Welcome! Here are the website rules, as well as some tips for using this forum.
Need to contact us? Visit https://heatinghelp.com/contact-us/.
Click here to Find a Contractor in your area.
Delta p vs delta t
Options
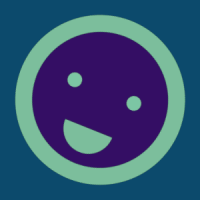
Snowmelt
Member Posts: 1,438
Just curious because I was reading the grundfos pressure pump, but there is a delta t pump that measure the true temperature of supply and return.
Who uses what and why?
Who uses what and why?
0
Comments
-
I use both
I have had this discussion a bunch of times, I have tried and tested the taco bumble bee vs the g-foss alpha in my own personal systems..
First Delta T- I use these to feed single zones, they work great on an air handler, baseboard, radiant, ect when you have a separate circ for each zone... The bumble bee will let you set your delta {say 25 degrees} so it will start out fast and then ramp down so that the emitter has a chance to emit the energy...
Now the alpha has its place too, I use these to feed zone valves, systems with trv's, and I like them for primary loops. They seem to work well on systems that change and feed more than one zone...
For example I notice when using delta t for a pump feeding 3 zone valves, what happens is- the first zone calls, the pump ramps and after a minute or so adjusts to match your desired delta, then another zone calls and now a head full of cold water comes by the shared return {where the return sensor is located} and speeds up the pump, but it speeds the zone that it originally had slowed down. After a few minutes it will all regulate and it works, but what I found is with the alpha, it sees the pressure differences when the second zone opens and adjusts itself accordingly, ramping up but not to full speed, just a little and then after a minute it evens out..
I watched a system with the Thermal imager and I like the delta P for multi zone single circ systems.... While I still think separate Delta t for each zone is the best way to pipe a system, zone valves are here to stay, I personally don't use them in new installs for a few reasons {when one pump goes down the entire property goes with out heat, its impossible to properly size a non variable pump since 1 zone can call or 6 changing the pumps demands, ect}..
I just find the small cost difference in zv vs separate circs is not enough to make up for the short comings.. I cant say I never use them, but when I do I try to keep it to 3 per circ {depending on zone size} and when you do this the costs will surpass separate circs..
Anyway back to delta p vs t, I also like delta p for primary loops, they seem to adapt well to zone circs pulling from the loop and the changing the flow needs...
So they both have their places, I am sure someone will be making a circ soon that does both under certain situations, I am also sure someone will perfect getting rid of zone controls, in the near future you will just plug the t-stat rite into the circ, connect all circs together and plug the circ rite into the boiler control, and for zone valve apps you will plug the tstat into the zv plug the zv into the circ and circ into the boiler control. Zone boards will be a thing of the past..
Taco already have the circs with s-relays built in, just a matter of time and circs will have burners built in, lol...0 -
Well said
∆P pumps work like a charm with the proportional zone valves we use (think electric TRV.) I save the ∆T pumps for zones large enough to actually need their own pump. Given that the smallest smart circs currently available have curves roughly equivalent to a 008, the overwhelming majority get CCVs.0 -
Both great circs in there applications
I like them both, but they both have their place where they shine. I've had better consistent control and results with a lot fewer call backs using the Delta T circs. But the majority of our retrofits are 1-3 circ systems, and 1-4 zones. 1 circ and 2-3 ZV's are the most common. Using set point or DT , I get setup now. A few stadler strap on gauges , some zone balancing and I have results.
With the alpha, customers are NOT patient enough for the learning curve and I usually end up setting a fixed pressure for quick happy customers and for consistent results. I will admit I don't think the alpha shines for me until I have more than 4 ZV's and I have to add or balance the system to get even temps. If the zones are of large differing loads, they have to be balanced to get even return temps. This is where we are maxing out the auto adapt GPM limits, where fixed pressure says it will flow much more according to the chart. I would say I don't have enough time or proper applications to do justice for the alpha, and also why I was asking more questions about the auto adapt to answer my customers with more detail.
I do think there is more brand bandwagon riding at the supply house than real usable info, not real in depth like we have here. Thanks0 -
CCV
Are you creating your own proportional zone valves with CCVs somehow?0 -
Characterized Control Valves
From Belimo https://www.belimo.us/americas/ccv.html We pair them with DDC using 2-10V outputs.0 -
Is this true
Just thinking to myself and out loud to my fellow wet heads
Is it true that with the delta p, the pump has no idea of water temp. There for if the temp outside is 50 and you have no odr the pump really can't identify water temp to get a tru 20 degree differential. Or does the water temp have anything to do with the pressure of what is going on with the system.
The delta t pump knows temp all the time there for can adjust / adapt to any situation. Like the 2nd post said when a zone opens it gets a cold rush so it ramps up for a few minutes until the zone water gets hot then levels out.0 -
DDC
What outputs the 2-10v? There is a thermostat that does this?0 -
DDC = Direct Digital Control
In our case, programmable BACnet devices from http://www.reliablecontrols.com/
The Honeywell TB7980 outputs 0-10V or 2-10V, but has fixed PI parameters optimized for coils. Viconics has a few stats with a bit more programmability. Noting in the "small zoning box" category of which I am currently aware.0 -
∆T pump
You mentioned saving ∆T pumps for larger zones. In this case, are you then controlling the pump directly with 0-10volt or utilizing a pulse width modulation approach?0 -
∆T control
of larger zones generally means installing supply and return thermistors and adding a 0-10V module to the pump. Simpler and less expensive to have a pump with built-in controls, but not so many options there. For larger commercial projects the added costs (two thermowells, two sensors, two control inputs, installation and programming) generally pan out.0 -
keep researching
Really the heat emitters are what drive the system temperature, called thermal equilibrium (TE). All systems will seek thermal equilibrium, if not for the temperature limiting or controlling devices we add, the fluid temperature would adjusts to attain TE
Check this link for some better reading on this and other fundamentals.
http://www.caleffi.com/sites/default/files/file/idronics_12.pdf
See page 51
You can control heat output by temperature, or flow.
A delta P circ adjusts it output (speed)to match the changing hydraulics as ZVs open and close, really no need for temperature input.
Hydraulic equilibrium (HE) is the point where the head loss curve crosses the pump curve, see page 31 of the above mentioned journal. Delta p technology is aimed at pinning near perfect HE. As we agree the perfect pump curve would be a straight line
Delta t circs try to accomplish the heat output balance by adjusting their output (speed) based on two temperature inputs. This can be helpful in some applications.
I'm not convinced "fixing" or trying to fix a set delta T is always an advantage. Watch any well designed hydronic system operate across a range of conditions from start up to shutdown and observe an ever-changing delta T condition.
Energy transfers related to delta T. Wider deltas move more energy, consider a cold slab start up, especially a snowmelt as your handle reminds me. Huge delta Ts on start up ramp the energy to the load quickly, the delta T lessens as the emitter nears the shutdown, setpoint condition.
The goal of a cold start is to move the energy to the load ASAP, not constipated by a fixed delta T.
Balancing valves are a under-ultilized component in residential hydronics. Designers calculate a design flow rate for best performance, the balance valve assures multiple zones, circuits, or levels of a multi story building get the required flow under all conditions.
The type of balance valve you chose is important. IF you require a fixed flow rate under varying delta P conditions, you need a PIBV, "pressure independent balance valve". This valve has a floating spool and a designed passage that allows it to adjust flow as the delta P changes.
Manually set balance valve cannot adjust, or change their settings automatically as the systems delta p changes.
Also see HPAC magazine Jan/Feb 2010 article "A pair of Certainties" to learn more about the two "equilibrium" sisters, crucial to system design and troubleshooting.Bob "hot rod" Rohr
trainer for Caleffi NA
Living the hydronic dream0 -
Hot Rod
like0
Categories
- All Categories
- 87.1K THE MAIN WALL
- 3.2K A-C, Heat Pumps & Refrigeration
- 58 Biomass
- 427 Carbon Monoxide Awareness
- 113 Chimneys & Flues
- 2.1K Domestic Hot Water
- 5.7K Gas Heating
- 110 Geothermal
- 161 Indoor-Air Quality
- 3.6K Oil Heating
- 70 Pipe Deterioration
- 996 Plumbing
- 6.3K Radiant Heating
- 391 Solar
- 15.4K Strictly Steam
- 3.4K Thermostats and Controls
- 55 Water Quality
- 44 Industry Classes
- 48 Job Opportunities
- 18 Recall Announcements