Welcome! Here are the website rules, as well as some tips for using this forum.
Need to contact us? Visit https://heatinghelp.com/contact-us/.
Click here to Find a Contractor in your area.
Air in system

keyote
Member Posts: 659
Hey Guys My KHN i installed last fall has this problem I cant figure out. Or at least cant figure out why its happening. when it first starts a cycle it sounds like a washing machine when it's pumping out. At first it wasnt so bad consistent but its actually a bit worse longer and almost always.Figured it was air but cant figure how since I did everything correctly. The radiant manifold on the top floor has a little air vent.there's another on top pressure tank valve. everything was well purged and I added a wall panel loop to that top manifold and purged it and can see through the pex its well purged. Most of all i have a big honking caleffi discal m magnet etc exactly where KHN wanted it ( return side just before entering boiler. And my pump is pumping away from the exp tanks (needed two to get capacity) Now if I recall I did not want to put that discalator on the return wanted it on supply before exp tanks because that was what god recomended, But The KHN schematics were pretty clear and you guys thought i should just follow them. As I remember thats why i went the extra step and added the little vent on the top of the exp tanks cause im stubborn like that and worry and over think.
So Im pretty sure the sound is air and its settles down usually after a few seconds. It bothered me but the thought of redoing the configuration when practically every joint is 1/2" from the next wasnt appealing and i couldnt think what the problem was but this year i decided i had to figure it out before the season and was looking at it and decided o close the caps on top of the discolator and the small vent and guess what no noise. So then Im thinking Im not supposed to do that tough Im not clear why they have caps if they need to stay open. so it seems to solve it and I wonder why and decide the pump is drawing air in from the vents which seems like it ought to be impossible for a vent to do exactly what its designed to solve but life sucks like that alot.Now some will remember i used the taco DT pump and it worked but with the KHNs logic modulating they would seesaw up and down not tripping but it wasnt ideal at all and since i only have one zone hooked up at this point i put the pump on fixed second speed until i add more zones ill then swap into the delta pressure version. so the pumps on second speed and theres a indirect with its own wilo 3 speed on full speed and the sound happens with DHW calls as well.
Why is this happening? I hear callefi make s a little check valve you can put on top before the cap i suppose that might work i assume i should leave the caps tight.
thanks for the help in advance.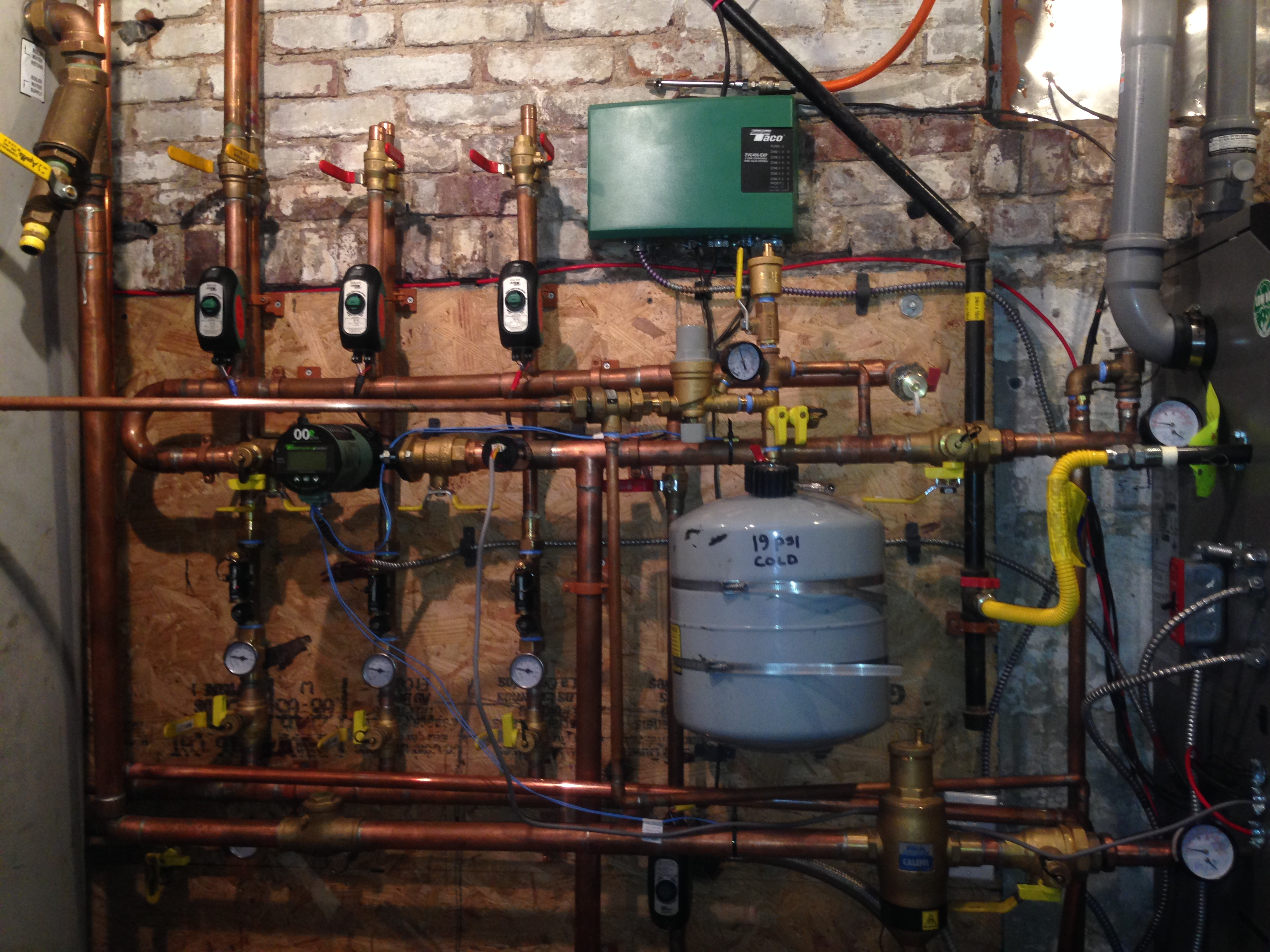
So Im pretty sure the sound is air and its settles down usually after a few seconds. It bothered me but the thought of redoing the configuration when practically every joint is 1/2" from the next wasnt appealing and i couldnt think what the problem was but this year i decided i had to figure it out before the season and was looking at it and decided o close the caps on top of the discolator and the small vent and guess what no noise. So then Im thinking Im not supposed to do that tough Im not clear why they have caps if they need to stay open. so it seems to solve it and I wonder why and decide the pump is drawing air in from the vents which seems like it ought to be impossible for a vent to do exactly what its designed to solve but life sucks like that alot.Now some will remember i used the taco DT pump and it worked but with the KHNs logic modulating they would seesaw up and down not tripping but it wasnt ideal at all and since i only have one zone hooked up at this point i put the pump on fixed second speed until i add more zones ill then swap into the delta pressure version. so the pumps on second speed and theres a indirect with its own wilo 3 speed on full speed and the sound happens with DHW calls as well.
Why is this happening? I hear callefi make s a little check valve you can put on top before the cap i suppose that might work i assume i should leave the caps tight.
thanks for the help in advance.
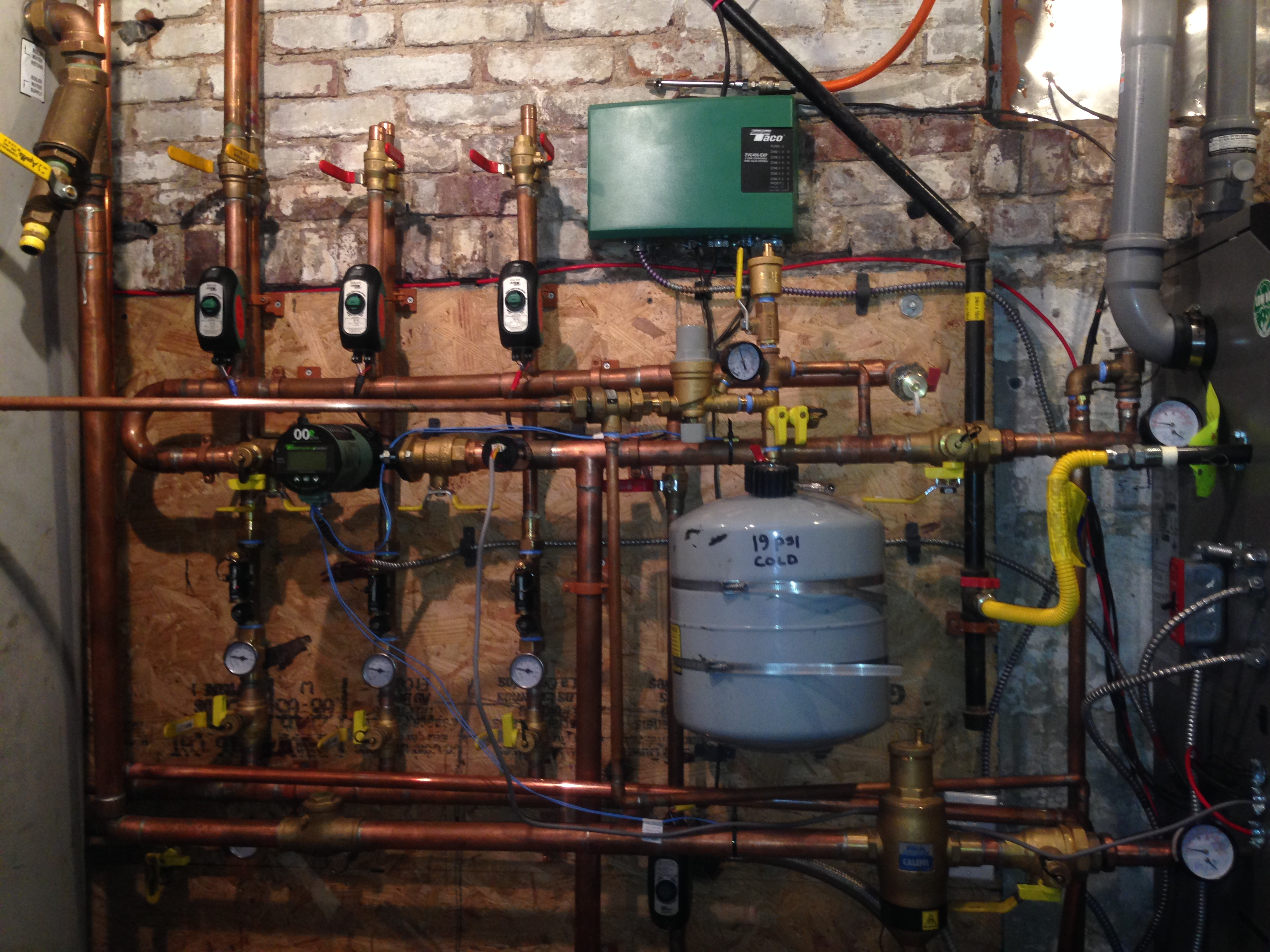
0
Comments
-
I had one more theory of cause, the boiler came with 1" S/R stubouts and I was making my bulkheads out of 1 1/4" for flow,and I also had already bought the fancy 1 1/4" isolation drain valves so i soldered 1 1/4 x 1" reducers right onto boiler stubs and wonder if that doing some weird pressure drop scenario.0
-
Which Lochinvar drawing shows the air eliminator on the return?
Really no need for the air vent at the expansion tank.
The DiscaDirt should be at the hottest point in the system, right at the boiler discharge. It should be where that large Webstone valve is at the boiler supply out, within inches if possible.
Also no need for a y strainer in the system the DiscalDirt is both an air and dirt eliminator.Bob "hot rod" Rohr
trainer for Caleffi NA
Living the hydronic dream1 -
Thanks Bob its been a while since I was neck deep in all this. reading your comment just now i thought i couldn't have made that big a mistake so I looked back at the miles of old threads and realized first i was misremembering what my KHN 085 install manual schematic 6-12 configuration was showing differently from siggs book and your guys advice. They were showing the pumps on the return, and also that sort of put the tank/ airsep downstream of pump although the water passed through the boiler first. So back then i asked you guys about pump location and it seemed the consensus was i could go ahead and change the pump to supply, but more importantly to make sure the tank ended upstream of the pump ("pumping away" i have an autographed copy) .-so far nothing controversial.
However i wanted to use the discal dirt mag separator so my tank would not be able to connect underneath that and space wise was pretty much maxed out on supply header. And i wanted to use the webstone tank valve, because you can never have too much brass in your boiler trim right? LOL. So I just saw in one thread you say the discal dirt mag could actually go anywhere (I think your reasoning was it was so large and efficient?) you also say although ideally a air separators best location is the high and hot spot lowest pressure etc. So in no way am i blaming you but Im guessing i decided then that i could put a small air eliminator on the webstone tank valve at the high hot spot just as the supply exits boiler, and since i had more room for the discaldirtmag just as it enters on the return which also sort of gave the boiler a air and dirt cleaning before boilers HX.
But Bob Ok I didn't put the discalmag in the absolute ideal place, but i do have a normal air relief valve in the ideal place, shouldnt that alone be enough and my return side discalmage be a suspenders on top of the belt? i mean its a closed system it shouldn't even have any air, unless my guess (btw from watching your caleffi video which mentions that pumps can sometime pull air in through the relief valves) is correct. the caps should be a bit loose correct?0 -
Pump away from the expansion tank, but the air eliminator needs to be in the hot point of the system.
I think it gets confusing when folks are use to hanging the expansion tank below the air sep. So you move the pump to pump into the boiler, but leave the air sep at the boiler supply, they don't need to be married together.
An air vent is not an air eliminator. The flow needs to go thru the device to scrub air 100%
As long as you have flow going around the air will make it back to the DiscalDirt on the return, it's not ideal and may take longer but it should scrub all the air out.Bob "hot rod" Rohr
trainer for Caleffi NA
Living the hydronic dream0 -
Let me see if i understand
Yes I am pumping away from the expansion tank both immediately after the boiler on the supply.
But if I were to move the pump to the return then I would be pumping into the ex tank, so I dont think you mean that.
Ok you re saying the smaller air vent i put on top of the ex tank is not in any way equivalent to an air sep. I didnt think it was or i wouldnt have bought the discal, but i thought it might be a help.
Then you write- "As long as you have flow going around the air will make it back to the DiscalDirt on the return, it's not ideal and may take longer but it should scrub all the air out."
which is pretty much what you said last year and still makes sense to me, and yet for several seconds immediately when boiler starts a heating or DHW call, i get that sound like a washing machine pumping out which I can only think is air, in fact the manual says its likely air. But then it stops after 2-4 seconds. its as if the air is not in the system randomly which should have worked out after a day, but always right there next to the boiler ready to be injected into HX just at start of pump. As you say it should come out at the discal before going into boiler but seems instead to be providing boiler with air. where can this air be coming from its not leaking?
0 -
When I installed my Lochinvar Nobel fire tube, I has a similar noise. I ran for 1/2 hour or more thinking the Discal would get rid of all that sound.
So I ended up putting a bucket under my relief valve, which is at the top of the boiler HX and blasting it for about 30 seconds.
Even though there is a vent on the pump inside the Nobel, and I had a high point vent above the boiler, for some unknown reason a bubble traps atop some HX and never makes it way out to the air sep device.
As soon as I did the purge through the relief all that gurgling went away, been 6 months now, noise free. It seen a handful of air traps in that type of design and needs a bit additional encouragement to get from the inside out. Worked for me, it is a simple thing to try, make sure the fill valve is on, of course.Bob "hot rod" Rohr
trainer for Caleffi NA
Living the hydronic dream2 -
That sounds like a promising idea thanks. i actually had a vague thought like that at one point but only opened it for a second let me try your idea.0
-
Bob if that doesnt work do you think the pump is pulling air in through the discal ( i closed the cap tight on the other to isolate the problem) and if so i suppose i should try one of those check valves in your video before repiping during heating season0
-
-
Bob
it didnt work, but then today i thought id try to do it even longer and it worked- but the noise returned even worse on the second call cycle, so i tried again, same thing, worked for the first call, then an unplanned DHW call came in as the second cycle and still no noise, hmm that's good maybe... but after the next call it came back again?
Then by accident I noticed during the noise the condensate line was blowing air sort of in rhythm with the noise. I had no grey PVC at the time and so i found pex fit well over the condensate stub temporarily , but thought it should have a tee for a vapor lock vent before i elbowed into the drain. It was out of the vent the air was blowing I pulled the whole thing off and the noise stopped. two more runs and that seems to be the problem i had created a sort of tuba.
Im not clear on how that worked, i know there's a combustion air fan synched to the modulation, maybe another for condensation? or maybe there's a damper that open sometimes opens into the condensation side? , i guess the cold water injected when the pressure relief was opened somehow changed the air ratio delivered to the condensation side which also is why once its warms up a few seconds into a cycle the noise stops?
well thats a big relief.
I still have some other problems im working on if you have any leads Id appreciate it.
1. I have a yellow screen with a message that says "service required please call" Is there a way to find out what service the unit is worried about, there's no code with the message. Im trying to re read the manuals but keep getting side tracked, couldnt find that mentioned in the trouble shoot section.
2. Post purge; the pump runs after the cycle is met, this i noticed first with the DHW and its great it gives you the excess heat still in the loop. but just now i noticed it also happens after a heating call is met, the problem is the pump must be dead heading because the zone valve has closed. I guess this is ok in other configurations like one loop or primary secondary, but I have a single pump and zone valves on headers. I suppose theres a way to program it away just wondered if this is a common situation.
3. does your boiler wait between heat calls, it seems if it gets another call before its cooled down for about 25 minutes it reads setpoint met and ignores the call. I find if i pull its SWT sensor out of the supply well to cool i can trick it to come right on, it wont do this right after a dhw call only between two close heat calls. again i suppose theres a way to program this away but seems like an odd default setting because with multizones you might often get calls close together and that would keep it perpetually backed up on calls waiting0 -
Yeah the manual is not very clear on some of these settings. The post purge for example, it doesn't indicate time period or if it can be disabled. if it;t just seconds I'd not worry too much about damaging a pump, minute or more, not great.
Probably need to call the rep or tech support.
Bob "hot rod" Rohr
trainer for Caleffi NA
Living the hydronic dream-1 -
Bob
Thanks yes i just talked to them the service needed reminder goes off automatically once a year for routine maintenance.
Speaking with them about the post purge/ dead head issue they were basically i piped it wrong attitude. and its true the closest configuration they had 6-12 was very close headers with zone valves,But they have a pressure differential bypass connecting the ends of the supply and return headers. Its been a while but an sure i considered that If I recall the answer was with a pressure differential pump its not needed there orr on the manifolds.Im guessing this post purge was not considered. I know you said not to worry but humor me because its sort o causing another inadvertent issue which i could solve various ways.
As I said the delta T didnt really work out well so its now on speed two but I only have one zone connected once i have multiple zones hooked up ill swap it for the delt pressure taco or grundfos think my head requires the viridian. In either case wouldnt adding a differential bypass to the headers confuse and defeat one of those pumps? {the other problem is it wont answer a second heat call for about 20 minutes because it seems i put the swt sensor too close to unit or the near boiler pipes are just too short for it too matter. since its not able to cool that water with a post purge it waits, it doesn't lock out and i have found if i trick it by pulling the sensor to cool it it'll start right up otherwise about 25 minutes.
I might be able find a way to tell the zone valve to stay open until after post purge either through the boilers or the taco zone controller, which would be easier than moving the sensor.0 -
I was hoping to hear that you got the other zones plumbed over the summer.
<div class="Quote">Keyote said >>> 1. I have a yellow screen with a message that says "service required please call"</div>
That is your annual maintenance reminder. You can reset the service reminder through the installer menu. It's the second-to-last menu option: "Service Notification"
<div class="Quote">Keyote said >>> 2. Post purge; the pump runs after the cycle is met</div>
The Circulation Pump parameters, also available through the installer menu, control their behavior. Pumps that are running will continue to run for their respective pump delay times before turning off, unless programmed to remain on continuously.
<div class="Quote">Keyote said >>> 3. does your boiler wait between heat calls, it seems if it gets another call before its cooled down for about 25 minutes it reads setpoint met and ignores the call.</div>
Also available on the installer menu, the SH1-3 offset & differential control this behavior. The offset default is 10° and the differential is 20°.
SH temp + offset = Setpoint Met, boiler will not fire
(SH temp + offset) - differential = Boiler will fire again
When you pull the sensor you reduce its temperature and 'trick' the boiler into thinking the differential was met.
<div class="Quote">Keyote said >>> i suppose theres a way to program this away but seems like an odd default setting because with multizones you might often get calls close together and that would keep it perpetually backed up on calls waiting</div>
It won't get backed up, per se. The call for heat should still open the zone valves, energize the circulator(s), and distribute the remaining heat/hot water that is above the differential even though the boiler isn't ready to fire.DIY'er ... ripped out a perfectly good forced-air furnace and replaced it with hot water & radiators.-1 -
HEY BOON Thanks,
Yes I finally did the sensible thing and called them which i was putting off until i reread the manuals. Yes was relieved to learn the service req msg was a routine, i admit i felt i could skip service for a year since i think i have light duty environment no hard water dust etc.
Re the wait between calls I think you missed my last comment, its sort of a combination of issues with several cures or as you say just ignore it from what i learned i could actually just leave that sensor out of the well if its not high limiting which it does not. I realize the calls remain open but just worry if they all have to be met simultaneously its not ideal. That top floors seems to have a greater load than anticipated. The post purge pumping would cool the water and avoid the delay but I have closed end headers ideally i would find a way to keep the post purge and get the zone valve to remain open for it. What happens now is a subsequent call for heat shows up on the zone controls indicator light but the valve doest open because the boiler is waiting for the water to cool i think to avoid a high limit. You would think it would at least run its pre purge then see if it still need to hold the ignition.
Yes i too was hoping i finished my reno past year instead i did very little. Well I did actually use those foam radiant panels routed and lined with graphite to add a wall zone to the coldest upstairs room to balance the two apts loads better. So i wasnt a total wastrel. Im going to use them to do the radiant ceilings on the remaining floors. decided to sell the house in a year so i need to get off my ****.
0 -
crazy month chasing this sound well at least it got me to tear it apart and brush out the HX and blow out the burner. they seemed fine at least burns nicer now, but then damn noise started again Can believe when i explained to lochinvar teck that air was blowing out my condensate drain they didnt nail the problem then instead of having me repipe my discalmag and cleaning the boiler etc.
so what was the problem? In side the condensate trap is aball the rises with condensate level to open drain only when sealed with cond. the opening has a rubber washer to make the ball seal well. they use a two sided paper backed adhesive to glue the rubber washer down to its seat. of course the paper dissolves in the cond. and the washer comes loose and bangs around so when the ball tries to come down it cant seal. So the flue gas start blasting out like jerichos trumpet with the ball and washer bouncing around hitting notes. making you think you $4K boiler is about to blow. Glues it in with some silicone hope that holds it. had to retap the traps top cover cause cheap tiny screws strip which seems typical doing the teardown all te fasteners must be chinese cause my good american tools always tiny bit loose also fasteners are all in these ridiculously hard to reach places unnecessarily. starting to not like this machine0 -
-
Ill know for sure in a couple hours when the silicone dries. But the very first thing i found was one time while it happened i was near the con discharge where i had piped a bit of pex with a tee as a vent before elbowing to drain. and when the noise went off i felt the air pulsing through that tee and described that to them but theyre clueless. said i might need to prime my condensate trap well i didnt know what was inside that box bu i knew id been filling up bucket with condensate before i got to piping the stub out so knew i didnt need to prime a trap. but after the cleaning yesterday and still hearing the noise i decided to take that apart and found that washer at an angle and what was left of the paper adhesive backer in the seat and realized the ball was not able to seal so flue gas was blasting out. usually on startup or mod down guess at full throttle it floods itself closed but when low fire not enough cond. Think that makes sense huh?
I dont get how that condensate recaptures heat the flue comes out of bottom of HX so does cond trap how does cond heat anything?0 -
You get the extra energy by the phase change which occurs from condensing the water vapor in the exhaust gas to liquid form.0
-
how does a phase change in my flue help the water in my pipes.
0 -
that's the condensation that would normally drip onto the burner in a normal boiler. it has condensed because the return water temp is low. the flue temp is low because the heat has been transferred into the cool incoming water.
0 -
The yellow message is a setting you or and installer can program to come on every year. It doesn't take a fault to activate it0
-
0
-
I know what the theory is i know all about dew point and condensation but my KHN 085 (firetube) as far as i can tell has the top fan combustion blowing down through the heat exchanger. at the bottom of the heat exchanger is the flue connection cpvc up and out and the condensate connection down and out.no secondary heat exchangers. so seems to me hot gases just exit cooling as they go and the condensate just falling back down the flue and out the condensate. and frankly the flue is still plenty hot when it leaves.0
-
The bottom of the hx is only 90 degrees on a perfect system. So the condensing is a result of the low return water not necessarily part of the process0
-
Thanks
so its just running the flue gas over the RW, well actually it runs it through all the water but exits the bottom of the exchanger over the coldest water incoming so the condensation is really happening all through through HX and any further condensation in the flue is wasted. i guess some have those secondary HX when they are side blow or bottom blow0 -
That’s why higher efficiency is obtained in the sub 130 degree return water range. The greater the delta between the flue condensate, and the return water in the hi, the more btus are extracted.0
-
hey gordy
so i cleaned it up (HX and burner) seemed pretty clean, though towards the end bad flame so guess burner was clogged a bit blew it out good, seems clean flame now.
but have this theory last year when i commissioned it it read CO2 8.5 which was in the books range but low end ( 8-10.5) so i left it rather than mess with it. I now learn loch is recommending 9.2 and my book rev A is up to rev J HMM
im thinking maybe 8.5 caused some problems like burner clogging (does that make sense?)
Anyway was going to get someone to come analyze since i borrowed boons last year. but tonight had one of those ideas that I could buy this fieldpiece analyzer for what it would cost someone to come and then next year i would still have it.
it seems youre supposed to pay $600 a year to have someone clean and re analyze you high efficient boiler every year which kinda takes all the efficiency out of the deal and I hear they wear out quick like maybe ten years who knew. anyway whdya think0
Categories
- All Categories
- 87K THE MAIN WALL
- 3.2K A-C, Heat Pumps & Refrigeration
- 58 Biomass
- 427 Carbon Monoxide Awareness
- 113 Chimneys & Flues
- 2.1K Domestic Hot Water
- 5.7K Gas Heating
- 109 Geothermal
- 161 Indoor-Air Quality
- 3.6K Oil Heating
- 70 Pipe Deterioration
- 995 Plumbing
- 6.3K Radiant Heating
- 391 Solar
- 15.4K Strictly Steam
- 3.4K Thermostats and Controls
- 55 Water Quality
- 44 Industry Classes
- 48 Job Opportunities
- 18 Recall Announcements