Welcome! Here are the website rules, as well as some tips for using this forum.
Need to contact us? Visit https://heatinghelp.com/contact-us/.
Click here to Find a Contractor in your area.
7 sq. ft water tube boilers?
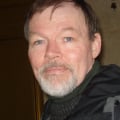
Brad White
Member Posts: 2,399
from when you stopped in at my old company, BR+A. Glad you still enjoy it! I would hate to see what that would fetch on e-Bay :)
Seriously- glad you have it. It would just collect dust at my house.
Seriously- glad you have it. It would just collect dust at my house.
"If you do not know the answer, say, "I do not know the answer", and you will be correct!"
-Ernie White, my Dad
-Ernie White, my Dad
0
Comments
-
7 Sq. Ft. Heating Surface Water Tube Boilers??
I just got my copy of Engineered Systems magazine for Oct. and saw an ad for Bryan's new 85% gauranteed efficiency water tube boiler models with "7 sq. ft. of heating surface per boiler horsepower". Maybe I don't understand but boilers move from 10 sq. ft. required in the age of hand-shoveled coal to 5 sq. ft? How does 7 sq. ft. produce better effciencies? Wouldn't this make the boiler larger or at least heavier? Can anyone explain the engineering reasoning behind this seemingly backward techology? Thank you...Joye0 -
HX area
I cannot speak to the exact boiler mentioned, but a larger heat exchanger has the ability to extract more heat from the flue gas. I believe this is why mod/con efficiencies increase as the firing rate decreases. I have wondered, If this is the case, why boiler manufacturers have not simply increased the size of their heat exchangers to run mod/cons at high efficiency at high temperatures.0 -
Economic Balance
I think the economic balance of material and delivery costs weighs heavily on this. Also the real crux of combustion technology is the ability to balance fuel and air across a modulating range.
If a boiler is designed for a certain high-fire mass-flow and not of a condensing variety, the lower turn-down limit would be a function of velocity or rather the lack thereof at lower firing rates. To keep velocity up you could use more air but that defeats other things....
With true condensing designs I can see lower velocities subject to draining the condensate but in the end, you still have to evacuate the flue gasses and that takes air...
The standard I always had in mind was 5 SF per BHP as offered by Cleaver-Brooks in their fire-tube lines. I recall others such as Johnson and Kewaunee I think, being a bit less than that.
Joye- you used to or may still work for Kewaunee boiler if I recall. What does Kewaunee do currently?
"If you do not know the answer, say, "I do not know the answer", and you will be correct!"
-Ernie White, my Dad0 -
Random thoughts
Viessmann makes a big deal of their 0.8mm gap between the coils in the HX as shown on page 5. I assume this is a function of flue gas flow rate/velocity and turbulence between the tubes? I suppose there must be practical limits to the long dimension of the rectangular tube that can be bent into a tight coil, and those limits probably controls that dimension.
If they increased the number of coils in the Vitodens without changing the burner, the flue gas velocity through the heat exchanger would decrease. Tighter gaps could increase the velocity, but I suppose the condensate might start to pose an obstruction as the gaps got tighter? Then the burner would need a high pressure blower to make that Glowcore work, and the flue gas flow would probably be less uniform through the heat exchanger.
I think I'm starting to reason myself out of the idea of increasing the heat exchanger area in a mod/con. The cost increase would likely be significant, and the benefit might be relatively small.
Thanks for knocking some sense into me, Brad. ;-)0 -
Hey Brad!
I left Kewanee Boiler to be an independent marketing consultant in 1999. Burnham Corp. closed Kewanee Sept. 12, 2001 after 133 years. I still have ties to the industry and still look at technology ads. I think the last time I posted here was asking were the 5 sq. ft. standard came from and kept those responses which had a lot of folk lore and how much coal a woman could shovel with all her windows open...then people came out with auto-feed systems and declared them "twice as effecient at half the size" as a matter of across the board marketing. Less that 5 sq. ft. with efficiency and a smaller footprint was the industry direction from 1995 up until I read this ad about a new 7 sq. ft. standard. I'm not an engineer so thought I'd ask. Typically demonstrated factory efficiencies are a percent or two higher than real world operational efficiencies. As you know, almost anyone can demonstrate any efficiency in a lab with controled ambient and flow temps for the short time needed for certification...but real world is something else. While 1-2% can mean big bucks these days with oil prices where they are, I'd wonder of the addition of 2 sq. ft. heating season would balance out with real world efficiency results. Any more thoughts? Joye0 -
Hey Joye!
I knew I had not heard much from Kewaunee lately... Maybe I knew they went under but forgot obviously....
It has been some time. My only thoughts on this are that the pendulum is swinging back a bit and they are finding a balance point between material cost and efficiency. Not sure what the older water-tube boilers were like in terms of SF per BHP but if they were 5.0 and now 7.0... where do you fit that extra 40% surface area?
I am sure it was tested out- no one pushes more material for no benefit... Hope you are well-
Brad"If you do not know the answer, say, "I do not know the answer", and you will be correct!"
-Ernie White, my Dad0 -
0.8 mm gap
From the exceptional Viessmann White Paper titled Condensing Technology:
"An alternative to...intensively swirling hot gas flow...is the laminar heat transfer method... These centres [0.8 mm], which are matched to the special flow characteristics of hot gasses, ensure that a laminar flow without a boundary layer is created in the gap..."
Here's a good definition of "laminar flow": uninterrupted flow in a fluid near a solid boundary in which the direction of flow at every point remains constant.
If I'm understanding properly not only are the flue gasses moving straight through the gap without any form of turbulence, but the lack of a boundary layer means the velocity of the gases are consistent throughout the entire area of the gap. The gap size is not about increasing turbulence, it's about eliminating turbulence...
Since the amount of combustion air is strictly controlled in the Vitodens burner I believe it fairly safe to say that the quantity of gasses leaving the HX through that gap (remember--there's technically only one gap as the HX is in a coil) will vary in quite close proportion to burner output. With a 4-1 turndown ratio, I would assume the amount of flue gasses varies quite similarly. Velocity of the gas [probably] does not vary by anywhere the same degree. Why do I say that? Because gas is highly compressible and something tells me that the velocity through the gaps stays fairly consistent regardless of burner output. The total surface area of the gap is tiny so it can actually build some pressure--the greater the output, the greater the pressure. Greater pressure means more gas can flow through the gap without a change in velocity.
Another thing to remember about the Vitodens 200 is that it uses a radiant burner. Since gas burns at a fixed temperature, I suspect--for a given average temp inside the HX--that the amount of energy transferred via radiation also remains fairly consistent regardless of burner output. I seriously doubt that heat transfer via radiation at full burner output is anywhere near 4x the radiant transfer at minimum burner output. Thus, the proportion of transfer via radiation will increase as burner output decreases. This means that the flue gasses will be significantly cooler before they ever reach the HX at minimum modulation than at maximum modulation.
In utterly ideal conditions, the Vitodens 200 seems capable of efficiency so close to 100% (GROSS fuel value) that further improvement is pointless. This is rather like very large electric motors/generators whose general design remains unchanged over 100 years after Tesla invented them... While not particularly common, I have logged numerous periods of sustained (30+ minutes) operation where flue gas temperature is below supply temperature. I've compared sensors at the exact same temp within a suitable range and can confidently say that the measured difference is a number of times greater than the relative temp error between the sensors.
If such ideal conditions could be constantly sustained, I could see a case for some increase in HX size, but in the real world conditions are anything but constant. Average temp in the HX affects the efficiency of any mod-con more than anything and in nearly any real-world space heating situation, average temperature will raise as system load increases and increased HX area will have less and less affect on overall efficiency. Even a genuinely uncompromising machine like the Vitodens 200 reaches a point where increased material/production costs could never provide a reasonable increase in efficiency.
0 -
I like Ike
Just thought I'd mention that I'm still a political collector and the Ike pin you gave me is now part of a 1200 collection of Ike pins framed and sparkling in my formal dining room...Joye0 -
I like Ike too
well that struck a chord. When I was a kid - a long time ago, I had a collection of political buttons. There were "I like Ike" and "I like Ike even better" but I don't remember the years. By the time I realized that these were collectible, they were long gone. Maybe you've got em?
Larry0 -
more Ike...
I have "Ike likes Me" and "Adlia Likes Ike" too. Actually as a child of the 50's and a lover of history, I remembered the colorful costume jewelry that was strongly suggested by Mamie to all those manufacturers of the day incorporating her husbands name. I'll be the one in NYC at AHR with the rhinestone "I Miss Ike" pin. Joye0 -
Laminar flow
Laminar flow to produce better heat transfer by a reduction in boundary layer thickness is counterintuitive to me. Perhaps they are riding the edge between laminar and turbulent flow in order to maximize heat transfer with a minimum of pressure drop? I would say the velocity would vary somewhere in the 4:1 range (probably a little less because of compression at higher flue gas flow rates), because there has to be a mass balance through the boiler.0 -
I think you are reading it right, Andrew
The use of laminar flow would be a way to reduce heat transfer (maybe not wasting turbulence where you do not need to?). But I agree with you that turbulence is what works, the constant wiping of the layer surface to assure "fresh meat" at the metal surface.
The use of turbulators (spiral bronze rifling devices) within coils and fin-tube is such a way to increase heat transfer at lower velocities. Turbulence if generated at a given mass flow can compensate for the lower mass flow. In other words, stirring things up can make up for the drop in velocity."If you do not know the answer, say, "I do not know the answer", and you will be correct!"
-Ernie White, my Dad0 -
When I first read about the laminar flow and lack of boundary layer in the Vitodens 200 HX gap, it seemed a bit counter-intuitive to me as well. Mfgr. literature (even
quite old) almost always seemed to make a big deal about how their design was achieved [better] heat transfer by forcing the flue gasses to swirl, change directions, etc.
So, I had to try to think why it was desirable to have the flue gasses swirling in a convoluted path to begin with...
As best I could understand that necessity came mainly from the establishment of boundary layers. When a fluid passes over a solid, friction tends to decrease the velocity of the fluid near the surface of the solid. To me, it's easiest to visualize this when a fluid is forced through a tube. The fluid "wants" to move in a laminar (e.g. equal velocity) manner, but friction builds against the tube walls.
As the friction builds, velocity along the walls of the tube reduces, yet right against the tube it's moving in nice and straight (e.g. little if any turbulence). As you get towards the center of the tube, the fluid is also moving nice and straight with little if any turbulence. What happens between these fluid layers? Friction. Since we're in a fluid environment that friction will,
more than anything, result in turbulence.
Meteorologically speaking (e.g. when the fluid is a gas), boundary layers aren't just about friction. Temperature difference plays a significant roll as well. Not only
can temperature difference help establish a boundary layer, but once the boundary is established it can actually enhance the boundary by increasing the temperature
difference by effectively insulating the layers from one another! (This is probably true for liquid fluids as well, but I see it mentioned most with regards to the atmosphere.)
What you wind up with is two layers of fairly coherent flow separated by a layer of intense turbulence. The flue gasses in the inner layer cannot liberate their heat to the solid as they are insulated from the outer layer by the turbulence... THIS, I believe, is why most (if not every save the Vitodens) boilers intentionally produce turbulence in the flue gasses. "Stir" the flue gasses and you'll reduce or eliminate the formation of boundary layers.
So what happens if you eliminate the boundary layers? Gasses are so energetic to begin with that they just don't "like" to hold or accept heat. Flue gasses aren't extremely hot because they're "made" hot, they're hot because they're created hot. They have such little affinity for heat that they can easily liberate nearly all of their temperature above ambient condition to even a relatively hideous metal conductor like thick stainless steel--as long as you don't let those insulating boundary areas form.
There's certainly friction in that very narrow gap in the Vitodens 200 HX, but the gap is narrow enough and so well suited to both the nature and velocity--Interstate if not Autobahn speeds-- of the flue gasses that they pass through the gap with nearly perfect coherence and are forced by nature to give up nearly all of their heat energy to anything cooler--even a relatively lousy conductor.
While I have no way to confirm, something still tells me that the velocity of the flue gasses through the gap stays fairly consistent regardless of the output level of the burner. Only when velocity gets high enough (due to maximum output) through that tiny gap that it can begin to establish a boundary layer does Viessmann increase the HX size. I'm nearly positive that the Vitodens 200 6-24 and 8-32 share the same HX as do the larger sizes.
0 -
Double post--Sorry
nm0
This discussion has been closed.
Categories
- All Categories
- 86.7K THE MAIN WALL
- 3.1K A-C, Heat Pumps & Refrigeration
- 56 Biomass
- 423 Carbon Monoxide Awareness
- 104 Chimneys & Flues
- 2K Domestic Hot Water
- 5.6K Gas Heating
- 103 Geothermal
- 158 Indoor-Air Quality
- 3.5K Oil Heating
- 68 Pipe Deterioration
- 938 Plumbing
- 6.2K Radiant Heating
- 385 Solar
- 15.3K Strictly Steam
- 3.4K Thermostats and Controls
- 54 Water Quality
- 43 Industry Classes
- 47 Job Opportunities
- 18 Recall Announcements