Welcome! Here are the website rules, as well as some tips for using this forum.
Need to contact us? Visit https://heatinghelp.com/contact-us/.
Click here to Find a Contractor in your area.
Pump Motors - question on saving energy
Options
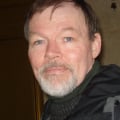
Brad White
Member Posts: 2,399
take a look at what the current actual load/duty is.
A VFD as a substitute for a properly selected motor is not a very good deal. Start with the right size motor (not just a nameplate replacement) then go for a VFD provided you have a control strategy to govern it.
My $0.02
Brad
A VFD as a substitute for a properly selected motor is not a very good deal. Start with the right size motor (not just a nameplate replacement) then go for a VFD provided you have a control strategy to govern it.
My $0.02
Brad
"If you do not know the answer, say, "I do not know the answer", and you will be correct!"
-Ernie White, my Dad
-Ernie White, my Dad
0
Comments
-
pump motors - question on saving energy
I have a 50hp motors that I am evaluating the feasibility of replacing, but am unsure of some of the terminology to figure this out.
I searched on the web and found that the conversion from hp to kw is 1hp = 1.341 kw. So that means that my 50 hp motor consumes 67 kw, right?
I understand that if I add on a VFD, the motor will be able to slow down as needed and therefore not run at its maximal capacity and therefore I will save some energy.
However, I don't understand what a high efficiency motor is. Is this a motor that is able to have similar work output but requires less hp?
what formulas can i use to calculate my energy savings to see if this project is worthwhile.0 -
High eff motors
See attached doc which has a good description of hi e motors and their makeup and difference to standard. Tim0 -
High-E Motors
Tim posted a good resource, thanks.
I can add that a net or brake horsepower is equal to 0.746 kW, the inverse of this is, as you say, 1.341 which expresses "HP per kW", not the other way around. Thus, a 50 HP load would consume 37.3 kW net. My electrical engineers then incorporate a power factor and efficiency numbers. In the end, for rough discussion purposes, they use "one kW per HP" when scoping out a system. Not meant to be accurate so much as convenient. Suffice it to say, the actual demand lies somewhere in-between.
Your state or local energy code or local utility may dictate what efficiency motor you use. EPACT is one standard that is fairly universal, and specifies industry-acceptable (meaning
"practical and available") efficiencies in all motor namplate horsepower categories.
You have an opportunity here though! Maybe the 50 HP motor was based on a thumbnail guess of what was needed. Might be that the pump or fan, whatever you are driving, has since had capacity removed (or even added!).
What I would do is map out motor demand over time, coupled to a certified balancing report. Find out how much air or water you are moving against what pressure and plot that on the pump or fan curve. Just suppose that you could reduce that motor to 40 HP or even 30?
The bigger question is, will the system benefit at all operationally by installing a VFD?
If you have constant volume systems without variable terminal devices, is there a point, an operational strategy which will respond effectively to the change in variables? At the very least you would have to add variable terminal devices (2-way control valves or VAV boxes) plus the requisite pressure transducers.
You also have to take into account the hours of operation at reduced load to get an idea of payback.
Too often I have seen hydronic systems retrofitted with drives and have seen no savings at all. The reason was that the coils all had 3-way valves and when in bypass mode, not only did the energy use not go down, it actually went up because in bypass mode there was less restriction (no coil seen by the water, easy path around the unit).
The solution was to change out the control valves with 2-way valves so that when they closed, they affected system differential pressure which was picked up by a transducer to control the VFD. No point in adding a VFD unless the system would benefit. It becomes an expensive manual speed control otherwise. Great for balancing though, especially if going in new ILO a starter.
As for savings, Brake Horsepower (BHP) varies by the cube of the load (flow rate) in a given system.
Say you have a 50 HP pump drawing 43 BHP while moving 1275 GPM of water at 100 feet of head at 75% pump efficiency. At a low load period of say 850 GPM (with reduced head of course, by a 1.75 exponent) at about 49 feet of head.
Your BHP would drop from 43 to about 13 BHP.
One can only imagine what this does to the demand charge let alone the electric bill, if it occurs outside or or at least lessens your demand peak."If you do not know the answer, say, "I do not know the answer", and you will be correct!"
-Ernie White, my Dad0 -
HP to KW
1.341 Horsepower = 1 kW not the reverse (easy error to make), so, inverting 1.341 you get: 1 HP = 0.746 kW
Your 50 HP motor can produce 50HP of output (perhaps even a little more), and 50HP*0.746kW/HP = 37.3 kW of output. Since it's not 100% efficient it will require more electric power *input* than that though. A high efficency motor that size might be say 94% efficient and use just under 40 kW, whereas a 90% efficient motor (for example) would need almost 41.5 kW to give the same 37.3 kW (50HP) of output.
What's the load, does it vary a lot, and can it be run at slower speeds?0 -
thanks for the answers
thanks for catching the fact that it is 37kw and not the 60-something i had. plus the fact that this is the output and I have to take into account the motor efficiency.
The motor might be able to be slowed down in which case i think i will look at a VFD and see if that works out.
I found a formula in a book that gives the kwh saved by upgrading to a more efficient motor. For those that may be interested, i found it in "Simple Solutions to Energy Calculations" by Vaillencourt and it is:
kw saved = 0.746 * hp * [ (1/motor eff1)-(1/motor eff2) ]0 -
naughty naughty
"The bigger question is, will the system benefit at all operationally by installing a VFD?" Brad shame on you.
Great for cooling. Not so great on heating.
Alot of people look toward this route as a cure for piss poor piping skills. Ooops that slipped. Then if air elimination becomes a problem we then spec. a big high tech. air elimination device for the problem we just caused. This happens daily.
Just look at at the pictures that get put on this site, they look impressive but 50% or more violate all piping flow and velocity principles.
Then we talk about super pumps. It only takes circulation to move water in a heating system.... Pumps are for well, or people that don't understand the basic principles of moving water in a hydronic system.
I am sure the salesmen of this site will correct me.
0 -
Huh?
Hi RW- Not sure what you mean unless you did not understand my response.
Heating or cooling can and do both benefit from VFD's there is no question.
My concern was if the VFD was installed, then what? What would control it? It would respond to what variable?
Piping skills, air separation, etc. are not related issues nor am I suggesting that a VFD or larger circulator would change that. It seems a bit of a non-sequitur to me.
Also, unless I am missing something, what violations of piping flow and velocity principles? Not all are perfect but the systems work. Just not sure what you mean."If you do not know the answer, say, "I do not know the answer", and you will be correct!"
-Ernie White, my Dad0 -
:-)
I was just picking on the phrase of possibly no benefit to the system because some salesmen type would insist that you need a VFD on ever job regardless of the control strategy or lack there of.
As far as piping skills, air separation, VFD's and etc. THEY ARE ALL IN DIRECT RELATION TO EACH OTHER IN EVERY SYSTEM.
Just think of that 1" branch that the VFD for days on end only lets see 2 to 3 gpm. Or that 3" main when its gets a little warm out that is slowed to 20 to 30 gpm because that is all the heat the system needs? What's happening now?
Alot of things happen in a properly designed heating system when you adjust the flow away from the designed flow of the piping system. VFD's do this all the time. How many people set minimums on their flow rates for the VFD's? Few. Most don't even give it a second thought.
Then there is also the whole thing of bringing the entrained air out of the heating solution because of the new PD on the system. That's another story.
VFD's can be and are detrimental to good air elimination in many cases and I did not say all. VFD's are better suited and reap the most benefits from mainline circulation of fixed delta T systems like chillers.0 -
Ah, I see said the blind man
as he spit into the wind. "It all comes back to me now"....
Glad you cleared that up!
I do see your piping point although I would maintain that when retrofitting an existing system, such conditions are a "given" and would not ordinarily be corrected.
Yes the dynamics do change but I do not see that as a bad thing necessarily.
The notion of needing velocity to entrain air has my partial support. I say "partial" because air in water will rise to high points (which should have vents) as well as at radiators. If you are dealing with copper tube and small sizes, purging becomes the mode if vents are not provided.
Gravity HW systems are a case in point. Very low velocities yet the air gets out with occasional difficulty. The idea of scooting it along using larger flow rates than necessary especially when most air would be taken out at or near the boiler is foreign to my thinking.
My $0.02 anyway!
Brad"If you do not know the answer, say, "I do not know the answer", and you will be correct!"
-Ernie White, my Dad0 -
Low Velocities
How many piping jobs have all the piping pitched to the boiler room? None of the piping pictures on this site. So just slow down the water in that piping system and you are guaranteed to have air in the tops of those pipes. Get enough air and now you have a VFD. Very Familiar Demise. Purging is for pumps. But what do I know.0 -
wow
so rw,
what you are saying is that by a picture alone, you can tell what the velocites are? and they are all too slow to move air around?
how do you determine head loss of a system by the near boiler piping pictures, this I'd like to learn.
i'm amazed.0 -
Easy
When you see big pump feeding a piece of copper pipe than needs x gpm to be near a proper velocity for air elimination and other concerns, then it feeds a single or double loop of pex tubing that will only handle half of that it's not to difficult to see. See.0 -
the correct phrase is...
"i see, said the blind man, as he picked up his hammer and saw"
anyway i dont know why, you even let rw get your goat - all the air separators (from a Spirovent to a secondary one like the Caleffi hydro-separator) work better at 4ft per second or less, not faster, and once purged its "pressure" that keeps the air out - exactly how would he pump,pipe,pitch the attic's radiant loops to keep the air out
and modern day VFD's are so good, that they always, and i mean ALWAYS help, do this test, (i have) - take any dumb system with a lousy motor and all, put a power draw meter on it or even just an amprobe, and do an a/b test with and without the vfd - and you will all quickly sing a different tune
copper is getting expensive and the power companies cant just run bigger lines soon, they will subsidize vfd's, just like they subsidize compact florescent bulbs just the fact, that a vfd can sense the load and adjust without any programming at all, is alone a huge saving!!! so I just aint gona sit by whilst he bad mouths the friendly neighborhood vfd salesperson if the little fan in your laptop didnt have a vfd, your battery would be dead in 20min even if it is a permanent magnet motor!!!
0 -
Keep this in mind too
If you choose to use a VFD on your motors, see if there is an auto-reset feature of some kind. If you have a power failure,or glitch, these devices can trip very easily, and (at least the ones on my cooling tower fans)need to be reset manually. This is the main reason I will not use VFD's on my condenser pumps, for if I lose them, I lose flow thru the whole building, and the self-contained units trip on no flow.0 -
Pressure
Here is one for you Kal. If "pressure keeps the air out" why all the hype about oxygen barrier tubing? That kinda blows that theory. No goat intended.
"-exactly how would he pump,pipe,pitch the attic's radiant loops to keep the air out" Answer simple ensure that I had the correct velocities in my piping system.
If people would stop listening to the spin doctors about the newest gadget invented for a problem that we ourselves created and then focused that energy on basic design principles wow that would be something.
Of course the alternative would mean this website would see a lot less postings in general and that would not create business revenues and so on.
I am guessing this posting will get modified or pulled.
0 -
almost all the new ones do....
and many now turn off or modulate the cooling fan as needed, as well as have an alarm when the fan is failing, an ETON one i just wired up, even goes as far as to alarm -but nevertheless run the motor at reduced output if the cooling fan fails - this could be good for your application,
i only wish there was a minimum set of standard features that they all had to provide - as well as standard pinouts, wish NEMA would get on the case0 -
whatever are you on, i want some...
reg pex tubing is gas permeable and allows the oxidation process across it to continue - pressure notwithstanding, the -al- layer stops that - you could have a vacuum in the tube and 1000psi outside and the o2 molecules would not get across
and again what has velocity got to do with air, except for making it worse with the venturi effect? - air separators are put near the outlet side of a boiler where the temp is the highest and the flow rate not to high so that the coalescing material in the air separator can attach to the entrained air and grab it out of the water you need look at http://www.spirotherm.com/docs/brochures/HV_Air-1A.pdf this one they make just to handle higher velocities
we design piping for delta-ps and delta-ts, we leave the air for the ac guys
dont know of any hydronic science other than keeping velocities down, pressure up, and pumping away from the point of zero pressure change that helps for air if you have a link that explains what you are on about I am all clicks
0 -
Never I shall play the fool, O2 be a molecule...
That is entirely correct, Kal. Gaseous diffusion is the motive force...
No goat was taken, I just did not understand the question and did not see it in jest. I took it as a "huh?" kind of question, not a challenge, but thanks. You are mensch.
Now, sheep on the other hand, well that gets personal....."If you do not know the answer, say, "I do not know the answer", and you will be correct!"
-Ernie White, my Dad0 -
This is killing my spreadsheet.
anyway i dont know why, you even let rw get your goat - all the air separators (from a Spirovent to a secondary one like the Caleffi hydro-separator) work better at 4ft per second or less, not faster, and once purged its "pressure" that keeps the air out - exactly how would he pump,pipe,pitch the attic's radiant loops to keep the air out
reg pex tubing is gas permeable and allows the oxidation process across it to continue - pressure notwithstanding, the -al- layer stops that - you could have a vacuum in the tube and 1000psi outside and the o2 molecules would not get across
These two paragraphs contradict each other. The first paragraph's pressure keeps the air out, and the second one says its the tubing that does.
If I am not mistaken all objects are oxygen permeable.
There is another point here but we will let that hide in the pipeline until it comes out of solution. Pun intended.0 -
permeablilty
you could be right I do not remember all my chemistry.
but who cares if Al allow 1 ppm per day to enter the system, when non barrier, lets say, allows 1,000 ppm a day?
see!
ps I do not see the contradiction either. they work together.
to be more correct partial pressures keep things at bay.
0 -
My point exactly
"we design piping for delta-ps and delta-ts, we leave the air for the ac guys"Read your own statement. Because that is the issue and it always has been...
You design your piping system for delta p&t regardless to flow. Spot a trend here.
Talk about driving a tack with a sledgehammer.0 -
I was
taught to always try and keep minimum velocity above 2FT/sec to keep air entrained. B&G even recommends reducing pipe size to increase velocity when flow is verticle-down. It seems like the micro-processor and the petrochemical industries have eliminated the need for engineering and piping skills. Jest git yerself a modcon a VFD pump and sling a roll a PEX on yer shoulder an go fer it. It'll all self adjust. bob0 -
RW
you got me a bit confused here.
how do YOU design a system if you do not design for delta T & P?????????
FLOW is delta T and P, or am I missing something?
how do you heat a structure if you don't design to delta T?0 -
mangna and stratos,,,
hey, you could play dumb and put in a grundfos mangna or a wilo statos and let the pump figure it out - they are only 700-1000 dollars, chump change - just kidding0
This discussion has been closed.
Categories
- All Categories
- 87K THE MAIN WALL
- 3.2K A-C, Heat Pumps & Refrigeration
- 57 Biomass
- 425 Carbon Monoxide Awareness
- 116 Chimneys & Flues
- 2.1K Domestic Hot Water
- 5.7K Gas Heating
- 109 Geothermal
- 160 Indoor-Air Quality
- 3.6K Oil Heating
- 70 Pipe Deterioration
- 987 Plumbing
- 6.3K Radiant Heating
- 389 Solar
- 15.4K Strictly Steam
- 3.4K Thermostats and Controls
- 54 Water Quality
- 44 Industry Classes
- 48 Job Opportunities
- 18 Recall Announcements