Welcome! Here are the website rules, as well as some tips for using this forum.
Need to contact us? Visit https://heatinghelp.com/contact-us/.
Click here to Find a Contractor in your area.
Revising heatloss calc with addition of unvented attic
Options
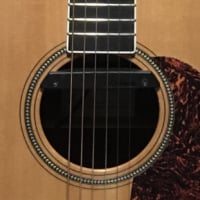
D107
Member Posts: 1,911
I need to adjust my previous heat loss calc to the
addition of an unvented attic. With the removal of the insulation in the attic
floor (2fl ceiling) I assume that whole space has to be added as another room,
and account for the change in the location of the cold ceiling.
The leaky old existing fiberglass insulation under the attic
floor and ac duct intrusions are very ineffective. I’m guessing with some
reasonably tight insulation under the attic eaves and gable walls, real heat
loss could decrease even with addition of the new ‘room’. I’d be curious to
hear if others who have done this found their heating costs decrease.
This expansion is predicated upon our ability to move the ac
ducts under the attic floor; we should know soon after exploring any possible
obstructions. If it turns out to be not doable, and we do a vented attic, I
was wondering if it’s possible to isolate the ac handler and manifold in a
mini-conditioned space, and thereby increase its efficiency. Has this kind of
thing been done?
Thanks.
addition of an unvented attic. With the removal of the insulation in the attic
floor (2fl ceiling) I assume that whole space has to be added as another room,
and account for the change in the location of the cold ceiling.
The leaky old existing fiberglass insulation under the attic
floor and ac duct intrusions are very ineffective. I’m guessing with some
reasonably tight insulation under the attic eaves and gable walls, real heat
loss could decrease even with addition of the new ‘room’. I’d be curious to
hear if others who have done this found their heating costs decrease.
This expansion is predicated upon our ability to move the ac
ducts under the attic floor; we should know soon after exploring any possible
obstructions. If it turns out to be not doable, and we do a vented attic, I
was wondering if it’s possible to isolate the ac handler and manifold in a
mini-conditioned space, and thereby increase its efficiency. Has this kind of
thing been done?
Thanks.
0
Comments
-
PS No rads in attic
I forgot to mention there will be no rads in the attic since we're not making this into a habitable space, so I'd expect the attic to be a few degrees colder than the floor below, heated in effect by heat rising from the rest of the house. Not sure how you calc that kind of added loss.0 -
Attic Heat Loss:
It has always been my understanding that an enclosed attic space is figured at 1/2 the heat loss of an outside space. Because the average of the space is 50% of the inside space and the outside space. Removing the attic insulation because it "leaks" must be a new and novel idea that I haven't heard about. As I age, I'm learning that everything I learned appears to be wrong. I don't understand the concept of removing all the insulation because of some infiltration. Air Handlers and AC units in attics that I have seen, often deliver conditioned air that would be great in the winter and air in the winter that would be great in the summer.
That same concept of heat loss applies to knee walls and other unconditioned enclosed spaces. The only ones that don't fall in that rule are garages because you can leave the doors open to the outside. My home was built in 2000, has a two car attached garage with a heated space over it with an insulated floor and one side abuts the heated house. I have never had anything freeze in the garage and I keep water and soda in the floor. It has been down to zero with 30 MPH winds and no freezing.0 -
I
thought it was just me........Why go through all that work, when simply properly insulating what you have now, accomplishes the same thing. If you were reclaiming usable space, it would make sense.0 -
Clarifying....
Regret if some of the plan wasn't clear. The attic is currently not conditioned--owing to the insulation under the floor. So we are reclaiming space that was not usable before--too hot in summer (for humans and AC handler alike) too cold in winter. Sort of a vented attic w/o the vents, converted to unvented attic space.
I believe it is actually a requirement to remove the old insulation under the attic floor, just like houses don't usually have insulation in the ceilings between floors; we are adding a floor in a sense. If we left the old insulation in, the attic would not be heated too well at all. Building Science.com goes into this alot but I believe making the attic part of the envelope means that some of the heat will rise to keep the roof decking warm enough to not condense in the cold.
So, expanding the envelope by removing one level of insulation and adding insulation under attic eaves and gable walls making the rooftop and walls the new ceiling. Also need to remove insulation to bury the AC ducts. See photos.0 -
So
you'll redo the heat loss for all the rooms below the attic, change the ceiling heights( you plan to vent through), and add necessary emitters?0 -
No
'change the ceiling heights you plan to vent through'. I am not venting through anything; this is an unvented attic, no soffit, ridge, gable, mushroom or other vents. Based on the hydronics institute heat loss method, I don't think I'd be changing the ceiling heights in my calculation, but I'd have to add the attic space as part of the heat loss--maybe at 50% as Ice Sailor says since we're not heating to 70 degrees. And the second floor ceiling, previously considered a 'cold ceiling' would now only be partially cold, and the attic ceiling (roof) would be the new cold ceiling. The old heat loss was 50K with very leaky 2fl ceiling insulation; with tight attic insulation now I'd bet I get the extra space without increasing the loss. If I was going with a vented attic, I would re-do the existing insulation as tight as I could.
I can't add emitters given that our attic size isn't large enough to legally convert to what I believe is called 'habitable space' with heating, plumbing etc. We have way-oversized cast iron rads so emitters are fine as is.
Here is a quote from Building Design's Joe Lstiburek's "Builder's Guide To Cold Climates": (for unvented attics)..."the key is to keep the roof deck--the principal condensing surface in roof assemblies--sufficiently warm throughout the year. This can be accomplished....principally through the use of rigid insulation installed above the roof deck or air-impermeable spray foam insulation installed under the roof deck in direct contact with it..."
I am currently researching and getting advice on the kinds of insulation to use. Sometimes insulation is put both above and below the roof deck to get near the required R38 in this Zone 4. The initial impetus for this was to reclaim the space by burying those AC ducts.0 -
Sorry
I misread your post. I thought you were planning on adding registers in the ceiling to heat the space. Two pound urethane foam is what I would use.0 -
spray this
Not a polyurethane fan for the most part. A good wet-spray cellulose would be my choice for this application, and polystyrene (XPS preferred) for sheet goods.0 -
You need spray foam if workling from the underside
Unless you are going to strip the roof and apply rigid insulation to the topside of the roof decking, you will need to install spray foam.
Since you mentioned R-38, I assume you are in either Climate Zone 4 or 5. Depending on which zone, you will need to install a minimum of R-15 or R-20 foam directly to the underside of the sheathing. You can top off with fiberglass or cellulose to reach the required R-38, or you can foam the entire thing.
Given the depth of your rafters, closed cel foam is the only product that will get you near R-38 in that depth. If you want to fur the rafters down, you have more choices (open cel, fiberglass).
The caveat here is that if you use the attic for storage, you must install a thermal barrier over the foam. A thermal barrier is 1/2" drywall-- you cannot leave it exposed. See sections R314.4 and R314.5 of the residential code.
Tim0 -
Heat Loss:
I guess I totally disagree with this premise from experience. If any code that says that you MUST remove insulation from between floors, it is just plain wrong. STUPIDLY wrong. You mentioned IBR. Without going upstairs and getting my IBR book or switching programs in my computer, we'll say that in your case, the insulated ceiling (for for the attic) has a insulated heat loss factor of .05 but if you remove the insulation, it becomes .25. I can't locate my old H-22 IBR heat loss guide that retards like myself used for years. I have the new and improved version that is easier to use and no one seems to use it because it is mostly incomprehensible to me. However, just the heat loss of the ceiling in a 24' X48' ranch or Cape with an unfinished attic space, the heat loss in the entire un-insulated ceiling is around 20160 BUT's per hour (.25). If the ceiling is insulated with 10" of fiberglass insulation and now looses 4032 BTU's per hour. One needs 33'+ of baseboard (uninsulated) and the other needs 6' (insulated) which is divided in half. When I figure by hand, I don't bother with ceiling loss in rooms that have that insulated ceiling factor because if the room comes out to needing 3.34' of baseboard, I am going to use a 4' length. If it is uninsulated, I figure it. If it is a cape with a knee wall, I figure it as "outside" even though I can divide the wall loss by 1/2. Its fudge factor.
My current home is fully insulated in all ceilings for heat loss and sound transmission. Any code that requires you to remove insulation if you finish the attic was written by building design zealots that are deserving of the Bill Maher HUA award. Houses breath. Wood breaths. Take a spray bottle and spray water on the floor boards. Then spray the same amount of water on a piece of foam board. A foam meat container will do. Which one has all the water disappear first? The wood floor. When the water on the foam board is finally gone, the floor will be completely dry and no sign of the water remains. We old farts used to nail on shingle siding with 1 1/4" to 1 3/8" common galvanized shingle nails, They stuck through siding by 1/4" +/-. Now, everything is air nailed. Because SS ring nails saw" a hole in the wood while being driven home, expansion will work them out. But they use 1 1/2" or 2" SS ring nails. I have seen ice formed around the protruding nails the size of golf balls when the insulation is pulled away. Where did the moisture come from? It came through the insulation. The nail through convection, transfers the outside cold into the heated space and moisture forms as ice on the cold nail point. A code may say that you can't turn the attic spacer into a bedroom but you can turn it into finished space. I would leave the insulation in the floor. Insulate the rafters with trays to let air pass under the roof sheathing and ventilate the ridge. That brings the AC into a warmer of cooler space. I would power ventilate the attic space with power out the gable ends with fans controlled by thermostats and humidistats. Do you see any mildew or rot on the inside of all that sheathing? That old boarding will absorb a tremendous amount of moisture. Its been doing it as long as the house is standing. And if the house is wrapped with #15 tar paper, the moisture goes through that, both ways and doesn't support rot. Only water leaking on to the wood will do that.0 -
I agree
As I mentioned on a separate air quality thread, there are enough reports of problems with spray foam from both installer error and adverse reactions for me to take that kind of risk with an oil-based product that hasn't been in use long enough to be confident in its use. (Recall the formaldehyde problems years ago.) Removing it once it's in is a major project since it hardens like a rock and has to be chopped out. So even if there's no adverse reaction, if you ever need to replace the roof sheathing, it's an issue. Also those products that say they are bio-based--soy etc--are really not that different. They are allowed to have a very small percentage of bio-based material to use that moniker.0 -
Yes
We're Zone 4. As you said because my rafters are only 5.5inches deep, it presents all kinds of problems. If I fur down to get more insulation in--and then add some rigid board to lessen thermal bridging, then the sheetrock for the fire-rating, I've lowered my ceiling to the point where the entire space becomes less desirable.
If I add two or four inches of foam above the roof deck--plus another layer of plywood sheathing on top of that to hold it all in place, I also have to rebuild the fascias and rake molding to accommodate the new roof height. Drilling in long screws through all this is sometimes not easy either. All becomes added cost.
In all cases I have to be mindful of the acceptable dead load, and allow for snow load on an old 1924 roof.
I also must get some kind of sensor to check the attic floor to find out where the wiring and junction boxes are. I'd hate to open the floor to find out I have major electrical re-wiring to do in order to move those AC ducts underneath.0 -
furring up
We've had good luck adding 1-1/2" of rigid foam above the roof deck (after tear-off.) Run 2 x 2 stringers perpendicular to the joists, on 16" or 24" centers (depends on wind zone, check with your engineer) then rip the foam board so it fits snugly between them. Fastening a metal roof on top works quite well, but the roofers will need extra long fasteners and they have to stay on layout far more tightly than they usually do. Adding that extra R-7.5 (polystyrene) or R-10 (PolyIso) plus significantly reducing thermal bridging (down to the 1-1/2" square area where the furring and the joists cross) you get a significant reduction in the assembly U-value. You do have to re-work (or more frequently replace in the case of an older building) the fascia, but the improvement is significant. I've seen 15F reductions in indoor summer temps after doing this to a south facing slope over a clerestory living room.0 -
polystyrene
Thanks very much. OK so from roof deck up it would be:
felt paper/underlayment (ice/water shield for first two feet above eaves), 2x2s (in reality a 1.5 right?) with 1.5inch polyiso in between, then no 3/4" ply? then asphalt shingles? you'd want alot of those screws going into the 2x2 AND the joists not just the sheathing right? There are reports of the long screws--with washers built in?--themselves being a thermal bridge and causing dripping onto the attic floor. I hope to have an ERV which should reduce moisture buildup.) Then you have to build up the rake fascia, yes? Is the fascia rebuild a big job for an experienced roofer? I'd definitely have to find a roofer willing to do something different than usual--around here they just bang 'em in quick.
What is the advantage of your method vs just putting the polyiso boards in whole above the underlayment and then plywood over that then the shingles?
They say it's best to balance the insulation from above and below. If I had 5.5" sprayed cellulose under the eaves (possibly having eco-sealed the deck underside first at the joints), that's R21, plus an inch of polyiso and sheetrock AND if I can count the shingles, underlayment and sheathing as part of the assembly that might put me near R30 which I understand is really the minimum in this zone 4. This would be without any additional insulation above the roofline.0 -
Metal Roofing
- Metal roofs have coatings that prevent 75 to 80 percent of the sun's energy from being absorbed into the roof.A metal roof can reduce roof surface temperatures by 60 to 70 degrees.
0 -
layers
You will need sheathing if you're doing shingles. Better check your local codes - it's been over a decade since we did these and the assembly I described was engineered for a metal roof. Adhesives are continuously improving so it's worth checking with a few different manufacturers to see if they have a recipe that works sans fasteners.0 -
metal roofs
Having owned a couple now I would never go back to composite roofing. A properly installed standing seam roof (or something else with hidden fasteners) will outlive the lot of us.0 -
Before
the economy went in the toilet, I repaired, set up and installed standing seam machines and gutter machines.The "old school" metal roofs would last 80 or 90 years without leaking. They had none of the modern coatings applied to them.They are not the "tin roofs" of old, and now are being installed on mansions.We had a few contractors that did nothing but copper roofs.0 -
more metal
Copper roofs were spendy when copper was $0.60/lb. I wouldn't even want to guess what they cost now. Slate might be cheaper...
70% Kynar is miraculous stuff. Anything less on a window around here and you're asking for trouble.0
This discussion has been closed.
Categories
- All Categories
- 87K THE MAIN WALL
- 3.2K A-C, Heat Pumps & Refrigeration
- 57 Biomass
- 426 Carbon Monoxide Awareness
- 116 Chimneys & Flues
- 2.1K Domestic Hot Water
- 5.7K Gas Heating
- 109 Geothermal
- 160 Indoor-Air Quality
- 3.6K Oil Heating
- 70 Pipe Deterioration
- 991 Plumbing
- 6.3K Radiant Heating
- 389 Solar
- 15.4K Strictly Steam
- 3.4K Thermostats and Controls
- 54 Water Quality
- 44 Industry Classes
- 48 Job Opportunities
- 18 Recall Announcements