Welcome! Here are the website rules, as well as some tips for using this forum.
Need to contact us? Visit https://heatinghelp.com/contact-us/.
Click here to Find a Contractor in your area.
Conservation versus efficiency?
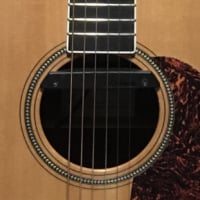
D107
Member Posts: 1,906
Thanks for the feedback last month Constantin on the corbond. I was at a buildings conference last week and a contractor who does both open and closed cell said with closed cell you'd never know if your roof was leaking which could rot the wood sheathing. I guess that makes sense.
I'm also hoping that installing a new roof after foaming the attic would not be problematic as long as not alot of sheathing has to be replaced, therefore upsetting the foam. Roof/nail tearoff and shingle renailing shouldn't be a problem I guess....
Alot of closed cell foam installers are recommending only 2 inches of it (saves money I'm sure).
Thanks,
David
I'm also hoping that installing a new roof after foaming the attic would not be problematic as long as not alot of sheathing has to be replaced, therefore upsetting the foam. Roof/nail tearoff and shingle renailing shouldn't be a problem I guess....
Alot of closed cell foam installers are recommending only 2 inches of it (saves money I'm sure).
Thanks,
David
0
Comments
-
Conservation versus Efficiency?
--------------------------------------------------------------------------------
Lets say you have 2 options but you only have limited funds, and you are building a house or doing a significant reno.
1) Have a super high efficiency geothermal heating system installed your house with radiant floors and an air handler for cooling in the summer off of your geothermal heat pump, with say a boiler back up with indirect fired HWT, etc. With conventional 2 x4 or 2 x 6 outside walls with average batt insulation, poly vapour barrier, etc.
2) Insulate the living PISS out of your house. 2x8 or 2x10 outside walls, with the latest, high quality technology in insulation, say spray in foam with reflectix insulation as a vapour barrier if needed, etc. etc. With say just a condensing boiler with an indirect HWT and radiant floors and a radiant barrier in the attic with an attic fan for hot days, a high efficiency HRV for air exchange, etc.
Which is better? Efficiency, or conservation? Sure the premise behind them is similar but....There was an error rendering this rich post.
0 -
Option 2
Option 2..its a no brainer.Equipment will come and go but the envelope is there to stay.
Look at the numbers of how the heat loss and gain drops with a great envelope.
Also make for a smaller boiler,ac and emitter.
0 -
Vote: Conservation and Alternative Energy Production
My vote is always to require the least heat possible. I cannot imagine 2x8 or 2x10 walls being necessary to do this. The key is the thermal break. Sheathe the house with plyisocyanurate foam if stick frame or use SIP's and ICF's on a new home.
My vote: Super insulate, install a high efficiency boiler and as much solar as you can afford, and of course a very tight home will require an HRV.0 -
May i add
May I add that iqd force air heatpump system and a very tight home could complete with a wet system or geo system.
0 -
Agree
also with southern exposure aligned with mag deviance and chases installed for future solar and upgrades.Also some passive solar figured in the design.0 -
HRV or
2 kids and a couple dogs lol0 -
foam/concrete
walls. R54 value. infloor does not work that well with this type of construction, in my area, as I found out. Even with reset. I'm thinking panel rads for my own, if I ever get the chance! LOL!
Leo G0 -
option 2
IMO, going from say, 82% efficiency to 95% efficiency still leaves the elephant in the room unnoticed. You're still using a LOT of energy! I tell my steam clients this: We can get your steam system to work very economically, but the fact is that 100% of your fuel's heat goes outdoors. We just want to make sure that as much as possible stays indoors for as long as is practical. Yes, we want to restore the efficiency of the heating system and improve it with better controls, but "insulate, insulate, insulate" if you really want to conserve energy.
BTW, a friend of a friend chose both options 1 AND 2. So the expensive heating/cooling equipment is rarely used. You could install an old gravity coal furnace converted to millivolt gas at 40% efficiency in such a structure and your fuel use would still be next to nothing! The pilot light on those furnaces would probably overheat the house in mild temps.
So, yes. Option 2.
-TerryTerry T
steam; proportioned minitube; trapless; jet pump return; vac vent. New Yorker CGS30C
0 -
#2 only if
you end up with healthy IAQ. Building a structure that could be heated by just internal gains, lights, appliances, human beings, etc.
Cooling, humidity and fresh air would need to be factored in. Building with cooling shafts or towers to use convective currents to move heat out.
Control-able passive solar makes a lot of sense, doesn't get any cheaper or easier than sunshine through the windows. Windows with internal motorized blinds to shut the sun off when needed.
Cooling via thermal solar panels, a few hybrid panels (thermal/ PV) to power fans and filtration, etc.
Certainly low mass, quick responding radiant, or panel radiators for heat and maybe somme of the cooling load.
Get some back issues of Solar Today mag, some very unique alternate energy homes in there.
Build small.
hrBob "hot rod" Rohr
trainer for Caleffi NA
Living the hydronic dream0 -
I agree
option 2 is the way to go. I've personally experienced this as I've tightened up my own house. Its calculated heat loss is now 68% of what it was when the house was built in 1924, and there's still much to be done in this area.
Already, I'm to the point where if I have to replace the boiler today, I can use one 25% smaller than the present unit. Once the walls are insulated, I can probably get down to 50% or 60%. This means The Lovely Naoko can stay warm on much less fuel ;-)
To Learn More About This Professional, Click Here to Visit Their Ad in "Find A Professional"0 -
Don't forget windows
Well insulated building shell is the way to go.
Windows are the weak-link - greatest heat loss in any conventional building shell. Run a heat loss calc on building elements - walls, windows, ceiling and basement. No point in over-insulating walls and then putting in R = 2 windows.
Buy the best windows you can find.
Doug0 -
Option 2, no doubt. IAQ high on the list with this option
HRV distributed well will do well. Sounds pretty cool.0 -
So then?
I work for a company that installs a lot of geothermal heat pumps w/boiler backups and some air to waters, as well as the odd split pump. Why then, is there such an emphasis on having the high efficiency heat pump, and yet I see the general contractor/builder skimp out on slab insulation with nice dense ground on the other side of the slab sucking heat out of the radiant floors, or typical bare bones batt insuation or?
There was an error rendering this rich post.
0 -
I'm sure you already know the answer. People can't see the insulation or the barrier.0 -
... and ...
customers/clients cannot show off fancy insulation the way they can show off a countertop, a car, or perhaps even a boiler. Insulation is hidden.
Many architects hate the effects it has on building appearance that proper "green" building dictates (i.e. window overhangs, inset windows, site orientation, etc.). So you end up battling the aesthetic component, a battle that, until energy prices rise and more truly "green" architects manage to get commissions, is unlikely a battle you will prevail in. Architects can be worse than the trades in saddling the owner with high operational costs - however, it is the clients fault for engaging them! - preferring vision over efficiency.
As bad as the battle is in new construction, it's even worse for renovations because historic commissions may not like the look of a home with fatter walls, no matter how much you do to hide it. Thus, you'd have to shrink the interior space, which is never popular. Corbond is my friend, though thermal shortcuts are likely all over the place. Then, there is the issue of windows, historic glass, etc. I picked my battles and I live with the R2 glass I have, knowing that there are better options that would destroy the look of the home.
There you have it, from a homeowner perspective.0 -
open cell vs closed cell
Hi Constantin,
you have mentioned how well Corbond (closed cell) worked for your attic. There are those that claim that closed cell traps moisture where it shouldn't and that the open cell icynene foam allows 'breathing'. Not sure breathing is good if you want to seal the space, but are there situations where one is superior to the other? I'm talking an unvented attic here with foam in the under-roof joists and gable walls.
Thanks,
David0 -
A good place to look...
... is Passive House Institute US. (www.passivehouse.us) Efficiency is basically what they do by making very snug homes with little thermal bridging or air leakage. Heat recovery ventilation is standard, central heating systems are not. It is only one way of getting there, but it is well thought out.
I can say Synergistic Building Technologies (www.synergisticbt.com) has just produced their first prototypes of insulated exterior automatic shutters, so window heat loss/gain can be substantially reduced.
Yours, Larry0 -
Worked well everywhere...
I think the major shortcoming of the stuff is that many builders/installers don't like it because it's more difficult to work with than icynene and similar materials. Whereas Icynene, et. al. have the consistency of shaving cream, Corbond is tough stuff. Overspray is harder to remove and greater care has to be taken applying it or windows will get bowed, etc. Plus, open cavities are almost a must (unless you are really good at it).
I have noticed no issues in the walls or the rest of the house where we applied it re: breathing / wetting / etc. That is probably most likely the result of having traditional window frames, sashes, etc. still in place, i.e. lots and lots of ex/infiltration via them vs. the walls. My recollection from building science is that unless the water gets in AND the wall has the dewpoint inside it, that the issue is not likely to be a problem.
Corbond is so impermeable that a vapor barrier is not likely to be required. It also stiffens walls significantly. Given the option, I'd happily go for Corbond again and as you may recall, we have a unvented roof/ attic. IMO, the only way to go, especially if you have any kind of HVAC up there (as we do).0 -
renovation
I'm actually a historic conservationist. Rather than preservation, which can imply a museum-like restoration, most good buildings of the past require conservation, in my mind. Wanton destruction of buildings and their irreproducible materials quality is the most anti-"green" thing we can do.
So back to that insulation thing. Most old homes leave plenty of room for good insulation to be applied without any visible effect. The fact that the wall cavities are wide open simplifies things. The question is what the most effective insulation is for a particular application and most likely to be applied correctly so that the results are real. I'm no expert on this, but one product that really looks good is AirKrete. I also wonder about the cost-benefit of the radiant barrier products out there.
Regarding old windows, I think emissivity and air leakage are the easiest things to improve upon. Frankly, a wood window with a low e storm panel is a decent thing. In my case, I'm never going to give up my 30's vintage Truscon steel casement windows with the rolled glass and brass hardware. These are impossible to replicate architecturally since the sight lines extend to within 5/8" of the fenestration opening and replacement always destroys that large open glass area. Once they're gone, future and more sensitive historic re-replacement is impossible.
But I didn't say that I could live with them the way they were! In disrepair, they could leave the house with an "outdoorsey" feeling --inside.
So with these windows, after retrofit gasketing to stop infiltration, I made frameless coated acrylic storm windows that attach magnetically directly to the steel sections. Who needs frames when you've already got the strongest window frames in the world? Only the locking and operating hardware remains as a thermal bridge. There's no need to remove them seasonally for ventilation, so their benefits remain throughout the AC season as well. Exceptionally important to me is that the visual transmittance of the end result is unparalleled by new windows.
As it would turn out, acrylic sheets have very good low e properties in the portion of the IR wavelengths we are concerned about in a normal window application. Technically, the IR bandwidth is quite wide and acrylic has poor e blocking at many wavelengths. So if you're doing smelting in your living room, the molten materials IR will pass through the acrylic. But normal room temps, radiators, light bulbs and body temperatures are blocked extremely well, especially when the angle of incidence is anything off perpendicular to the glazing surface.
Anyway, the gaskets and the thermally broken/ directly attached frameless storms have provided a difference in indoor comfort that is nothing less than radical. With that, I'm satisfied.
The big problem now is what to do about the walls that already have fiberglass in them but that has gaps that make the R-13 rather fictional as the IR camera confirmed. Seriously, this is a big problem since the exterior is a nice tapestry brick and the interior is very hard plaster with a china-smooth surface. Over my dead body is that going to get replaced with drywall! So I guess I still have a problem. Any suggestions?
-TerryTerry T
steam; proportioned minitube; trapless; jet pump return; vac vent. New Yorker CGS30C
0 -
Terry,
I looked at a house that matches this description almost exactly,with a cracked CI boiler and high oil bills. I advised the owners to consider a condensing boiler, trv's on existing CI radiators,reset mixing,buffer tank,... and new windows.
They were appreciative of the information and even seemed to be convinced of the worthiness of these investments, but ended up having there oil company just swap out a new boiler. Unfortunately people have alot of other things they would rather do with their money.
BTW- I think I offended them a bit with the window replacement suggestion, the steel windows were a non-negotiable. Could you send some pictures of the magnet storms?
Agree with you about the value of reuse, The problem of converting our infrastructure from an economy of energy abundance to one of scarcity is at the core of our current dilemma. The non-negotiability of your plaster and steel windows is what is referred to as the psychology of previous investment. It is very hard for people to abandon something they are invested in, as unsustainable as that investment may be.0 -
You could be my hero...
... if you could point me in the direction of someone that makes acrylic sheets to order with the southwall coating baked into them. They'd be ideal for my home on the south side in the summer... I'd remove them for winter. I have yet to find someone that makes this sort of stuff. They could be hung from the outside or, ideally, simply slid into place for the summer between the storm and the historic glass.
The Autoshutters mentioned by Larry are tasty as well. Trouble is, historic shutters interfere with storm windows. Would have to find new hinges... The to-do list gets longer!0 -
Hi Constantin & Scott!
I'll take some pictures of the acrylic storm windows when I get back in town. They're so simple that I don't know what took me so long to think of it. You'll find a common modular proportioning system to the windows. Essentially we're dealing with a general 18" module in width, and about 12 1/2" in height. The point is, when you measure for a sheet that will fully cover the transom lite, for example, each one might be 12 1/2 inches tall by either 18" for an average narrow window, or 36" for an average bedroom size, or 48" to the next width up. ANyway, you find a pattern that will be the same for every window. Since we are using the window frame itself for support, we can size the sheets to the window itself, making them fully interchangeable. Size them so they full cover as much steel as possible. A little exposed steel at the hardware points isn't as big a deal as you might think. Even IGUs have a metal frame that bridges thermally to some extent. Don't worry about a few square inches of exposed steel. You'll find that multiple sheets in a handful of sizes will do every window you have. And there's no trying to fit a sheet or two in the return opening -a process aggravating beyond description since the plaster or wood is so variable. So that idea went out the window. [heh. I kill me!]
edit: Take the measurements to a good plastics house. They'll cut them in bulk for you. The local hardware store will be very expensive and may not have access to the scratch-free coated acrylics either. I use standard acrylic higher up on the windows and only use the scratch-free where it is likely to be damaged by a jumping dog, a cat trying to attack a tormenting feline sitting on the outside window sill (ask me how I know), or by simply sliding large flower vases, etc that find their way onto those large window sills.
I don't use adhesive magnetic strips since they are so unsightly. Frankly, I use very little sealing at all since the window openers are gasketed with a caulk-and-plastic trick. The fixed portions don't leak air at all anyway. You'll see in the pictures that you really can't see the storms unless you're looking for them. There is no frame and its all clear so you don't lose your window sill either. All you can see is a handful of small 1/8" thick disk magnets. If you choose full coverage over the operation portion (i.e. the dimensions of the screen) you will have to remove that section in summer. The remainder should all stay in place all year long.
Since we will never have a hermetic seal on a storm window system, we shouldn't attempt one lest the moisture get between the storm and the steel window and take forever to escape. Unless you grossly over humidify in the winter, these storms stop the condensation problem. Each magnet is a dual arrangement, one stuck to the window frame the other clamping the acrylic sheet to the frame magnet. This way we have good holding strength and provide a 1/8" thermal break at the mullions and muntins. This gap also accommodates the Fenestra/Crittal muntin design where one muntin "flows over" the other where they cross.
Where the sheets butt together, there is no seal at all. I don't have a seal where the acrylic butts against the wood edge molding either since I couldn't tell a difference when I tried one. Where we need a seal, a slim 1/8" thick acrylic strip is bonded to the sheet so that it fills the 1/8" gap.
When completed, you've now got a tight window that doesn't leak air, has excellent low-e properties, and a decent U value, is strong, elegant, VERY clear and bright, and quiet.
-Terry
P.S. We can also make them virtually maintenance free for 20 years at a time. Next time, we have to have a talk about paint. Modern paints destroy windows. Period. We have to move to something thats quite exotic today, but will last a very long time (like 20 years without maintenance), doesn't build up and protects the window from any kind of rot or deterioration.
Its also the absolute best paint and preservative I have ever used in the boiler room.
And no. I don't represent the company. I merely have found their product indispensable.Terry T
steam; proportioned minitube; trapless; jet pump return; vac vent. New Yorker CGS30C
0 -
Awesome!
I look forward to seeing those pictures and thanks for the description!0 -
Red Herring, IMO
A leak is a leak is a leak. Considering what a sieve this place was before we started working on it, I'm not convinced that the lack of foam here before we started work helped any. Some holes were big enough to stick a fist through, lots of bird nests, etc. Bottom line, you have to inspect the roof from time to time. If something doesn't look right, replace it.
Who knows how long the fake slate we have on the outside now will last? I don't... but we did use Grace Ice and Water Shield below and copper nails to put it all in. Hopefully, that means a long time. The nice thing about the plastic slate is that you can walk on it if it's dry. Try that on real slate (crack!)
If water leaks are a real concern, another way to check for them is to use a IR camera. Allegedly, wet areas do show up if the camera is sensitive enough.0
This discussion has been closed.
Categories
- All Categories
- 86.7K THE MAIN WALL
- 3.1K A-C, Heat Pumps & Refrigeration
- 56 Biomass
- 423 Carbon Monoxide Awareness
- 105 Chimneys & Flues
- 2K Domestic Hot Water
- 5.6K Gas Heating
- 103 Geothermal
- 160 Indoor-Air Quality
- 3.6K Oil Heating
- 69 Pipe Deterioration
- 950 Plumbing
- 6.2K Radiant Heating
- 385 Solar
- 15.3K Strictly Steam
- 3.4K Thermostats and Controls
- 54 Water Quality
- 43 Industry Classes
- 47 Job Opportunities
- 18 Recall Announcements