Vacuum gauge question on a Tigerloop with a new oil line install?

I have read mixed things about non-coated 3/8 copper fuel line being in contact with cement. Most of the stuff I read said it's required with buried lines. I redid my oil line from my tank to the burner after finding some issues and because the age of it. I bought the house from my great uncle and he said the oil line setup hasn't been touched in 30 years. The prior setup was firomatic valve off the bottom off the tank to a unfilter 77 then a 3/8 compression line (which I know they should not be used) to the burner with a firomatic shutoff with a flare fitting.
I removed everything back to the firomatic shutoff on the tank and installed a new General 1a25b with a felt filter. I then ran a 3/8 line with flare fittings on the general and the tigerloop.
My question is the vacuum gauge shows zero which I assume is because it is being gravity feed and will only show vacuum when the downstream general starts clogging up and creates vacuum on the line?
My other question is should I protect the 3/8 copper line. I can easily install a small piece of wood under it to keep it off the concrete floor though I don't know if that is necessary. I could also buy some plastic conduit wrap for it. The 30 year old line was run in almost the exact same spot along the concrete floor and had zero signs of corrosion.
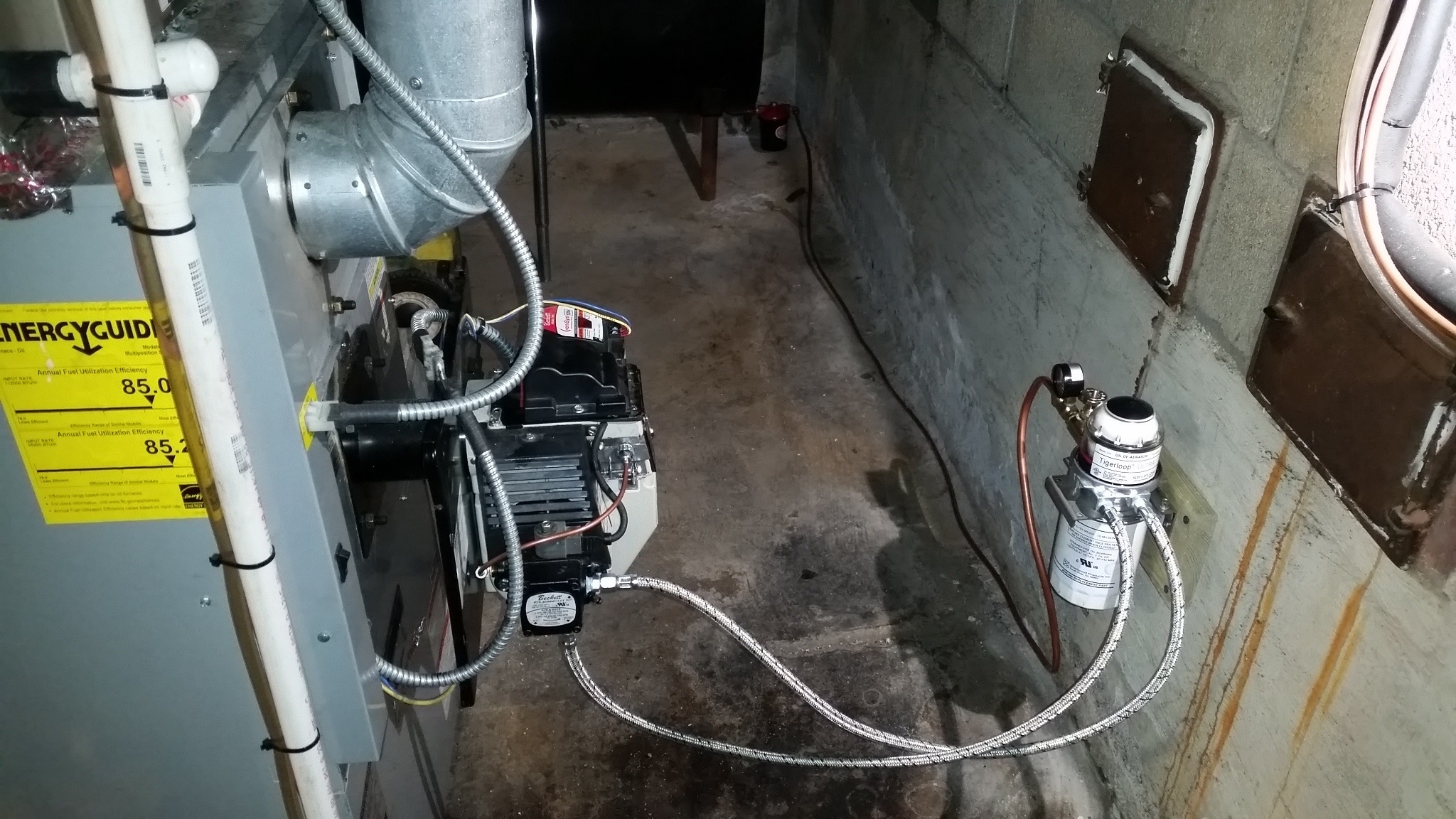
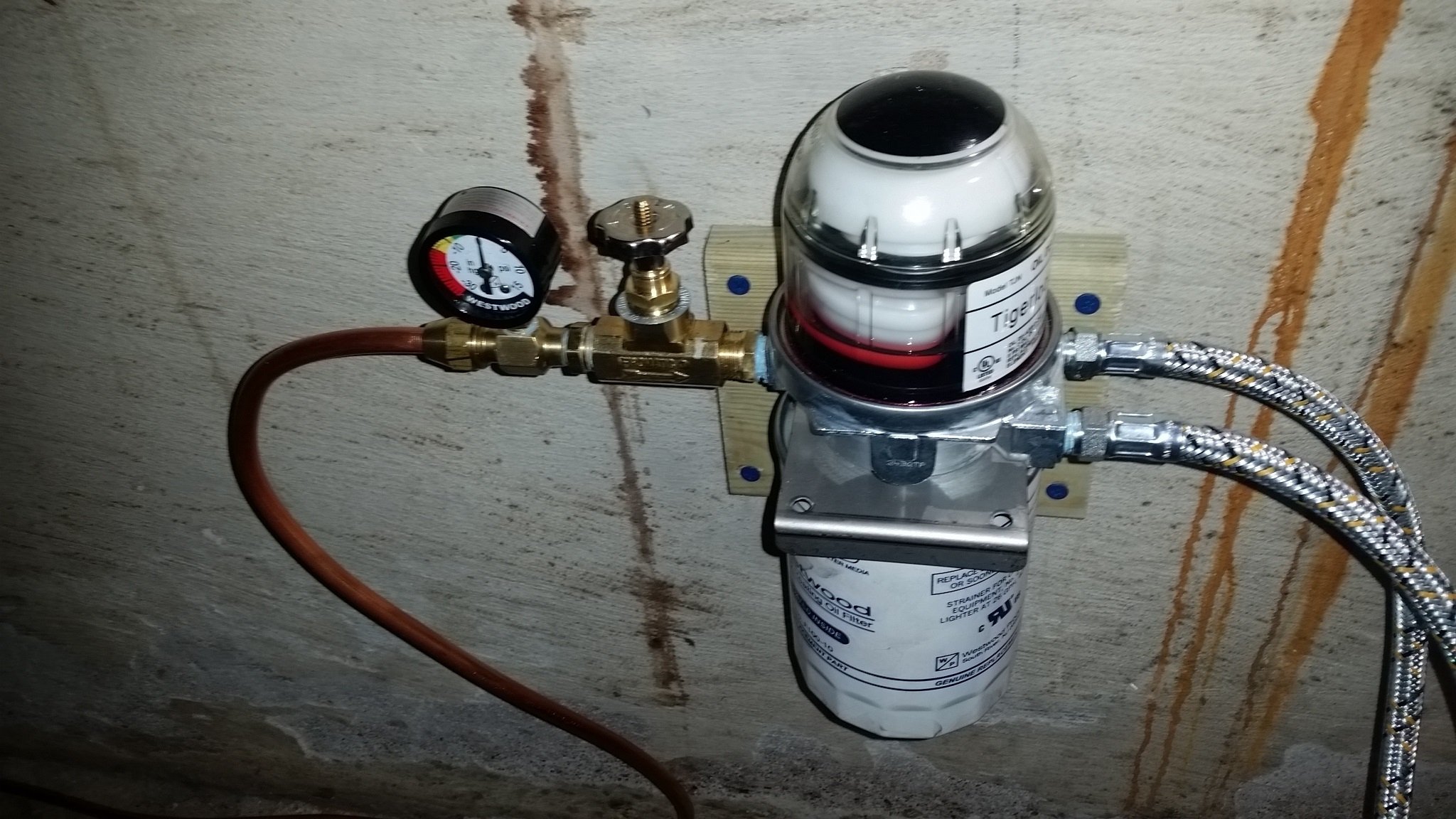
Comments
-
There won't be any vacuum on the gauge unless there is a restriction on the line feeding the Tigerloop. Seems to me it be a better location for the gauge to be on the suction line to the pump. Then it would read the filter. ( I think it actually shows this in the Tigerloop installation).
And, I would sleeve the fuel line just because. Most likely will be fine, but cheap insurance to get it off the concrete.
Rick0 -
Sheathing is required by code now in MA & RI. You should check your local code. BTW, the Tigerloop is overkill in your application.
The problem with compression fittings is they invariably leak.
Oil line can be purchased sheathed:
New England SteamWorks
Service, Installation, & Restoration of Steam Heating Systems
newenglandsteamworks.com2 -
we sleeve them in black water pipe...little extra protection..0
-
-
Before the pre-coated lines, we used non-metallic 1/2" liquidtight to protect the oil line. As RI steam mentioned, it is code in some states. It has been here in Mass since 1990, or at least on Cape. The Tigerloop is overkill for you. Always use flare fittings, and thermal valves. How does that NX run on that unit?1
-
Thanks for the input everyone. I ended up just putting some scrap 2x4's on the floor and the line is resting on top of them off the concrete.
I realize the Tigerloop is overkill but I had already purchased it as I was getting constant lockouts due to bad ignition and suspected air getting in the line. I figured I would just install it as it also had the 10 micron spin on filter. When I found a compression fitting on the old oil filter on the tank I just redid everything back to the tank. Every connection is now flared.
Its a night and day difference on ignition with the Tigerloop and not ever having to deal with bleeding the line again was worth it. Fuel oil is smelly and messy and my entire house would stink every time I bleed the line.
Though I don;'t have much experience with oil burners the NX has been great. The only adjustment is the pump pressure and the air/head setting is just one screw. It also has pre and post purge which I think helps big time.0 -
You are gravity feeding the oil to the burner. You would only need to bleed air out if you ran out of oil, or you have an air/vacuum leak when the oil level in the tank goes below the burner, and looks to be anything below 1/2 tank? You have put a band-aid on by using the Tigerloop. If you experience loss of prime, do a vacuum test to locate the source
1 -
-
You should send that pic to Tigerloop...
Never thought about 'Flir'ing it. I have a church with a 2 line, that the caretaker insists the 2 line 'warms up the tank', even though when you put your hand on the return line in the basement it's ice cold.There was an error rendering this rich post.
0 -
-
I did a filter change and relocated the gauge to the suction line off the tigerloop to the pump inlet. The gauge stays at zero when running. Should there be a vacuum on the suction line?rick in Alaska said:There won't be any vacuum on the gauge unless there is a restriction on the line feeding the Tigerloop. Seems to me it be a better location for the gauge to be on the suction line to the pump. Then it would read the filter. ( I think it actually shows this in the Tigerloop installation).
And, I would sleeve the fuel line just because. Most likely will be fine, but cheap insurance to get it off the concrete.
Rick
Also, as others have mentioned the wool filters let a ton of stuff through. When I replaced the 10 micron spin on filter there was a bunch of sludge/crap on the top. Still running on the same nozzle and my combustion analyzer shows its still running at peak efficiency
.0 -
Hi Brian,
If you don't mind me asking, what is the max negative reading on your vacuum gauge? I can't quite make it out in the pic?
Reason I ask is I just installed a vacuum gauge on my incoming suction line (my house is a 2 line system, I'm in Europe). We are bar, not psi readings.
When my German Weishaupt burner is running, my vacuum gauge shows -0.5, firmly in the middle of its "red" zone. Is this good, bad or what? I equally asked in my thread today too.
At rest (when burner is o"off"), of course it just sits at 0 to -0.01 bar.
Since we both have similar suction line sizes (yours is 3/8", or 10 mm, and mine is 12 mm, sheathed, 20+ yr old lines), I am curious what a good "vacuum" reading during a burner run is.
So, can you tell me the full range of your gauge (what is its 'green' zone range & its 'red' zone range?). Also, what does the vacuum gauge actually show when your burner is running---again, mine is showing -0.5 bar (or -7.5 psi), which I think might be too much or at least at the edge of what is acceptable (at least I hope, its winter here).?
Thanks!
Update: Think I just found, through Google, an answer:
Well, since I have a 'single-stage' pump, on a 2-line system, looks like I am exceeding the max of what Suntec recommends.My pump is a Danfoss, virtually identical to Suntec pumps. So my -0.5 vacuum reading during a run (in-ground tank, level lines from burner to tank, 20 feet run) equates to 14.75 HG, which is more than the max of 12 inches (Hg) states. Ugh..
0 -
This gauge is 15 psi pressure to 30 inch Hg, (-15 psi) vacuum. Green to -8”, yellow to -15”, then red to -30”.0
-
Thanks, scrook (are you Brian?),
I am at -14.75 (~0.5 bar) vacuum now. SteveUSA just posted in my thread a reading like that is "way too" high, and that my pump (which is a brand new Danfoss I just put on 2 wks ago) is going to fail or the seals blow or.... I realize I am right on the border line of that yellow & red section---didn't realize that means certain death for components.
Am dejected as he!!.I was hoping I could get by 3 or 4 months until spring thaw where I could lay new sheathed copper line from my underground tank to the burner (impossible to do it now, ground is frozen tundra where I live).
Anyhow, thanks again for the quick answer.0 -
This is correct. I have a Westwood gauge. My gauge stays at zero when I am running. I turned the firomatic valve off where it enters the tigerloop and it started to show a vacuum. I assume i have good flow and as the filter loads up it will show a vacuum?scrook said:This gauge is 15 psi pressure to 30 inch Hg, (-15 psi) vacuum. Green to -8”, yellow to -15”, then red to -30”.
0 -
Yes, a properly installed vacuum gauge should be able to show you the condition of the filter. I have a tiger loop and 10 micron spin on filter to my burner and the vacuum gauge is a great tool. Saves me from unnecessary filter replacements.
I wish all oil fired equipment was installed with a tiger loop ultra, vacuum gauge, digital primary control to enable pre and post purge. And a outdoor reset control should be mandatory too....0 -
I agree. Some will say the tigerloop is overkill especially with a 1 line gravity feed. I installed it for the benefits that Tigerloop advertises and have seen the results including proof in my earlier post with my FLIR that it heats the oil to 70 degrees. My Beckett NX lights off real smooth and runs flawless with it.SuperTech said:Yes, a properly installed vacuum gauge should be able to show you the condition of the filter. I have a tiger loop and 10 micron spin on filter to my burner and the vacuum gauge is a great tool. Saves me from unnecessary filter replacements.
I wish all oil fired equipment was installed with a tiger loop ultra, vacuum gauge, digital primary control to enable pre and post purge. And a outdoor reset control should be mandatory too....
I only changed the filter just to see what it looked like and relocate the vacuum gauge. Im pretty sure I can go probably 2 years before needing to do any maintenance. My combustion analyzer and smoke test shows the exact results from last year and I burned 2 tanks through it.1 -
That post with the FLIR camera picture of the tiger loop was awesome. I saved it to show to my customers proof of one of the many benefits of installing the tiger loop ultra.
The NX can be a tricky burner for some techs. I've had to re-tune several that were not properly set up. It can be a great burner, but I still prefer my AFG. You can't re-invent the wheel...0 -
I agree the NX when tuned runs great but it can take time to setup right. I have found mine runs best with a smaller nozzle with a higher pump pressure. It took some precision to dial it in with right pump pressure/nozzle/air setting. Once you find that sweet spot its a great burner.SuperTech said:That post with the FLIR camera picture of the tiger loop was awesome. I saved it to show to my customers proof of one of the many benefits of installing the tiger loop ultra.
The NX can be a tricky burner for some techs. I've had to re-tune several that were not properly set up. It can be a great burner, but I still prefer my AFG. You can't re-invent the wheel...
The Beckett Clean Cut pump it came with though did give me some issues but I swapped it out with a Suntec AV2A 30006 and its been good since then.1
Categories
- All Categories
- 87K THE MAIN WALL
- 3.2K A-C, Heat Pumps & Refrigeration
- 58 Biomass
- 427 Carbon Monoxide Awareness
- 113 Chimneys & Flues
- 2.1K Domestic Hot Water
- 5.7K Gas Heating
- 109 Geothermal
- 161 Indoor-Air Quality
- 3.6K Oil Heating
- 70 Pipe Deterioration
- 995 Plumbing
- 6.3K Radiant Heating
- 391 Solar
- 15.4K Strictly Steam
- 3.4K Thermostats and Controls
- 55 Water Quality
- 44 Industry Classes
- 48 Job Opportunities
- 18 Recall Announcements