Welcome! Here are the website rules, as well as some tips for using this forum.
Need to contact us? Visit https://heatinghelp.com/contact-us/.
Click here to Find a Contractor in your area.
Steamer Stumper solved!
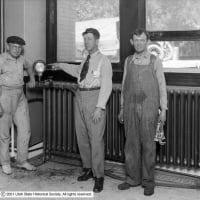
Timco
Member Posts: 3,040
Pulled old gas train, went with one RS 700 series GV, which gave them a t-couple...imagine that, a safety devise on this boiler! Old rate was about 140K, now at 186K, and I get 2lbs in about 40 min from cold, 15 min between cycles. BINGO! I do have 2 questions...1) there is a odd component on the old burner housing that the 24V loops through with long contacts. That shut me off twice (while cold) before a minor tightening kept it on. What is this? My guess is a roll-out sensor, but I can assure you there is no rollout and excellent draft. Second, exactly where is the orifice(s) on a burner like this? Train leads to a box that takes gas to the pri air shitters (2) and off to the burner ring. Burner is a ring with ports all around. GV is near maxed to get me to 186K and I want to check orifice. Birner is sealed pretty well and I want to know where I am going before tearing into it. Thanks to all those who chimed in! CO is barely at 25ppm. Waterline very steady. Lowered the water line from 3/4 to just about 1/3 and it made a huge difference.
Tim
Tim
Just a guy running some pipes.
0
Comments
-
First things first
the 700 series gas valve is a single seated valve and should not be used. When retrofitting it is code to use a dual seated redundant valve such as the 720 series Robertshaw.
The gas train photo DSC01025.JPG left to right is the gas regulator, then a pilot solenoid valve and finally a Honeywell motorized either V-155 (Series 10) or a V855 (Series 80).
That boiler needs major refurbishing from the looks of it what did you get for combustion readings?
The orifice on those is up inside after the primary air opening, when you had it apart you could have pulled it out to see what size.
Old systems never had rollout protection that did not come about until the 1970's.
Boy you sure have some old stuff out your way I thought we only had that stuff here in New England.0 -
My local RS rep / supplier sold me the 700 series. I will take combustion readings either this evening or tomorrow, I had to run for a family emergency which was a HUGE scare but turned out fine. Would you elaborate on the difference between the 700 & 720? Why code? Did not need the reg, as service to boiler room is 4oz, and the older hywell valve was just jammed open. I checked CO and had to run. Clocked meter on my way to the truck...Old pilot solenoid was chattering and buzzing. Pilot was direct from gas main.
TimJust a guy running some pipes.0 -
Ex air 72.7, Stack 473*, O2 9.4%, CO2 6.5%, CO 6ppm, COAF 11ppm, draft -.02wc...
I made some small adjustments to the pri shutters and got the CO down from 25ppm to 6ppm. Burning very well. Is the requirement for the 720 over the 700 series a NFGC requirement or a local / state code? Never heard that one, but our state certification class was a joke compared to the training NE'rs are required to take...I also have noted that it passed inspection recently with only one pressuretrol...
TimJust a guy running some pipes.0 -
Tim
My local RS rep / supplier sold me the 700 series.
HE SHOULD KNOW BETTER.
I will take combustion readings either this evening or tomorrow, I had to run for a family emergency which was a HUGE scare but turned out fine.
Would you elaborate on the difference between the 700 & 720? Why code? THE ANSI STANDARD FOR GAS VALVES IN 1988 WAS CHANGED TO REQUIRE GAS VALVES TO BE DUAL SEATED INSTEAD OF SINGLE SEATED FOR SAFETY PURPOSES. IT IS REQUIRED WHEN UPGRADING TO INSTALL THE DUAL SEATED VALVES WHICH IS ROBERTSHAWS 720 SERIES. THE VALVE BY THE WAY HAS A REGULATOR BUILT IN CALLED A SERVO REGULATOR.
Did not need the reg, as service to boiler room is 4oz,
4 OUNCES ??? WHAT IS THE PRESSURE IN INCHES WATER COLUMN? YOU SHOULD HAVE AT LEAST 6 TO 7 INCHES PRESSURE TO THE VALVE AND THE OUTLET PRESSURE BE 3.5" W.C. THE VALVE CAN'T TAKE MORE THAN 1/2 A LB OF PRESSURE ROUGHLY 14" W.C.
and the older hywell valve was just jammed open. I checked CO and had to run. Clocked meter on my way to the truck...Old pilot solenoid was chattering and buzzing. Pilot was direct from gas main.
0 -
Tim some more
Ex air 72.7, Stack 473*, O2 9.4%, CO2 6.5%, CO 6ppm, COAF 11ppm, draft -.02wc... YOUR EXCESS AIR IS TOO HIGH WHICH TELLS ME YOU HAVE AIR LEAKS COMING IN AROUND THE OUTSIDE OF THE BOILER.
I made some small adjustments to the pri shutters and got the CO down from 25ppm to 6ppm.IF ADJUSTING THOSE CHANGE CO THEN THEY ARE SECONDARY AIR DOORS NOT PRIMARY AIR. Burning very well.
Is the requirement for the 720 over the 700 series a NFGC requirement or a local / state code? I EXPLAINED THAT IN THE OTHER POSTING NFGC HAS NOTHING TO DO WITH GAS VALVES IT IS ESTABLISHED BY THE AMERICAN NATIONAL STANDARDS WHICH IS NATIONWIDE.
Never heard that one, but our state certification class was a joke compared to the training NE'rs are required to take...I also have noted that it passed inspection recently with only one pressuretrol...
0 -
I will be making some calls Monday about the single seat valve. As I mentioned, never heard that one, and I doubt anyone else in this state has either. As for incomming pressure, I did not check it. I follow the guidelines set forth in the classes I have taken and it was never suggested to check incoming gas pressure. When I say 4oz, I mean it is a low pressure service to the boiler room, not 2lb. The meter and the unregulated water heater in the same room on the same line verified that. Gas company just gave the meter a clean bill of health, the report was read to me when I called. If I am missing a crutial step, please let me know. As I said, we do not have the training requirements (or classes available) that you offer in NE. Must be nice, if it were offered, I would be there.
As for the ex air, with numbers otherwise very good, it seems to be really picky to get the excess air down, but I can seal up the old draft shutter opening and that will reduce air infiltration. Otherwise, no openings besides maybe around floor, which can be sealed. As for the pri/sec air, my bad. The book from my class has it listed as "That portion of the combustion air introduced with the fuel in a burner". I adjusted the shutters (large discs at the beginning of the run to the burner where the gas mixes with the air) and opened them fully to get the lower CO reading.
Again, I strive to offer services and make repairs where no one else even knows where to begin, and offer results. I do now know about the need for the dual seat valve, and stand by my combustion numbers. If gas pressure should always be taken on the incoming side, it will be done from now on but I do follow the guidelines taught by the Rocky Mountain Gas Association for gas fired equipment certification.
TimJust a guy running some pipes.0 -
coal conversion
Last time i worked on one of those conversion babies was 1972. did you pull out the torque swich & replace w/ basso . don't forget to oil the motorized valve. what memories. not all good0 -
Odd Component?
Might that mystery set of contacts be the old thermostatic pilot safety? I have seen one like that on a 1950's gas boiler with a White-Rogers diaphragm valve. The thermostatic switch was wired in series with the valve coil as you describe.0 -
These contacts are outside of the burner. It does appear that something leads into the boiler, but the tiny lower access door does not offer a view of the pilot. It would make sense as this devise killed the voltage to the gas valve...and did it while it was cold and just fired...
TimJust a guy running some pipes.0
This discussion has been closed.
Categories
- All Categories
- 86.8K THE MAIN WALL
- 3.1K A-C, Heat Pumps & Refrigeration
- 56 Biomass
- 423 Carbon Monoxide Awareness
- 106 Chimneys & Flues
- 2K Domestic Hot Water
- 5.6K Gas Heating
- 104 Geothermal
- 160 Indoor-Air Quality
- 3.6K Oil Heating
- 69 Pipe Deterioration
- 952 Plumbing
- 6.3K Radiant Heating
- 385 Solar
- 15.3K Strictly Steam
- 3.4K Thermostats and Controls
- 54 Water Quality
- 43 Industry Classes
- 47 Job Opportunities
- 18 Recall Announcements