Welcome! Here are the website rules, as well as some tips for using this forum.
Need to contact us? Visit https://heatinghelp.com/contact-us/.
Click here to Find a Contractor in your area.
Expansion Tank Placement
Options
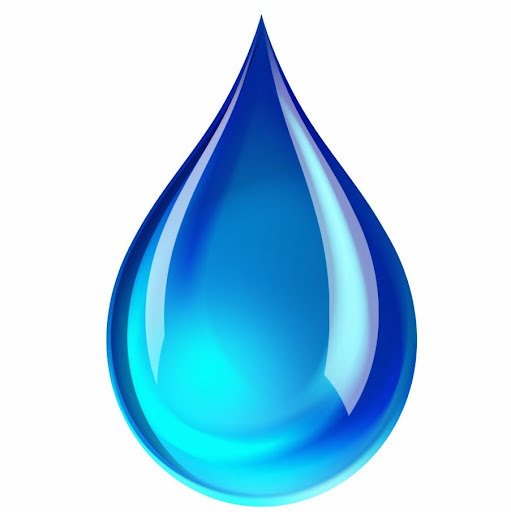
Dennis_Spectrum45
Member Posts: 3
in Geothermal
I am working on a large geothermal project. I am pumping water from a large geothermal loop field to multiple buildings a few hundred feet a way. In each building is a geothermal heat pump with a heat exchanger. Each heat pump uses a valve to allow water to circulate inside the heat exchanger and when it is satisfied it slowly closes.
The pump will be controlled by a frequency drive that will operate off of pressure.
The pumping station is located at the loop field underground. This is where the expansion tank, along with the pump will be located. The elevation rise from the pumping station to one of the legs of the system is estimated to be about 20ft, while the rest of the system will be relatively even.
The system volume is 3000 gallons of water, 21% antifreeze (methanol?)
The design Temp is 55 degrees
Min Temperature is 38 degrees
Max Temperature is 75 degrees
Fill Pressure is 25-30 psi
Max pressure (relief valve) is 70psi
A lot of professionals in the industry recommend putting the expansion tank on the suction side of the pump. However, I was also told that by putting it on the discharge, it would create a cushion for the pump when the valves at the heat pumps open and close. What are your thoughts on this?
Also, where is the best place to read the pressure of the system with the frequency drive.
The pump will be controlled by a frequency drive that will operate off of pressure.
The pumping station is located at the loop field underground. This is where the expansion tank, along with the pump will be located. The elevation rise from the pumping station to one of the legs of the system is estimated to be about 20ft, while the rest of the system will be relatively even.
The system volume is 3000 gallons of water, 21% antifreeze (methanol?)
The design Temp is 55 degrees
Min Temperature is 38 degrees
Max Temperature is 75 degrees
Fill Pressure is 25-30 psi
Max pressure (relief valve) is 70psi
A lot of professionals in the industry recommend putting the expansion tank on the suction side of the pump. However, I was also told that by putting it on the discharge, it would create a cushion for the pump when the valves at the heat pumps open and close. What are your thoughts on this?
Also, where is the best place to read the pressure of the system with the frequency drive.
0
Comments
-
Will the pump dead head when all the valves close? If so, you will want the drive to go into sleep mode at a specific signal. If this is the case, let me know and I can elaborate.
Cushion for the pump, do you meen to prevent hammer from the the last valve closing? Cheaper to make the last valve a 3-way valve, lose the sudden dead-head. The drive can be speed can be adjusted to slow quickly, this may help too.
The disadvantage of having the expansion tank on the discharge of the pump will be the point of no pressure change moving to that side. Where will the make-up water be entering the system? Every time the low side (suction) of the pump changes pressure, the make-up water will react when it reaches the pres reducing valves fill.
The expansion tank will gladly absorb your discharge pressure, but then you lose the available cushion you are looking for.
If you beleive water hammer is going to be an issue, resolve it by not allowing it to happen. Instal a 3 way valve in the loop to prevent dead-head.
Read the pressure for the drive (diferential) about 2/3rd into the loop, or at the very end. Each will have a distinct operational advantage, but you can explore both options.
When the valves open, esentially full flow, the diferential between the supply and return will be low, drive will then need to increase speed. When the valves close, difernetial pressure will be high, the drive will slow.
Don't run the pump into the NPSH range, fear here is damage to the pump. Dont run the pump slower than 6hz, as it may likely overheat the motor (consult with motor manufacture).
Did that help?
0 -
At certain times in this system, the pump will shut off because all of the geothermal heat pumps are satisfied. All the valves at the heat pumps are slow close belimo valves. This will let the drive slow down the pump to a standstill slowly. I am assuming this would weaken the argument for placing the expansion tank on the discharge side since there is hardly any hammer effect in my opinion.
This is a closed system. There is no make-up water. The same water circulates continuously.
I'm assuming by the end of the loop, this would classify as the return side, or the suction side of the pump.0 -
@aircooled81 , that was an impressive reply man. You have done some of this before I'm guessing !!!hvacfreak
Mechanical Enthusiast
Burnham MST 396 , 60 oz gauge , Tigerloop , Firomatic Check Valve , Mcdonnell Miller 67 lwco , Danfoss RA2k TRV'sEasyio FG20 Controller
0 -
Thank you @hvacfreak2 , I am flattered.
I have not worked on any geothermal loops, but hydronics is water and that I spend some time in once inawhile.
@Dennis_Spectrum45 , closed loop, I assume the original 20' was refrence to the total head for the loop then? If not, the lift from pump to high point in the loop will not be relevent.
Make-up water would be what you prime the system with, and have available should the system spring a leak. Should you choose not to have MUW, Think about protection from leaks, as you may dry run a pump should no one catch it in time. You could use a low pressure cut-out switch, or low water cut-out (never seen for this application though) upstream of the pump.
Remember the NPSH (net postitive suction head), the pump you choose will show this on the pump curve. If one zone running at minimum flow pulls your pump into this curve, you can loose a pump seal or impellar.
End of the loop would regarding the DP's location would certainly meen the diffrence between the supply and return pressure at the last heat-pump branch in the loop.
We will typically do this when we have multiple branches and can not find a reliable 2/3rd location because the loop is not one straight line.
The 2/3rd option will allow for a more moderate average of the entire loop. If the loop is 400' long in a straight shot, you can put the dp after the 66% mark and be able to have a reliable measurment to assist the last load off the loop, and still not over-shoot the first load branched off the loop.
Pump should not be slowed to a standstill. The speed below 10% of the pumps rpm can have a negative affect on motor temperature and bearing wear. You might not be on the curve either, especially if you dont get the largest impellar for that pump.
The nice part about a drive is you can get the largest cut impellar, and still stay within the efficiency range of the pump curve well. If you have a severley cut impellar, at slow speed the water comes off the tip of the impellar and goofs around inside the valute because there is extra space to do so.
I would suggest when all the valves have closed, this is where it gets to lets say 6 to 10hz minum speed, holds this as the low speed. Should it not see a request within 90 seconds to 2 minutes for speed increase it goes to sleep.
This is just some drive programming and available on most drives (at least the ones I typically see)
Is this loop just discharge from the pump, branchs to each load, with no return to pump unless it's through a load (heat pump condenser barrel)? I meen thats what I am gathering, single loop, single pump, no bypass back to the pump from disch to suction.
Does each heat pump control it's required flow through that belimo valve? This would be where it modulated due to the inlet water temp being too cool or warm for the dx side to maintain head pressure. Or does each heat pump also have it's own condenser water regulator? If so....
Make sure at low flow, lets say one zone is calling and requires minamal flow to keep condenser temps where it wants, your pump speed it not so low it shuts off too soon. There might be a balancing act here, have you chosen the pumps, dp, drive and actuated valves yet?
0 -
This is just a single loop and no return unless it goes through the heat pumps.
Each heat pump slowly opens a valve to a set point, in this case 3gpm per ton. When satisfied, it slowly closes again.
What I am wondering is if the idea of the expansion tank on the discharge side of the pump is a good idea when considering that it would possibly be a cushion to the pump.0 -
Hydraulic cushion, I would assume you are concerened with watter hammer.
Seperate devices for water hammer,
http://www.amtrol.com/diatrol.html
Or
http://www.flexicraft.com/Hydropad_Accumulator/Surge/?gclid=CjwKEAjwqJ67BRCzzJ7Hy-LYlFYSJABwp9PG7IqEW3CrOl2idgB8jEV2Y_JvnuPkylF3Bx-yujLHMBoCo1rw_wcB
Expansion tank is the point of no pressure change, not a shock absorber for the loop. I get the theory behind the idea, it is just not going to help.
The other option to prventing this "shock" would be to make one of the 2-way valves a 3-way valve.0 -
This is a great read, you would also enjoy the book "pumping away", I did.
https://heatinghelp.com/systems-help-center/the-point-of-no-pressure-change/0 -
I would upsize the expansion tank at least one size and use two pressure switches. One trips below (perhaps 5 PSI) the design operating pressure for the loop, and is wired to an audible alarm. The second switch should be set just above the minimum pressure required to maintain NPSH at the pump inlet, and is wired to the VFD so it kills the pump.aircooled81 said:Make-up water would be what you prime the system with, and have available should the system spring a leak. Should you choose not to have MUW, Think about protection from leaks, as you may dry run a pump should no one catch it in time. You could use a low pressure cut-out switch
0 -
A flow switch would be another protection device to consider.Bob "hot rod" Rohr
trainer for Caleffi NA
Living the hydronic dream0
Categories
- All Categories
- 87K THE MAIN WALL
- 3.2K A-C, Heat Pumps & Refrigeration
- 58 Biomass
- 427 Carbon Monoxide Awareness
- 113 Chimneys & Flues
- 2.1K Domestic Hot Water
- 5.7K Gas Heating
- 109 Geothermal
- 161 Indoor-Air Quality
- 3.6K Oil Heating
- 70 Pipe Deterioration
- 995 Plumbing
- 6.3K Radiant Heating
- 391 Solar
- 15.4K Strictly Steam
- 3.4K Thermostats and Controls
- 55 Water Quality
- 44 Industry Classes
- 48 Job Opportunities
- 18 Recall Announcements