's no down side to it.0 -
@belham if it's running as good as you say leave it alone until the weather warms up. Check the piping, filters etc inside the building for kinks and restrictions. If you don't find anything let it run0
-
A few years ago I was writing a manual on oil combustion for a training class. I read and read everything I could get my hands on when it came to piping oil systems. No where is it written by a oil pump manufacturer that I could find that stated to use a 2-line system for lift. They all said the reason for a 2-line system was to compensate for leaky supply lines and self prime. That is pretty much a self-destructive system. There should be no leaks. Two stage pumps for lift. I refused to even help a contractor on a standard oil system if it had two line. Other than booster pumps I found no use for two lines and found them to be problematic most of the time.
I worked with a wholesaler that rebuilt oil pumps and we had a pumping station with two lines that were only 4 feet long. I would bleed the pump until it ran clear and then close the bleed. I would run the pump for another 2 minutes and then open up the bleed again. Every time, more foam came out. This is when I realized how two lines caused cavitation and air bubble separation. Also found it was almost impossible to get rid of afterdrip.0 -
@captainco
Respectfully, I strongly disagree. Read the Suntec manual. One pipe is limited to 8' of lift under the best of circumstances.
They also show drawings for two pipe systems for both lift and gravity feed jobs. I read nothing in their manual that condemned two pipe systems, nor did I see anything that said two pipe was to compensate for leaky suction lines. Two pipe self bleeding was mentioned.0
Categories
- All Categories
- 87K THE MAIN WALL
- 3.2K A-C, Heat Pumps & Refrigeration
- 58 Biomass
- 427 Carbon Monoxide Awareness
- 113 Chimneys & Flues
- 2.1K Domestic Hot Water
- 5.7K Gas Heating
- 109 Geothermal
- 161 Indoor-Air Quality
- 3.6K Oil Heating
- 70 Pipe Deterioration
- 995 Plumbing
- 6.3K Radiant Heating
- 391 Solar
- 15.4K Strictly Steam
- 3.4K Thermostats and Controls
- 55 Water Quality
- 44 Industry Classes
- 48 Job Opportunities
- 18 Recall Announcements